El motor VAZ-21114 utiliza un sistema de inyección por fases distribuidas: el combustible se suministra mediante boquillas a cada cilindro por turno de acuerdo con el orden de funcionamiento de los cilindros del motor
El sistema de control electrónico del motor (ECM) consta de un controlador, sensores para los parámetros de funcionamiento del motor y del vehículo, así como dispositivos adicionales.
El controlador del sistema de inyección es la unidad central del sistema de gestión del motor.
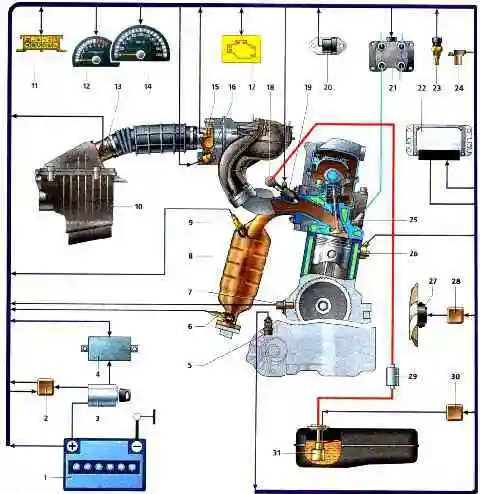
Esquema del sistema de control electrónico del motor: 1 - batería; 2 - relé principal; 3 - cerradura de encendido; 4 - unidad de control del inmovilizador; 5 - sensor de velocidad; 6 - sensor de oxígeno de diagnóstico; 7 - sensor de posición del cigüeñal; 8 - coleccionista; 9 - sensor de oxígeno de control; 10 - filtro de aire; 11 - conector de diagnóstico (bloque de diagnóstico); 12 - tacómetro; 13 - sensor de flujo masivo de aire; 14 - velocímetro; 15 - sensor de posición del acelerador; 16 - regulador de ralentí; 17 - dispositivo de señalización de mal funcionamiento del sistema de control del motor; 18 - riel de combustible; 19 - boquilla; 20 - sensor de camino en mal estado; 21 - bobina de encendido; 22 - controlador; 23 - sensor de temperatura del refrigerante; sensor de 24 fases; 25 - bujía; 26 - sensor de detonación; 27 - electroventilador del sistema de refrigeración; 28 - electroventilador del sistema de refrigeración; 29 - filtro de combustible; 30 - relé de la bomba de combustible eléctrica; 31 - módulo de combustible
El controlador está conectado al cuerpo del calentador desde abajo, debajo del panel de instrumentos.
El controlador recibe información de sensores y controla actuadores como inyectores de combustible, bobina de encendido, controlador de velocidad de ralentí, elemento calefactor del sensor de concentración de oxígeno, válvula solenoide de purga del recipiente, ventilador eléctrico del sistema de enfriamiento y varios relés del sistema.
Cuando se enciende el encendido, el controlador enciende el relé principal, a través del cual se suministra voltaje de suministro a los elementos del sistema (excepto la bomba de combustible eléctrica, la bobina de encendido, el ventilador eléctrico, la unidad de control y el indicador de estado del inmovilizador). .
