Antes de montar el motor se deben limpiar todas sus piezas de depósitos de carbón y alquitrán
No se pueden lavar piezas fabricadas con aleaciones de aluminio (bloque y culata de cilindros, pistones, etc.) en soluciones alcalinas, ya que estas soluciones corroen el aluminio.
Se recomiendan las siguientes soluciones para limpiar piezas de depósitos de carbón:
Para piezas de aluminio:
- Refresco (Na2CO3) – 18,5 g
- Jabón (verde o de lavandería) – 10,0 g
- Vaso líquido – 8,5 G
- Agua – 1 litro
Para piezas de acero:
- Sosa cáustica (NaOH) – 25,0 g
- Refrescos (Na2CO3) – 33,0
- Jabón (verde o de lavandería) – 8,5 g
- Vaso líquido – 1,5 g
- Agua – 1l
Al ensamblar el motor, observe las siguientes condiciones:
- - limpie todas las piezas antes del montaje con un paño limpio y sople con aire comprimido, y lubrique todas las superficies de fricción con aceite limpio;
- - inspeccionar las piezas antes de colocarlas en su lugar (en busca de grietas, astillas, mellas en otros defectos), comprobar la fiabilidad del ajuste de las piezas prensadas, las piezas defectuosas deben repararse o sustituirse por otras nuevas;
- - todas las piezas roscadas (pernos, tapones, racores), si fueron desatornilladas o reemplazadas durante el proceso de reparación, deben instalarse con mina roja o blanca diluida con aceite secante natural.
Todas las conexiones permanentes, como tapones de bloque de cilindros, etc., deben instalarse con barniz nitro.
No se permite la instalación de lo siguiente en el motor:
- - pasadores de chaveta, alambre de chaveta y placas de bloqueo usados;
- - arandelas elásticas que han perdido su elasticidad;
- - juntas dañadas;
- - piezas con más de dos hilos obstruidos o rotos en el hilo;
- - pernos y espárragos con roscas alargadas; Pernos y tuercas con bordes desgastados.
Los pernos y tuercas deben estar correctamente apretados (con pasadores, chaveta, resorte y arandelas y contratuercas especiales).
Monte el motor en el siguiente orden:
- - limpie todas las superficies de contacto del bloque de cilindros de juntas pegadas y rotas durante el desmontaje;
- - fije el bloque de cilindros en el soporte, desenrosque el tapón del canal de aceite del extremo trasero y sople todos los canales de aceite con aire comprimido. Vuelva a atornillar el tapón;
- - si es necesario reemplazar la carcasa del embrague o si está instalada en el bloque de cilindros después de la reparación, primero es necesario quitar dos pasadores de alineación del bloque y luego asegurar la carcasa al bloque de cilindros con seis pernos.
Se instala un cigüeñal en el bloque de cilindros sobre los cojinetes exteriores, a cuya brida se fija el soporte del indicador.
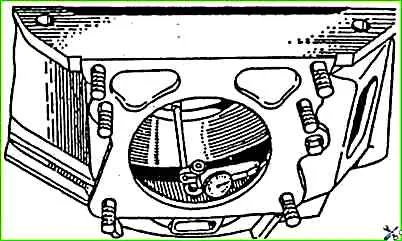
Al girar el cigüeñal, verifique el descentramiento del orificio para el collar de centrado de la caja de cambios, así como la perpendicularidad del extremo trasero de la carcasa del embrague con respecto al eje del cigüeñal, como se muestra en la Fig. 1 y fig. 2.
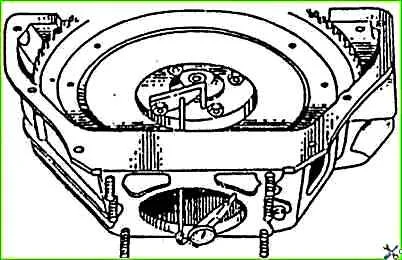
El descentramiento del cárter y de los orificios finales no debe exceder los 0,08 mm.
Si el descentramiento del orificio excede el valor especificado, se deben aflojar los tornillos que sujetan el cárter al bloque de cilindros y golpear ligeramente la brida del cárter para asegurar su correcta instalación;
- - después de apretar los pernos, los orificios para las clavijas en la carcasa del embrague y el bloque de cilindros se expanden hasta el tamaño de reparación. El diámetro del agujero debe ser tal que no quede nada negro en los agujeros expandidos.
