Um die Literleistung im KamAZ-7403.10-Motor zu erhöhen, wird eine Aufladung verwendet, d. h. den Zylindern wird Luft mit einem Kompressor unter einem Druck zugeführt, der 1,5-1,9-mal höher ist als der atmosphärische Druck.
Dadurch war es möglich, die jedem Zylinder zugeführte Luftmasse zu erhöhen und infolgedessen höhere Kraftstoffmengen in den Zylindern zu verbrennen.
Bei gleichen Motorabmessungen, gleicher Kurbelwellendrehzahl und gleicher Zylinderzahl erhöhte sich die Leistung beim Aufladen auf 191 kW (um 24 %).
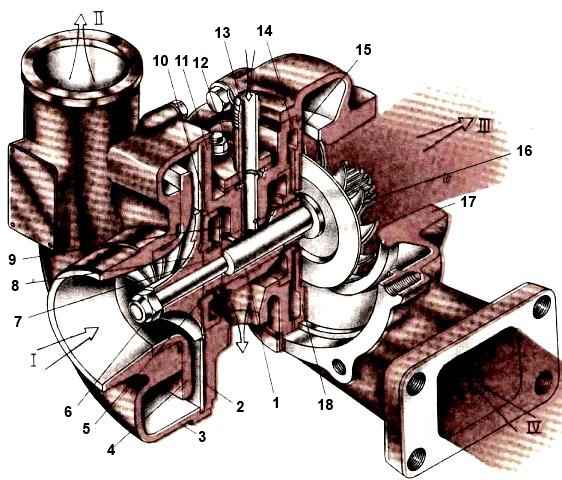
Technische Eigenschaften des TKR7N-Turboladers
Luftzufuhrbereich durch den Kompressor 0,05–0,2 kg/s
Ladedruck (Überschuss) bei Nennmotorleistung, 1 kPa (kgf/cm 2) 54–83,4 (0,55–0,85)
Rotorgeschwindigkeit bei Nennmotorleistung, min. -1 80.000–85.000
Temperatur der Gase am Turbineneintritt, °C:
- - im Langzeitbetrieb nicht mehr als 650
- - für kurzfristigen Betrieb (bis zu 1 Stunde), nicht mehr als 700
Schmieröldruck am Einlass des Turboladers, kPa (kgf/cm 2):
- - am Motor unter Last 196,2-392,4 (2-4);
- - am Motor ohne Last, nicht weniger als 98,1 (1)
Aufgrund der Verwendung von Turboaufladung wurden geringfügige Änderungen am Grunddesign des KamAZ-740.10-Motors vorgenommen.
Das Verdichtungsverhältnis wird durch die Änderung der Form des Brennraums im Kolbenboden auf 16 reduziert.
Die Kolben eines Turbomotors verwenden einen zylindrischen Brennraum anstelle eines toroidalen, d. h. ohne Verdränger, mit größerem Durchmesser und größerer Tiefe.
Dadurch konnte das Volumen der Brennkammer vergrößert werden, die Kolben waren jedoch nicht mehr mit denen des Basismotormodells austauschbar.
Die Kraftstoffausrüstung des Turbomotors hat folgende Änderungen erfahren: Es wurde eine Einspritzpumpe Modell 334 eingebaut, die auf zyklische Kraftstoffzufuhr (96 mm 3/Zyklus) eingestellt ist; Es werden Einspritzdüsen des Modells 271 mit einem auf 0,32 mm vergrößerten Durchmesser der Spritzlöcher und einem erhöhten Druck zu Beginn der Kraftstoffeinspritzung verwendet.
Zwei Turbolader sorgen für Luftdruck in den Zylindern.
Ein Turbolader versorgt die linke Zylinderbank, der andere die rechte Zylinderbank. Sie nutzen die Energie von Abgasen.
Üblicherweise geht die Energie der Abgase verloren und in einem Turbolader wird ein Teil davon für den Betrieb genutzt. Dadurch sinkt mit zunehmender Leistung der spezifische Kraftstoffverbrauch.