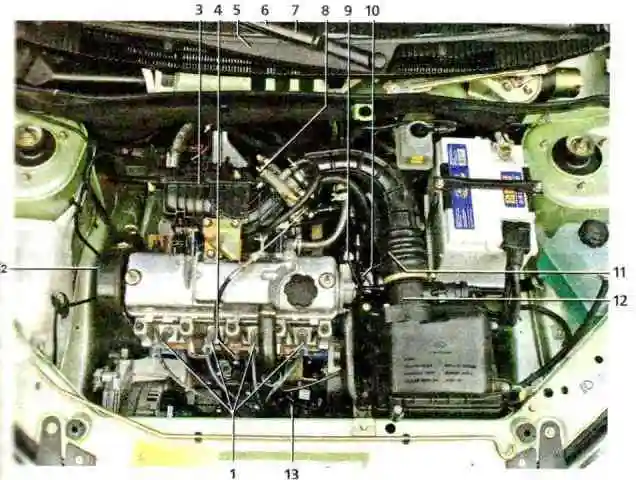
Elementos del sistema de control electrónico del motor: 1 - bujía; 2 - sensor de posición del cigüeñal; 3 - sensor de concentración de oxígeno; 4 - sensor de detonación; 5 - controlador y bloque de relés del sistema de control; 6 - conector de diagnóstico y caja de fusibles; 7 - indicador de mal funcionamiento; 8 - sensor de posición del acelerador; sensor de 9 fases; 10 - sensor de temperatura del refrigerante; 11 - sensor de velocidad; 12 - sensor de flujo masivo de aire; 13 - bobina de encendido
Cuando se apaga el encendido, el controlador retrasa el apagado del relé principal durante el tiempo necesario para prepararse para el siguiente encendido (para completar los cálculos, configure el controlador de velocidad de ralentí, controle el ventilador eléctrico del sistema de enfriamiento).
El controlador es una minicomputadora de propósito especial.
Contiene tres tipos de memoria: memoria de acceso aleatorio (RAM), memoria programable de sólo lectura (PROM) y memoria eléctricamente reprogramable (EPROM).
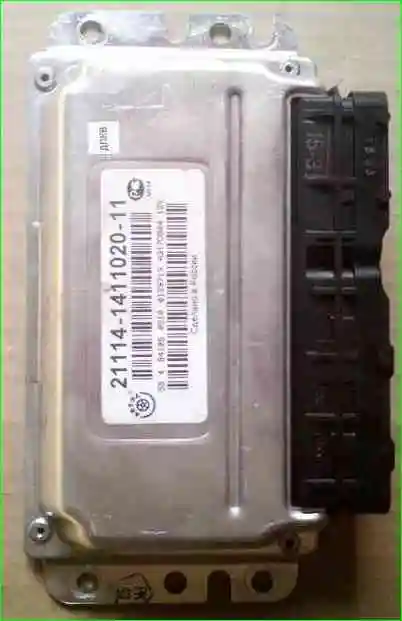
El microprocesador utiliza la RAM para almacenar temporalmente información actual sobre el funcionamiento del motor (parámetros medidos) y datos calculados.
Además, los códigos de error se escriben en la RAM.
Esta memoria es volátil, es decir, cuando se corta la energía (desconectando la batería o desconectando el arnés del controlador), su contenido se borra.
La PROM almacena un programa de control que contiene una secuencia de comandos operativos (algoritmo) y datos de calibración (configuraciones).
Así, la PROM determina los parámetros más importantes del motor: la naturaleza del cambio en el par y la potencia, el consumo de combustible, etc. La PROM no es volátil, es decir, su contenido no cambia cuando se corta la alimentación.
EEPROM se utiliza para almacenar identificadores de controlador, motor y vehículo (los códigos del inmovilizador se escriben al aprender las claves) y otros códigos de servicio.
Además, la EEPROM registra los parámetros operativos (kilometraje total del vehículo y tiempo de funcionamiento del motor, consumo total de combustible), así como violaciones de los modos de funcionamiento del motor y del vehículo (tiempo de funcionamiento del motor: con sobrecalentamiento, a baja combustible bronceado, exceso de velocidad máxima permitida, sensores de detonación, concentración de oxígeno y velocidad defectuosos).
EPROM es una memoria no volátil y puede almacenar información cuando el controlador no está encendido.
El controlador también realiza funciones de diagnóstico del sistema de gestión del motor (sistema de diagnóstico a bordo).
El controlador determina la presencia de mal funcionamiento de los elementos del sistema de control, enciende el indicador de mal funcionamiento en el grupo de instrumentos y almacena códigos de falla en su memoria.
Si se detecta un mal funcionamiento, para evitar consecuencias negativas (quema de los pistones por detonación, daños al catalizador en caso de fallos de encendido en la mezcla aire-combustible, superación de los valores límite de gases de escape toxicidad, etc.), el controlador cambia el sistema a modos de funcionamiento de emergencia.
