Для підвищення літрової потужності в двигуні КамАЗ-7403.10 використано наддув, тобто повітря в циліндри подається за допомогою компресора під тиском, що в 1,5-1,9 раза перевищує атмосферне
Це дозволило збільшити масу повітря, що подається в кожен циліндр, і, отже, спалювати в циліндрах підвищені дози палива.
При тих же розмірах двигуна, частоті обертання колінчастого валу та кількості циліндрів потужність його при наддуві зросла до 191 кВт (на 24%).
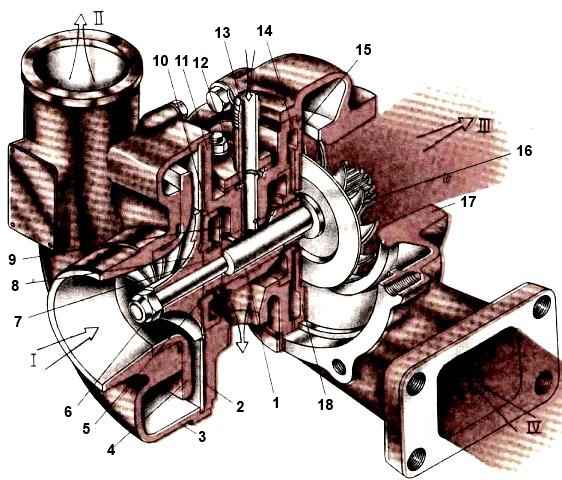
Технічна характеристика турбокомпресора ТКР7Н
Діапазон подачі повітря через компресор 0,05-0,2 кг/с
Тиск наддуву (надлишковий) при номінальній потужності двигуна, 1кПа (кгс/см 2) 54-83,4 (0,55-0,85)
Частота обертання ротора при номінальній потужності двигуна, хв -1 80 000-85 000
Температура газів на вході в турбіну, °С:
- - при тривалій роботі не більше 650
- - при короткочасній роботі (до 1 години) не більше 700
Тиск мастила на вході в турбокомпресор, кПа (кгс/см 2):
- - на двигуні під навантаженням 196,2-392,4 (2-4);
- - на двигуні без навантаження не менше 98,1 (1)
У зв'язку із застосуванням турбонаддува базова конструкція двигуна КамАЗ-740.10 зазнала незначних змін.
Ступінь стиснення зменшено до 16 за рахунок зміни форми камери згоряння в днище поршня.
На поршнях для двигуна з турбонаддувом замість тороїдальної використана циліндрична камера згоряння, тобто без витіснювача, більшого діаметра та глибини.
Це дозволило збільшити об'єм камери згоряння, але поршні стали незамінними з тими, що застосовуються на базовій моделі двигуна.
Паливна апаратура двигуна з турбонаддувом зазнала наступних змін: встановлено ТНВД моделі 334, відрегульований на циклову подачу палива (96 мм 3/цикл); застосовані форсунки моделі 271 зі збільшеним до 0,32 мм діаметром отворів, що розпилюють, і підвищеним тиском початку впорскування палива.
Забезпечують наддув повітря в циліндри два турбокомпресори.
Один турбокомпресор обслуговує лівий ряд циліндрів, інший правий. Вони працюють за рахунок енергії відпрацьованих газів.
Зазвичай енергія газів, що відпрацювали, втрачається, а в турбокомпресорі деяка її частина використовується для роботи. В результаті з підвищенням потужності зменшується питома витрата палива.
Турбокомпресори встановлені на патрубках випускних колекторів так, що вісь ротора перпендикулярна осі колінчастого валу.
Випускні колектори виконані цільнолитими зі спеціального чавуну.
Під болти кріплення випускного колектора встановлені спеціальні сферичні шайби, що компенсують кутові переміщення болтів при нагріванні колектора щодо головок циліндрів; від вивертання болти кріплення застопорені відгинними пластинами.
Для ущільнення газового стику між колектором і головками циліндрів встановлені прокладки з азбостального полотна, окантованого металевим листом, а ущільнення стику між випускним колектором і патрубком забезпечується прокладкою з листової жароміцної сталі, так само як стику між компресором і патрубком.
Впускна система двигуна КамАЗ-7403.10 відрізняється від впускної системи базового двигуна КамАЗ-740.10 наявністю додаткових патрубків, зміненою конструкцією впускних колекторів та іншим місцем під'єднання індикатора засміченості очищувача повітря.
Об'єднання впускних колекторів кожного ряду циліндрів патрубком сприяє зниженню амплітуди коливань тиску у впускному колекторі та зменшенню їх шкідливого впливу на роботу турбокомпресора.
Змащування підшипників турбокомпресора циркуляційне під тиском від мастильної системи двигуна. Злив масла здійснюється в картер двигуна.
