Для повышения литровой мощности в двигателе КамАЗ-7403.10 использован наддув, т. е. воздух в цилиндры подается с помощью компрессора под давлением, в 1,5-1,9 раза превышающим атмосферное
Это позволило увеличить массу воздуха, подаваемого в каждый цилиндр, и, следовательно, сжигать в цилиндрах повышенные дозы топлива.
При тех же размерах двигателя, частоте вращения коленчатого вала и числе цилиндров мощность его при наддуве возросла до 191 кВт (на 24%).
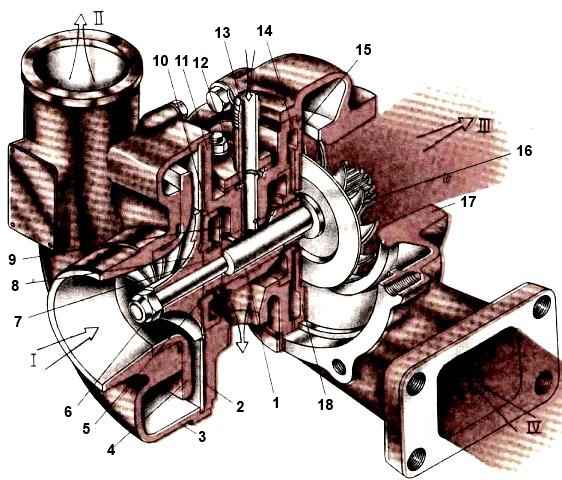
Техническая характеристика турбокомпрессора ТКР7Н
Диапазон подачи воздуха через компрессор 0,05-0,2 кг/с
Давление наддува (избыточное) при номинальной мощности двигателя, 1кПа (кгс/см 2) 54-83,4 (0,55-0,85)
Частота вращения ротора при номинальной мощности двигателя, мин -1 80 000-85 000
Температура газов на входе в турбину, °С:
- - при длительной работе, не более 650
- - при кратковременной работе (до 1 часа), не более 700
Давление смазочного масла на входе в турбокомпрессор, кПа (кгс/см 2):
- - на двигателе под нагрузкой 196,2-392,4 (2-4);
- - на двигателе без нагрузки, не менее 98,1 (1)
В связи с применением турбонаддува базовая конструкция двигателя КамАЗ-740.10 претерпела незначительные изменения.
Степень сжатия уменьшена до 16 за счет изменения формы камеры сгорания в днище поршня.
На поршнях для двигателя с турбонаддувом вместо тороидальной использована цилиндрическая камера сгорания, т. е. без вытеснителя, большего диаметра и глубины.
Это позволило увеличить объем камеры сгорания, но поршни стали невзаимозаменяемыми с теми, что применяются на базовой модели двигателя.
Топливная аппаратура двигателя с турбонаддувом претерпела следующие изменения: установлен ТНВД модели 334, отрегулированный на цикловую подачу топлива (96 мм 3/цикл); применены форсунки модели 271 с увеличенным до 0,32 мм диаметром распыливающих отверстий и повышенным давлением начала впрыскивания топлива.
Обеспечивают наддув воздуха в цилиндры два турбокомпрессора.
Один турбокомпрессор обслуживает левый ряд цилиндров, другой — правый. Они работают за счет энергии отработавших газов.
Обычно энергия отработавших газов теряется, а в турбокомпрессоре некоторая ее часть используется для работы. В результате с повышением мощности уменьшается удельный расход топлива.
Турбокомпрессоры установлены на патрубках выпускных коллекторов так, что ось ротора перпендикулярна оси коленчатого вала.
Выпускные коллекторы выполнены цельнолитыми из специального чугуна.
Под болты крепления выпускного коллектора установлены специальные сферические шайбы, компенсирующие угловые перемещения болтов при нагреве коллектора относительно головок цилиндров; от выворачивания болты крепления застопорены отгибными пластинами.
Для уплотнения газового стыка между коллектором и головками цилиндров установлены прокладки из асбостального полотна, окантованного металлическим листом, а уплотнение стыка между выпускным коллектором и патрубком обеспечивается прокладкой из листовой жаропрочной стали, так же как стыка между компрессором и патрубком.
Впускная система двигателя КамАЗ-7403.10 отличается от впускной системы базового двигателя КамАЗ-740.10 наличием дополнительных патрубков, измененной конструкцией впускных коллекторов и другим местом подсоединения индикатора засоренности воздухоочистителя.
Объединение впускных коллекторов каждого ряда цилиндров патрубком способствует снижению амплитуды колебаний давления во впускном коллекторе и уменьшению их вредного воздействия на работу турбокомпрессора.
Смазывание подшипников турбокомпрессора циркуляционное под давлением от смазочной системы двигателя. Слив масла осуществляется в картер двигателя.
