Перед сборкой двигателя необходимо все его детали очистить от нагара и смолистых отложений
Нельзя промывать в щелочных растворах детали, изготовленные из алюминиевых сплавов (блок и головку цилиндров, поршни и др.), так как эти растворы разъедают алюминий.
Для очистки деталей от нагара рекомендуются следующие растворы:
Для алюминиевых деталей:
- Сода (Na2CO3) – 18,5 г
- Мыло (зеленое или хозяйственное) – 10,0 г
- Жидкое стекло – 8,5 Г
- Вода – 1 л
Для стальных деталей:
- Каустическая сода (NaOH) – 25,0 г
- Сода (Na2CO3) – 33,0
- Мыло (зеленое или хозяйственное) – 8,5 г
- Жидкое стекло – 1,5 г
- Вода – 1л
При сборке двигателя соблюдать следующие условия:
- - протереть все детали перед сборкой чистой салфеткой и продуть сжатым воздухом, а все трущиеся поверхности смазать чистым маслом;
- - осмотреть детали перед постановкой на место (нет ли трещин, отколов, забоин в других дефектов), проверить надежность посадки запрессованных в нее деталей, дефектные детали подлежат ремонту или замене новыми;
- - все резьбовые детали (шпильки, пробки, штуцера), если они вывертывались или были заменены в процессе ремонта, необходимо ставить на сурике или белилах, разведенных на натуральной олифе.
Все неразъемные соединения, например заглушки блока цилиндров и т. п., должны ставиться на нитролаке.
К постановке на двигатель не допускаются:
- - шплинты, шплинтовочная проволока и стопорные пластины, бывшие в употреблении;
- - пружинные шайбы, потерявшие упругость;
- - поврежденные прокладки;
- - детали, имеющие на резьбе более двух забитых или сорванных ниток;
- - болты и шпильки с вытянутой резьбой; болты и гайки с изношенными гранями.
Болты и гайки должны быть соответствующим образом законтрены (шплинтами, шплинтовочной проволокой, пружинными и специальными шайбами и контргайками).
Сборку двигателя производить в следующем порядке:
- - очистить все привалочные поверхности блока цилиндров от прилипших и порванных при разборке прокладок;
- - закрепить блок цилиндров на стенде, вывернуть с заднего торца пробку масляного канала и продуть все масляные каналы сжатым воздухом. Завернуть пробку на свое место;
- - если имеется необходимость в замене картера сцепления или он устанавливается на блок цилиндров после ремонта, необходимо из блока предварительно удалить два установочных штифта, затем картер крепить к блоку цилиндров шестью болтами.
В блок цилиндров на крайних подшипниках устанавливают коленчатый вал, к фланцу которого крепится стойка индикатора.
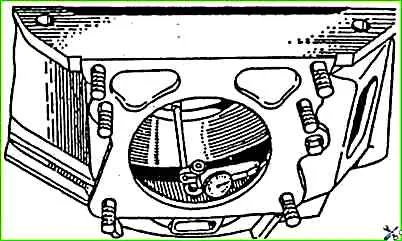
Вращая коленчатый вал, проверяют биение отверстии для центрирующего бурта коробки передач, а также перпендикулярность заднего торца картера сцепления относительно оси коленчатого вала, как показано на рис. 1 и рис. 2.
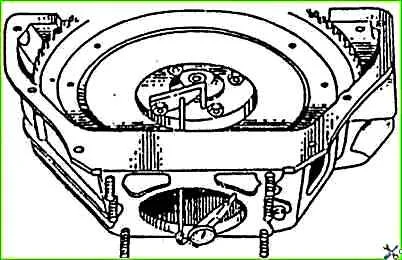
Биения отверстий картера и торца не должны превышать 0,08 мм.
Если биение отверстия превышает указанную величину, следует ослабить затяжку болтов, крепящих картер к блоку цилиндров, и легкими ударами по фланцу картера добиваться правильной его установки;
- - после затяжки болтов отверстия для установочных штифтов в картере сцепления и блоке цилиндров развертывают до ремонтного размера. Диаметр отверстия должен быть таким, чтобы в развернутых отверстиях не оставалась чернота.