Su esencia es que en caso de falla de cualquier sensor o su circuito, el controlador utiliza datos de reemplazo almacenados en la EEPROM para controlar el motor.
El indicador de mal funcionamiento del sistema de control del motor está ubicado en el grupo de instrumentos.
Si el sistema está bien, entonces la luz de advertencia debe encenderse cuando se enciende el encendido; por lo tanto, el ECM verifica que la luz de advertencia y el circuito de control estén funcionando.
Después de arrancar el motor, el indicador debe apagarse si no hay condiciones para encenderlo en la memoria del controlador.
Encender el indicador cuando el motor está en marcha informa al conductor que el sistema de diagnóstico a bordo ha detectado un mal funcionamiento y que se produce un mayor movimiento del automóvil en modo de emergencia.
En este caso, algunos parámetros del funcionamiento del motor (potencia, respuesta del acelerador, economía) pueden deteriorarse, pero es posible conducir con tales fallas y el automóvil puede conducir solo hasta la estación de servicio.
La única excepción es el sensor de posición del cigüeñal, si el sensor o sus circuitos están defectuosos, el motor no puede funcionar.
Después de eliminar las causas del mal funcionamiento, el controlador apagará el indicador después de un cierto tiempo de retardo, durante el cual el mal funcionamiento no aparece, y siempre que no haya otros códigos de falla en la memoria del controlador que requieran la activación del indicador.
Los códigos de falla (incluso si el indicador se apaga) permanecen en la memoria del controlador y se pueden leer usando la herramienta de diagnóstico DST-2M conectada al conector de diagnóstico.
Al borrar códigos de falla de la memoria del controlador usando una herramienta de diagnóstico o desconectando la batería (durante al menos 10 s), el indicador se apaga.
Los sensores del sistema de inyección proporcionan al controlador información sobre los parámetros del motor y del vehículo, a partir de los cuales calcula el momento, la duración y el orden de apertura de los inyectores de combustible, el momento y el orden de las chispas. .
El sensor de posición del cigüeñal (DPKV) está montado en la carcasa de la bomba de aceite.
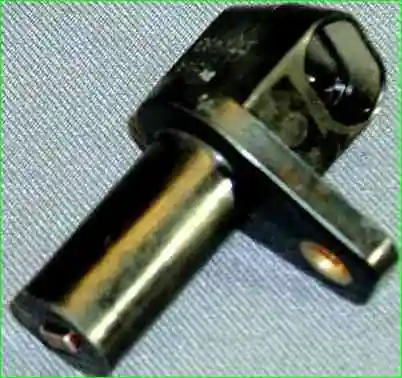
El sensor proporciona al controlador información sobre la velocidad y la posición angular del cigüeñal.
El sensor es de tipo inductivo, reacciona al paso de los dientes del disco impulsor, combinado con la polea impulsora del generador, cerca de su núcleo.
Los dientes están espaciados 6˚ en el disco. Para sincronizar con el PMS de los pistones de 1 y 4 cilindros se cortan dos de los 60 dientes, formando una cavidad.
Cuando la cavidad pasa por el sensor, en él se genera el llamado pulso de sincronización de referencia.
El espacio de instalación entre el núcleo y la parte superior de los dientes debe estar dentro de 1 ± 0,4 mm.
Cuando el disco maestro gira, el flujo magnético en el circuito magnético del sensor cambia: se inducen pulsos de voltaje de corriente alterna en su devanado.
En base al número y la frecuencia de estos pulsos, el controlador calcula la fase y la duración de los pulsos para controlar los inyectores y la bobina de encendido.
El sensor de fase (DF) está instalado en el tapón de la culata.
