Ремонт та огляд насоса гідропідсилювача, клапана керування та силового циліндра
Для проведення ремонту або огляду стану деталей необхідно розібрати насос гідропідсилювача, клапан керування та силовий циліндр.
Розбирання та перевірка насоса гідропідсилювача
Перед розбиранням насос (рис. 1) необхідно зняти з автомобіля, злити масло, очистити та промити зовнішню поверхню насоса.
- Мал. 1. Насос гідропідсилювача:
1. Шків.
2. Фільтр.
3. Сапун.
4. Кришка бачка.
5. Бачок.
6. Колектор.
7. Запобіжний клапан.
8. Перепускний клапан.
9. Кришка насоса.
10. Розподільний диск.
11. Статор.
12. Ротор.
13. Вал.
14. Корпус насоса.
Порядок розбирання та перевірки насоса:
- 1. Зняти кришку бачка та фільтри.
2. Зняти бачок 5.
3. Встановити насос так, щоб його вал був розташований вертикально, а шків знаходився внизу і зняти кришку 9 насоса. При знятті кришки утримувати клапан перепуску 8 від випадання.
4. Відзначити положення розподільчого диска щодо статора 11 і зняти його зі штифтів.
5. Відзначити положення статора 11 щодо корпусу 14 насоса і зняти статор (стрілка на статорі вказує напрямок обертання вала насоса).
6. Зняти ротор 12 разом із лопатями. Статор, ротор та лопаті насоса підібрані на заводі індивідуально, тому їхню комплектність при розбиранні порушувати не можна.
7. Зняти шків 1 (при необхідності), стопорне кільце і вал 13 насоса разом із переднім підшипником.
8. Перевірити вільне переміщення перепускного клапана у кришці насоса та відсутність вибоїн чи зносу. Клапан та кришка насоса підібрані на заводі індивідуально, тому їхню комплектність при розбиранні порушувати не можна.
9. Перевірити затягування сідла запобіжного клапана 7 і у разі потреби підтягнути його.
10. Перевірити канали деталей насоса та очистити їх.
11. Перевірити, чи немає задирок або зносу на торцевих поверхнях ротора, корпусу та розподільчого диска. У разі незначних задирів або зношування притерти ці поверхні на плиті, після чого деталі ретельно промити.
12. Перевірити, чи вільно переміщуються в пазах лопаті 4 і чи не зношені вони.
13. Оглянути гумові ущільнювачі. Затверділі, з тріщинами та іншими дефектами замінити ущільнювачі.
Технічно справний стан насоса визначається двома показниками:
- Максимальним тиском, який створює насос.
- Шумністю при роботі.
**Примітка:**
Зношування окремих деталей, крім явних задирів, не може бути підставою для їх заміни. Ротор, статор та лопаті при складанні на заводі сортують на три групи за довжиною. У насос встановлюють деталі лише однієї групи. При ремонті насоса ротор, статор та лопаті замінюють також комплектно.
**Розміри для сортування ротора, статора та лопатей наведені в табл. 1.**
**Золотник перепускного клапана та кришку насоса також підбирають комплектно, сортуючи на три групи за діаметрами отвору та шийки. Розміри для сортування наведено у табл. 2.**
**При підвищеній шумності роботи насоса:**
Замінити кульковий підшипник валика насоса.
**Примітка:**
Насос уніфікований з насосом автомобіля ЗІЛ-130, крім шківа та пружини перепускного клапана.
Складання насоса гідропідсилювача
- 1. Перед складання всі деталі ретельно промити і просушити. Не слід протирати деталі кінцями та ганчірками, що залишають на деталях нитки, ворсинки тощо.
2. Встановити статор, ротор з лопатями та розподільний диск відповідно до міток, нанесених при розбиранні, та стрілкою, що вказує напрямок обертання. Фаска шліцевого отвору має бути звернена до корпусу насоса.
