Ремонт и осмотр насоса гидроусилителя, клапана управления и силового цилиндра
Для проведения ремонта или осмотра состояния деталей необходимо разобрать насос гидроусилителя, клапан управления и силовой цилиндр.
Разборка и проверка насоса гидроусилителя
Перед разборкой насос (рис. 1) необходимо снять с автомобиля, слить масло, очистить и промыть наружную поверхность насоса.
- Рис. 1. Насос гидроусилителя:
1. Шкив.
2. Фильтр.
3. Сапун.
4. Крышка бачка.
5. Бачок.
6. Коллектор.
7. Предохранительный клапан.
8. Перепускной клапан.
9. Крышка насоса.
10. Распределительный диск.
11. Статор.
12. Ротор.
13. Вал.
14. Корпус насоса.
Порядок разборки и проверки насоса:
- 1. Снять крышку бачка и фильтры.
2. Снять бачок 5.
3. Установить насос так, чтобы его вал был расположен вертикально, а шкив находился внизу, и снять крышку 9 насоса. При снятии крышки удерживать перепускной клапан 8 от выпадения.
4. Отметить положение распределительного диска относительно статора 11 и снять его со штифтов.
5. Отметить положение статора 11 относительно корпуса 14 насоса и снять статор (стрелка на статоре указывает направление вращения вала насоса).
6. Снять ротор 12 вместе с лопастями. Статор, ротор и лопасти насоса подобраны на заводе индивидуально, поэтому их комплектность при разборке нарушать нельзя.
7. Снять шкив 1 (при необходимости), стопорное кольцо и вал 13 насоса вместе с передним подшипником.
8. Проверить свободное перемещение перепускного клапана в крышке насоса и отсутствие забоин или износа. Клапан и крышка насоса подобраны на заводе индивидуально, поэтому их комплектность при разборке нарушать нельзя.
9. Проверить затяжку седла предохранительного клапана 7 и в случае необходимости подтянуть его.
10. Проверить каналы деталей насоса и очистить их.
11. Проверить, нет ли задиров или износа на торцовых поверхностях ротора, корпуса и распределительного диска. В случае незначительных задиров или износа притереть эти поверхности на плите, после чего детали тщательно промыть.
12. Проверить, свободно ли перемещаются в пазах лопасти 4 и не изношены ли они.
13. Осмотреть резиновые уплотнители. Затвердевшие, с трещинами и другими дефектами уплотнители заменить.
Технически исправное состояние насоса определяется двумя показателями:
- Максимальным давлением, которое создает насос.
- Шумностью при работе.
**Примечание:**
Износ отдельных деталей, кроме явных задиров, не может служить основанием для их замены. Ротор, статор и лопасти при сборке на заводе сортируют на три группы по длине. В насос устанавливают детали только одной группы. При ремонте насоса ротор, статор и лопасти заменяют также комплектно.
**Размеры для сортировки ротора, статора и лопастей приведены в табл. 1.**
**Золотник перепускного клапана и крышку насоса также подбирают комплектно, сортируя на три группы по диаметрам отверстия и шейки. Размеры для сортировки приведены в табл. 2.**
**При повышенной шумности работы насоса:**
Заменить шариковый подшипник валика насоса.
**Примечание:**
Насос унифицирован с насосом автомобиля ЗИЛ-130, кроме шкива и пружины перепускного клапана.
Сборка насоса гидроусилителя
- 1. Перед сборкой все детали тщательно промыть и просушить. Не следует протирать детали концами и тряпками, оставляющими на деталях нитки, ворсинки и т.п.
2. Установить статор, ротор с лопастями и распределительный диск в соответствии с метками, нанесенными при разборке, и стрелкой, указывающей направление вращения. Фаска шлицевого отверстия должна быть обращена к корпусу насоса.
3. Установить крышку с перепускным клапаном. Шестигранник седла должен быть обращен внутрь отверстия.
