En el sistema de potencia del motor de inyección de combustible, la presión es de 30 MPa (3 kgf/cm²)
Por lo tanto, está prohibido aflojar las conexiones de las líneas de combustible mientras el motor está en marcha o inmediatamente después de pararlo
Para realizar trabajos de reparación en el sistema de potencia en un motor recién parado, primero es necesario reducir la presión en el sistema de potencia
2-3 horas después de detener el motor, la presión en el sistema cae casi a cero.
Una característica fundamental del sistema de potencia del motor ZMZ-4062 es la ausencia de un carburador, que combina las funciones de formación de mezcla y dosificación de la mezcla de aire y combustible en los cilindros del motor.
En el sistema de inyección distribuida instalado en este motor, estas funciones están separadas: los inyectores realizan una inyección dosificada de combustible en el tubo de admisión y el aire necesario en cada momento de funcionamiento del motor es suministrado por un sistema que consta de un acelerador. y un regulador de aire inactivo.
El sistema de inyección de combustible y el sistema de encendido están controlados por una unidad de control electrónico del motor, que monitorea continuamente, utilizando sensores apropiados, la cantidad de carga del motor, la velocidad del vehículo, el estado térmico del motor y el medio ambiente, y el proceso de combustión óptimo. en los cilindros del motor.
Este método de control permite asegurar la composición óptima de la mezcla combustible en cada momento específico de funcionamiento del motor, lo que permite obtener la máxima potencia con el menor consumo de combustible posible y una baja toxicidad de los gases de escape.
El El diagrama del sistema de inyección de combustible se muestra en la figura.
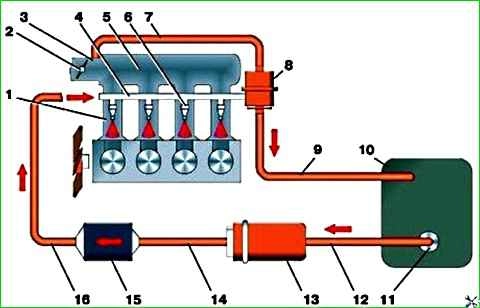
El depósito de combustible 10 está soldado, estampado y asegurado con dos abrazaderas de acero a través de juntas debajo del piso del maletero.
En la parte superior del tanque de combustible hay instalados una entrada de combustible y un sensor de nivel de combustible.
Al lado del tanque de combustible, debajo del piso de la carrocería, hay una bomba de combustible eléctrica conectada por una línea de combustible al tanque de combustible.
Para reducir la vibración, el soporte de la bomba está fijado al suelo mediante almohadillas de goma.
Desde la bomba, el combustible se suministra al filtro de combustible instalado en el compartimiento del motor y desde allí ingresa a la línea de combustible del motor montada en el tubo de admisión del motor.
El combustible se inyecta desde la línea de combustible del motor mediante inyectores al tubo de admisión.
El exceso de combustible se drena al tanque de combustible a través de una válvula de alivio de presión instalada en el extremo trasero de la línea de combustible del motor.
Además del sistema de alimentación de elementos que se muestra en el diagrama, incluye un filtro de aire instalado en el compartimiento del motor, conectado mediante una manguera de goma a un sensor de flujo masivo de aire, que a su vez está conectado a un acelerador montado en el depósito de aire, así como un regulador de ralentí, también instalado en el depósito de aire.
La boquilla es una válvula electromecánica en la que la aguja de la válvula de cierre se presiona contra el asiento mediante un resorte.
Cuando se aplica un impulso eléctrico desde la unidad de control al devanado del electroimán, la aguja se eleva y abre el orificio de la boquilla, a través del cual se suministra combustible al tubo de entrada del motor.
La cantidad de combustible inyectada por el inyector depende de la duración del pulso eléctrico.
La válvula reductora de presión es un recipiente separado por un diafragma sobre el que se fija una válvula que cierra el orificio de drenaje de combustible bajo la acción de un resorte.
La válvula reductora de presión mantiene una presión constante en el sistema de energía de aproximadamente 0,3 MPa.
La parte superior de la válvula de alivio de presión está conectada al receptor con una manguera de vacío.
Cuando la caída de presión en el receptor no es superior a 0,3 MPa, la válvula se cierra y la presión en el sistema de suministro aumenta.