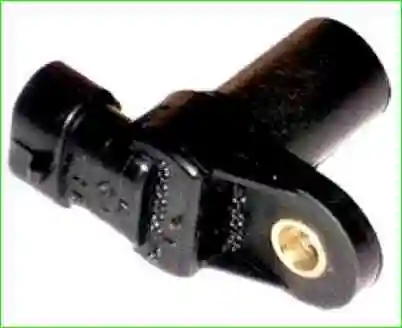
El principio de funcionamiento del sensor se basa en el efecto Hall.
Se presiona un pasador en el orificio del vástago del árbol de levas.
Cuando el pasador del eje pasa por el núcleo del sensor, el sensor envía un pulso de bajo voltaje (aproximadamente 0 V) al controlador, correspondiente a la posición del pistón del primer cilindro al final de la carrera de compresión.
El controlador utiliza la señal del sensor de fase para la inyección secuencial de combustible de acuerdo con el orden de funcionamiento de los cilindros.
Si el sensor de fase falla, el controlador cambiará Cambie al modo de inyección de combustible monofásico.
El sensor de temperatura del refrigerante (CTOZH) está instalado en el tubo de escape de la culata.
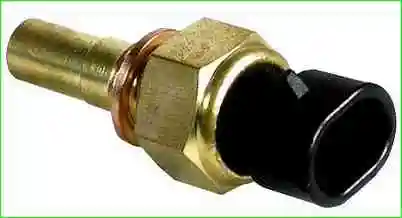
El sensor es un termistor NTC, es decir, su resistencia disminuye a medida que aumenta la temperatura.
El controlador suministra al sensor a través de una resistencia (aproximadamente 2 kOhm) un voltaje estabilizado de +5 V y, basándose en la caída de voltaje a través del sensor, calcula la temperatura del refrigerante, cuyos valores se utilizan en la mayoría funciones de control del motor.
Si ocurre un mal funcionamiento en los circuitos DTOZH, el indicador de mal funcionamiento del sistema de control del motor se enciende, el controlador enciende el ventilador del sistema de enfriamiento a un modo de operación constante y calcula el valor de temperatura usando un algoritmo de derivación.
El sensor de posición del acelerador (TPS) está instalado en el eje de la válvula del acelerador y es una resistencia de tipo potenciométrico.
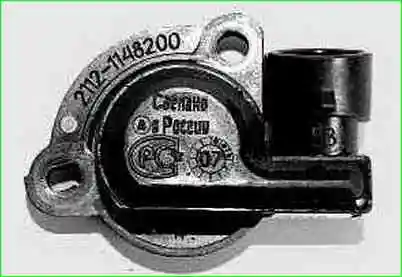
Se suministra un voltaje estabilizado de +5 V desde el controlador a un extremo de su devanado, y el otro está conectado a la "masa" del controlador.
Una señal para el controlador se toma de la tercera salida del potenciómetro (deslizador).
Al medir periódicamente el voltaje de salida de la señal TPS, el controlador determina la posición actual del acelerador para calcular el tiempo de encendido y la duración de los pulsos de inyección de combustible, así como para controlar el controlador de velocidad de ralentí.
Si el TPS o sus circuitos fallan, el controlador enciende el indicador de mal funcionamiento y calcula el valor estimado de la posición del acelerador a partir de la velocidad del cigüeñal y el flujo másico de aire.
El sensor de flujo de masa de aire (MAF) de tipo cable caliente está ubicado entre el filtro de aire y la manguera de suministro de aire al conjunto del acelerador.
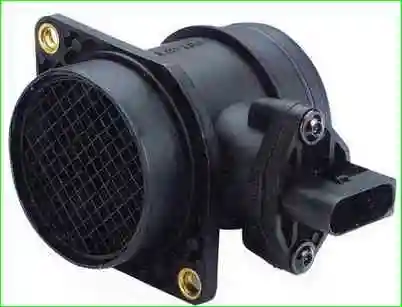
Dependiendo del flujo de aire, el voltaje de salida del sensor varía de 1,0 a 5,0 V.
Si el sensor falla, el controlador calcula el valor del flujo másico de aire a partir de la velocidad del cigüeñal y la posición del acelerador.
