Wenn die Servolenkung nicht funktioniert, dreht der Lenkmechanismus immer noch die Räder, aber die Kugelumlaufspindeln und andere Teile sind stark belastet
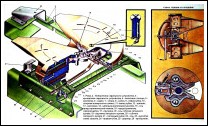
Die Anhängerkupplung ist für das Ziehen von Anhängern konzipiert, hat eine doppelte Wirkung und ermöglicht die Abfederung axialer Stöße, die bei der Bewegung in beide Richtungen auftreten.

Der Rohr-Band-Kühler befindet sich vor dem Motor. Es besteht aus einem wärmeableitenden Kern (Kern) 14, oberen 16 und unteren 8 Tanks und Befestigungselementen

Antriebsstrang des KamAZ-Autos
Das Kardangetriebe dient zur Übertragung des Drehmoments von der Welle des Getriebes oder Verteilergetriebes auf die Welle der Antriebsachse des Fahrzeugs bei wechselnden Winkeln und Abständen zwischen diesen.
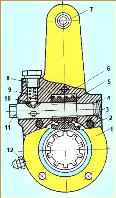
Einstellhebel (Ratsche) eines KamAZ-Fahrzeugs
Der Einstellhebel dient dazu, die Lücken zwischen den Belägen und der Bremstrommel zu verringern, die durch den Verschleiß der Reibbeläge größer werden.
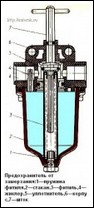
Frostschutz für das KamAZ-Luftbremssystem
Der Frostschutzschutz soll Rohrleitungen und Geräte des pneumatischen Bremsantriebs vor dem Einfrieren von Kondensat schützen