Después de esto, se presionan pasadores en los orificios, cuyo diámetro es 0,015-0,051 mm mayor que el tamaño de los orificios;
- - El descentramiento del extremo del cárter se elimina mediante raspado. Hay que tener en cuenta que durante la comprobación descrita anteriormente es necesario utilizar un cigüeñal y cojinetes en buen estado. Si las piezas están desgastadas, los resultados serán incorrectos;
- - quitar el cigüeñal;
- - reemplace (si es necesario) las camisas de los cilindros por otras nuevas de la siguiente manera:
- - utilice un extractor (Fig. 3) para quitar el manguito viejo del bloque;
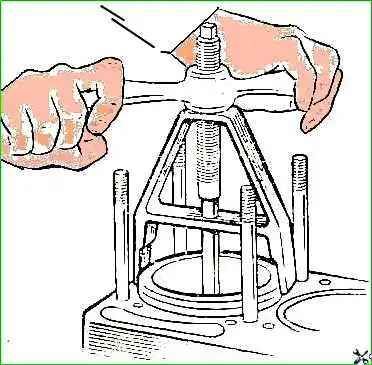
- - limpiar a fondo proteger las superficies de asiento y de sellado de la camisa y del bloque de cilindros contra las incrustaciones y la corrosión;
- - inserte un manguito nuevo o reparado con una junta de cobre roja. La camisa debe encajar libremente en el bloque de cilindros, sin esfuerzo;
- - fije la funda con un soporte para evitar que se caiga.
Nota. Al reemplazar camisas defectuosas o desgastadas por otras nuevas o reparadas, su posición en el bloque de cilindros no está orientada.
En otros casos, antes de retirar las camisas del bloque de cilindros, es necesario marcarlas con números de serie (contar desde la bomba de agua y la caja de cambios), y también marcar su posición en el bloque de cilindros para asegurar su instalación. en la posición anterior durante el montaje.
Cuando se utilizan camisas de cilindro desgastadas, así como cada vez que se instalan anillos de pistón nuevos en camisas desgastadas, es necesario perforar la correa no gastada por encima del anillo de compresión superior en una máquina o con un raspador.
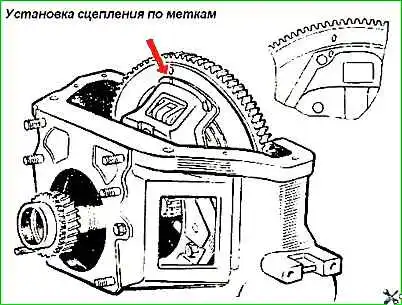
El metal debe retirarse a ras de la parte desgastada del manguito;
- cortar dos empaquetaduras de retén de aceite para el cojinete principal trasero del cigüeñal (cada uno de 120 mm de largo), insertarlos en el bloque y en el soporte del retén de aceite;
Montar el cigüeñal:
- - desenrosque todos los tapones de los colectores de suciedad de los muñones de biela y elimine los depósitos que contengan. Enjuague y sople los canales de aceite y las cavidades de los colectores de suciedad con aire comprimido, apriete y selle los tapones;
- - comprobar el estado de las superficies de trabajo del eje. No se permiten mellas, nadires y otros defectos externos;
- - lubrique con grasa refractaria 1-13 y presione el cojinete del eje de transmisión de la caja de cambios en el extremo trasero del cigüeñal;
- - atornillar el volante al cigüeñal del motor con una llave dinamométrica (par de apriete de la tuerca 7,6-8,3 kgm); apretar las tuercas;
- Atornille el conjunto del plato de presión del embrague con carcasa al volante, habiendo centrado previamente el disco impulsado con un mandril (puede usar el eje de transmisión) a lo largo del orificio del cojinete en el extremo trasero del cigüeñal.
Las marcas "O" estampadas en la placa de presión y la carcasa del volante cerca de uno de los orificios para los pernos de montaje de la carcasa (Fig. 4) deben estar alineadas.
Coloque el disco accionado por el embrague en una posición tal que el amortiguador mire hacia el volante.
El cigüeñal, el volante y el embrague se equilibran como un conjunto, por lo que se debe realizar un equilibrio dinámico al reemplazar una de estas piezas. El desequilibrio no debe exceder los 70 Gsm.
Al equilibrar, la eliminación del exceso de peso del lado pesado se realiza perforando el metal del volante en un radio de 151 mm con un taladro con un diámetro de 10 mm hasta una profundidad de no más de 12 mm.
La distancia entre los centros de las perforaciones debe ser de al menos 14 mm.
El equilibrio de la unidad no debe comenzar si el desequilibrio inicial supera los 180 Gcm.