3. Встановити кришку із перепускним клапаном. Шестигранник сідла має бути звернений всередину отвору.
4. Поступово затягнути болти кріплення кришки. Момент затягування болтів: 2,1–2,8 кгс·м.
5. Момент затягування болтів, що кріплять бачок: 0,8–1 кгс·м.
6. Момент затягування гайки, що кріпить шків насоса: 5–6,5 кгс·м.
7. Вал насоса повинен обертатися вільно, без заїдання.
Розбирання клапана керування
- 1. Злити масло із системи гідропідсилювача керма.
2. Від'єднати трубки та шланги від клапана керування.
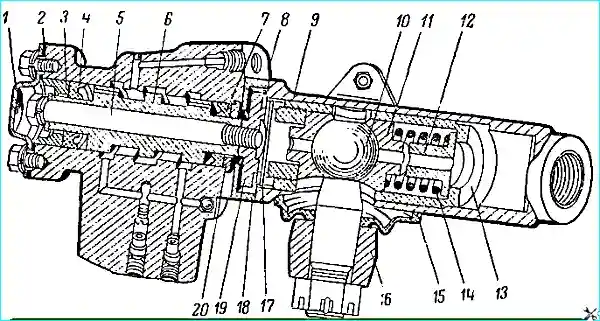
Мал. 2. Клапан керування гідропідсилювача рульового керування:
- 1. Кришка.
2. Прокладка.
3. Кришка золотаіка.
4. Манжета.
5. Болт кріплення золотника.
6. Золотник.
7. Манжета.
8. Корпус клапана управління.
9. Наконечник поздовжньої тяги.
10. Кульовий палець.
11. Сухар кульового пальця.
12. Обмежувач.
13. Склянка.
14. Пружина.
15. Ущільнювач пальця.
16. Рульова сошка.
17. Штифт.
18. Перехідник.
19. Гайка.
20. Кришка.
- **Порядок розбирання:**
1. Зняти кришку 1 клапана управління.
2. Вивернути центральний болт 5.
3. Відвернути болти кріплення корпусу клапана управління до поздовжньої тяги та зняти клапан управління.
4. Відвернути гвинт кріплення перехідника та зняти перехідник 18.
5. Вийняти кришки та манжети з обох боків клапана.
6. Вийняти золотник 6 клапана управління.
7. Якщо бронзові сідла сильно обім'яті та деформовані, випресувати їх та запресувати нові. - **Визначення технічного стану деталей клапана:**
- На робочих шийках золотника не повинно бути вибоїн, задирок або глибоких рисок. При необхідності зачистити оздоблювальним бруском, не завалюючи гострих кромок.
- Золотник повинен вільно, без заїдань переміщатися в корпусі клапана. Прочистити два отвори в шийках золотника.
- Ущільнювальні манжети 4 і 7 повинні зберігати еластичність, не мати тріщин, вихоплень та інших дефектів.
- Ретельно промити внутрішні порожнини та канали корпусу клапана.
**Примітка:**
Золотник і корпус клапана сортують на три групи за діаметром шийок та отвори. Розміри деталей за групами наведено у табл. 3.
Складання клапана управління
- 1. Встановити на поздовжню тягу перехідник 18 та затягнути гвинт його кріплення. Слідкувати, щоб на сполучених торцях не було вибоїн та забруднень.
2. Зібрати в корпусі клапана золотник 6, манжети 4 та 7 та кришки 3 та 20.
3. Золотник та манжети перед встановленням змастити турбінною або веретеною олією.
4. Вставляти золотник у корпус без перекосів, не прикладаючи силу.
5. Збирати корпус клапана та золотник по сполученому діаметру тільки однієї групи.
6. Переконатися, що крайня шийка золотника більшого діаметра звернена до поздовжньої тяги.
7. Болти кріплення корпусу клапана остаточно затягувати після затягування центрального болта 5.
8. Перевірити свободу переміщення золотника в корпусі.