После этого в отверстия запрессовывают штифты, диаметр которых на 0,015—0,051 мм больше размера отверстий;
- - биение торца картера устраняется шабровкой. Следует иметь в виду, что при вышеописанной проверке необходимо пользоваться неизношенными коленчатым валом и вкладышами. При изношенных деталях результаты будут неверными;
- - снять коленчатый вал;
- - заменить (при необходимости) гильзы цилиндров новыми следующим образом:
- - с помощью съемника (рис. 3) вынуть старую гильзу из блока;
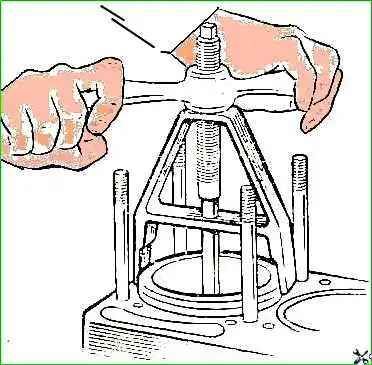
- - тщательно очистить от накипи и коррозии посадочные поверхности и поверхности уплотнения на гильзе и в блоке цилиндров;
- - вставить новую или отремонтированную гильзу с надетой на нее прокладкой из красной меди. Гильза должна входить в блок цилиндров свободно, без усилий;
- - закрепить гильзу держателем от выпадания.
Примечание. При замене дефектных или изношенных гильз новыми или отремонтированными положение их в блоке цилиндров не ориентируется.
В остальных случаях, прежде чем вынуть гильзы из блока цилиндров, необходимо маркировать их порядковыми номерами (счет вести от водяного насоса и коробке передач), а также отметить их положение в блоке цилиндров чтобы при сборке обеспечить их установку в прежнее положение.
При использовании - изношенных гильз цилиндров, а также при каждой установке в изношенные гильзы новых поршневых колец необходимо расточкой на станке или шабером неизношенный поясок над верхним компрессионным кольцом.
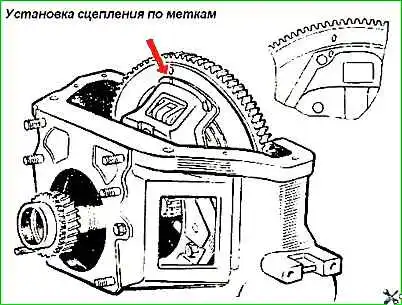
Снимать металл надо вровень с изношенной частью гильзы;
- отрезать от шнура две набивки сальника заднего коренного подшипника коленчатого вала (длиной 120 мм каждая), вложить их в блок и держатель сальника;
Произвести подсборку коленчатого вала:
- - вывернуть все пробки грязеуловителей шатунных шеек и удалить из них отложения. Промыть и продуть масляные каналы и полости грязеуловителей сжатым воздухом, завернуть и закернить пробки;
- - проверить состояние рабочих поверхностей вала. Забоины, надиры и другие наружные дефекты не допускаются;
- - смазать тугоплавкой консистентной смазкой 1-13 и запрессовать в задний конец коленчатого вала подшипник ведущего вала коробки передач;
- - привернуть маховик к коленчатому валу двигателя динамометрическим ключом (момент затяжки гаек 7,6-8,3 кгм); гайки зашплинтовать;
- привернуть нажимной диск сцепления в сборе с кожухом к маховику, предварительно отцентровав ведомый диск с помощью оправки (можно использовать ведущий вал коробки передач) по отверстию в подшипнике в заднем торце коленчатого вала.
Метки «О», выбитые на кожухе нажимного диска и маховика около одного из отверстий для болтов крепления кожуха (рис. 4), должны быть совмещены.
Ведомый диск сцепления ставить в такое положение, чтобы демпфер был обращен к маховику.
Коленчатый вал, маховик и сцепление балансируются в сборе, поэтому при замене одной из этих деталей следует произвести динамическую балансировку. Дисбаланс не должен превышать 70 Гсм.
При балансировке снятие лишнего веса с тяжелой стороны производится высверливанием металла маховика на радиусе 151 мм сверлом диаметром 10 мм на глубину не более 12 мм.
Расстояние между центрами сверлений должно быть не менее 14 мм.
Балансировку узла не следует начинать, если начальный дисбаланс превышает 180 Гсм.
