Die beim Bremsen aus dem Hahn austretende Luft wird durch den an den atmosphärischen Auslass (II) angeschlossenen Luftkanal nach außen abgeleitet.
Demontage, Montage und Einstellung des Krans
Spannt den Gewindebohrer in einen Schraubstock mit weichen Backen und befestigt ihn mit dem Körper 1 (Abb. 1), wobei die Abdeckung 5 nach oben zeigen muss.
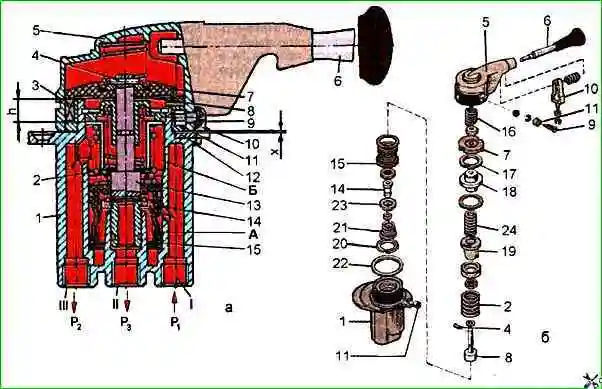
Achsen 9 der Rollen 11 abschrauben, dabei den Deckel 5 mit der Hand festhalten und mit der Feder 16 abnehmen.
Anschließend mit einem Körner den Bolzen 4 vorsichtig herausschlagen und die Stangennocke 7 mit Unterlegscheibe entfernen.
Mit einer Rundzange den Druckring 17 entfernen und die Stangenführung 18, die Federn 2 und 29, die Federplatte 19 und die Stange 8 aus dem Gehäuse 1 herausnehmen.
Körper 1 des Hahns aus dem Schraubstock lösen und Kolben 15 mit Ventil 14 als Baugruppe mit Hilfe eines durch den atmosphärischen Auslass (III) eingeführten Holzdorns herausnehmen.
Um Ventil 14 von Kolben 15 zu demontieren, ist es notwendig, den Druckring 20 mit einer Rundzange zu entfernen. Halten Sie dabei Kolben 15 in der Hand und seien Sie vorsichtig, da sich im Kolben eine zusammengedrückte Kegelfeder 21 befindet.
Nach der Demontage der Bremsventilteile der Feststellbremsanlage müssen diese mit sauberem Benzin oder Aceton gewaschen, getrocknet und sorgfältig geprüft werden.
Risse, Haarrisse und andere mit dem Auge erkennbare Mängel sind auf der Oberfläche von Karosserieteilen nicht zulässig. Die Teile müssen von Rost und eingebrannten Ablagerungen gereinigt werden.
Alle Gummiteile müssen durch neue ersetzt werden. Bemalen Sie die Federn mit Lack oder Farbe.
Bevor Sie die Kranteile zusammenbauen, schmieren Sie diese per Hand mit einer dünnen Schicht TSIA-TIM-221-Fett.
Ventile, Gummidichtringe und andere Gummiteile müssen sorgfältig montiert werden, um Beschädigungen zu vermeiden.
Das Vorhandensein von Kratzern, Schnitten und anderen Defekten auf der Oberfläche dieser Teile ist nicht zulässig.
Die Montage des Hahns sollte mit der Untermontage des Ventils 14 mit dem Kolben 15 beginnen und auf einen flachen Tisch gelegt werden.
Ventil 14, Stützscheibe 23 (mit dem Flansch zum Gummielement des Ventils hin ausgerichtet), Kegelfeder 21 und Druckring 20 (mit einer Rundzange) in den Kolben einbauen.
Dann muss der Körper 1 in einen Schraubstock eingespannt und der Kolben 15 zusammen mit dem Ventil 14 darin installiert werden (siehe Abb. 1).
Feder 2 mit Platte 19 einbauen.
Stange 8 mit Unterlegscheibe, Feder 2, Platte 19 zusammenbauen und in Gehäuse 1 einbauen. Anschließend Feder 24 und Stangenführung 18 einbauen und dabei darauf achten, dass sich darauf ein Gummidichtring befindet.