Основними частинами турбокомпресора є корпус 11 (рис. 1) підшипника, корпус 3 компресора, корпус 17 турбіни і ротор, що складається з валу з привареним до нього колесом 16 турбіни з одного боку та 8 колеса компресора, закріпленого на валу гайкою 6.
Гарячі відпрацьовані гази, що виходять з циліндрів, через колектор надходять під тиском в корпус 17 і, ширяючись в міжлопатковому просторі, обертають колесо 16 турбіни з дуже великою частотою (до 85 000об/хв); по випускній трубі та глушнику гази виходять в атмосферу.
Вал ротора обертає колесо 8 компресора, яке засмоктує з атмосфери через очищувач повітря, стискає його і нагнітає в колектор двигуна. Під надмірним тиском повітря надходить у циліндри двигуна.
Оскільки температура газів, що відпрацювали, на вході в турбіну досягає 700 °С, колесо турбіни відлито з жароміцного сплаву, а її корпус — з чавуну.
Для зменшення теплопередачі від корпусу турбін» до корпусу підшипника між ними встановлені чавунний екран 15 та азбостальна прокладка 14.
При високих частотах обертання підшипники кочення працюють не надійно, тому для турбокомпресора застосований підшипник 1 ковзання, виконаний за типом «втулка, що коливається» і встановлений у розточування корпусу 11с зазором до 0,1 мм.
В цей зазор нагнітається олія, яка служить рідинною подушкою, що гасить вібрацію.
Від осьового зміщення та провертання в корпусі втулка утримується фіксатором 12, через який нагнітається олія з головної магістралі двигуна.
Масло, проходячи по зазорах вздовж підшипника та його каналів, надходить у зливну порожнину корпусу підшипника і далі в картер двигуна.
Під тиском масло з підшипникового вузла прагне перетекти в проточну частину компресора, причому протікання олії зростають із збільшенням розрідження повітря з боку компресора.
Для запобігання надходженню масла в проточну частину компресора служить контактне ущільнення між масловідбивачем 7 і кришкою 10, що являє собою два чавунні ущільнювальні кільця 5 поршневого типу, встановлені в канавки масловідбивача.
До складу ущільнення входить олійний екран 9, призначений для відділення порожнини ущільнювальних кілець від зливної порожнини корпусу підшипника.
З боку турбіни є аналогічне контактне ущільнення без маслоскидаючого екрану, але тут кільця ущільнювачів при всіх режимах дизеля працюють з протитиском газу, що знижує можливість протікання масла.
Водночас ці кільця працюють в умовах більш високих температур, що створює небезпеку закоксування канавок та втрати рухливості кілець. Це можливо при різкій зупинці двигуна, який працював над навантаженням.
Якщо ж перед зупинкою двигуна дати попрацювати йому 3-5 хв на холостому ходу, то підвищена температура в зоні ущільнювальних кілець не спостерігається, а значить, і не відбувається коксування олії в канавках ротора.
Турбокомпресор є найбільш віддаленою від масляного насоса точкою змащування.
Ця обставина вимагає дотримання певних умов пуску та прогріву двигуна, особливо при негативних температурах навколишнього повітря.
У момент пуску двигуна масляний насос подає масло до підшипників турбокомпресора з деякою затримкою за часом, спричиненою гідродинамічним опором трубопроводів на лінії всмоктування масляного насоса та каналів на лінії нагнітання масла.
Затримка надходження олії змінює гідродинамічні умови роботи підшипникового вузла, що при порушенні режиму прогріву дизеля після пуску може призвести до відмови турбокомпресора.
Для уникнення відмови прогрів двигуна виробляють на частоті обертання колінчастого валу менше 1500 об/хв доти, поки тиск масла в мастильній системі не підніметься вище 100 кПа (1 кгс/см 2 на манометрі) .
Після зміни масла в картері двигуна та фільтруючих елементів повнопоточного фільтра рекомендується провертати колінчастий вал перед пуском стартером протягом 10-15 с при вимкненій подачі палива.
При появі тиску в головній масляній магістралі, що визначається за манометром, можна пускати двигун.
Дослідження показали, що при роботі двигуна в режимі холостого ходу розрідження перед кільцями контактного ущільнення за колесом компресора досягає максимальної величини, що сприяє виникненню протікання масла в проточну частину компресора і далі в циліндри двигуна.
Тривала робота двигуна в режимі холостого ходу викликає утворення синього диму на вихлопі, підвищену витрату масла, нагароутворення на проточній частині турбіни.
Щоб уникнути цих несправностей, наприклад при накачуванні повітря в ресивери гальмівної системи, рекомендується підтримувати частоту обертання колінчастого валу в межах 1200-1600 об/хв.