Before assembling the engine, all its parts must be cleaned of carbon deposits and tar deposits
You cannot wash parts made of aluminum alloys (cylinder block and head, pistons, etc.) in alkaline solutions, as these solutions corrode aluminum.
The following solutions are recommended for cleaning parts from carbon deposits:
For aluminum parts:
- Soda (Na2CO3) – 18.5 g
- Soap (green or laundry) – 10.0 g
- Liquid glass – 8.5 G
- Water – 1 l
For steel parts:
- Caustic soda (NaOH) – 25.0 g
- Soda (Na2CO3) – 33.0
- Soap (green or laundry) – 8.5 g
- Liquid glass – 1.5 g
- Water – 1l
When assembling the engine, observe the following conditions:
- - wipe all parts before assembly with a clean cloth and blow with compressed air, and lubricate all rubbing surfaces with clean oil;
- - inspect the parts before putting them in place (for cracks, chips, nicks in other defects), check the reliability of the fit of the parts pressed into it, defective parts must be repaired or replaced with new ones;
- - all threaded parts (studs, plugs, fittings), if they were unscrewed or replaced during the repair process, must be installed with red lead or white diluted with natural drying oil.
All permanent connections, such as cylinder block plugs, etc., must be installed with nitro varnish.
The following are not allowed for installation on the engine:
- - used cotter pins, cotter wire and locking plates;
- - spring washers that have lost their elasticity;
- - damaged gaskets;
- - parts with more than two clogged or broken threads on the thread;
- - bolts and studs with elongated threads; bolts and nuts with worn edges.
Bolts and nuts must be properly tightened (with cotter pins, cotter wire, spring and special washers and locknuts).
Assemble the engine in the following order:
- - clean all mating surfaces of the cylinder block from gaskets stuck and torn during disassembly;
- - secure the cylinder block on the stand, unscrew the oil channel plug from the rear end and blow out all oil channels with compressed air. Screw the plug back into place;
- - if there is a need to replace the clutch housing or it is installed on the cylinder block after repair, it is necessary to first remove two alignment pins from the block, then secure the housing to the cylinder block with six bolts.
A crankshaft is installed in the cylinder block on the outer bearings, to the flange of which the indicator stand is attached.
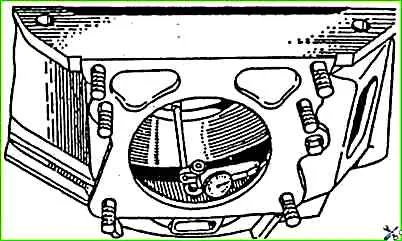
By rotating the crankshaft, check the runout of the hole for the centering collar of the gearbox, as well as the perpendicularity of the rear end of the clutch housing relative to the axis of the crankshaft, as shown in Fig. 1 and fig. 2.
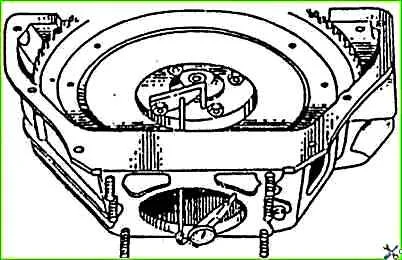
The runout of the crankcase and end holes should not exceed 0.08 mm.
If the hole runout exceeds the specified value, you should loosen the bolts securing the crankcase to the cylinder block and lightly hit the crankcase flange to ensure its correct installation;
- - after tightening the bolts, the holes for the dowel pins in the clutch housing and cylinder block are expanded to repair size. The diameter of the hole must be such that no blackness remains in the expanded holes.
After this, pins are pressed into the holes, the diameter of which is 0.015-0.051 mm larger than the size of the holes;
- - runout of the crankcase end is eliminated by scraping. It should be borne in mind that during the above-described check it is necessary to use an unworn crankshaft and bearings. If parts are worn out, the results will be incorrect;
- - remove the crankshaft;
- - replace (if necessary) the cylinder liners with new ones as follows:
- - use a puller (Fig. 3) to remove the old sleeve from the block;
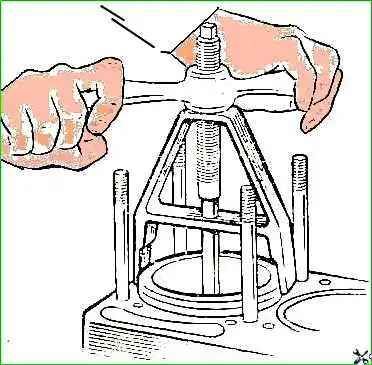
- - clean thoroughly protect the seating surfaces and sealing surfaces on the liner and in the cylinder block from scale and corrosion;
- - insert a new or repaired sleeve with a red copper gasket on it. The liner should fit into the cylinder block freely, without effort;
- - secure the sleeve with a holder to prevent it from falling out.