В этом случае необходимо разукомплектовать узел и проверить балансировку каждой детали в отдельности;
- - надеть на первую коренную шейку коленчатого вала заднюю упорную шайбу баббитовой стороной к щеке вала;
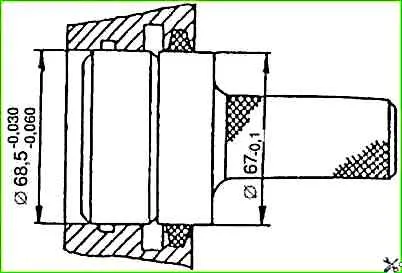
- - обжать задний сальник вала. Для этого в отверстие заднего коренного подшипника поставить оправку (рис. 5), установить держатель сальника и затянуть гайки подшипника и держателя;
протереть чистой салфеткой вкладыши коренных подшипников в их постели вложить вкладыши в постели;
- - смазать чистым маслом для двигателя вкладыши коренных подшипников и шейки коленчатого вала и уложить коленчатый вал в блок цилиндров;
- - надеть крышки коренных подшипников на шпильки блока цилиндров так, чтобы фиксирующие выступы на верхнем и нижнем вкладышах каждой крышки были с одной стороны, а номера, выбитые на крышках, соответствовали номерам постелей, выбитым на блоке цилиндров около шпилек.
При установке крышки переднего подшипника усик задней шайбы упорного подшипника коленчатого вала должен войти в паз крышки. Торец крышки переднего подшипника должен быть в одной плоскости с торцом блока цилиндров;
- - посадить крышки коренных подшипников на свои места легким постукиванием резиновым молотком; крышки должны войти в пазы постелей блока;
- - навернуть гайки крепления крышек и равномерно затянуть их, предварительно поставив стопорную пластину. Окончательную затяжку необходимо производить динамометрическим ключом (момент 10-11 кГм), отогнуть усики стопорной пластины;
- - установить в пазы держателя сальника резиновые прокладки и их боковую поверхность, выступающую из паза, обмазать мыльным раствором. Установить держатель сальника на место и затянуть гайки;
- - провернуть коленчатый вал, который должен свободно вращаться при небольшом усилии.
Вращать коленчатый вал можно за маховик или с помощью приспособления, состоящего из ведущего вала коробки передач с приваренным к нему четырехгранником под ключ или ручкой с квадратным отверстием.
Приспособление может быть использовано также для центрирования при постановке ведомого и нажимного дисков сцепления;
- - поставить переднюю шайбу упорного подшипника баббитовой стороной к валу так, чтобы штифты, запрессованные в блок цилиндров и крышку, входили в пазы шайбы;
- - надеть стальную упорную шайбу коленчатого вала неизношенной поверхностью к покрытой баббитом поверхности передней шайбы упорного подшипника;
- - напрессовать до упора шестерню коленчатого вала и проверить осевой зазор коленчатого вала.
Проверка производится следующим образом: заложить отвертку (вороток, рукоятку молотка и. т. п.) между первым кривошипом вала к передней стенкой блока цилиндров и, пользуясь ею как рычагом, отжать вал к заднему концу двигателя.
С помощью щупа определить зазор между торцом задней шайбы упорного подшипника и плоскостью бурта первой коренной шейки. Зазор должен быть в пределах 0,075-0,175 мм;
произвести подсборку шатунно-поршневой группы:
очистить днища поршней и канавки для поршневых колец от нагара, как показано на рис. 6;
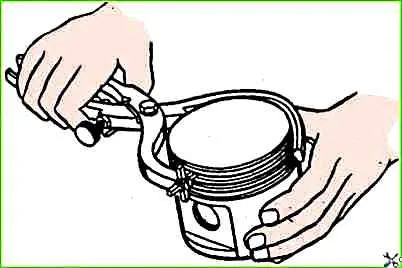
- - в случае замены поршня, поршневого пальца или шатуна необходимо:
- - вынуть с помощью плоскогубцев стопорные кольца поршневого пальца;
- - на приспособлении вынуть поршневой палец (поршневые кольца перед этим должны быть сняты);
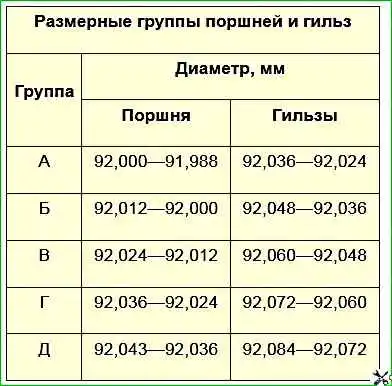
- подобрать новые поршни по гильзам с зазором 0,012—0,024 мм.