Cuando la presión del combustible alcanza más de 0,3 MPa, la membrana se dobla, se abre un orificio y el exceso de combustible se drena depósito de combustible.
Tan pronto como la presión del combustible cae a 0,3 MPa, la membrana vuelve a su posición original y cierra el orificio de drenaje de combustible.
El sensor de flujo de masa de aire se utiliza para determinar la cantidad de aire que ingresa a los cilindros del motor.
Las señales del sensor ingresan a la unidad de control del motor y son uno de los parámetros que determinan la duración de la inyección de combustible por parte de los inyectores; la cantidad de combustible depende de la cantidad de aire en un momento dado.
El elemento principal del sensor es un filamento de platino, que se calienta hasta 150 °C durante el funcionamiento.
A medida que la entrada de aire del motor pasa a través de la carcasa del sensor, el filamento se enfría y el circuito electrónico del sensor se esfuerza constantemente por mantener una temperatura del filamento de 150 °C.
La energía eléctrica gastada para mantener la temperatura del filamento es el parámetro mediante el cual la unidad de control del motor determina la duración del impulso eléctrico suministrado a los inyectores.
El grado de enfriamiento del filamento de platino depende no sólo de la cantidad, sino también de la temperatura del aire que pasa, determinada por una resistencia de compensación térmica, que corrige en consecuencia la señal suministrada por el sensor a la unidad de control.
Para que sea posible ajustar la cantidad de monóxido de carbono en los gases de escape al ralentí, el módulo electrónico dispone de una resistencia variable, con cuyo tornillo se puede cambiar manualmente la magnitud de la señal suministrada por el sensor al unidad de control electrónico, cambiando así la duración del pulso suministrado a los inyectores y, por tanto, la cantidad de combustible inyectado.
Para limpiar el hilo de platino de contaminantes, el módulo electrónico le suministra periódicamente un mayor voltaje, provocando un calentamiento a 1000 °C. En este caso, todos los depósitos se queman.
Si el sensor falla, la unidad de control del motor activa un programa de respaldo que garantiza el funcionamiento del motor con características de potencia y consumo ligeramente diferentes, pero aceptables.
Al mismo tiempo, se enciende el testigo del cuadro de instrumentos.
El regulador de ralentí se utiliza para mantener constante el ralentí del motor al arrancarlo, calentarlo y cambiar la carga provocada por el encendido del equipo auxiliar.
El regulador es una válvula de carrete controlada por solenoide y se utiliza para suministrar aire adicional al tubo de admisión, sin pasar por la válvula del acelerador.
Si el regulador de ralentí falla o no hay contacto en el bloque de enchufe, la estabilidad del ralentí se altera (la velocidad “flota”). Al mismo tiempo, se enciende el testigo de control en el cuadro de instrumentos.
Si el ralentí es inestable y el testigo no se enciende, es necesario comprobar el apriete de las mangueras de conexión.
El sensor de posición del acelerador, que es una resistencia semiconductora variable dual, está instalado en el acelerador en el mismo eje que la válvula del acelerador.
Utilizando la señal del sensor, la unidad de control del motor determina la posición de la válvula de mariposa para calcular la duración del impulso eléctrico suministrado a los inyectores y el momento óptimo de encendido.
La señal determinante es la magnitud de la caída de voltaje a través de la resistencia variable del sensor, que cambia dependiendo de la posición de la válvula del acelerador (completamente cerrada, parcialmente abierta, completamente abierta).
Si falla un sensor, la unidad de control del motor funciona de acuerdo con el programa de respaldo almacenado en ((memoria)), utilizando datos de otros sensores. Al mismo tiempo, se enciende el testigo de control en el cuadro de instrumentos.
El sensor de velocidad y sincronización está ubicado en la parte delantera del motor, en el lado derecho.
Utilizando la señal del sensor, la unidad de control del motor determina la posición angular del cigüeñal y su velocidad de rotación.
De acuerdo con la frecuencia de las señales generadas por el sensor al girar el disco de sincronización, Montada en la polea del cigüeñal, la unidad de control determina la velocidad del cigüeñal del motor, sincronizando el suministro de combustible por los inyectores y el tiempo de encendido con el proceso de funcionamiento del motor.
Si falla el sensor de posición del cigüeñal, el motor no arrancará, ya que la centralita, sin recibir una señal del sensor, no encenderá los sistemas de inyección y encendido.