Note. When replacing defective or worn liners with new or repaired ones, their position in the cylinder block is not oriented.
In other cases, before removing the liners from the cylinder block, it is necessary to mark them with serial numbers (count from the water pump and gearbox), and also mark their position in the cylinder block in order to ensure their installation in the previous position during assembly.
When using worn cylinder liners, as well as each time new piston rings are installed in worn liners, it is necessary to bore the unworn belt above the upper compression ring on a machine or with a scraper.
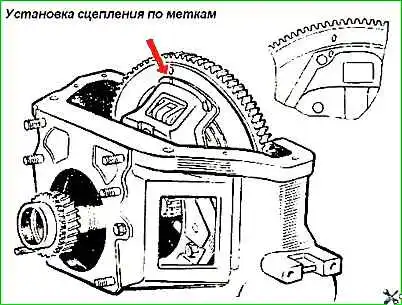
The metal must be removed flush with the worn part of the sleeve;
- cut off two oil seal packings for the rear main bearing of the crankshaft (each 120 mm long), insert them into the block and oil seal holder;
Assemble the crankshaft:
- - unscrew all plugs of dirt traps of the connecting rod journals and remove deposits from them. Rinse and blow out the oil channels and cavities of the dirt traps with compressed air, tighten and seal the plugs;
- - check the condition of the working surfaces of the shaft. Nicks, nadirs and other external defects are not allowed;
- - lubricate with refractory grease 1-13 and press the gearbox drive shaft bearing into the rear end of the crankshaft;
- - screw the flywheel to the engine crankshaft with a torque wrench (nut tightening torque 7.6-8.3 kgm); tighten the nuts;
- screw the clutch pressure plate assembly with housing to the flywheel, having previously centered the driven disc using a mandrel (you can use the transmission drive shaft) along the hole in the bearing in the rear end of the crankshaft.
The “O” marks stamped on the pressure plate and flywheel housing near one of the holes for the housing mounting bolts (Fig. 4) must be aligned.
Put the clutch driven disc in such a position that the damper faces the flywheel.
The crankshaft, flywheel and clutch are balanced as an assembly, so dynamic balancing should be performed when replacing one of these parts. The imbalance should not exceed 70 Gsm.
When balancing, removing excess weight from the heavy side is done by drilling out the flywheel metal at a radius of 151 mm with a drill with a diameter of 10 mm to a depth of no more than 12 mm.
The distance between the centers of drillings must be at least 14 mm.
Balancing of the unit should not begin if the initial imbalance exceeds 180 Gcm.
In this case, it is necessary to disassemble the unit and check the balancing of each part separately;
- place the rear thrust washer on the first main journal of the crankshaft with the babbitt side facing the shaft cheek;
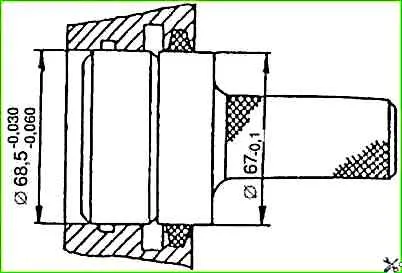
- compress the rear shaft seal. To do this, place a mandrel in the hole of the rear main bearing (Fig. 5), install the oil seal holder and tighten the bearing and holder nuts;
wipe the main bearing shells in their bed with a clean cloth and place the shells in the bed;
- - lubricate the main bearing shells and the crankshaft journal with clean engine oil and place the crankshaft in the cylinder block;
- - put the main bearing caps on the cylinder block studs so that the locking lugs on the upper and lower liners of each cap are on one side, and the numbers stamped on the caps correspond to the bed numbers stamped on the cylinder block near the studs.