En este caso, es necesario desmontar la unidad y comprobar el equilibrio de cada pieza por separado;
- coloque la arandela de empuje trasera en el primer muñón principal del cigüeñal con el lado babbitt hacia la mejilla del eje;
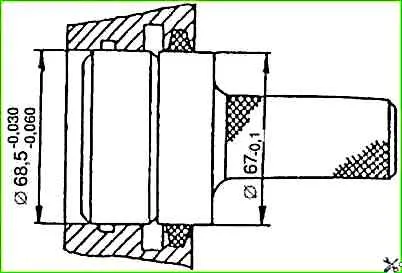
- comprimir el sello del eje trasero. Para ello, coloque un mandril en el orificio del cojinete principal trasero (Fig. 5), instale el soporte del retén de aceite y apriete las tuercas del cojinete y del soporte;
limpie los casquillos del cojinete principal en su base con un paño limpio y coloque los casquillos en la base;
- - lubrique los casquillos del cojinete de bancada y el muñón del cigüeñal con aceite de motor limpio y coloque el cigüeñal en el bloque de cilindros;
- - coloque las tapas de los cojinetes de bancada en los pernos del bloque de cilindros de modo que las orejetas de bloqueo en los revestimientos superior e inferior de cada tapa estén en un lado, y los números estampados en las tapas correspondan a los números de la base estampados en el bloque de cilindros. cerca de los montantes.
Al instalar la tapa del cojinete delantero, la lengüeta de la arandela del cojinete de empuje del cigüeñal trasero debe encajar en la ranura de la tapa. El extremo de la tapa del cojinete delantero debe estar en el mismo plano que el extremo del bloque de cilindros;
- - coloque las tapas de los cojinetes de bancada golpeándolas ligeramente con un martillo de goma; las fundas deben encajar en las ranuras de los bloques;
- - enroscar las tuercas que sujetan las tapas y apretarlas uniformemente, habiendo instalado previamente la placa de bloqueo. El apriete final debe realizarse con una llave dinamométrica (par de apriete 10-11 kgm), doblar las antenas de la placa de bloqueo;
- - instalar en las ranuras de los soportes Para sellar el sello, cubra las juntas de goma y su superficie lateral que sobresale de la ranura con agua y jabón. Coloque el soporte del sello de aceite en su lugar y apriete las tuercas;
- - girar el cigüeñal, que debe girar libremente con poco esfuerzo.
Puedes girar el cigüeñal usando el volante o usando un dispositivo que consiste en un eje de transmisión de la caja de cambios con una llave tetraédrica soldada o un mango con un orificio cuadrado.
El dispositivo también se puede utilizar para centrar al instalar los discos conducidos y de presión del embrague;
- - coloque la arandela delantera del cojinete de empuje con el lado babbitt hacia el eje de modo que los pasadores presionados en el bloque de cilindros y la tapa encajen en las ranuras de la arandela;
- - coloque la arandela de empuje de acero del cigüeñal con su superficie no desgastada contra la superficie recubierta de Babbitt de la arandela del cojinete de empuje delantero;
- - presione el engranaje del cigüeñal hasta el fondo y compruebe el juego axial del cigüeñal.
La verificación se realiza de la siguiente manera: coloque un destornillador (llave inglesa, mango de martillo, etc.) entre la primera manivela del eje hacia la pared frontal del bloque de cilindros y, utilizándolo como palanca, presione el eje hacia la parte trasera del motor.
Utilizando una galga de espesores, determine el espacio entre el extremo de la arandela trasera del cojinete de empuje y el plano del hombro del primer muñón principal. El espacio debe estar en el rango de 0,075 a 0,175 mm;
subensamblar el grupo biela y pistón:
limpie las cabezas de los pistones y las ranuras para los anillos de los depósitos de carbón, como se muestra en la Fig. 6;
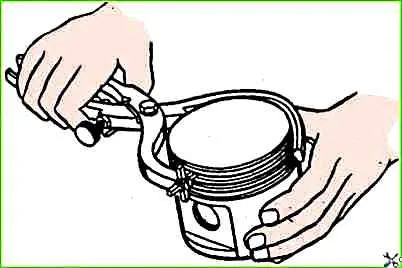
- - en caso de sustituir un pistón, bulón o biela, es necesario:
- - quitar los anillos de retención del pasador del pistón con unos alicates;
- - retire el pasador del pistón del dispositivo (los segmentos del pistón deben retirarse antes de hacer esto);
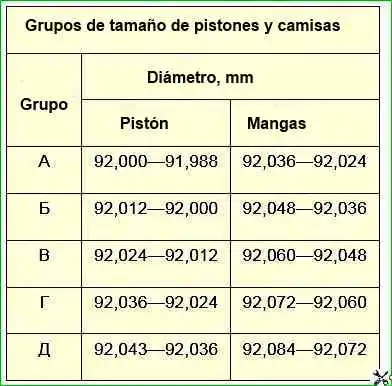
- seleccione pistones nuevos utilizando camisas con un espacio de 0,012-0,024 mm.