4. Равномерно затянуть болты крепления крышки. Момент затяжки болтов: 2,1–2,8 кгс·м.
5. Момент затяжки болтов, крепящих бачок: 0,8–1 кгс·м.
6. Момент затяжки гайки, крепящей шкив насоса: 5–6,5 кгс·м.
7. Вал насоса должен вращаться свободно, без заеданий.
Разборка клапана управления
- 1. Слить масло из системы гидроусилителя руля.
2. Отсоединить трубки и шланги от клапана управления.
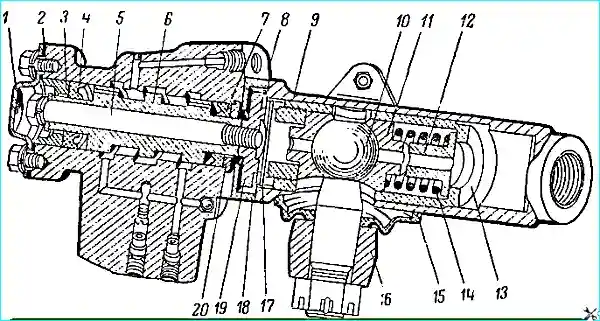
Рис. 2. Клапан управления гидроусилителя рулевого управления:
- 1. Крышка.
2. Прокладка.
3. Крышка золотника.
4. Манжета.
5. Болт крепления золотника.
6. Золотник.
7. Манжета.
8. Корпус клапана управления.
9. Наконечник продольной тяги.
10. Шаровой палец.
11. Сухарь шарового пальца.
12. Ограничитель.
13. Стакан.
14. Пружина.
15. Уплотнитель пальца.
16. Рулевая сошка.
17. Штифт.
18. Переходник.
19. Гайка.
20. Крышка.
- **Порядок разборки:**
1. Снять крышку 1 клапана управления.
2. Вывернуть центральный болт 5.
3. Отвернуть болты крепления корпуса клапана управления к продольной тяге и снять клапан управления.
4. Отвернуть винт крепления переходника и снять переходник 18.
5. Вынуть крышки и манжеты с обеих сторон клапана.
6. Вынуть золотник 6 клапана управления.
7. Если бронзовые седла сильно обмяты и деформированы, выпрессовать их и запрессовать новые. - **Определение технического состояния деталей клапана:**
- На рабочих шейках золотника не должно быть забоин, задиров или глубоких рисок. При необходимости зачистить отделочным бруском, не заваливая острых кромок.
- Золотник должен свободно, без заеданий перемещаться в корпусе клапана. Прочистить два отверстия в шейках золотника.
- Уплотнительные манжеты 4 и 7 должны сохранять эластичность, не иметь трещин, выхватов и других дефектов.
- Тщательно промыть внутренние полости и каналы корпуса клапана.
**Примечание:**
Золотник и корпус клапана сортируют на три группы по диаметру шеек и отверстия. Размеры деталей по группам приведены в табл. 3.
Сборка клапана управления
- 1. Установить на продольную тягу переходник 18 и затянуть винт его крепления. Следить, чтобы на сопрягаемых торцах не было забоин и загрязнений.
2. Собрать в корпусе клапана золотник 6, манжеты 4 и 7 и крышки 3 и 20.
3. Золотник и манжеты перед установкой смазать турбинным или веретенным маслом.
4. Вставлять золотник в корпус без перекосов, не прикладывая силу.
5. Собирать корпус клапана и золотник по сопряженному диаметру только одной группы.
6. Убедиться, что крайняя шейка золотника большего диаметра обращена к продольной тяге.
7. Болты крепления корпуса клапана окончательно затягивать после затяжки центрального болта 5.
8. Проверить свободу перемещения золотника в корпусе.
9. Установить крышку 1, заменив пробковую прокладку 2.
10. Если шланги не сразу присоединяют к клапану, заглушить места их присоединения заглушками.