When installing the front bearing cap, the tab of the rear crankshaft thrust bearing washer must fit into the groove of the cap. The end of the front bearing cap must be in the same plane with the end of the cylinder block;
- - put the main bearing caps in place by lightly tapping with a rubber hammer; the covers must fit into the grooves of the block beds;
- - screw on the nuts securing the covers and tighten them evenly, having previously installed the locking plate. The final tightening must be done with a torque wrench (torque 10-11 kgm), bend the locking plate antennae;
- - install in the grooves of the holders To seal the seal, coat the rubber gaskets and their side surface protruding from the groove with soapy water. Place the oil seal holder in place and tighten the nuts;
- - turn the crankshaft, which should rotate freely with little effort.
You can rotate the crankshaft using the flywheel or using a device consisting of a gearbox drive shaft with a tetrahedron wrench welded to it or a handle with a square hole.
The device can also be used for centering when installing the driven and pressure disks of the clutch;
- - place the front washer of the thrust bearing with the babbitt side facing the shaft so that the pins pressed into the cylinder block and cover fit into the grooves of the washer;
- - place the crankshaft steel thrust washer with its unworn surface against the Babbitt-coated surface of the front thrust bearing washer;
- - press the crankshaft gear all the way and check the axial clearance of the crankshaft.
The check is carried out as follows: place a screwdriver (wrench, hammer handle, etc.) between the first crank of the shaft towards the front wall of the cylinder block and, using it as a lever, press the shaft towards the rear end of the engine.
Using a feeler gauge, determine the gap between the end of the rear washer of the thrust bearing and the plane of the shoulder of the first main journal. The gap should be in the range of 0.075-0.175 mm;
subassemble the connecting rod and piston group:
clean the piston heads and grooves for the piston rings from carbon deposits, as shown in Fig. 6;
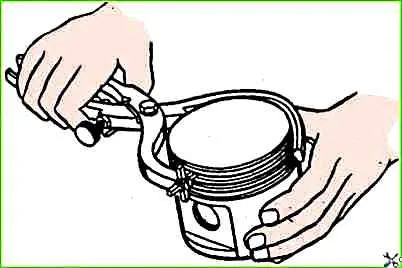
- - in case of replacing a piston, piston pin or connecting rod, you must:
- - remove the piston pin retaining rings using pliers;
- - remove the piston pin from the device (the piston rings must be removed before doing this);
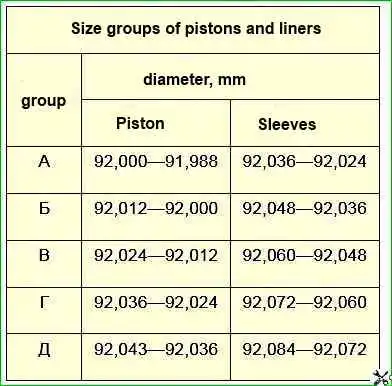
- select new pistons using liners with a gap of 0.012-0.024 mm.
The selection is checked by pulling using a spring balance gauge tape placed between the piston and cylinder.
The dipstick is located in a plane perpendicular to the piston pin axis.
The piston must be without piston rings.
The pulling force at normal room temperature (+20°C) should be in the range of 3.5-4.5 kg.
Tape dimensions: thickness -0.05 mm, width - 13 mm, length - 250 mm;
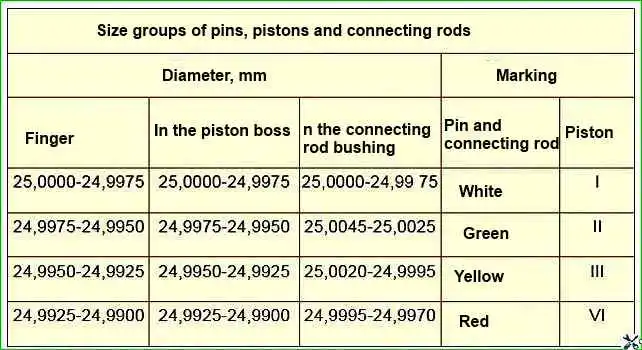
- select the piston pin to the connecting rod so that at normal room temperature it moves smoothly in the hole of the upper head under a light force of the thumb.
The piston pin should be lightly lubricated with oil.
The color of the pin markings must match the color of the markings on the piston bosses;
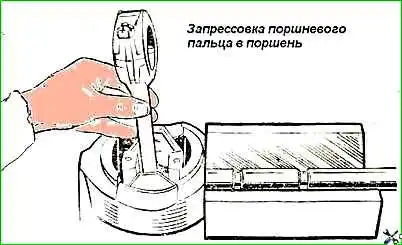
- subassemble the connecting rod and piston group on the device (Fig. 7).