Подбор проверяется протягиванием при помощи пружинного безмена ленты-щупа, заложенного между поршнем и цилиндром.
Щуп располагается в плоскости, перпендикулярной оси поршневого пальца.
Поршень должен быть без поршневых колец.
Усилие протягивания при нормальной комнатной температуре (+20°с) должен быть в пределах 3,5—4,5 кг.
Размеры ленты: толщина —0,05 мм, ширина — 13 мм, длина — 250 мм;
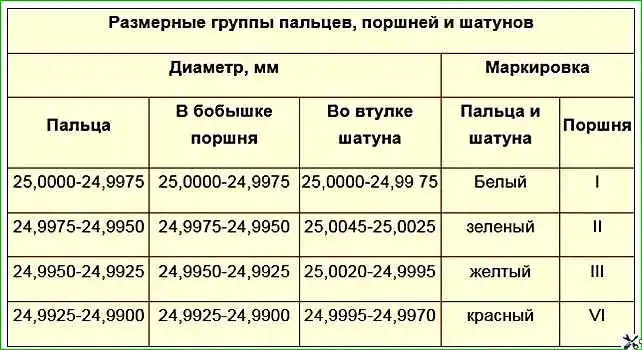
- подобрать поршневой палец к шатуну так, чтобы при нормальной комнатной температуре он плавно перемещался в отверстии верхней головки под легким усилием большого пальца руки.
Поршневой палец, должен быть слегка смазан маслом.
Цвет маркировки пальца должен соответствовать цвету маркировки на бобышках поршня;
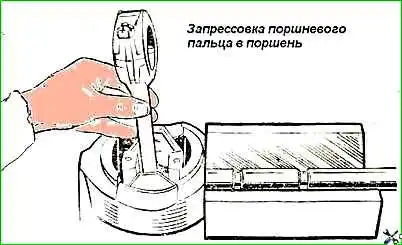
- произвести подсборку шатунно-поршневой группы на приспособлении (рис. 7).
Поршень перед запрессовкой в него поршневого пальца необходимо нагреть в горячей воде до температуры 70°С; запрессовка пальца о холодный поршень может привести к повреждению поверхности отверстий в бобышках поршня, а также к деформации самого поршня.
Вставить стопорные кольца поршневого пальца в кольцевые канавки бобышек поршня;
- подобрать по цилиндру поршневые кольца; зазор; замеренный в стыке кольца с помощью щупа, должен быть 0,3-0,5 мм.
В изношенных цилиндрах наименьший зазор следует делать 0,3 мм;
- щупом проверить боковой зазор между кольцом и стенкой поршневой канавки (рис. 8). Проверку произвести по окружности поршня в нескольких точках.
Величина бокового зазора должна быть для верхнего компрессионного кольца в пределах 0,050—0,082 мм, а для нижнего компрессионного и маслосъемного колец — 0,035 — 0,067 мм;
- - надеть с помощью приспособления на поршень поршневые кольца. Компрессионные кольца ставят внутренней фаской к днищу поршня, как показано на рис. 12, кольца в канавках должны перемещаться свободно;
- - протереть салфеткой постели шатунов и их крышек, протереть и вставить в них вкладыши;
- - повернуть коленчатый вал так, чтобы кривошипы первого и четвертого цилиндров заняли положение, соответствующее нижней мертвой точке;
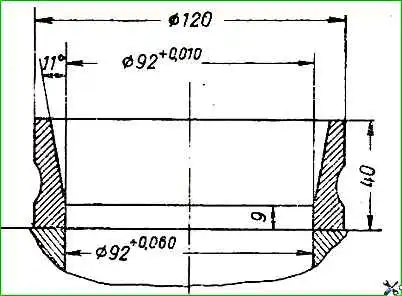
- смазать вкладыши, поршень, шатунную шейку вала и гильзу первого цилиндра чистым маслом для двигателя, развести стыки поршневых колец под углом 120° друг к другу, надеть на болты шатунов предохранительные латунные наконечники, сжать кольца обжимкой или, пользуясь конусным кольцом (рис. 9), вставить поршень в цилиндр.
Перед установкой поршня следует еще раз убедиться, что номера, выбитые на шатуне и его крышке, соответствуют порядковому номеру цилиндра, проверить правильность положения поршня и шатуна в цилиндре; метка на поршне «Назад» должна быть направлена к маховику, а отверстие в нижней головке шатуна — в сторону, противоположную распределительному валу;
- подтянуть шатун за нижнюю головку к шатунной шейке, снять с болтов латунные наконечники, надеть крышку шатуна так, чтобы номера, выбитые на крышке и шатуне, были обращены в одну сторону.
