Design and operation of supply line devices
The pneumatic drive of the brake mechanisms (Fig. 1) has a source of compressed air - compressor 1
The compressor, pressure regulator 3, fuse 4 against freezing of condensate in compressed air and condensation receiver 20 form part of the drive from which purified compressed air and water at a given pressure are supplied in the required quantity to the remaining parts of the pneumatic drive and to other consumers of compressed air.
The drive is divided into autonomous circuits, separated from one another by protective valves. Each circuit operates independently of the others.
Circuit 1 of the drive mechanisms of the front axle service brake system includes:
- - part of the triple safety valve 6; receiver 15 with a volume of 20 l with a condensate drain valve and a pressure drop sensor 23 in the receiver, part of a two-pointer pressure gauge 21;
- - lower section of two-section brake valve 17;
- - control valve “C”;
- - pressure limitation valve 19; two brake chambers 20;
- - front axle brake mechanisms;
- - pipelines and hoses between these devices.
In addition, the circuit includes a pipeline connecting the lower section of the brake valve 17 with the valve 27 for controlling the brake systems of a trailer with a two-wire drive.
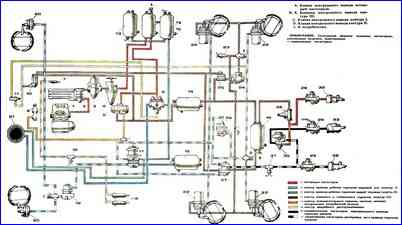
Circuit II of the drive mechanisms of the working brake system of the rear bogie consists of:
- - from part of the triple safety valve;
- - 13 receivers with a total volume of 40 liters with condensate drain valves 16 and pressure drop sensor 23 in the receiver;
- - parts of two-pointer pressure gauge 21;
- - upper section of two-section brake valve 17;
- - valve control terminal “D”;
- - automatic regulator of 26 brake forces with an elastic element;
- - four brake chambers 26 brake mechanisms.
The circuit also includes a pipeline connecting the upper section of the brake valve 17 with the valves 26 for controlling the trailer brake systems.
Circuit III of the drive mechanisms of the spare and parking brake systems, as well as the combined drive of the brake systems of the trailer (semi-trailer) includes:
- - part of double safety valve 5;
- - two air receivers 14 with a total volume of 40 liters with a condensate drain valve and a pressure drop sensor 23 in the receiver;
- - two control valves “B” and “E”;
- - valve 10 for controlling the parking brake system;
- - accelerator valve 25; part of a two-line bypass valve 24;
- - four spring energy accumulators 22, pressure drop sensor 18 in the line of spring energy accumulators;
- - valve 31 for controlling trailer brake systems with a two-wire drive;
- - single safety valve 28;
- - valve 27 for controlling trailer brake systems with a single-wire drive;
- - three disconnect valves 29. three connecting heads (one head 38 type “A” for a single-wire drive of trailer brake systems and two heads 32 type “Palm” for a two-wire drive of trailer brake systems);
- - pneumoelectric sensor 31 for turning on the brake signal;
- - pipelines and hoses between these devices.
Circuit IV of the auxiliary mechanism drive of the braking system and other consumers consists of:
- - from part of the double safety valve 5; pneumatic crane 11;
- - two cylinders that drive the gas-dynamic brake mechanism flaps;
- - one pneumatic cylinder 10 for driving the engine stop lever, a pneumoelectric sensor, pipelines and hoses between these devices.
The drive is supplied with air from the condensation receiver; the circuit does not have a pressure drop indicator lamp.
From circuit IV of the drive mechanisms of the auxiliary brake system, compressed air is supplied to additional consumers: pneumatic signal, pneumatic clutch booster, transmission unit drives, etc.
Features of the pneumatic drive of the brake systems of cars models 5511, 53212: to improve moisture and oil separation in the supply part of the brake drive of the car mod. 53212 in the compressor – pressure regulator section, a moisture-oil separator is additionally installed on the first cross member of the frame in the zone of intense airflow; on a dump truck mod. 5511 lacks trailer brake system control equipment, disconnect valves, and connecting heads.