Основными частями турбокомпрессора являются корпус 11 (рис. 1) подшипника, корпус 3 компрессора, корпус 17 турбины и ротор, состоящий из вала с приваренным к нему колесом 16 турбины с одной стороны и колеса 8 компрессора, закрепленного на валу гайкой 6.
Горячие отработавшие газы, выходящие из цилиндров, через коллектор поступают под давлением в корпус 17 и, расширяясь в межлопаточном пространстве, вращают колесо 16 турбины с очень большой частотой (до 85 000об/мин); по выпускной трубе и глушителю газы выходят в атмосферу.
Вал ротора вращает колесо 8 компрессора, которое засасывает из атмосферы через воздухоочиститель воздух, сжимает его и нагнетает в коллектор двигателя. Под избыточным давлением воздух поступает в цилиндры двигателя.
Поскольку температура отработавших газов на входе в турбину достигает 700 °С, колесо турбины отлито из жаропрочного сплава, а ее корпус — из чугуна.
Для уменьшения теплопередачи от корпуса турбин» к корпусу подшипника между ними установлены чугунный экран 15 и асбостальная прокладка 14.
При высоких частотах вращения подшипники качения работают не надежно, поэтому для турбокомпрессора применен подшипник 1 скольжения, выполненный по типу «качающаяся втулка» и установленный в расточку корпуса 11с зазором до 0,1 мм.
В этот зазор нагнетается масло, которое служит жидкостной подушкой, гасящей вибрацию.
От осевого смещения и проворачивания в корпусе втулка удерживается фиксатором 12, через который нагнетается масло из главной магистрали двигателя.
Масло, проходя по зазорам вдоль подшипника и его каналам, поступает в сливную полость корпуса подшипника и далее в картер двигателя.
Под давлением масло из подшипникового узла стремится перетечь в проточную часть компрессора, причем протечки масла возрастают с увеличением разрежения воздуха со стороны компрессора.
Для предотвращения поступления масла в проточную часть компрессора служит контактное уплотнение между маслоотражателем 7 и крышкой 10, представляющее собой два чугунных уплотнительных кольца 5 поршневого типа, установленные в канавки маслоотражателя.
В состав уплотнения входит маслосбрасывающий экран 9, предназначенный для отделения полости уплотнительных колец от сливной полости корпуса подшипника.
Со стороны турбины имеется аналогичное контактное уплотнение без маслосбрасывающего экрана, но здесь уплотнительные кольца при всех режимах дизеля работают с противодавлением газа, что снижает возможность протечки масла.
Вместе с тем эти кольца работают в условиях более высоких температур, что создает опасность закоксовки канавок и потери подвижности колец. Это возможно при резкой остановке двигателя, работавшего над нагрузкой.
Если же перед остановкой двигателя дать поработать ему 3-5 мин на холостом ходу, то повышенная температура в зоне уплотнительных колец не наблюдается, а значит, и не происходит коксования масла в канавках ротора.
Турбокомпрессор является наиболее удаленной от масляного насоса точкой смазывания.
Это обстоятельство требует соблюдения определенных условий пуска и прогрева двигателя, особенно при отрицательных температурах окружающего воздуха.
В момент пуска двигателя масляный насос подает масло к подшипникам турбокомпрессора с некоторой задержкой по времени, вызванной гидродинамическим сопротивлением трубопроводов на линии всасывания масляного насоса и каналов на линии нагнетания масла.
Задержка поступления масла изменяет гидродинамические условия работы подшипникового узла, что при нарушении режима прогрева дизеля после пуска может привести к отказу турбокомпрессора.
Во избежание отказа прогрев двигателя производят на частоте вращения коленчатого вала менее 1500 об/мин до тех пор, пока давление масла в смазочной системе не поднимется выше 100 кПа (1 кгс/см 2 на манометре).
После смены масла в картере двигателя и фильтрующих элементов полнопоточного фильтра рекомендуется проворачивать коленчатый вал перед пуском стартером в течение 10-15 с при выключенной подаче топлива.
При появлении давления в главной масляной магистрали, определяемом по манометру, можно пускать двигатель.
Исследования показали, что при работе двигателя в режиме холостого хода разрежение перед кольцами контактного уплотнения за колесом компрессора достигает максимальной величины, что способствует возникновению протечки масла в проточную часть компрессора и далее в цилиндры двигателя.
Длительная работа двигателя в режиме холостого хода вызывает образование синего дыма на выхлопе, повышенный расход масла, нагарообразование на проточной части турбины.
Чтобы избежать этих неисправностей, например при накачке воздуха в ресиверы тормозной системы, рекомендуется поддерживать частоту вращения коленчатого вала в пределах 1200-1600 об/мин.