DMRV tiene un sensor de temperatura del aire (ATS) incorporado, cuyo elemento sensible es un termistor instalado en la corriente de aire.
La salida del sensor varía de 0 a 5,0 V, dependiendo de la temperatura del aire que pasa a través del sensor.
Si ocurre un mal funcionamiento en el circuito DTV, el controlador enciende el indicador de mal funcionamiento y reemplaza la lectura del sensor con un valor fijo de temperatura del aire (33˚С).
El sensor de detonación (KD) está montado en la parte superior delantera del bloque de cilindros.
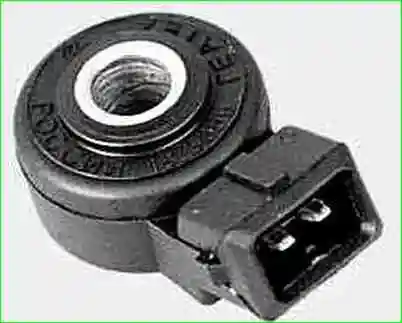
El elemento sensor piezocerámico del sensor genera una señal de voltaje CA, cuya amplitud y frecuencia corresponden a los parámetros de vibración del motor.
Cuando se produce una detonación, la amplitud de las vibraciones de una determinada frecuencia aumenta.
Al mismo tiempo, el controlador ajusta el tiempo de encendido para amortiguar la detonación.
El sensor de control de concentración de oxígeno (UDC) está instalado en el convertidor catalítico antes del convertidor catalítico.
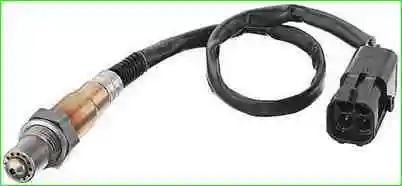
El controlador calcula la duración del pulso de inyección de combustible a partir de parámetros como el flujo másico de aire, la velocidad del motor, la temperatura del refrigerante y la posición del acelerador.
De acuerdo con la señal de la UDC sobre la presencia de oxígeno en los gases de escape, el controlador ajusta el suministro de combustible por los inyectores para que la composición de los gases de escape sea óptima para el funcionamiento eficiente del convertidor catalítico.
El oxígeno contenido en los gases de escape crea una diferencia de potencial a la salida del sensor, que varía aproximadamente de 50 a 900 mV.
Un nivel de señal bajo corresponde a una mezcla pobre (presencia de oxígeno) y un nivel alto corresponde a una mezcla rica (sin oxígeno).
Cuando el UDC está en estado frío, no hay señal de salida del sensor, porque su resistencia interna en este estado es muy alta: varios MΩ (el sistema de control del motor funciona en un circuito abierto).
Para un funcionamiento normal, el sensor de concentración de oxígeno debe tener una temperatura de al menos 300 ˚c, por lo que para un calentamiento rápido después de arrancar el motor, se incorpora un elemento calefactor controlado por el controlador.
A medida que el sensor se calienta, la resistencia cae y comienza a generar una señal de salida.
El controlador emite constantemente un voltaje de referencia estabilizado de 450 mV al circuito del sensor.
Hasta que el sensor se calienta, su voltaje de salida oscila entre 300 y 600 mV. En este caso, el controlador controla el sistema de inyección sin tener en cuenta el voltaje en el sensor.
A medida que el sensor se calienta, su resistencia interna disminuye y comienza a cambiar el voltaje de salida más allá del rango especificado.
Luego, el controlador apaga la calefacción del sensor y comienza a tener en cuenta la señal del sensor de concentración de oxígeno para el control del combustible en modo de circuito cerrado.
El sensor de concentración de oxígeno puede envenenarse por el uso de gasolina con plomo o el uso de selladores que contienen grandes cantidades de silicona altamente volátil (compuestos de silicio) al ensamblar el motor.
Los vapores de silicona pueden entrar en la cámara de combustión a través del sistema de ventilación del cárter.
La presencia de compuestos de plomo o silicio en los gases de escape puede provocar fallos en el sensor.
