Reparatur und Inspektion der Servopumpe, des Steuerventils und des Servozylinders
Um Reparaturen durchzuführen oder den Zustand von Teilen zu überprüfen, ist es notwendig, die Servopumpe, das Steuerventil und den Antriebszylinder zu zerlegen.
Servolenkungspumpe zerlegen und prüfen
Vor der Demontage muss die Pumpe (Abb. 1) aus dem Fahrzeug ausgebaut, das Öl abgelassen und die Außenfläche der Pumpe gereinigt und gewaschen werden.
- Abb. 1. Servopumpe:
1. Rolle.
2. Filter.
3. Sapun.
4. Tankdeckel.
5. Panzer.
6. Sammler.
7. Sicherheitsventil.
8. Bypassventil.
9. Pumpendeckel.
10. Verteilungsdiskette.
11. Stator.
12. Rotor.
13. Wert
14. Pumpenkörper.
Vorgehensweise zur Demontage und Überprüfung der Pumpe:
- 1. Entfernen Sie den Tankdeckel und die Filter.
2. Tank 5 ausbauen.
3. Installieren Sie die Pumpe so, dass ihre Welle vertikal steht und die Riemenscheibe unten ist, und entfernen Sie die Pumpenabdeckung 9. Halten Sie beim Abnehmen der Abdeckung das Bypassventil 8 fest, damit es nicht herausfällt.
4. Die Lage der Verteilerscheibe zum Stator 11 markieren und von den Bolzen lösen.
5. Markieren Sie die Position des Stators 11 im Verhältnis zum Pumpengehäuse 14 und entfernen Sie den Stator (der Pfeil auf dem Stator zeigt die Drehrichtung der Pumpenwelle an).
6. Den Rotor 12 samt Rotorblättern herausnehmen. Stator, Rotor und Schaufelblätter der Pumpe werden im Werk einzeln ausgewählt, so dass deren Vollständigkeit bei einer Demontage nicht beeinträchtigt werden kann.
7. Riemenscheibe 1 (falls erforderlich), Sicherungsring und Welle 13 der Pumpe zusammen mit dem vorderen Lager entfernen.
8. Überprüfen Sie das Bypassventil im Pumpendeckel auf freie Beweglichkeit und auf Kerben oder Verschleiß. Ventil und Pumpendeckel werden im Werk individuell ausgewählt, daher darf deren Vollständigkeit bei der Demontage nicht beeinträchtigt werden.
9. Den Sitz des Sicherheitsventils 7 auf Dichtheit prüfen und ggf. nachziehen.
10. Kanäle der Pumpenteile prüfen und reinigen.
11. Überprüfen Sie die Endflächen von Rotor, Gehäuse und Verteilerscheibe auf Riefen oder Verschleiß. Bei leichten Kratzern oder Abnutzungserscheinungen reiben Sie diese Flächen an der Platte und waschen Sie die Teile anschließend gründlich ab.
12. Prüfen Sie, ob sich die Messer 4 in den Nuten frei bewegen und ob diese abgenutzt sind.
13. Überprüfen Sie die Gummidichtungen. Ersetzen Sie verhärtete Dichtungen mit Rissen und anderen Defekten.
Der technisch einwandfreie Zustand der Pumpe wird durch zwei Indikatoren bestimmt:
- Der maximale Druck, den die Pumpe erzeugt.
- Geräusche während des Betriebs.
**Hinweis:**
Der Verschleiß einzelner Teile, mit Ausnahme von deutlich erkennbaren Riefen, ist kein Grund für deren Austausch. Rotor, Stator und Rotorblätter werden bei der Montage im Werk nach Länge in drei Gruppen sortiert. In der Pumpe sind nur Teile einer Gruppe verbaut. Bei einer Pumpenreparatur werden Rotor, Stator und Schaufelblätter ebenfalls im Set ausgetauscht.