La selección se comprueba tirando con una cinta calibradora de equilibrio de resorte colocada entre el pistón y el cilindro.
La varilla de nivel está situada en un plano perpendicular al eje del pasador del pistón.
El pistón debe estar sin aros.
La fuerza de tracción a temperatura ambiente normal (+20 °C) debe estar en el rango de 3,5 a 4,5 kg.
Dimensiones de la cinta: espesor -0,05 mm, ancho - 13 mm, largo - 250 mm;
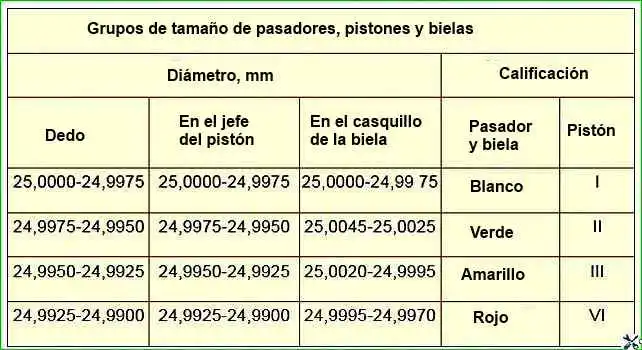
- seleccione el pasador del pistón en la biela de modo que, a temperatura ambiente normal, se mueva suavemente en el orificio del cabezal superior con una ligera fuerza del pulgar.
El pasador del pistón debe lubricarse ligeramente con aceite.
El color de las marcas de los pasadores debe coincidir con el color de las marcas en los jefes del pistón;
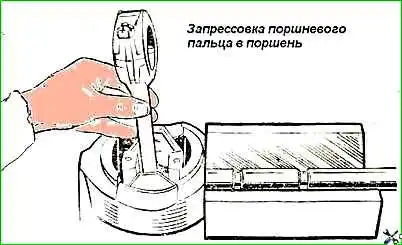
- submontar el grupo biela y pistón en el dispositivo (Fig. 7).
Antes de presionar el pasador del pistón, el pistón debe calentarse en agua caliente a una temperatura de 70°C; Presionar un pistón frío con el dedo puede dañar la superficie de los orificios de los resaltes del pistón, así como deformar el propio pistón.
Inserte los anillos de retención del pasador del pistón en las ranuras anulares de los resaltes del pistón;
- seleccionar anillos de pistón para el cilindro; brecha; medido en la unión del anillo con una galga de espesores, debe ser de 0,3 a 0,5 mm.
En cilindros desgastados, el espacio más pequeño debe ser de 0,3 mm;
- utilice una galga de espesores para comprobar el juego lateral entre el segmento y la pared de la ranura del pistón (Fig. 8). Compruebe la circunferencia del pistón en varios puntos.
La cantidad de espacio lateral debe estar en el rango de 0,050-0,082 mm para el anillo de compresión superior y de 0,035-0,067 mm para los anillos de compresión inferiores y raspadores de aceite;
- - coloque los anillos del pistón en el pistón usando el dispositivo. Comprimir Los anillos de presión se colocan con un bisel interno en la parte inferior del pistón, como se muestra en la Fig. 12, los anillos en las ranuras deben moverse libremente;
- - limpie los lechos de las bielas y sus cubiertas con una servilleta, limpie e inserte los revestimientos en ellas;
- - girar el cigüeñal de modo que las manivelas del primer y cuarto cilindro adopten una posición correspondiente al punto muerto inferior;
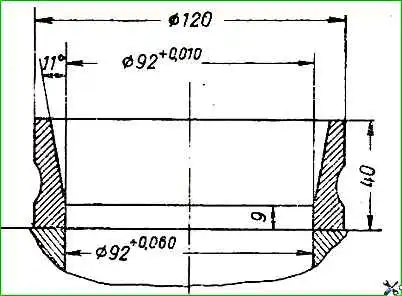
- lubrique las camisas, el pistón, el muñón de la biela del eje y la camisa del primer cilindro con aceite de motor limpio, separe las juntas de los segmentos del pistón en un ángulo de 120° entre sí, coloque puntas de latón de seguridad en las pernos de biela, comprimir los anillos usando un engarce o usando un anillo cónico (Fig. 9), inserte el pistón en el cilindro.
Antes de instalar el pistón, debe asegurarse una vez más de que los números estampados en la biela y su tapa correspondan al número de serie del cilindro, verifique la posición correcta del pistón y la biela en el cilindro; la marca en el pistón "Atrás" debe estar dirigida hacia el volante, y el orificio en la cabeza inferior de la biela debe estar en dirección opuesta al árbol de levas;
- tire de la biela por la cabeza inferior hasta el muñón de la biela, retire las puntas de latón de los pernos, coloque la tapa de la biela de modo que los números estampados en la tapa y la biela miren en la misma dirección.