Завернуть гайки динамометрическим ключом (момент 6,8-4,5 кГм) и законтрить при помощи штампованной из листовой стали стопорной гайки. Момент затяжки стопорной гайки 0,3-0,5 кГм;
- в таком же порядке вставить поршень четвертого цилиндра, затем повернуть коленчатый вал на 180° и вставить поршни второго и третьего цилиндров.
Провернуть несколько раз коленчатый вал, который должен вращаться легко от небольших усилий;
произвести подсборку распределительного вала:
- - надеть на передний конец распределительного вала распорную втулку и упорный фланец;
- - напрессовать распределительную шестерню на вал и закрепить ее болтом с шайбой;
- - с помощью щупа, вставляемого между упорным фланцем распределительного вала и ступицей распределительной шестерни, проверить осевой зазор распределительного вала, который должен быть в пределах 0,1-0,2 мм;
- - прочистить трубку для смазки распределительных шестерен и привернуть ее с помощью болта и хомутика к блоку;
- - вставить подсобранный распределительный зал в отверстие блока, смазав предварительно его опорные шейки маслом для двигателя.
При зацеплении шестерен зуб шестерни коленчатого вала с меткой «О» должен быть против риски у впадин зубьев шестерни распределительного вала (см. рис. 17).
Боковой зазор в зацеплении должен быть в пределах 0,0З-0,08 мм. При большем или меньшем зазоре подобрать другую пару;
- - через отверстия в шестерне распределительного вала прикрепить двумя болтами с пружинными шайбами упорный фланец к блоку;
- - надеть на шейку переднего конца коленчатого вала маслоотражатель выпуклой стороной к шестерне;
- - проверить пригодность к дальнейшей работе сальника, запрессованного в крышку распределительных шестерен. Если сальник имеет изношенные рабочие кромки или слабо охватывает ступицу шкива коленчатого вала, вставленную в сальник, заменить его новым.
Запрессовку сальника в крышку рекомендуется производить при помощи оправки на прессе, как показано на рис. 10;
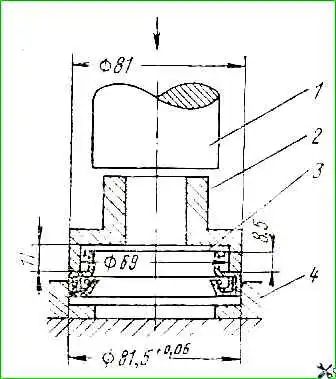
- надеть на шпильки прокладку и крышку распределительных шестерен;
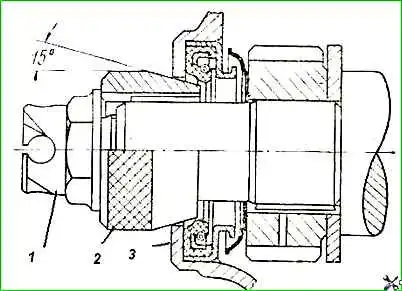
Сцентрировать крышку по переднему концу коленчатого вала при помощи оправки (рис. 11) и завернуть все гайки и болты крепления крышки.
Если нет центрирующей оправки, то установку крышки можно производить по ступице шкива коленчатого вала.
Ступицу надо напрессовать на коленчатый вал так, чтобы ее конец входил на глубину 5 мм в отверстие крышки.
После этого закрепить крышку гайками, выдерживая одинаковый зазор по окружности между ступицей и отверстием крышки.
Выравнивание зазора производить легкими ударами деревянного или резинового молотка по крышке. После этого окончательно закрепить крышку;
удалить центрирующую оправку и напрессовать ступицу шкива коленчатого вала;
- - завернуть в коленчатый вал храповик, предварительно надев на него пружинную шайбу.
Проворачивая за храповик коленчатый вал, проверить, не задевает ли отражатель за крышку распределительных шестерен из-за погнутости отражателя или ослабления посадки на ступице;
- - привернуть шкив коленчатого вала к ступице;
- - установить масляный насос в сборе с маслоприемником;
- - установить привод прерывателя-распределителя;
- - поворачивая коленчатый вал, совместить метку в. м. т. на ободе шкива коленчатого вала с указателем на крышке распределительных шестерен (см. рис. 14).