**Maße zur Sortierung von Rotor, Stator und Schaufelblättern sind in der Tabelle angegeben. 1.**
**Die Bypassventilspule und die Pumpenabdeckung werden ebenfalls als Satz ausgewählt und nach den Durchmessern von Loch und Hals in drei Gruppen sortiert. Die Größenangaben zur Sortierung sind der Tabelle zu entnehmen. 2.**
**Wenn die Pumpe laut ist:**
Ersetzen Sie das Kugellager der Pumpenwelle.
**Hinweis:**
Die Pumpe ist mit Ausnahme der Riemenscheibe und der Feder des Bypassventils mit der Pumpe des Fahrzeugs ZIL-130 vereinheitlicht.
Montage der Servopumpe
- 1. Vor dem Zusammenbau alle Teile gründlich waschen und trocknen. Wischen Sie die Teile nicht mit Enden und Lappen ab, die Fäden, Flusen usw. auf den Teilen hinterlassen.
2. Stator, Rotor mit Schaufeln und Verteilerscheibe entsprechend den bei der Demontage angebrachten Markierungen und dem Drehrichtungspfeil montieren. Die Fase der Keilwellenbohrung muss zum Pumpenkörper zeigen.
3. Montieren Sie die Abdeckung mit dem Bypassventil. Der Sechskant der Aufnahme muss dabei zur Bohrungsinnenseite zeigen.
4. Ziehen Sie die Befestigungsschrauben der Abdeckung gleichmäßig fest. Anzugsdrehmoment der Schrauben: 2,1–2,8 kgf m.
5. Anzugsdrehmoment der Tankbefestigungsschrauben: 0,8–1 kgf m.
6. Anzugsdrehmoment der Mutter zur Befestigung der Pumpenriemenscheibe: 5–6,5 kgf m.
7. Die Pumpenwelle muss sich frei drehen können, ohne zu blockieren.
Demontage des Steuerventils
- 1. Lassen Sie das Öl aus der Servolenkung ab.
2. Trennen Sie die Rohre und Schläuche vom Steuerventil.
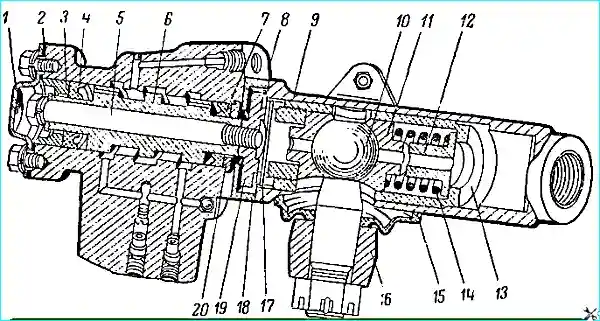
Abb. 2. Servolenkungssteuerventil:
- 1. Abdeckung.
2. Dichtung.
3. Golddeckel ica.
4. Manschette.
5. Ventilbefestigungsschraube.
6. Spule.
7. Manschette.
8. Steuerventilkörper.
9. Längszugspitze.
10. Kugelbolzen.
11. Kugelbolzenknacker.
12. Begrenzer.
13. Glas.
14. Frühling.
15. Fingerdichtung.
16. Achsschenkel.
17. Stecknadel.
18. Adapter.
19. Nuss.
20. Abdeckung.
- **Demontageverfahren:**
1. Deckel 1 vom Steuerventil abnehmen.
2. Zentralschraube 5 lösen.
3. Lösen Sie die Schrauben, mit denen das Steuerventilgehäuse an der Längsstange befestigt ist, und entfernen Sie das Steuerventil.
4. Befestigungsschraube des Adapters lösen und Adapter 18 abnehmen.
5. Entfernen Sie die Kappen und Dichtungen von beiden Seiten des Ventils.
6. Den Steuerschieber 6 vom Regelventil abmontieren.
7. Wenn die Bronzesitze stark verbeult und verformt sind, drücken Sie diese heraus und pressen Sie neue ein. - **Bestimmung des technischen Zustands der Ventilteile:**
- Die Laufzapfen des Ventils dürfen keine Kerben, Grate oder tiefe Kratzer aufweisen. Bei Bedarf mit einem Polierblock reinigen, ohne die scharfen Kanten zu beschädigen.
