Ural diesel vehicles are equipped with a KamAZ-740 engine of the third configuration. Therefore, we look at engine repair and maintenance in articles on repairing a KamAZ diesel engine Kamaz engine
Engine malfunction during operation is determined:
- - power drop;
- - increased fuel and oil consumption;
- - low oil pressure;
- - the nature of the knocks and noise of operation.
A drop in engine power affects the dynamic qualities of the car: poor acceleration, climbing hills in a lower gear, reduced maximum speed.
A drop in engine power can also be characterized by a decrease in compression in one or more cylinders.
A decrease in the compression value in the engine cylinders indicates wear of the piston rings and valve leaks.
Compression is measured using a compression meter on a warm engine at a coolant temperature of at least 80 °C and at a minimum idle speed (600 rpm).
To determine the compression pressure, install a compression gauge in the cylinder head glass instead of an injector and clamp it with the injector mounting bracket.
Place a fuel-resistant rubber hose onto the fitting of the high-pressure pump section being tested and lower its end into a vessel to collect the fuel that will come from the pump section when checking the compression.
Then start the engine and record the pressure indicated by the pressure gauge of the device at minimum engine crankshaft speed.
Measure compression in the remaining cylinders in the same way.
In a working engine, the compression value should not be lower than 30 kgf/cm 2, and the pressure difference in the cylinders should not exceed 2 kgf/cm 2.
The control fuel consumption, indicated in the technical specifications of the vehicle, is determined by measuring the fuel consumption when a loaded vehicle is moving at a speed of 40 km/h in top gear in two opposite directions on a flat horizontal asphalt section of the highway with a length of 1 km.
If other vehicle components are in good condition, the increased control fuel consumption is a consequence of the unsatisfactory technical condition of the engine.
Longitudinal and transverse section of the engine
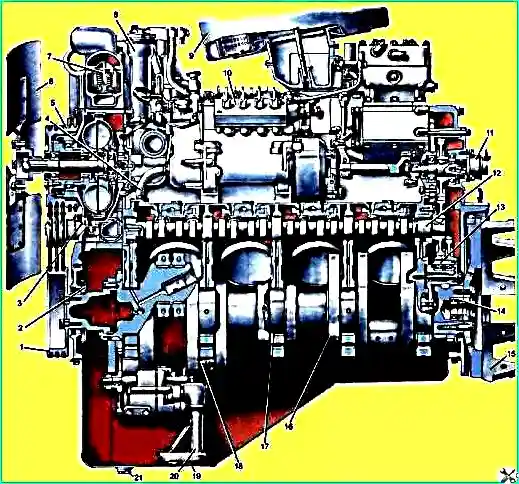
Cross section of the engine
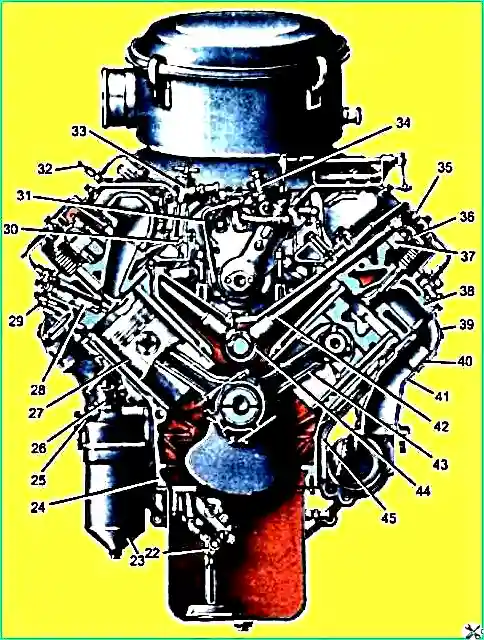
Increased oil consumption (in the absence of leakage) indicates wear of the cylinder-piston group, coking of the holes in the grooves for the oil scraper rings, and burnt-on rings.
Low oil pressure (if the lubrication system is working properly) is a consequence of significant wear of the crankshaft and camshaft bearings.
The reasons for a sudden and sharp drop in oil pressure in the main oil line may be clogging and sticking in the open position of the oil pump valve, the lubrication system, as well as emergency wear and damage to the liners of one or more bearings.
Valve sticking and emergency wear of the liners may be a consequence of operating the engine with dirty oil.
Use a stethoscope to detect oil and determine the nature of knocking and noise.
By the tone of the knock, as well as by the location on With greater audibility, you can determine the cause and location of the malfunction.
Strong, high-pitched (metallic) knocks, which intensify with increasing crankshaft speed, are characteristic of the piston hitting the valve when the spring breaks or the valve is stuck in the guide.
Knocks heard in the upper part of the cylinder block, which subside as the crankshaft rotation speed increases and increase as it decreases, can be caused by scuffing of the working surface of the liners or pistons.
As the clearances increase in the connections of the piston with the piston pin or the piston pin with the upper head of the connecting rod, as well as in the main and connecting rod bearings, knocking noises may appear, easily audible under load, with a sharp change in fuel supply.
With an increased gap between the piston and cylinder liner, a dull knock is heard after a cold start and subsides or disappears completely after the engine warms up.
A high-pitched sound in the area where the valves are located, as a rule, indicates increased clearances between the toe of the rocker arm and the end of the valve stem.