9. Встановити кришку 1, замінивши пробкову прокладку 2.
10. Якщо шланги не відразу приєднують до клапана, заглушіть місця їх приєднання заглушками.
Розбір силового циліндра
Перед розбиранням силового циліндра рекомендується перевірити свободу переміщення штока з поршнем з одного крайнього положення в інше.
- Мал. 3. Силовий циліндр гідропідсилювача рульового управління:
1. Циліндр.
2. Шток з поршнем.
3. Штуцер.
4. Болт штуцера.
5. Контргайка кріплення головки.
6. Гайка кріплення головки.
7. Головка циліндра.
8. Пружина манжети.
9. Чашка пружини.
10. Манжета.
11. Кришка.
12. Регулювальні шайби.
13. Стопорне кільце.
14. Повстяний сальник.
15. Кільця ущільнювачів. - **Порядок розбирання:**
1. Відпустити контргайку 5.
2. Відвернути гайку 6 кріплення головки 7 циліндра.
3. Вийняти з циліндра головку 7 разом із штоком 2.
4. Вийняти шток із головки.
5. У разі зношування шарового шарніра розібрати шарнір і замінити зношені деталі. - **Визначення технічного стану деталей циліндра:**
- На внутрішній поверхні циліндра не повинно бути задир.
- Поршневі кільця повинні прилягати по всьому колу циліндра або до циліндричного калібру діаметром 50 мм. ки.
- В отворі під шток в головці 7 циліндра не повинно бути надір.
- Латунні шайби 12 не повинні бути деформовані.
- Гумова манжета 10 повинна бути еластичною і не мати пошкоджень.
- Повстяний сальник 14 повинен обтискати. Якщо сальник забруднений або не обтискає шток, його потрібно замінити.
- Гумові кільця ущільнювачів на головці циліндра повинні зберігати еластичність.
Складання силового циліндра
- 1. Шток з поршнем і внутрішню поверхню циліндра при складанні змастити турбінною або веретеною олією.
2. Поршневі кільця на поршні встановити замками в різні боки.
3. Гайку 6 кріплення головки циліндра загорнути до упору в торець циліндра і зупинити контргайкою 5.
4. Перевірити свободу переміщення штока у циліндрі. Шток повинен переміщатися рівномірно, без заїдань, під невеликим зусиллям (не більше 6 кгс).
5. За наявності установки перевірити циліндр на перетікання олії через поршневі кільця. Нормальний витік олії не повинен перевищувати 360 г на хвилину.
Таблиці розмірів
**Таблиця 1. Розміри ротора, статора та лопатей за групами:**
Найменування деталі | Номер групи | Довжина деталі, мм |
---|---|---|
Ротор | 1 | 22,000–21,996 |
2 | 21,996–21,992 | |
3 | 21,992–21,988 | |
Статор | 1 | 22,017–22,013 |
2 | 22,013–22,009 | |
3 | 22,009–22,005 | |
Лопатість | 1 | 21,998–21,992 |
2 | 21,992–21,988 | |
3 | 21,988–21,984 |
**Таблиця 2. Діаметри отвору кришки та шийки золотника за групами:**
Найменування деталі | Номер групи | Діаметр, мм |
---|---|---|
Кришка | 1 | 20,015–20,010 |
2 | 20,010–20,005 | |
3 | 20,005–20,000 | |
Золотник | 1 | 19,992–19,987 |
2 | 19,987–19,982 | |
3 | 19,982–19,977 |
**Таблиця 3. Діаметри отвору та шийки золотника та корпусу клапана за групами:**
Найменування розміру | Номер групи | Діаметр, мм |
---|---|---|
Отвор у корпусі | 1 | 27,012–27,008 |
2 | 27,008–27,004 | |
3 | 27,004–27,000 | |
Великі шийки золотника | 1 | 27,003–26,999 |
2 | 26,999–26,995 | |
3 | 26,995–26,991 |