Кулачки распределительного вала, приводящие в действие клапаны первого цилиндра, должны быть при этом направлены вершинами в противоположную от толкателей сторону (в сторону поддона картера) и расположены симметрично, как показано на рис. 12;
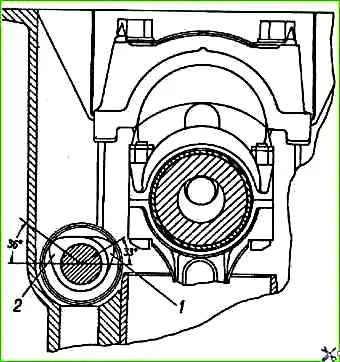
- проверить осевой зазор валика привода при помощи щупа, вставляемого между корпусом привода и шестерней.
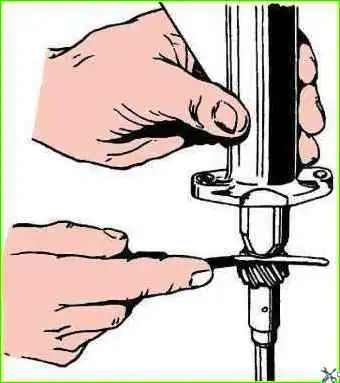
Зазор должен быть в пределах 0,15—0,40 мм;
Надеть на шпильки крепления привода прерывателя-распределителя прокладку;
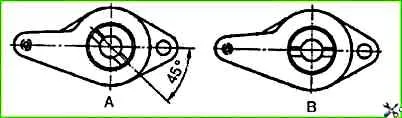
- - повернуть валик привода в положение, показанное на рис. 13, а, и поставить привод в гнездо блока цилиндров.
При введении привода в гнездо необходимо поворачивать валик масляного насоса, чтобы конец валика привода вошел в отверстие вала насоса
В правильно установленном приводе прорезь во втулке валика должна быть направлена параллельно оси двигателя и смещена от двигателя, как показано на рис. 13, б;
- - закрепить привод;
- - проверить наличие зазора в винтовых шестернях распределительного вала и привода прерывателя-распределителя.
Если по какой-либо причине с двигателя был снят только один привод прерывателя-распределителя, его можно установить, не снимая поддона картера.
В этом случае, установив поршень первого цилиндра в в. м. т. хода сжатия, при установке привода слегка поворачивать коленчатый вал в ту или иную сторону.
При правильно установленном приводе, когда поршень первого цилиндра находится в ВМТ. хода сжатия, ротор прерывателя-распределителя займет положение против первого контакта, помеченного цифрой 1 на крышке прерывателя-распределителя;
- положить на фланец блока цилиндров прокладку поддона картера;
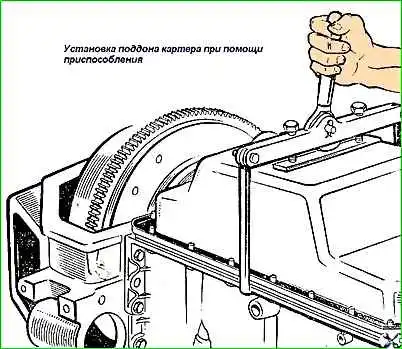
- - установить подсобранный поддон на шпильки, прижать с помощью приспособления (рис. 14) к блоку и закрепить гайками с шайбами;
- - установить и привернуть болтами нижнюю часть картера сцепления;
- - очистить камеры сгорания головки цилиндров от нагара, протереть и продуть сжатым воздухом. Если необходимо, прочистить отверстия в водораспределительной трубе для чего ее вынуть, как показано на рис. 15;
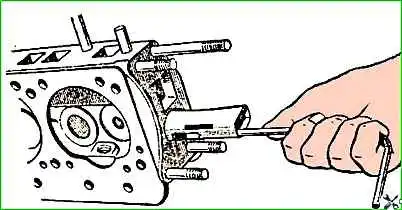
- - притереть клапаны, для этого необходимо:
- - нанести на притираемую поверхность седла клапана тонкий слой смеси, составленной из одной части порошка М-20 (ГОСТ 3647-59) и двух частей масла индустриального 20 (веретенного 3) (ГОСТ 1707-51). Перед употреблением смесь тщательно перемешать;
надеть на стержень клапана технологическую пружину, вставить клапан в направляющую втулку.
Внутренний диаметр пружины должен быть около 10 мм.