Apriete las tuercas con una llave dinamométrica (par de apriete de 6,8 a 4,5 kgm) y asegúrelas con una contratuerca estampada en chapa de acero. El par de apriete de la contratuerca es de 0,3-0,5 kgm;
- inserte el pistón del cuarto cilindro en el mismo orden, luego gire el cigüeñal 180° e inserte los pistones del segundo y tercer cilindro.
Gire el cigüeñal varias veces, el cual debería girar fácilmente con poco esfuerzo;
subensamblar el árbol de levas:
- - colocar un casquillo espaciador y una brida de empuje en el extremo delantero del árbol de levas;
- - presione el engranaje de distribución sobre el eje y asegúrelo con un perno y una arandela;
- - utilizando una galga de espesores insertada entre la brida de empuje del árbol de levas y el cubo del árbol de levas, verifique el juego axial del árbol de levas, que debe estar entre 0,1 y 0,2 mm;
- - limpiar el tubo de lubricación de los engranajes de distribución y atornillarlo al bloque mediante un perno y una abrazadera;
- - introducir el distribuidor montado en el orificio del bloque, habiendo previamente lubricado sus muñones de soporte con aceite de motor.
Cuando los engranajes están engranados, el diente del engranaje del cigüeñal con la marca “O” debe estar contra las ranuras de los dientes del engranaje del árbol de levas (ver Fig. 17). La holgura lateral en el acoplamiento debe estar en el rango de 0,03 a 0,08 mm. Si hay una brecha mayor o menor, elige otro par;
- - a través de los orificios del engranaje del árbol de levas, fije la brida de empuje al bloque con dos pernos y arandelas elásticas;
- - colocar el deflector de aceite en el muñón del extremo delantero del cigüeñal con el lado convexo hacia el engranaje;
- - compruebe la idoneidad para un funcionamiento posterior del sello de aceite presionado en la tapa del engranaje de distribución. Si el sello de aceite tiene bordes de trabajo desgastados o cubre débilmente el cubo de la polea del cigüeñal insertado en el sello de aceite, reemplácelo por uno nuevo.
Se recomienda presionar el sello de aceite dentro de la tapa usando un mandril en una prensa, como se muestra en la Fig. 10;
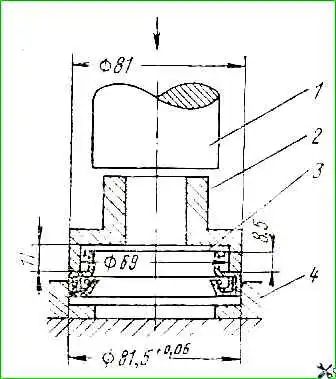
- colocar la junta y la tapa de la distribución en los espárragos;
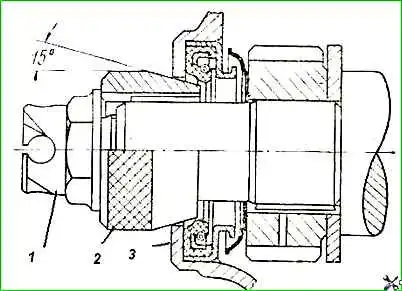
Centra la tapa a lo largo del extremo delantero del cigüeñal usando un mandril (Fig. 11) y aprieta todas las tuercas y tornillos que sujetan la tapa.
Si no hay mandril de centrado, la cubierta se puede instalar a lo largo del cubo de la polea del cigüeñal.
Se debe presionar el cubo sobre el cigüeñal de manera que su extremo encaje 5 mm en el orificio de la tapa.
Después de esto, asegure la tapa con tuercas, manteniendo el mismo espacio alrededor de la circunferencia entre el cubo y el orificio de la tapa.
El espacio debe nivelarse golpeando ligeramente la cubierta con un martillo de madera o goma. Después Esto finalmente asegurará la tapa;
retirar el mandril de centrado y presionar sobre el cubo de la polea del cigüeñal;
- - atornillar el trinquete en el cigüeñal, después de colocarle una arandela elástica.
Al girar el cigüeñal con el trinquete, verifique si el reflector está tocando la cubierta del engranaje de distribución debido a un reflector doblado o un ajuste flojo en el cubo;
- - atornillar la polea del cigüeñal al buje;
- - instale el conjunto de la bomba de aceite con el receptor de aceite;
- - instalar el variador del interruptor-distribuidor;
- - girando el cigüeñal, alinee la marca. m.t. en el borde de la polea del cigüeñal con un puntero en la tapa del engranaje de distribución (ver Fig. 14).