Разборка силового цилиндра
Перед разборкой силового цилиндра рекомендуется проверить свободу перемещения штока с поршнем из одного крайнего положения в другое.
- Рис. 3. Силовой цилиндр гидроусилителя рулевого управления:
1. Цилиндр.
2. Шток с поршнем.
3. Штуцер.
4. Болт штуцера.
5. Контргайка крепления головки.
6. Гайка крепления головки.
7. Головка цилиндра.
8. Пружина манжеты.
9. Чашка пружины.
10. Манжета.
11. Крышка.
12. Регулировочные шайбы.
13. Стопорное кольцо.
14. Войлочный сальник.
15. Уплотнительные кольца. - **Порядок разборки:**
1. Отпустить контргайку 5.
2. Отвернуть гайку 6 крепления головки 7 цилиндра.
3. Вынуть из цилиндра головку 7 вместе со штоком 2.
4. Вынуть шток из головки.
5. В случае износа шарового шарнира разобрать шарнир и заменить изношенные детали. - **Определение технического состояния деталей цилиндра:**
- На внутренней поверхности цилиндра не должно быть задиров.
- Поршневые кольца должны прилегать по всей окружности цилиндра или к цилиндрическому калибру диаметром 50 мм.
- Поршневые кольца должны свободно проворачиваться в канавках поршня.
- На хромированной поверхности штока не должно быть выработки.
- В отверстии под шток в головке 7 цилиндра не должно быть надиров.
- Латунные шайбы 12 не должны быть деформированы.
- Резиновая манжета 10 должна быть эластичной и не иметь повреждений.
- Войлочный сальник 14 должен обжимать шток. Если сальник загрязнен или не обжимает шток, его нужно заменить.
- Резиновые уплотнительные кольца на головке цилиндра должны сохранять эластичность.
Сборка силового цилиндра
- 1. Шток с поршнем и внутреннюю поверхность цилиндра при сборке смазать турбинным или веретенным маслом.
2. Поршневые кольца на поршне установить замками в разные стороны.
3. Гайку 6 крепления головки цилиндра завернуть до упора в торец цилиндра и застопорить контргайкой 5.
4. Проверить свободу перемещения штока в цилиндре. Шток должен перемещаться равномерно, без заеданий, под небольшим усилием (не более 6 кгс).
5. При наличии установки проверить цилиндр на перетекание масла через поршневые кольца. Нормальная утечка масла не должна превышать 360 г в минуту.
Таблицы размеров
**Таблица 1. Размеры ротора, статора и лопастей по группам:**
Наименование детали | Номер группы | Длина детали, мм |
---|---|---|
Ротор | 1 | 22,000–21,996 |
2 | 21,996–21,992 | |
3 | 21,992–21,988 | |
Статор | 1 | 22,017–22,013 |
2 | 22,013–22,009 | |
3 | 22,009–22,005 | |
Лопасть | 1 | 21,998–21,992 |
2 | 21,992–21,988 | |
3 | 21,988–21,984 |
**Таблица 2. Диаметры отверстия крышки и шейки золотника по группам:**
Наименование детали | Номер группы | Диаметр, мм |
---|---|---|
Крышка | 1 | 20,015–20,010 |
2 | 20,010–20,005 | |
3 | 20,005–20,000 | |
Золотник | 1 | 19,992–19,987 |
2 | 19,987–19,982 | |
3 | 19,982–19,977 |
**Таблица 3. Диаметры отверстия и шейки золотника и корпуса клапана по группам:**
Наименование размера | Номер группы | Диаметр, мм |
---|---|---|
Отверстие в корпусе | 1 | 27,012–27,008 |
2 | 27,008–27,004 | |
3 | 27,004–27,000 | |
Большие шейки золотника | 1 | 27,003–26,999 |
2 | 26,999–26,995 | |
3 | 26,995–26,991 |