Усилие пружины небольшое; она должна слегка приподнимать клапан над седлом. При легком нажатии клапан должен садиться на седло;
- - прижать резиновый присосок к верхней плоскости головки клапана. Поверхности присоса и клапана должны быть сухими и совершенно чистыми;
- - вращая ручку присоска поочередно то в одну, то в другую сторону и одновременно перемещая клапан вверх и вниз, добиться на рабочих поверхностях седла и головки равномерной матовой фаски на всей окружности.
Перед началом притирки следует проверить, нет ли коробления головки клапана и пригорания клапана и седла.
При наличии этих дефектов восстановить герметичность клапана одной притиркой невозможно и следует сначала прошлифовать седло, а поврежденный клапан заменить новым.
Если зазор между клапаном и втулкой превышает 0,25 мм, то герметичность, также не может быть восстановлена, в этом случае клапан и втулку следует заменить новыми.
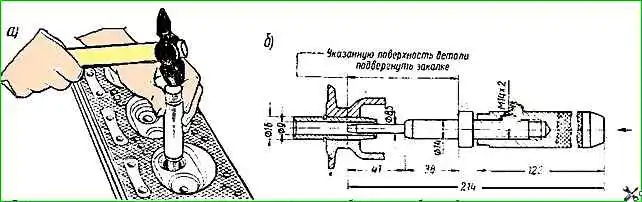
Клапаны (в запасные части) выпускаются стандартного размера, а направляющие втулки — с внутренним - диаметром, уменьшенным на 0,3 мм (для развертывания их под окончательный размер после запрессовки в головку цилиндров).
Выпрессовка изношенной направляющей втулки производится с помощью выколотки (рис. 16). С
едла клапанов удаляются фрезерованием твердосплавным зенкером.
Ремонтные седла имеют наружный диаметр на 0,25 мм больше, чем стандартные, поэтому гнезда для седел растачиваются до размеров:
- для седла впускного клапана — 47,25+0,027мм и для выпускного - 38,75+0,027мм.
Седла клапанов и направляющие втулки перед сборкой надо охладить в двуокиси углерода (сухом льду), а головку цилиндров нагреть о температуры 160—175°С.
Седла и втулка при сборке должны вставляться в гнезда головки цилиндров свободно или с легким усилием.
После установки седла металл головки цилиндров при помощи плоской оправки диаметром 49 или 41 мм, соответственно, центрируемой по отверстию в седле, завальцовывается вокруг седла.
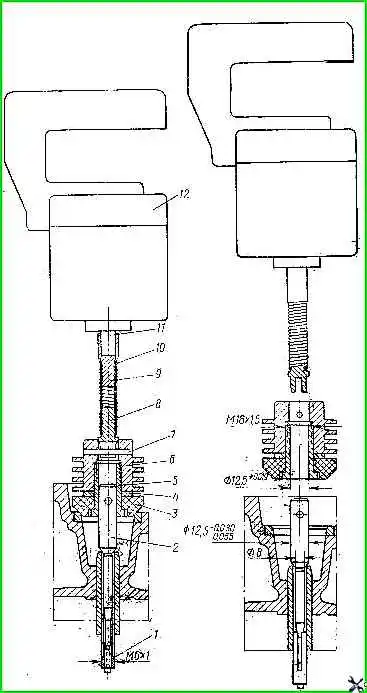
Запрессовка новой втулки производится со стороны коромысел с помощью выколотки.
Втулка после запрессовки должна выступать над плоскостью головки цилиндров на 22 мм.
После запрессовки развернуть, отверстие втулки до диаметра 9+0,022 мм, а фаски седел прошлифовать, центрируя по отверстию во втулке.
Для шлифовки седел можно использовать приспособление, показанное на рис. 17.
Разжимная оправка устанавливается в обработанное отверстие во втулке, а хвостовик оправки служит осью для шлифовального круга с фаской под углом 45°.
Привод шлифовального круга осуществляется небольшим электродвигателем.
При шлифовке следует обеспечить концентричность фаски на седле клапана с отверстием во втулке в пределах 0,03 мм общих показаний индикатора.
Фаски шлифуют под углом 45°. Наружный диаметр «d» (рис. 16) фаски у седла для впускного клапана должен быть 46 мм, а у выпускного — 35 мм.
Ширина фаски «в» должна быть у седла впускного клапана 1,8-2,3 мм, у выпускного — 2,3-2,5 мм.