En caso de falla del sensor o de sus circuitos, el controlador enciende el indicador de falla, almacena el código de falla correspondiente en su memoria y controla el suministro de combustible en un circuito abierto.
El sensor de concentración de oxígeno de diagnóstico (DDC) se utiliza en el sistema de gestión del motor, fabricado según los estándares de toxicidad Euro-3.
El DDK se instala en el convertidor catalítico después del convertidor catalítico de gases de escape.
El principio de funcionamiento del DDC es el mismo que el de la UDC. la señal generada por el DDC indica la presencia de oxígeno en los gases de escape después del convertidor.
Si el neutralizador funciona correctamente, las lecturas del DDC diferirán significativamente de las lecturas del UDC.
El voltaje de la señal de salida del DDC calentado cuando funciona en modo de circuito cerrado y un buen convertidor debe estar en el rango de 590 a 750 mV.
Si se produce un mal funcionamiento del sensor o de sus circuitos, el controlador ingresa el código de mal funcionamiento en su memoria y activa la alarma.
El sensor de velocidad del vehículo está montado en la parte superior de la caja de cambios.

El principio de su funcionamiento se basa en el efecto Hall. El accionamiento del sensor está montado en la caja del diferencial.
El sensor emite pulsos de voltaje rectangulares al controlador (nivel inferior - no más de 1 V, nivel superior - no menos de 5 V) con una frecuencia proporcional a la velocidad de rotación de las ruedas motrices.
El número de pulsos del sensor es proporcional a la distancia recorrida por el vehículo. El controlador determina la velocidad del coche mediante la frecuencia de los pulsos.
Si el sensor o sus circuitos fallan, el controlador almacena el código de falla en su memoria y activa la alarma.
El sensor de carretera en mal estado (RDS) se utiliza en el sistema de gestión del motor, fabricado según los estándares de toxicidad Euro-3.
El sensor está instalado en el compartimento del motor, en la copa del guardabarros derecho.
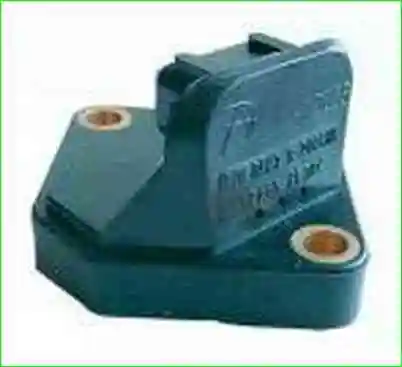
El sensor está diseñado para medir la amplitud de las vibraciones corporales.
El principio de su funcionamiento se basa en el efecto piezoeléctrico.
La carga variable en la transmisión que se produce al conducir por carreteras en mal estado afecta la velocidad angular de rotación del cigüeñal del motor.
Al mismo tiempo, las oscilaciones en la velocidad del cigüeñal son similares a las oscilaciones similares que ocurren durante los fallos de encendido de la mezcla de aire y combustible en los cilindros del motor.
En este caso, para evitar una detección falsa de fallos de encendido, el controlador desactiva esta función del sistema de diagnóstico a bordo cuando la señal LND excede un cierto umbral.
Si el sensor o sus circuitos fallan, el controlador almacena el código de falla en su memoria y activa la alarma.
Cuando se enciende el encendido, el controlador intercambia información con el inmovilizador (si está activado), diseñado para evitar el arranque no autorizado del motor águila.
Si durante la comunicación se determina que se permite el acceso para arrancar el motor, el controlador continúa funcionando. De lo contrario, se bloquea el arranque del motor.
La unidad de control del inmovilizador está ubicada dentro del panel de instrumentos.
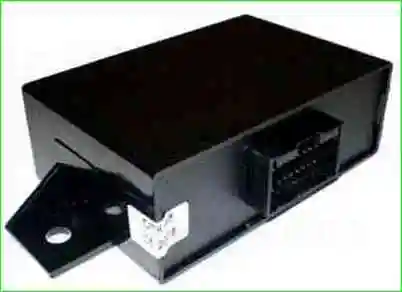
El sistema de encendido consta de una bobina de encendido, cables de alto voltaje y bujías. Durante el funcionamiento no requiere mantenimiento ni ajuste, salvo sustitución de velas.