Turbolader werden an den Abgaskrümmerrohren so installiert, dass die Rotorachse senkrecht zur Achse der Kurbelwelle steht.
Die Abgaskrümmer bestehen aus massivem Gusseisen.
Unter den Befestigungsschrauben des Abgaskrümmers sind spezielle Kugelscheiben angebracht, die die Winkelbewegungen der Schrauben ausgleichen, wenn der Krümmer relativ zu den Zylinderköpfen erhitzt wird; Die Befestigungsbolzen sind mit Klappblechen gegen Herausdrehen gesichert.
Um die Gasverbindung zwischen dem Krümmer und den Zylinderköpfen abzudichten, werden Dichtungen aus Asbeststahl mit eingefasstem Blech eingebaut, und die Abdichtung der Verbindung zwischen dem Abgaskrümmer und dem Rohr wird durch eine Dichtung aus Hitze gewährleistet -beständiges Stahlblech, sowie die Verbindung zwischen Kompressor und Rohr.
Das Ansaugsystem des KamAZ-7403.10-Motors unterscheidet sich vom Ansaugsystem des Basismotors KamAZ-740.10 durch zusätzliche Rohre, ein geändertes Design der Ansaugkrümmer und einen anderen Anschlusspunkt für die Luftfilter-Verstopfungsanzeige.
Die Kombination der Ansaugkrümmer jeder Zylinderreihe mit einem Rohr trägt dazu bei, die Amplitude der Druckschwankungen im Ansaugkrümmer zu reduzieren und deren schädliche Auswirkungen auf den Betrieb des Turboladers zu verringern.
Die Turboladerlager werden durch Zirkulation unter Druck vom Motorschmiersystem geschmiert. Das Öl wird in das Kurbelgehäuse des Motors abgelassen.
Die Hauptteile des Turboladers sind das Lagergehäuse 11 (Abb. 1), das Verdichtergehäuse 3, das Turbinengehäuse 17 und der Rotor, bestehend aus einer Welle mit einem einseitig daran angeschweißten Turbinenrad 16 und einem Verdichterrad 8 mit einer Mutter 6 an der Welle befestigt.
Heiße Abgase, die die Zylinder verlassen, gelangen unter Druck durch den Verteiler in das Gehäuse 17 und Das Turbinenrad 16 dehnt sich im Zwischenschaufelraum aus und dreht sich mit einer sehr hohen Frequenz (bis zu 85.000 U/min). Gase entweichen durch das Auspuffrohr und den Schalldämpfer in die Atmosphäre.
Die Rotorwelle dreht das Kompressorrad 8, das durch den Luftfilter Luft aus der Atmosphäre ansaugt, sie komprimiert und in den Motorverteiler pumpt. Unter Überdruck gelangt Luft in die Motorzylinder.
Da die Temperatur der Abgase am Turbineneintritt 700 °C erreicht, ist das Turbinenrad aus einer hitzebeständigen Legierung gegossen und sein Körper besteht aus Gusseisen.
Um die Wärmeübertragung vom Turbinengehäuse zum Lagergehäuse zu reduzieren, sind dazwischen ein Gusseisensieb 15 und eine Asbeststahldichtung 14 eingebaut.
Bei hohen Drehzahlen arbeiten Wälzlager nicht zuverlässig, daher verwendet der Turbolader das Gleitlager 1, das vom Typ „Schwingbuchse“ gefertigt und mit einem Spalt von bis zu 0,1 mm in der Gehäusebohrung 11 eingebaut ist.
In diesen Spalt wird Öl gepumpt, das als Flüssigkeitspolster dient und Vibrationen dämpft.
Die Buchse wird durch die Klemme 12, durch die Öl aus der Hauptleitung des Motors gepumpt wird, gegen axiale Verschiebung und Drehung im Gehäuse gehalten.
