Necesitarás: una lámpara portátil, un juego de sondas planas, una regla, un calibre, un calibre, un micrómetro, un raspador
Después del desmontaje, lave bien las piezas con queroseno, sople y séquelas con aire comprimido (especialmente los canales de aceite de las piezas)
Inspecciona el bloque, con especial atención los soportes del cigüeñal.
No se permiten grietas en ningún lugar del bloque.
Si sospecha que hay grietas en el bloque (ha entrado refrigerante en el cárter o ha entrado aceite en el refrigerante), verifique la estanqueidad del bloque en un soporte especial. Realizar la revisión en talleres que dispongan del equipamiento adecuado.
Inspeccione los cilindros en ambos lados.
No se permiten rayones, muescas ni grietas.
Al inspeccionar los cilindros, recomendamos iluminar los espejos de los cilindros con una lámpara portátil; en este caso, los defectos se ven mucho mejor.
Determine los diámetros reales de los cilindros con un calibre de diámetro.
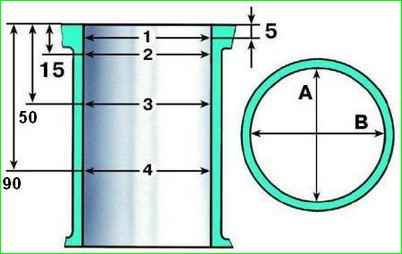
Mida el diámetro del cilindro en cuatro zonas (Fig. 1), ubicadas a lo largo de la altura del cilindro a una distancia de 5, 15, 50 y 90 mm del plano del conector con la cabeza del bloque.
En cada cinturón, el diámetro se mide en dos direcciones mutuamente perpendiculares (longitudinal y transversal).
Los cilindros tipo bloque se dividen en cinco clases según su diámetro:
- A = 82,00–82,01 mm;
- B = 82,01–82,02 mm;
- C = 82,02–82,03 mm;
- D = 82,03–82,04 mm;
- E = 82,04–82,05 mm.
La clase de cada cilindro del bloque de acuerdo con la documentación del fabricante está marcada con un sello en el lado derecho del plano inferior (el plano del conector con el cárter de aceite).
De acuerdo con la documentación del fabricante, se debe aplicar un sello con el número convencional del bloque de cilindros en el lado izquierdo del plano inferior del bloque.
El mismo número debe estar en todas las tapas de los cojinetes principales para indicar que las tapas pertenecen a este bloque.
En la zona de la primera correa (a una distancia de 5 mm del plano del conector con la cabeza del bloque), los cilindros prácticamente no se desgastan.
Por la diferencia de tamaño entre la primera correa y el resto, se puede juzgar el desgaste de los cilindros.
Si el valor de desgaste máximo es superior a 0,15 mm, taladre los cilindros al tamaño de reparación del pistón más cercano (aumentado en 0,4 o 0,8 mm), dejando un margen de 0,03 mm para el diámetro de bruñido.
Luego, pula los cilindros, manteniendo un diámetro tal que al instalar el pistón de reparación seleccionado, el espacio calculado entre este y el cilindro sea de 0,05 a 0,07 mm.
Realizar la reparación de averías, mandrinado y bruñido del bloque en talleres con equipamiento especial.
Compruebe la desviación de la planitud de la superficie del conector de la culata.
Coloque un calibrador (o regla) al plano: en el medio del bloque; en las direcciones transversal y longitudinal; a lo largo de las diagonales del avión.
En cada posición, utilice una galga de espesores plana para determinar el espacio entre la pinza y el plano.
Esta será la desviación de la planitud. Si la desviación supera los 0,1 mm, reemplace la unidad.
Limpie la parte inferior del pistón de los depósitos de carbón con un raspador (se puede hacer con una lima vieja).
Limpie las ranuras del anillo del pistón de los depósitos de carbón utilizando el anillo viejo girándolo.
Inspeccionar los pistones, bielas, tapas: no deben tener grietas.
Inspeccione los revestimientos.
Si encuentra marcas, desgastes y descamación de la capa antifricción en la superficie de trabajo, reemplace los revestimientos por otros nuevos.
Todos los cojinetes de biela son iguales e intercambiables.
Mida el diámetro de los pistones en un plano perpendicular al eje del pasador del pistón, a una distancia de 52,4 mm del fondo del pistón.
Según los resultados de la medición, determine la distancia entre el pistón y el cilindro y, si es necesario, seleccione nuevos pistones para los cilindros.