La bobina de encendido de cuatro terminales es un bloque de dos bobinas.
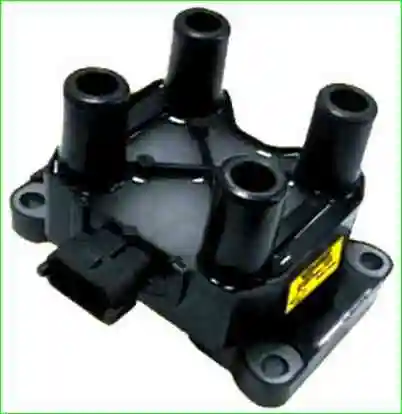
La corriente en los devanados primarios de las bobinas es controlada por el controlador, dependiendo del modo de funcionamiento del motor.
Los cables de las bujías están conectados a los terminales de los devanados secundarios (alto voltaje) de las bobinas: a un devanado, el primer y cuarto cilindro, al otro, el segundo y el tercero.
Así, la chispa salta simultáneamente en dos cilindros (1-4 o 2-3), en uno durante la carrera de compresión (chispa de trabajo) y en el otro durante la carrera de escape (ralentí).
La bobina de encendido es inseparable, se reemplaza en caso de falla.
Bujías A17DVRM o sus análogas, con resistencia de supresión de ruido de 4-10 kOhm y núcleo de cobre.
La distancia entre los electrodos de la vela es de 1,0-1,1 mm.
Tamaño de la llave hexagonal: 21 mm.
Debido a la dirección constante de la corriente en los devanados secundarios de la bobina, la corriente de chispa para cada par de velas que funcionan simultáneamente siempre fluye desde el electrodo central al electrodo lateral para una vela y desde el electrodo lateral al electrodo central. uno por el otro.
El desgaste electroerosivo de un par de bujías será diferente.
Tres fusibles (15 A cada uno) y el conector de diagnóstico del sistema de control se encuentran debajo de la cubierta del túnel del piso.
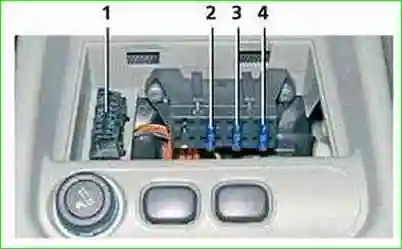
Fusibles y conector de diagnóstico del sistema de gestión del motor: 1 - conector de diagnóstico; 2 - fusible para el circuito de alimentación del relé principal; 3 - fusible para el circuito de alimentación del relé de la bomba de combustible; 4 - fusible para la alimentación constante del controlador
Además del fusible en el circuito de alimentación del sistema de control del motor, se proporciona un fusible en el extremo del cable rojo (conectado al terminal “+” de la batería), realizado en forma de una pieza. de cable gris con una sección transversal de 1 mm.
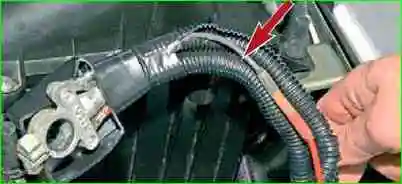
La caja de relés del sistema de control, que consta del relé principal, el relé de la bomba de combustible eléctrica y el relé del ventilador de refrigeración, está ubicada debajo de la consola del panel de instrumentos, al lado del controlador.
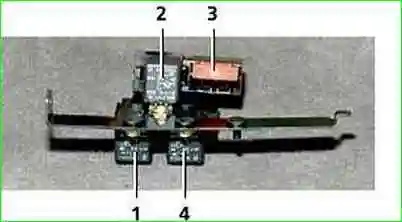
Bloque de relés del sistema de control: 1 - relé del ventilador eléctrico del sistema de refrigeración; 2 - relé de la bomba de combustible eléctrica; 3 - fusible (50 A) del electroventilador del sistema de refrigeración; 4 - relé principal
Cuando se enciende el encendido, el controlador energiza el relé de la bomba de combustible eléctrica durante 2 segundos para crear la presión necesaria en el riel de combustible.