Ширина фаски обеспечивается расшлифовкой отверстия седла под углом 30°, как показано на рис. 18, а.
При шлифовке изношенных седел наружный диаметр фаски получается больше указанных выше размеров. В этом случае наружный диаметр фаски доводят до необходимого шлифовкой торца седла под углом 30°, как указано на рис. 18, б.
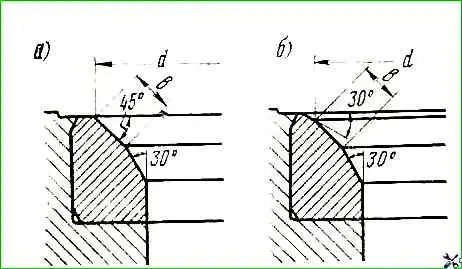
После шлифовки седел и притирке клапанов все газовые каналы тщательно очистить и продуть сжатым воздухом, чтобы не осталось абразивной пыли.
Стержни клапанов перед сборкой смазываются смесью, состоящей из семи частей масляного коллоидно-графитового препарата (ГОСТ 5262—50) и трех частей авиационного масла МС-20;
- - вставить клапаны во втулки согласно сделанным меткам и собрать их с пружинами. Убедиться, что выступы сухарей вошли в кольцевую канавку стержня клапана;
- - надеть на шпильки головки цилиндров прокладку, установить головку и закрепить ее гайками с шайбами. Затянуть гайки динамометрическим ключом с моментом 7,3-7,8 кГм, соблюдая порядок, указанный на рис. 20;
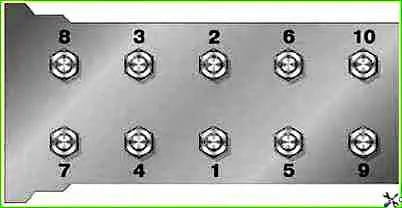
- прочистить проволокой и продуть сжатым воздухом отверстия в коромыслах, в оси коромысел и регулировочных винтах, отверстие в задней стойке оси коромысел и в головке цилиндров.
Проверить надежность посадки втулок коромысел.
В случае слабой посадки во время работы втулка может сместиться и перекрыть отверстие смазки штанги толкателя клапана. Такие втулки необходимо заменить;
- произвести подсборку оси коромысел. Перед постановкой каждого коромысла смазать его втулку маслом для двигателя.
Коромысла и стойки собираются на оси в таком положении, чтобы смещение отверстий под шпильки крепления в стойках было обращено к регулировочным винтам коромысел.
Четвертая (задняя) стойка должна иметь на нижней плоскости отверстие для прохода масла;
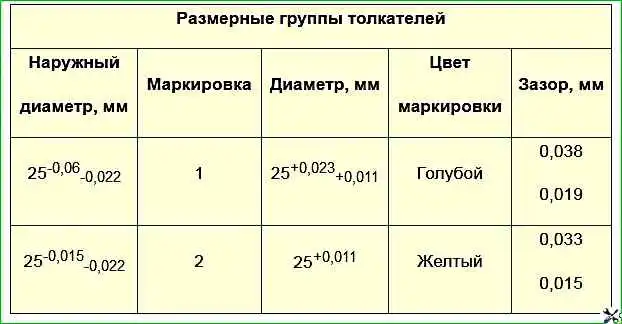
- - вставить толкатели в гнезда согласно меткам на них. Толкатели и отверстия в блоке предварительно смазать маслом для двигателя;
- - вставить штанги в сборе с наконечниками в отверстия в головке цилиндров;
- - установить подсобранную ось коромысел на шпильки и закрепить гайками с шайбами. Регулировочные винты своей сферической частью должны ложиться на сферу верхнего наконечника штанги;
- - установить зазоры между торцом стержня средних клапанов и носком коромысла 0,35-0,40 мм, а крайних клапанов (выпускных первого и четвертого цилиндров) — 0,30-0,35 мм. Сделать это надо, как указано в статье «Регулировка зазоров клапанов»;
- - поставить прокладку и крышку коромысел и закрепить их винтами с шайбами;
- - смазать и надеть на переднюю крышку коробки передач муфту выключения сцепления в сборе с подшипником и закрепить оттяжную пружину;
- - поставить и закрепить коробку передач;
- - поставить вилку выключения сцепления;
- - поставить детали и агрегаты двигателя, соблюдая обратную последовательность.