La separación estimada entre el pistón y el cilindro (para piezas nuevas) es de 0,05 a 0,07 mm.
Se determina midiendo los cilindros y pistones y prever la instalación de pistones de la misma clase que los cilindros.
Separación máxima permitida (si las piezas están desgastadas) 0,15 mm.
Si un motor usado tiene una holgura superior a 0,15 mm, es necesario hacer coincidir los pistones con los cilindros: la holgura debe ser lo más cercana posible a la de diseño.
Inserte un dedo lubricado con aceite de motor en el orificio del saliente del pistón.
El pasador gira libremente en los resaltes del pistón y en la cabeza superior de la biela.
Según el diámetro exterior, los dedos se dividen en tres categorías cada 0,004 mm.
La categoría está indicada por pintura en la punta del dedo:
- Primero (marca azul): 21,982–21,986 mm;
- Segundo (marca verde): 21 986–21 990;
- Tercero (marca roja): 21 990–21 994.
El dedo debe encajar firmemente, pero sin atascarse, en los orificios del saliente y la biela debido a la fuerza del pulgar.
Gira el pistón con el eje del pasador verticalmente.
El dedo no debe caerse del jefe.
Reemplaza el dedo que se cae del jefe por otro de la siguiente categoría.
Si el pistón tiene un pasador de tercera categoría, reemplace el pistón con el pasador.
Compruebe el espacio de altura entre las ranuras del pistón y los anillos con una galga de espesores plana insertando el anillo en la ranura correspondiente.
La brecha nominal (calculada) es:
- – para el (primer) anillo de compresión superior 0,04–0,07 mm;
- – para el segundo anillo de compresión 0,03–0,06 mm;
- – para anillo rascador de aceite de 0,02 a 0,05 mm.
Separaciones de desgaste máximas permitidas: 0,15 mm.
Compruebe el espacio en el bloqueo del anillo con una galga de espesores plana, instalando el anillo en el cilindro hasta una profundidad de unos 50 mm.
Para instalar el anillo sin deformarlo, empújelo profundamente dentro del cilindro con el pistón.
La separación se comprueba en anillos insertados en un calibre especial que tiene un diámetro de orificio igual al diámetro nominal del anillo con una tolerancia de ±0,003 mm.
El espacio debe ser de 0,25 a 0,45 mm para todos los anillos nuevos.
La holgura de desgaste máxima permitida es de 1,0 mm.
Si no hay calibre, está permitido utilizar el método que se muestra. Si el espacio es insuficiente, corte las superficies de unión del anillo.
Si el espacio excede el valor permitido, reemplace el anillo.
Si es posible, compruebe el peso de los pistones: para un motor, no deben diferir entre sí en más de ±2,5 g.
Puedes ajustar su peso quitando el metal en el área que se muestra a ambos lados del pistón.
La profundidad de eliminación de metal no debe exceder los 4,5 mm, basándose en la altura nominal del pistón de 59,4 mm.
Mida el diámetro interior Dв del asiento de la biela ensamblada con la tapa utilizando un calibre de orificio. Antes de medir, apriete las tuercas de los pernos de la biela al par nominal.
Mida el espesor T de los cojinetes de biela con un calibre
Mida el diámetro Dн de los muñones de biela con un micrómetro
Calcule el espacio z entre los cojinetes de biela y los muñones del cigüeñal usando la fórmula z=Dв–2T–Дн.
El espacio nominal de diseño es de 0,02 a 0,07 mm.
Limitar la separación a 0,1 mm.
Si el espacio real calculado es menor que el límite, puede reutilizar los revestimientos que se instalaron.
Si el espacio es mayor que el límite, reemplace los revestimientos de estos muñones por otros nuevos de espesor nominal (1,723–1,730 mm).
Si los muñones del cigüeñal están desgastados y rectificados al tamaño de reparación, reemplace los cojinetes por unos de reparación (de mayor espesor):
- “0,25” = 1,848–1,855 mm;
- “0,50” = 1,973–1,980 mm;
- “0,75” = 2,098–2,105 mm;
- “1,0” = 2,223–2,230 mm.
Diámetro nominal de los muñones de biela 47,83–47,85 mm.