Si durante este tiempo el arranque del cigüeñal no ha comenzado, el controlador apaga el relé y lo enciende nuevamente después del inicio del arranque.
Si el encendido se encendió tres veces seguidas sin girar el motor de arranque del cigüeñal, el siguiente encendido del relé de la bomba de combustible eléctrica se producirá solo al comenzar el arranque.
Cuando el motor está en marcha, la composición de la mezcla se regula por la duración del pulso de control aplicado a los inyectores (cuanto más largo sea el pulso, mayor será el suministro de combustible).
Cuando se arranca el motor, el controlador procesa la señal del sensor de temperatura del refrigerante para determinar la duración de los pulsos de inyección necesarios para el arranque.
Durante el arranque del motor, el combustible se suministra a los cilindros del motor "asincrónicamente", independientemente de la posición del cigüeñal.
Tan pronto como la velocidad del motor alcanza un cierto valor (dependiendo de la temperatura del refrigerante), el controlador genera un pulso en fases para encender los inyectores: el combustible se suministra a los cilindros "sincrónicamente" (en dependiendo de la posición del cigüeñal).
Al mismo tiempo, el controlador, basándose en la información recibida de los sensores, calcula el momento en que se enciende cada inyector: el combustible se inyecta una vez en un ciclo completo del cilindro correspondiente.
Si no hay señal del sensor de posición del cigüeñal (el eje no gira o el sensor y sus circuitos están defectuosos), el controlador corta el suministro de combustible a los cilindros.
El suministro de combustible se corta incluso cuando el encendido está apagado, lo que evita que la mezcla se encienda espontáneamente en los cilindros del motor.
Si el controlador detecta una falla de encendido en uno o más cilindros, el suministro de combustible a esos cilindros se detiene y el indicador de mal funcionamiento del sistema de control parpadea.
Durante el frenado del motor (con la marcha y el embrague acoplados), cuando el acelerador está completamente cerrado y la velocidad del motor es alta, no se inyecta combustible en los cilindros para reducir las emisiones de escape.
Cuando cae el voltaje en el circuito a bordo del automóvil, el controlador aumenta el tiempo de acumulación de energía en la bobina de encendido (para un encendido confiable de la mezcla combustible) y la duración del pulso de inyección (para compensar el aumento de la boquilla). horario de apertura).
Cuando aumenta el voltaje en la red de a bordo, el tiempo de acumulación de energía en la bobina de encendido y la duración del pulso disminuyen.
El controlador controla la activación del ventilador eléctrico del sistema de refrigeración (a través de un relé) en función de la temperatura del motor, el régimen del motor y el aire acondicionado (si está instalado).
El ventilador de refrigeración se encenderá si la temperatura del refrigerante es demasiado alta.
En el sistema de gestión del motor, fabricado según los estándares de toxicidad Euro-3, se utilizan dos relés para encender el ventilador eléctrico.
Dependiendo de las condiciones de funcionamiento del motor y del aire acondicionado, el controlador puede encender el ventilador eléctrico a alta o baja velocidad, a través de otro relé y una resistencia adicional
Al dar servicio y reparar el sistema de gestión del motor, apague siempre el encendido (en algunos casos es necesario desconectar el terminal del cable del terminal negativo de la batería).
Al soldar en un vehículo, desconecte los arneses de control del motor del controlador. Antes de secar el coche en una cámara de secado (después de pintarlo), retire el controlador.
Con el motor en marcha, no desconecte ni ajuste los conectores del arnés de control del motor ni los terminales de la batería.
No arranque el motor si los terminales de los cables de la batería y los terminales del cable de tierra del motor están sueltos o sucios.