Las levas del árbol de levas que accionan las válvulas del primer cilindro deben estar dirigidas con sus vértices en dirección opuesta a los empujadores (hacia el cárter de aceite) y ubicadas simétricamente, como se muestra en la Fig. 12;
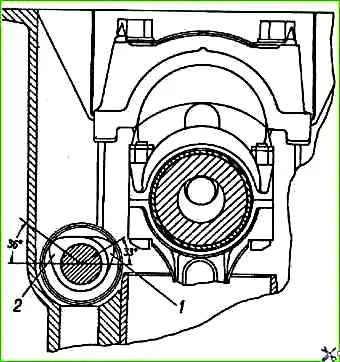
- comprobar el juego axial del eje de transmisión mediante una galga de espesores insertada entre la carcasa de transmisión y el engranaje.
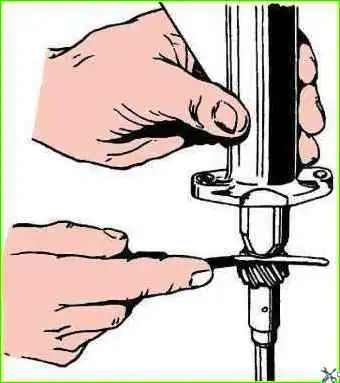
El espacio debe estar entre 0,15 y 0,40 mm;
Coloque una junta en los pernos de montaje del accionamiento del interruptor-distribuidor;
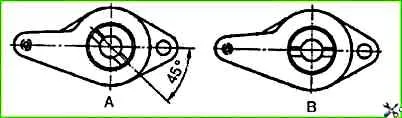
- - gire el eje de transmisión a la posición que se muestra en la Fig. 13, a, y coloque la transmisión en el casquillo del bloque de cilindros.
Al insertar la transmisión en el casquillo, es necesario girar el eje de la bomba de aceite de modo que el extremo del eje de transmisión entre en el orificio del eje de la bomba
En un variador instalado correctamente, la ranura en el buje del eje debe estar paralela al eje del motor y desplazada del motor, como se muestra en la Fig. 13, b;
- - asegurar la unidad;
- - comprobar la holgura en los engranajes helicoidales del árbol de levas y en el accionamiento del distribuidor picador.
Si por alguna razón solo se quitó una unidad del interruptor del distribuidor del motor, se puede instalar sin quitar el cárter de aceite.
En este caso, instalar el pistón del primer cilindro en c. m.t. carrera de compresión, al instalar la transmisión, gire ligeramente el cigüeñal en una dirección u otra.
Cuando la transmisión está correctamente instalada, cuando el pistón del primer cilindro está en el PMS. durante la carrera de compresión, el rotor del disyuntor-distribuidor tomará una posición opuesta al primer contacto marcado con el número 1 en la tapa del disyuntor-distribuidor;
- colocar la junta del cárter de aceite en la brida del bloque;
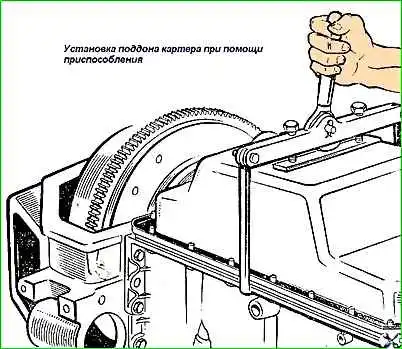
- - instalar el palet ensamblado sobre los montantes, presionarlo con el dispositivo (Fig. 14) contra el bloque y asegurarlo con tuercas y arandelas;
- - instalar y atornillar la parte inferior de la carcasa del embrague;
- - limpie las cámaras de combustión de las culatas de los depósitos de carbón, límpielas y soplelas con aire comprimido. Si es necesario, limpie los orificios de la tubería de distribución de agua y retírela, como se muestra en la Fig. 15;
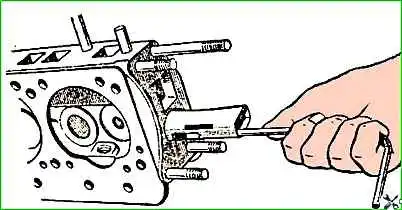
- - lape las válvulas, para ello necesitas:
- - aplique una capa delgada de una mezcla compuesta por una parte de polvo M-20 (GOST 3647-59) y dos partes de aceite industrial 20 (husillo 3) (GOST 1707-51) a la superficie rectificada del asiento de la válvula. Antes de usar, mezcle bien la mezcla;
poner technol en el vástago de la válvula resorte lógico, inserte la válvula en el manguito guía.
El diámetro interior del resorte debe ser de unos 10 mm.