El sensor de detonación está ubicado en la parte superior del bloque del motor en el lado derecho y está asegurado con una tuerca y una arandela de resorte.
Se utiliza para determinar el momento en que se produce la detonación cuando el motor está funcionando con gasolina con un octanaje inferior al requerido cuando el motor se sobrecalienta o el conductor selecciona el modo de conducción incorrecto.
El funcionamiento del sensor de detonación se basa en el principio del efecto piezoeléctrico.
Cuando se aplica un impacto mecánico a un elemento piezoeléctrico hecho de metal-cerámica, se genera en él una corriente eléctrica.
La acción mecánica la lleva a cabo una arandela de inercia, que percibe la onda de choque que se produce en la cámara de combustión y en el cilindro del motor durante la combustión por detonación de la mezcla de combustible.
Al mismo tiempo, aparece un impulso de tensión en el sensor, que éste transmite a la unidad de control desde el enchufe.
En función de esta señal, la unidad de control ajusta el tiempo de encendido hasta que se detiene la detonación.
Una falla del sensor o un mal funcionamiento en su circuito eléctrico resultará en la ausencia de un cambio óptimo en el tiempo de encendido en presencia de detonación.
Al mismo tiempo, se encenderá la luz indicadora en el grupo de instrumentos.
El sensor de fase está ubicado en la parte trasera de la culata del cilindro, en el lado izquierdo. El principio de funcionamiento del sensor se basa en el efecto Hall.
Cuando una placa metálica montada en el árbol de levas pasa por el extremo del núcleo del sensor, se genera un impulso que permite a la unidad de control determinar el momento en que el pistón del primer cilindro está en el punto muerto superior durante la carrera de compresión y enviar una señal de inyección al inyector de este cilindro en particular.
El suministro adicional de impulsos lo realiza la unidad de control de acuerdo con el orden de funcionamiento de los cilindros inherente a su programa.
Si falla el sensor de fase, la unidad de control cambia al modo de respaldo con suministro de combustible a todos los cilindros simultáneamente.
Al mismo tiempo, se mantiene el rendimiento del motor, pero el consumo de combustible aumenta significativamente.
Un mal funcionamiento del sensor se indica mediante una luz de advertencia en el grupo de instrumentos.
El filtro de aire con un elemento filtrante seco reemplazable hecho de papel de filtro corrugado está ubicado en la parte delantera derecha del compartimiento del motor.
El elemento filtrante se fija a la cubierta del filtro con una tuerca de mariposa y la cubierta se fija al cuerpo con tres clips de resorte.
La bomba de combustible eléctrica de tipo rotativo impulsada por un motor eléctrico de CC está ubicada directamente en la carcasa de la bomba y opera en el combustible.
En este sentido, en la bomba no hay juntas de ninguna pieza móvil y las superficies de fricción se lubrican con el combustible que fluye.
La válvula de retención instalada en la bomba evita que el combustible fluya desde la línea de combustible de alta presión hacia el tanque después de apagar el encendido.
La bomba de combustible eléctrica tiene un diseño no separable y debe reemplazarse si falla.
El filtro de combustible está instalado en el compartimiento del motor, encima del servofreno por vacío.
Está estrictamente prohibido reemplazar el filtro estándar por otro, por ejemplo uno estandarizado con carcasa de plástico, debido a la alta presión del combustible en el sistema.
El sistema de ventilación del cárter del motor de tipo cerrado es forzado y funciona debido al vacío en el colector de admisión.
Cuando el motor está en ralentí y con cargas bajas, cuando la válvula de mariposa está cerrada, los gases del cárter se aspiran a través de la manguera de la pequeña rama del sistema directamente al colector de admisión del motor y luego a los cilindros.
En otros modos, los gases del cárter se succionan a través de la manguera de la rama principal del sistema hacia el acelerador y desde allí hacia el colector de admisión.
Durante el funcionamiento es necesario asegurar la estanqueidad de la conexión y la limpieza de las tuberías, ya que si el sistema de ventilación del cárter no funciona se produce una rápida oxidación y envejecimiento del aceite del motor.
La obstrucción de las tuberías del sistema provoca fugas de aceite a través de los sellos de aceite y los sellos del motor debido a un aumento excesivo en la presión del gas del cárter.