KamAZ car driveline
The cardan transmission is used to transmit torque from the shaft of the gearbox or transfer case to the shaft of the vehicle's drive axle at changing angles and distances between them.
On three-axle KamAZ vehicles, torque is supplied to the intermediate and rear drive axles by one common shaft
From the intermediate axle, which is a through bridge, torque is transmitted to the rear axle by an additional driveshaft.
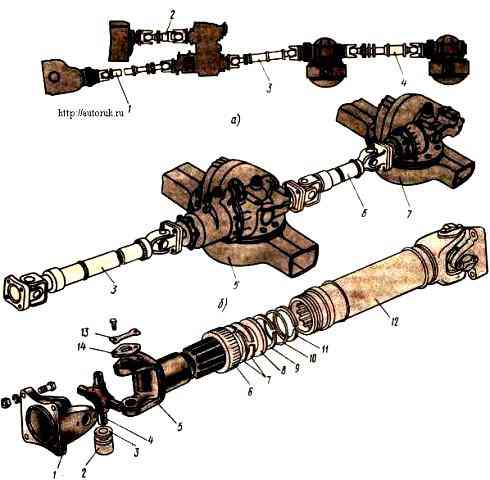
Drive shaft: 1 - fork flange; 2 - needle bearing; 3 - seal; 4 - cross; 5 - sliding fork; 6 - nut; 7, 9, 11 - split washers; 8 - felt ring; 10 - rubber ring; 12 - shaft; 13 - locking plate; 14 - support plate
The cardan transmission is designed to transmit torque to individual units and mechanisms (connection of the gearbox with the transfer case, winch drive, connection of the shaft and left column with the steering mechanism).
On off-road vehicles with a driven front axle, constant-velocity universal joints are used to drive the front steered wheels.
Gardan transmission device. The cardan transmission consists of shafts and universal joints.
All universal joints consist of a fixed or sliding fork, a fork flange and a cross mounted in the fork ears on needle bearings.
Needle bearings are sealed by two oil seals and a radial seal oil seal built into the bearing race, and a double-lip mechanical seal oil seal.
When the driving fork rotates uniformly, the driven fork rotates unevenly.
For one revolution of the propeller shaft, the driven fork, when rotating, twice overtakes the driving fork and twice lags behind it.
As a result, additional loads arise on the parts of the main gear, differential, axle shafts and wheels, and their wear increases.
To eliminate uneven rotation of the driven shaft, a cardan transmission is used, in which universal joints are installed at both ends of the shaft.
When installing the yokes of both universal joints on the shaft in the same plane, the uneven rotation created by the first universal joint will be equalized by the second joint.
To reduce vibration, perform dynamic balancing of the driveshaft assembly with cardan joints.
The imbalance is eliminated by welding balancing plates or installing them under the locking plate of the bolts securing the universal joint covers.
The cardan transmission of KamAZ-4310 and KamAZ-43105 vehicles, which have a 6X6 wheel arrangement with sequential through drive of the rear axles, is shown in Fig. 1.
It consists of four cardan shafts and main shaft 2 between the gearbox and transfer case, intermediate axle drive shaft 3 and front axle drive shaft 1.
The intermediate axle has a through shaft of the main drive, which transmits torque to the rear drive axle through the propeller shaft 4.
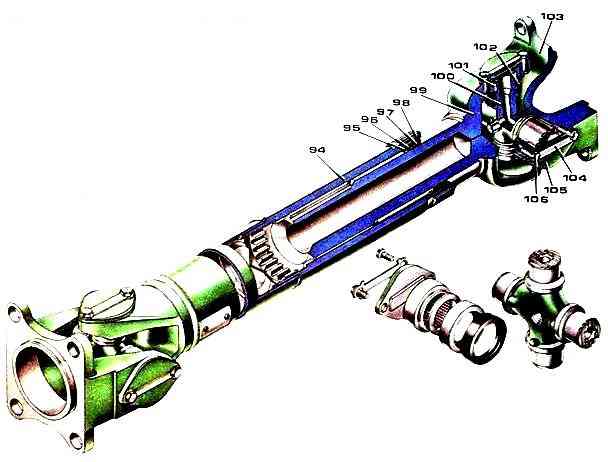
The design of the cardan shafts (Fig. 1) uses a movable spline connection, which ensures the necessary change in the working length of the shaft when the vehicle is moving.
To protect the spline joint from dirt and retain lubricant, the cardan shafts are sealed at the joints.
The lubricant is kept in the internal cavity from leaking out by a plug rolled into the splined sleeve, as well as by rubber and felt rings 10 and 8, which are tightened by the gland nut 6.
Drive shafts are assembled so that their fixed and sliding forks are located in the same plane.
For this purpose, arrows are stamped on the splined bushings of the cardan shafts and on the sliding forks. It is necessary that these arrows are aligned.
Balancing of the cardan shafts of the front, intermediate and rear axles is carried out by welding a balancer wax plates.
The main driveshaft is balanced by placing balancing plates under the locking plate of the support plate bolts on the forks.
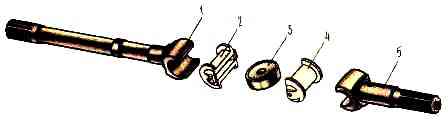
In the drive to the front driving steered wheels of the front axles of the KamAZ-4310 and KamAZ-43105 vehicles, cam-type universal joints are used.
They transmit torque from the main gear to the front wheels, ensuring equality of the angular velocities of the side gears of the main drive of the front wheels when they are turned at a significant angle.
The hinge consists of two fists 1 and 5 (Fig. 2) with liners 2, 4 and disk 3.
The disk fits into the grooves of the liners, which, in turn, are installed with cylindrical surfaces into the forks of the fists.
Thanks to this connection, the hinge works like two articulated hinges of unequal angular velocities.
In one plane the forks rotate relative to the liners, and in the other - together with them relative to the central disk.