La fuerza del resorte es pequeña; debe levantar la válvula ligeramente por encima del asiento. Cuando se presiona ligeramente, la válvula debe asentarse en el asiento;
- - presione la ventosa de goma contra el plano superior del cabezal de la válvula. Las superficies de la ventosa y de la válvula deben estar secas y completamente limpias;
- - girando el mango de la ventosa alternativamente en una dirección u otra y moviendo simultáneamente la válvula hacia arriba y hacia abajo, se consigue un bisel mate uniforme en las superficies de trabajo del asiento y la cabeza a lo largo de toda la circunferencia.
Antes de comenzar a rectificar, debe comprobar si la cabeza de la válvula está deformada o quemada en la válvula y el asiento.
Si estos defectos están presentes, es imposible restaurar la estanqueidad de la válvula simplemente esmerilando y primero se debe rectificar el asiento y reemplazar la válvula dañada por una nueva.
Si el espacio entre la válvula y el casquillo supera los 0,25 mm, tampoco se podrá restablecer la estanqueidad; en este caso, la válvula y el casquillo deben sustituirse por otros nuevos.
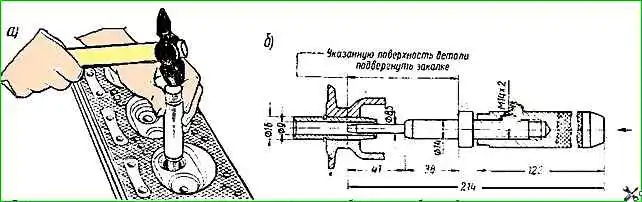
Las válvulas (para repuestos) se fabrican en un tamaño estándar y los casquillos guía se fabrican con un diámetro interno reducido en 0,3 mm (para desplegarlos al tamaño final después de presionarlos en la culata).
El casquillo guía desgastado se extrae utilizando un punzón (Fig. 16). S
Los asientos de las válvulas se retiran fresando con un avellanador de carburo.
Los sillines de reparación tienen un diámetro exterior 0,25 mm mayor que los estándar, por lo que los casquillos del asiento se perforan a la medida:
- para el asiento de la válvula de admisión - 47,25+0,027mm y para la válvula de escape - 38,75+0,027mm.
Los asientos de válvula y los casquillos guía deben enfriarse en dióxido de carbono (hielo seco) antes del montaje, y la culata debe calentarse a una temperatura de 160-175 °C.
Durante el montaje, los asientos y casquillos deben insertarse en los casquillos de la culata libremente o con una ligera fuerza.
Después de instalar el asiento, el metal de la culata se enrolla alrededor del asiento utilizando un mandril plano con un diámetro de 49 o 41 mm, respectivamente, centrado a lo largo del orificio del asiento.
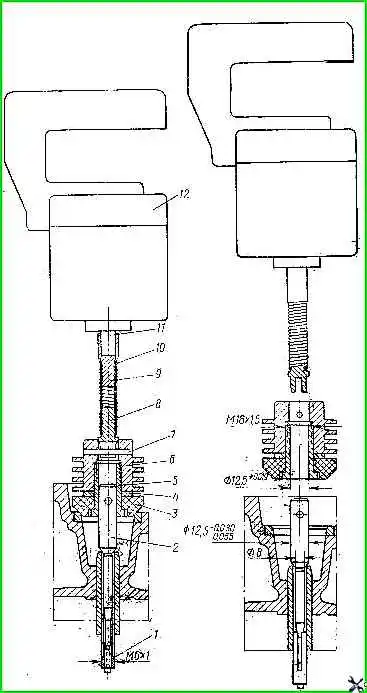
El nuevo casquillo se presiona desde el lado del balancín utilizando un punzón.
Después del prensado, el casquillo debe sobresalir 22 mm por encima del plano de la culata.
Después del prensado, ampliar el orificio del casquillo hasta un diámetro de 9+0,022 mm, y rectificar los chaflanes de los asientos, centrándolos a lo largo del orificio del casquillo.
Para pulir los asientos, puede utilizar el dispositivo que se muestra en la Fig. 17.
El mandril de expansión se instala en el orificio mecanizado del manguito y el vástago del mandril sirve como eje para la muela abrasiva con un chaflán en un ángulo de 45°.
La muela es accionada por un pequeño motor eléctrico.
Al rectificar, asegúrese de que el chaflán del asiento de la válvula sea concéntrico con el orificio del casquillo dentro de 0,03 mm de la lectura total del indicador.
Los chaflanes están rectificados en un ángulo de 45°. El diámetro exterior "d" (Fig. 16) del chaflán en el asiento de la válvula de entrada debe ser de 46 mm y en la válvula de escape, de 35 mm.
El ancho del chaflán “b” debe ser de 1,8-2,3 mm en el asiento de la válvula de admisión y de 2,3-2,5 mm en el asiento de la válvula de escape.