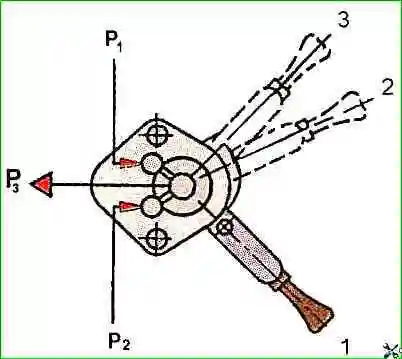
Anschließend können Sie bei Bedarf die Kraft der Feder 2 anpassen (siehe Abb. 2). Dazu ist es notwendig, die Feder 2 auf eine Größe von x = 13,8...13,9 mm vom oberen Ende des Körpers 1 bis zum oberen Ende der Platte 19 zusammenzudrücken. In diesem Fall sollte die Federkraft gleich 130 sein -155 N.
Ist diese Kraft geringer als der angegebene Wert, dann montieren Sie Einstellscheiben (Teil 100-3537095 oder 100-3537097), um die Federkraft auf den erforderlichen Wert zu bringen.
Der Einbau der Unterlegscheibe 1003537095 erhöht die Federkraft um 42,5 N und sorgt für einen Druckabfall von 0,035 MPa, während der Einbau der Unterlegscheibe 100-3537097 die Federkraft um 22,5 N bzw. 0,021 MPa erhöht.
Nach dem Einstellen der Federn wird die Nocke der Stange 7 aufgesetzt und der Stift 4 vorsichtig mit einem Dorn in die Stange 8 eingebracht. Anschließend werden die Feder 16 und die Abdeckung 5 eingebaut, nachdem die Rollen 11 in Die beiden Achsen 9 einschrauben und damit den Deckel 5 fixieren.
Messen Sie den Mindestspalt zwischen Deckel 5 und Unterlegscheibe 22, dieser sollte 0,15 mm nicht überschreiten.
Ist dieser Spalt größer, werden Passscheiben benötigt. 100-3537092 Dicke 0,15 mm, det. 100-3537093 Dicke 0,2 mm und Details. 100-3537094 0,3 mm dick, zusammenfügen und auf der Scheibe 22 zwischen Deckel 5 und Korpus 1 so auflegen, dass der Spalt den angegebenen Wert nicht überschreitet.
Puck 22 Teile. 100-3537091 0,5mm dicke Reste am Boden liegen bleiben. Die Unterlegscheiben müssen mit Fett TSIA-TIM-221, GOST 9433-60, geschmiert werden.
Überprüfen Sie, wie leicht sich der Griff in seine Ausgangsposition zurückbringen lässt, wenn er in einem Winkel von 40–45° und 65–70° geneigt wird.
Überprüfung der Kranfunktionalität
Installieren Sie den Kran auf dem Prüfstand und schließen Sie ihn gemäß dem in Reis. 2.
Füllen Sie Luft mit einem Druck von 0,75 MPa an den Auslass, wobei der Druck in Auslass 1 dem Druck in Auslass 1 entsprechen sollte.
Bewegen Sie den Zapfhahngriff dreimal von Position 1 in Position 3 und zurück.
Bewegen Sie anschließend den Hahngriff langsam von Position 1 in Position 3.
Beim Bewegen des Griffs darf kein Klemmen auftreten und er muss sich leicht in Position 3 fixieren lassen.
Wenn der Griff aus Position 1 um einen Winkel von bis zu 70° gedreht wird, sollte er automatisch in Position 1 zurückkehren.
Drehen Sie den Griff langsam aus Position 1. Beim Drehen des Griffs um 8-10° sollte der Druck im Auslass (II) abfallen, jedoch nicht mehr als 0,15 MPa.
Bei weiterer Drehung des Griffs sollte ein gleichmäßiger Druckabfall im Ausgang (II) auf 0 erfolgen.
Um den Hahn auf Dichtheit zu prüfen, muss bei den Griffstellungen 1 und 3 Luft unter einem Druck von 0,75 MPa in den Auslass (I) geleitet werden.
Beim Einseifen darf die Entstehung von Luftblasen 1 Minute lang nicht zugelassen werden.