Before pressing the piston pin into it, the piston must be heated in hot water to a temperature of 70°C; Pressing a finger onto a cold piston can damage the surface of the holes in the piston bosses, as well as deform the piston itself.
Insert the piston pin retaining rings into the annular grooves of the piston bosses;
- select piston rings for the cylinder; gap; measured at the joint of the ring using a feeler gauge, should be 0.3-0.5 mm.
In worn cylinders, the smallest gap should be 0.3 mm;
- use a feeler gauge to check the lateral clearance between the ring and the wall of the piston groove (Fig. 8). Check the circumference of the piston at several points.
The amount of side clearance should be in the range of 0.050-0.082 mm for the upper compression ring, and 0.035-0.067 mm for the lower compression and oil scraper rings;
- - put the piston rings on the piston using the device. Compresssion rings are placed with an internal chamfer to the piston bottom, as shown in Fig. 12, the rings in the grooves must move freely;
- - wipe the beds of the connecting rods and their covers with a napkin, wipe and insert the liners into them;
- - turn the crankshaft so that the cranks of the first and fourth cylinders take a position corresponding to the bottom dead center;
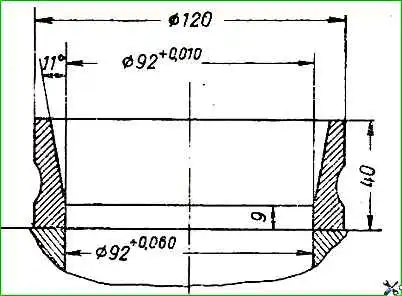
- lubricate the liners, piston, connecting rod journal of the shaft and liner of the first cylinder with clean engine oil, spread the joints of the piston rings at an angle of 120° to each other, put safety brass tips on the connecting rod bolts, compress the rings using a crimp or using a cone ring ( Fig. 9), insert the piston into the cylinder.
Before installing the piston, you should once again make sure that the numbers stamped on the connecting rod and its cover correspond to the serial number of the cylinder, check the correct position of the piston and connecting rod in the cylinder; the mark on the piston “Back” should be directed towards the flywheel, and the hole in the lower head of the connecting rod should be in the direction opposite to the camshaft;
- pull the connecting rod by the lower head to the connecting rod journal, remove the brass tips from the bolts, put on the connecting rod cover so that the numbers stamped on the cover and connecting rod face the same direction.
Tighten the nuts with a torque wrench (torque 6.8-4.5 kgm) and secure using a lock nut stamped from sheet steel. The tightening torque of the lock nut is 0.3-0.5 kgm;
- insert the piston of the fourth cylinder in the same order, then turn the crankshaft 180° and insert the pistons of the second and third cylinders.
Rotate the crankshaft several times, which should rotate easily with little effort;
subassemble the camshaft:
- - place a spacer sleeve and thrust flange on the front end of the camshaft;
- - press the timing gear onto the shaft and secure it with a bolt and washer;
- - using a feeler gauge inserted between the camshaft thrust flange and the camshaft hub, check the axial clearance of the camshaft, which should be within 0.1-0.2 mm;
- - clean the tube for lubrication of the timing gears and screw it to the block using a bolt and clamp;
- - insert the assembled distribution hall into the hole of the block, having first lubricated its support journals with engine oil.
When the gears are engaged, the crankshaft gear tooth with the “O” mark must be against the grooves of the camshaft gear teeth (see Fig. 17). The lateral clearance in engagement should be in the range of 0.03-0.08 mm. If there is a larger or smaller gap, choose another pair;
- - through the holes in the camshaft gear, attach the thrust flange to the block with two bolts and spring washers;
- - place the oil deflector on the journal of the front end of the crankshaft with the convex side facing the gear;
- - check the suitability for further operation of the oil seal pressed into the timing gear cover. If the oil seal has worn working edges or weakly covers the crankshaft pulley hub inserted into the oil seal, replace it with a new one.
