On the Niva, torque is transmitted from the transfer case to the front and rear axles by cardan shafts
The front and rear cardan shafts are identical in design, differing only in length.
The cardan shaft is a thin-walled steel pipe with a splined tip welded to one end, and a hinge fork on the other end.
A sliding fork of the second hinge is put on the splined tip.
The splined connection is sealed with an oil seal, pressed by a collar, and a steel plug is pressed into the hole in the sliding fork on the side of the cardan joint.
Both hinges are connected to flanges, one of which (on the side of the sliding fork) attaches the shaft to the flange of the transfer case, and the other (on the side of the welded fork) - to the flange gearbox.
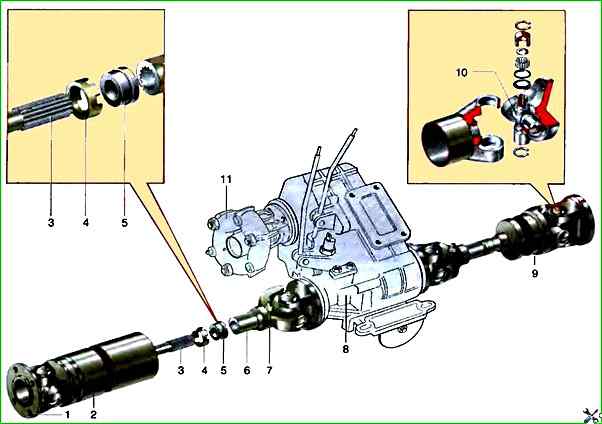
Cardan shafts: 1 - cardan joint flange-yoke; 2 - front cardan shaft; 3 - cardan shaft tip; 4 - oil seal collar; 5 - oil seal; 6 - sliding yoke; 7 - grease nipple; 8 - transfer case; 9 - rear cardan shaft; 10 - cardan shaft crosspiece; 11 – intermediate shaft
The cardan shaft assembly with flanges is dynamically balanced on special stands. The imbalance is balanced by welding balancing plates to the shaft pipe.
When disconnecting the parts of the cardan shaft, it is necessary to mark (with paint or a punch) their relative positions so that they can be installed in their places during assembly.
The cardan shaft must be rebalanced (or replaced) if the balancing plates are lost, deformed (it is straightened first), or if cardan transmission parts (sliding fork, flange, crosspiece with bearings) are replaced.
If, when replacing the crosspiece, it was not necessary to select new retaining rings (the sizes of the new and old ones match), then, as a rule, you can do without balancing.
The imbalance of the cardan transmission leads to noticeable vibrations at high speeds (above 60-80 km/h).
A strong imbalance can cause the destruction of the cardan transmission and adjacent units.
The universal joint consists of two forks connected to each other by a crosspiece.
The crosspiece has four pins on which the bearing housings with needles (thin rollers) are put on.
To protect against dirt, the bearing is sealed with an oil seal.
Since 1988, the design of the joints has been changed.
The diameter of the pins of the crosspiece and bearings has been increased, and the latter have become stamped (previously they were turned).
Accordingly, the size of the forks and holes in them has changed.
Therefore, individual parts of the cardan transmission of both the new and old models are not interchangeable, but the shafts can be replaced as an assembly.
In addition, the design of the oil seal has been changed: another working edge has been added, which made it possible to seal the bearing both in the radial and in the end direction.
To reduce friction between the bearing housing and the end of the crosspiece pin, a plastic washer is installed; there is no high temperature at the point of contact and the grease does not "weld".
On the surface of the washer facing the crosspiece tenon, grooves are made from the center to the periphery to supply grease from the tenon cavity to the bearing needles; grease nipples are installed to replenish the grease in the hinges and in the sliding fork.
Fiol-2U or grease No. 158 is used to lubricate the hinges, and Fiol-2U or Fiol-1 is used for the splined connection.
Due to the change in the design of the hinge, the procedure for dismantling it and selecting the retaining rings has changed.
Retaining rings are supplied in eight sizes, in different colors depending on the thickness: 1.45 mm - unpainted, 1.48 mm - yellow, 1.52 mm - brown, 1.56 mm - blue, 1.60 mm - black, as well as 1.40 mm and 1.67 mm without marking (the thickness is controlled by measurement).
When replacing the hinge, it is recommended to mark the position of the retaining rings and install them in their original places.
After pressing the bearing (force no higher than 1500 kgf), the rings should fit tightly into the gap between the end of the fork groove and the bottom of the bearing.
If the old rings do not fit into the gap or do not fit tightly, select new ones (if you need thinner rings, you can carefully grind the old ones).
After installing the rings, hit the hinge forks with a hammer with a plastic striker (or a regular hammer through a wooden block) so that the bearing housings are pressed tightly against the retaining rings (check whether the rings are clamped), and an axial clearance of 0.01-0.04 appears in the bearings mm.
A correctly assembled bearing should not have any noticeable play (the clearance is very small and, in addition, the bearing housing is pressed by the seal) and should rotate easily and without jamming.