Das Öl gelangt durch die Spalten entlang des Lagers und seiner Kanäle in den Abflusshohlraum des Lagergehäuses und dann in das Kurbelgehäuse des Motors.
Unter Druck neigt Öl aus der Lagerbaugruppe dazu, in den Strömungsteil des Kompressors zu fließen, und Öllecks nehmen mit zunehmender Luftverdünnung auf der Kompressorseite zu.
Um zu verhindern, dass Öl in den Strömungsweg des Kompressors gelangt, wird zwischen dem Ölabweiser 7 und dem Deckel 10 eine Kontaktdichtung verwendet, die aus zwei kolbenartigen Gusseisendichtringen 5 besteht, die in den Nuten des Ölabweisers installiert sind .
Die Dichtung umfasst ein Ölablasssieb 9, das den Hohlraum der Dichtungsringe vom Ablasshohlraum des Lagergehäuses trennt.
Auf der Turbinenseite gibt es eine ähnliche Kontaktdichtung ohne Ölaustrittssieb, hier arbeiten die Dichtringe jedoch in allen Dieselmodi mit Gasgegendruck, was die Möglichkeit einer Ölleckage verringert.
Diese Ringe arbeiten jedoch bei höheren Temperaturen, wodurch die Gefahr einer Verkokung der Nuten und eines Verlusts der Ringbeweglichkeit besteht. Dies ist möglich, wenn der Motor plötzlich stoppt, während er an der Last arbeitet.
Wenn Sie den Motor vor dem Abstellen 3-5 Minuten im Leerlauf laufen lassen, ist keine erhöhte Temperatur im Bereich der Dichtringe zu beobachten, was zu einer Verkokung des Öls im Rotor führt Rillen treten nicht auf.
Der Turbolader ist die Schmierstelle, die am weitesten von der Ölpumpe entfernt ist.
Dieser Umstand erfordert die Einhaltung bestimmter Bedingungen zum Starten und Aufwärmen des Motors, insbesondere bei negativen Umgebungstemperaturen.
Im Moment des Motorstarts versorgt die Ölpumpe die Lager des Turboladers mit einer gewissen Zeitverzögerung mit Öl, die durch den hydrodynamischen Widerstand der Rohrleitungen an der Saugleitung der Ölpumpe und der Kanäle an der Ölauslassleitung verursacht wird.
Eine Verzögerung des Ölflusses verändert die hydrodynamischen Betriebsbedingungen der Lagerbaugruppe, was bei Verletzung des Aufwärmmodus des Dieselmotors nach dem Start zum Ausfall des Turboladers führen kann.
Um einen Ausfall zu vermeiden, wird der Motor bei einer Kurbelwellendrehzahl von weniger als 1500 U/min aufgewärmt, bis der Öldruck im Schmiersystem über 100 kPa (1 kgf/cm 2 am Manometer) ansteigt ) .
Nach dem Ölwechsel im Motorkurbelgehäuse und den Filterelementen des Hauptstromfilters empfiehlt es sich, die Kurbelwelle vor dem Start mit dem Anlasser für 10-15 Sekunden bei abgeschalteter Kraftstoffzufuhr zu drehen.
Wenn in der Hauptölleitung ein Druck auftritt, der am Manometer gemessen wird, können Sie den Motor starten.
Untersuchungen haben gezeigt, dass im Leerlauf des Motors der Unterdruck vor den Kontaktdichtringen hinter dem Kompressorrad einen Maximalwert erreicht, was zur Ölleckage in den Kompressorströmungsweg und weiter in die Motorzylinder beiträgt.
Längerer Betrieb des Motors im Leerlauf führt zur Bildung von blauem Rauch im Abgas, erhöhtem Ölverbrauch und Kohlenstoffablagerungen im Strömungsweg der Turbine.
Um diese Störungen zu vermeiden, beispielsweise beim Pumpen von Luft in die Bremssystembehälter, wird empfohlen, die Kurbelwellendrehzahl im Bereich von 1200–1600 U/min zu halten.