It is recommended to press the oil seal into the cover using a mandrel on a press, as shown in Fig. 10;
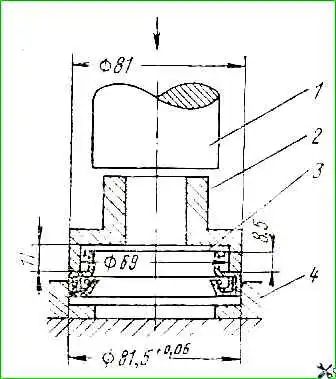
- put the gasket and timing gear cover on the studs;
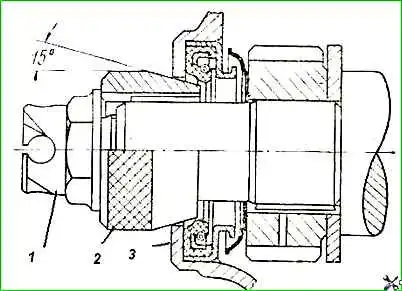
Center the cover along the front end of the crankshaft using a mandrel (Fig. 11) and tighten all the nuts and bolts securing the cover.
If there is no centering mandrel, the cover can be installed along the crankshaft pulley hub.
The hub must be pressed onto the crankshaft so that its end fits 5 mm into the hole in the cover.
After this, secure the cover with nuts, maintaining the same gap around the circumference between the hub and the cover hole.
The gap should be leveled by lightly hitting the cover with a wooden or rubber hammer. After This will finally secure the lid;
remove the centering mandrel and press on the crankshaft pulley hub;
- - screw the ratchet into the crankshaft, after putting a spring washer on it.
Turning the crankshaft using the ratchet, check whether the reflector is touching the timing gear cover due to a bent reflector or a loose fit on the hub;
- - screw the crankshaft pulley to the hub;
- - install the oil pump assembly with the oil receiver;
- - install the breaker-distributor drive;
- - turning the crankshaft, align the mark in. m.t. on the rim of the crankshaft pulley with a pointer on the timing gear cover (see Fig. 14).
The camshaft cams actuating the valves of the first cylinder must be directed with their apexes in the direction opposite to the pushers (towards the oil pan) and located symmetrically, as shown in Fig. 12;
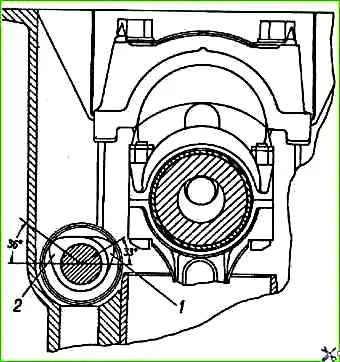
- check the axial clearance of the drive shaft using a feeler gauge inserted between the drive housing and the gear.
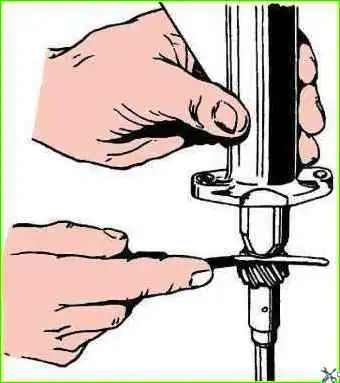
The gap should be within 0.15-0.40 mm;
Place a gasket on the mounting studs of the breaker-distributor drive;
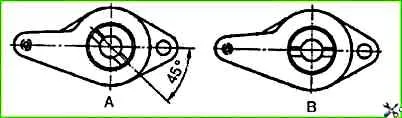
- - turn the drive shaft to the position shown in Fig. 13, a, and place the drive in the cylinder block socket.
When inserting the drive into the socket, it is necessary to turn the oil pump shaft so that the end of the drive shaft enters the hole in the pump shaft
In a correctly installed drive, the slot in the shaft bushing should be parallel to the motor axis and offset from the motor, as shown in Fig. 13, b;
- - secure the drive;
- - check for clearance in the helical gears of the camshaft and the chopper-distributor drive.
If for any reason only one distributor-interruptor drive was removed from the engine, it can be installed without removing the oil pan.
In this case, installing the piston of the first cylinder in c. m.t. compression stroke, when installing the drive, slightly turn the crankshaft in one direction or another.