Los muñones se rectifican si presentan mellas y rayones o si el desgaste (u ovalidad) es superior a 0,03 mm, reduciendo el diámetro en incrementos de 0,25 mm para obtener (según el grado de desgaste) los siguientes valores:< /p>
- "0,25" = 47,58–47,60 mm;
- “0,50” = 47,33–47,35 mm;
- “0,75” = 47,08–47,10 mm;
- "1,0" = 46,83–46,85 mm. Las designaciones “0,25” y otras indican cuánto disminuye el diámetro de los muñones del cigüeñal después del rectificado.
Inspeccione los casquillos del cojinete principal superior e inferior.
Los casquillos superiores de los cojinetes principales 1.º, 2.º, 4.º y 5.º tienen una ranura en la superficie interior (los inferiores no).
Las carcasas del cojinete principal central (3º) se diferencian de las demás por ser más anchas, además, su carcasa superior no tiene ranura.
Si hay marcas, raspaduras o descamación de la capa antifricción en la superficie de trabajo de los revestimientos, reemplace los revestimientos por otros nuevos. Está prohibido realizar operaciones de ajuste en los revestimientos.
Inspeccione el cigüeñal. No se permiten grietas.
No debe haber rayones, muescas o marcas en las superficies que coinciden con los bordes de trabajo de los sellos de aceite. Si lo encuentra, reemplace el eje.
Mida el diámetro exterior Dн de los muñones principales con un micrómetro.
El juego real entre los semicojinetes de bancada y los muñones del cigüeñal se determina según el método descrito para los semicojinetes de biela.
El espacio nominal de diseño es de 0,026 a 0,073 mm. El espacio máximo es de 0,15 mm.
Si el espacio real calculado es menor que el límite, puede reutilizar los revestimientos que se instalaron.
Si el espacio es mayor que el límite, reemplace los revestimientos de estos muñones por otros nuevos de espesor nominal (1,824–1,831 mm).
Si los muñones del cigüeñal están desgastados y rectificados al tamaño de reparación, reemplace los cojinetes por unos de reparación (de mayor espesor):
- “0,25” = 1,949–1,956 mm;
- “0,50” = 2,074–2,081 mm;
- “0,75” = 2,199–2,206 mm;
- “1,0” = 2,324–2,331 mm.
Diámetro nominal de los muñones principales 50,799–50,819 mm.
Los muñones se rectifican si presentan mellas y rayones o si el desgaste (u ovalidad) es superior a 0,03 mm, reduciendo el diámetro en incrementos de 0,25 mm para obtener (según el grado de desgaste) los siguientes valores:
- “0,25” = 50,549–50,569 mm;
- “0,50” = 50,299–50,319 mm;
- “0,75” = 50,049–50,069 mm;
- “1,0” = 49,799–49,819 mm. Las designaciones "0,25" y otras indican cuánto disminuye el diámetro de los muñones del cigüeñal después del rectificado. La marca correspondiente se coloca en la primera mejilla del cigüeñal, por ejemplo K 0,75; W 0,50.
Instale el eje con los muñones principales exteriores en los prismas y verifique con un indicador:
- – desviación axial de los muñones restantes (no más de 0,03 mm);
- – desviación axial de las superficies de asiento de la rueda dentada y del cojinete del eje de entrada de la caja de cambios (no más de 0,04 mm);
- – desplazamiento de los ejes de los muñones de biela desde el plano nominal pasando por los ejes de la biela y los muñones principales (no más de ±0,35 mm);
- – descentramiento final de la brida con un diámetro de 68 mm (no más de 0,025 mm). Comprobar el descentramiento en un taller es prácticamente imposible, así que hágalo en talleres con equipos especiales.
Inspeccione los tapones del canal del sistema de lubricación.
Comprueba que estén bien asentados con un destornillador sin aplicar fuerza significativa.
Si los enchufes no están instalados firmemente, reemplácelos.
Instale los tapones con sellador UG-6 y calafatee en tres lugares.
No recomendamos abrir tú mismo los tapones para limpiar los canales, lo que sin duda es útil.
Contactar con talleres que cuenten con equipos especiales, o lavar los canales sin abrir los tapones, para ello verter gasolina en los canales radiales (indicados por flechas), habiéndolos previamente taponado por un lado con tapones de madera.
Dejar actuar al menos 20 minutos y enjuagar los canales con gasolina, inyectándola con una pera de goma.
Retire los tapones de madera después de lavar los canales de conexión (que se muestran en líneas de puntos). Si es necesario, repita el lavado hasta que salga gasolina limpia.