El ancho del chaflán se garantiza rectificando el orificio del asiento en un ángulo de 30°, como se muestra en la Fig. 18, a.
Al rectificar asientos desgastados, el diámetro exterior del chaflán se vuelve mayor que las dimensiones indicadas anteriormente. En este caso, el diámetro exterior del chaflán se lleva al tamaño requerido rectificando el extremo del asiento en un ángulo de 30°, como se muestra en la Fig. 18, b.
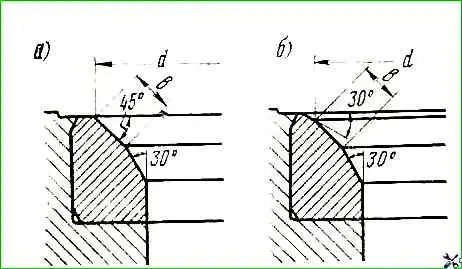
Después de pulir los asientos y las válvulas, limpie a fondo todos los canales de gas y sóplelos con aire comprimido para que no quede polvo abrasivo.
Antes del montaje, los vástagos de las válvulas se lubrican con una mezcla que consta de siete partes de una preparación de grafito coloidal de aceite (GOST 5262-50) y tres partes de aceite de aviación MS-20;
- - inserte las válvulas en los casquillos según las instrucciones siguiendo las marcas y ensamblarlos con los resortes. Asegúrese de que los salientes de las chavetas encajen en la ranura anular del vástago de la válvula;
- - coloque una junta en los pernos de la culata, instale la culata y asegúrela con tuercas y arandelas. Apriete las tuercas con una llave dinamométrica a un par de 7,3-7,8 kgm, siguiendo el orden que se muestra en la Fig. 20;
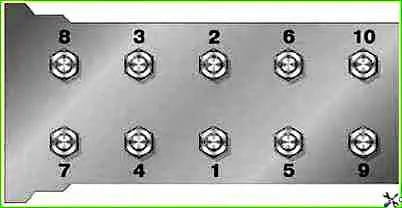
- limpiar con alambre y soplar con aire comprimido los orificios de los balancines, del eje de balancines y tornillos de ajuste, el orificio del poste trasero del eje de balancines y de la culata.
Compruebe que los casquillos del balancín estén bien asentados.
Si el ajuste está flojo durante la operación, el casquillo puede moverse y bloquear el orificio de lubricación de la varilla del elevador de válvula. Dichos casquillos deben ser reemplazados;
- realizar el submontaje del eje del balancín. Antes de instalar cada balancín, lubrique su casquillo con aceite de motor.
Los balancines y los puntales se ensamblan en el eje en una posición tal que el desplazamiento de los orificios para los pernos de montaje en los puntales mire hacia los tornillos de ajuste del balancín.
La cuarta rejilla (trasera) debe tener un orificio en el plano inferior para el paso del aceite;
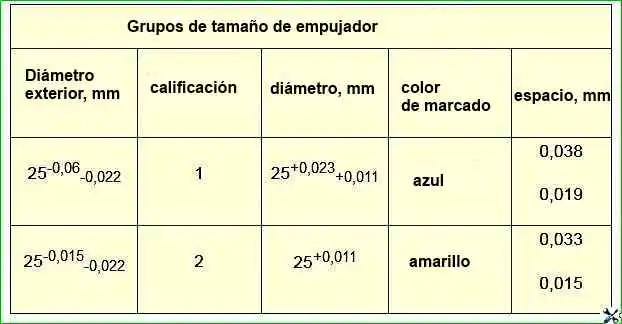
- - inserte los empujadores en los casquillos según las marcas que tienen. Lubrique previamente los empujadores y los orificios del bloque con aceite de motor;
- - introducir el conjunto de varilla con las puntas en los orificios de la culata;
- - instale el eje del balancín ensamblado en los pernos y asegúrelo con tuercas y arandelas. Los tornillos de ajuste con su parte esférica deben apoyarse en la esfera de la punta superior de la varilla;
- - establezca los espacios entre el extremo del vástago de la válvula central y la punta del balancín en 0,35-0,40 mm, y las válvulas exteriores (escape del primer y cuarto cilindro) en 0,30-0,35 mm. Esto debe hacerse como se indica en el artículo “Ajuste del juego de válvulas”;
- - colocar la junta y la tapa de balancines y fijarlos con tornillos y arandelas;
- - lubrique y coloque el conjunto del embrague de desembrague con cojinete en la tapa delantera de la caja de cambios y asegure el resorte de desembrague;
- - instalar y asegurar la caja de cambios;
- - instalar la horquilla de desembrague;
- - instale las piezas y conjuntos del motor en orden inverso.