When the drive is correctly installed, when the piston of the first cylinder is at TDC. compression stroke, the rotor of the breaker-distributor will take a position opposite the first contact marked with the number 1 on the cover of the breaker-distributor;
- place the oil pan gasket on the cylinder block flange;
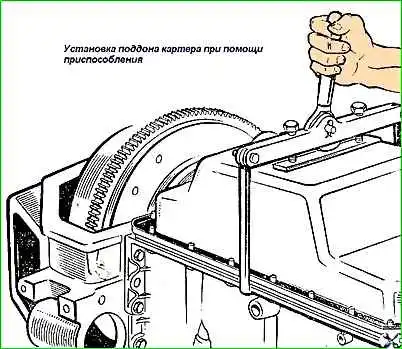
- - install the assembled pallet on the studs, press it using the device (Fig. 14) to the block and secure with nuts and washers;
- - install and bolt the lower part of the clutch housing;
- - clean the combustion chambers of the cylinder heads from carbon deposits, wipe and blow with compressed air. If necessary, clean the holes in the water distribution pipe and remove it, as shown in Fig. 15;
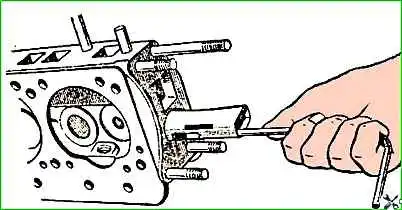
- - lap the valves, for this you need:
- - apply a thin layer of a mixture composed of one part M-20 powder (GOST 3647-59) and two parts industrial oil 20 (spindle 3) (GOST 1707-51) to the ground surface of the valve seat. Before use, mix the mixture thoroughly;
put technol on the valve stem logical spring, insert the valve into the guide sleeve.
The inner diameter of the spring should be about 10 mm.
The spring force is small; it should lift the valve slightly above the seat. When pressed lightly, the valve should seat on the seat;
- - press the rubber suction cup to the upper plane of the valve head. The surfaces of the suction cup and valve must be dry and completely clean;
- - by rotating the suction cup handle alternately in one direction or the other and simultaneously moving the valve up and down, achieve a uniform matte chamfer on the working surfaces of the seat and head along the entire circumference.
Before starting grinding, you should check for warping of the valve head and burning of the valve and seat.
If these defects are present, it is impossible to restore the tightness of the valve by grinding alone and the seat must first be ground and the damaged valve replaced with a new one.
If the gap between the valve and the bushing exceeds 0.25 mm, then the tightness cannot be restored either, in this case the valve and the bushing should be replaced with new ones.
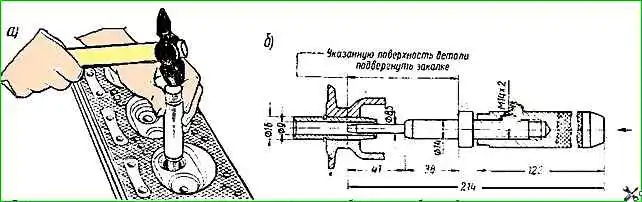
Valves (for spare parts) are produced in a standard size, and guide bushings are produced with an internal diameter reduced by 0.3 mm (to deploy them to the final size after pressing into the cylinder head).
The worn guide bushing is pressed out using a drift (Fig. 16). S
Valve seats are removed by milling with a carbide countersink.
Repair saddles have an outer diameter 0.25 mm larger than standard ones, so seat sockets are bored to size:
- for the intake valve seat - 47.25+0.027mm and for the exhaust valve - 38.75+0.027mm.
Valve seats and guide bushings must be cooled in carbon dioxide (dry ice) before assembly, and the cylinder head must be heated to a temperature of 160-175°C.
During assembly, the seats and bushing should be inserted into the cylinder head sockets freely or with light force.
After installing the seat, the metal of the cylinder head is rolled around the seat using a flat mandrel with a diameter of 49 or 41 mm, respectively, centered along the hole in the seat.
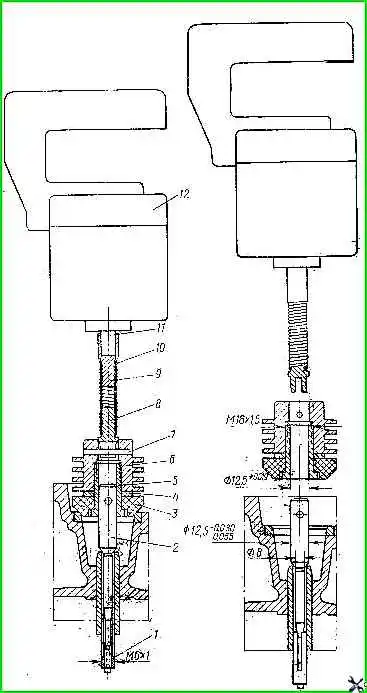
The new bushing is pressed in from the rocker arm side using a drift.
After pressing, the bushing should protrude above the plane of the cylinder head by 22 mm.
After pressing, expand the bushing hole to a diameter of 9+0.022 mm, and grind the chamfers of the seats, centering them along the hole in the bushing.
To grind the seats, you can use the device shown in Fig. 17.
The expanding mandrel is installed in the machined hole in the sleeve, and the shank of the mandrel serves as an axis for the grinding wheel with a chamfer at an angle of 45°.
The grinding wheel is driven by a small electric motor.
When grinding, ensure that the chamfer on the valve seat is concentric with the hole in the bushing within 0.03 mm of the total indicator reading.
The chamfers are ground at an angle of 45°. The outer diameter “d” (Fig. 16) of the chamfer at the seat for the inlet valve should be 46 mm, and at the exhaust valve - 35 mm.
The width of the chamfer “b” should be 1.8-2.3 mm at the intake valve seat, and 2.3-2.5 mm at the exhaust valve seat.
The width of the chamfer is ensured by grinding the seat hole at an angle of 30°, as shown in Fig. 18, a.
When grinding worn seats, the outer diameter of the chamfer becomes larger than the dimensions indicated above. In this case, the outer diameter of the chamfer is brought to the required size by grinding the end of the seat at an angle of 30°, as shown in Fig. 18, b.
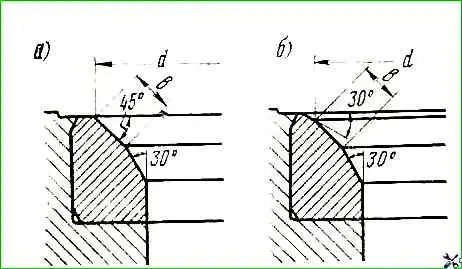
After grinding the seats and grinding the valves, thoroughly clean all gas channels and blow them with compressed air so that no abrasive dust remains.
Before assembly, the valve stems are lubricated with a mixture consisting of seven parts of an oil colloidal graphite preparation (GOST 5262-50) and three parts of MS-20 aviation oil;
- - insert the valves into the bushings according to the instructions along the marks and assemble them with the springs. Make sure that the projections of the cotters fit into the annular groove of the valve stem;
- - put a gasket on the cylinder head studs, install the head and secure it with nuts and washers. Tighten the nuts with a torque wrench to a torque of 7.3-7.8 kgm, following the order shown in Fig. 20;
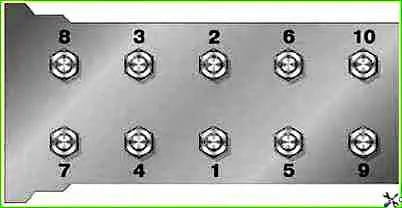
- clean with wire and blow out with compressed air the holes in the rocker arms, in the rocker arm axle and adjusting screws, the hole in the rear post of the rocker arm axle and in the cylinder head.
Check that the rocker arm bushings are securely seated.
If the fit is loose during operation, the bushing may move and block the lubrication hole of the valve lifter rod. Such bushings must be replaced;
- perform subassembly of the rocker arm axis. Before installing each rocker arm, lubricate its bushing with engine oil.
The rocker arms and struts are assembled on the axle in such a position that the offset of the holes for the mounting studs in the struts faces the rocker arm adjusting screws.
The fourth (rear) rack must have a hole on the bottom plane for oil passage;

- - insert the pushers into the sockets according to the marks on them. Pre-lubricate the pushers and holes in the block with engine oil;
- - insert the rod assembly with tips into the holes in the cylinder head;
- - install the assembled rocker arm axle on the studs and secure with nuts and washers. The adjusting screws with their spherical part should rest on the sphere of the upper tip of the rod;
- - set the gaps between the end of the middle valve stem and the toe of the rocker arm to 0.35-0.40 mm, and the outer valves (exhaust of the first and fourth cylinders) to 0.30-0.35 mm. This must be done as indicated in the article “Adjusting valve clearances”;
- - place the gasket and rocker cover and secure them with screws and washers;
- - lubricate and place the clutch release clutch assembly with bearing on the front cover of the gearbox and secure the release spring;
- - install and secure the gearbox;
- - install the clutch release fork;
- - install engine parts and assemblies in reverse order.