- Der Ventilschieber sollte sich frei im Ventilkörper bewegen lassen, ohne zu klemmen. Reinigen Sie die beiden Löcher in den Ventilhälsen.
- Die Dichtmanschetten 4 und 7 müssen elastisch bleiben und dürfen keine Risse, Abnutzungserscheinungen oder andere Mängel aufweisen.
- Die inneren Hohlräume und Kanäle des Ventilkörpers gründlich spülen.
**Hinweis:**
Ventilschieber und Ventilkörper sind nach dem Durchmesser der Hälse und der Bohrung in drei Gruppen sortiert. Die Abmessungen der Teile nach Gruppen sind in der Tabelle angegeben. 3.
Zusammenbau des Steuerventils
- 1. Montieren Sie den Adapter 18 an der Längsstange und ziehen Sie dessen Befestigungsschraube fest. Stellen Sie sicher, dass sich an den Steckenden keine Kerben oder Schmutz befinden.
2. Ventil 6, Dichtungen 4 und 7 sowie Abdeckungen 3 und 20 im Ventilkörper montieren.
3. Schmieren Sie den Ventileinsatz und die Dichtungen vor dem Einbau mit Turbinen- oder Spindelöl.
4. Den Ventileinsatz ohne Verformung und ohne Gewaltanwendung in das Gehäuse einführen.
5. Montieren Sie Ventilkörper und Spule entsprechend dem Passdurchmesser nur einer Gruppe.
6. Achten Sie darauf, dass der äußere Hals des Ventils mit dem größeren Durchmesser zur Längsstange zeigt.
7. Das endgültige Anziehen der Ventilkörper-Befestigungsschrauben sollte erst nach dem Anziehen der Zentralschraube 5 erfolgen.
8. Prüfen Sie die Leichtgängigkeit des Ventils im Gehäuse.
9. Deckel 1 montieren, Korkdichtung 2 ersetzen.
10. Wenn die Schläuche nicht unmittelbar mit dem Ventil verbunden sind, verschließen Sie die Anschlussstellen mit Stopfen.
Demontage des Arbeitszylinders
Bevor Sie den Arbeitszylinder zerlegen, empfiehlt es sich, die Bewegungsfreiheit der Stange mit dem Kolben von einer Extremposition in die andere zu prüfen.
- Abb. 3. Servolenkungszylinder:
1. Zylinder.
2. Stange mit Kolben.
3. Brustwarze.
4. Passschraube.
5. Kontermutter zur Kopfbefestigung.
6. Kopfbefestigungsmutter.
7. Zylinderkopf.
8. Manschettenfeder.
9. Federbecher.
10. Manschette.
11. Abdeckung.
12. Passscheiben.
13. Sicherungsring.
14. Filzdrüse.
15. Dichtringe. - **Demontageverfahren:**
1. Kontermutter 5 lösen.
2. Mutter 6 zur Befestigung des Zylinderkopfes 7 lösen.
3. Kopf 7 zusammen mit Stange 2 vom Zylinder entfernen.
4. Entfernen Sie die Stange vom Kopf.
5. Wenn das Kugelgelenk verschlissen ist, zerlegen Sie das Gelenk und ersetzen Sie die verschlissenen Teile. - **Bestimmung des technischen Zustandes der Zylinderteile:**
- Die Innenfläche des Zylinders darf keine Riefen aufweisen.
- Die Kolbenringe müssen um den gesamten Umfang des Zylinders bzw. in eine zylindrische Bohrung mit einem Durchmesser von 50 mm passen.
- Die Kolbenringe müssen sich frei in den Kolbennuten drehen können.
- Die Chromoberfläche der Stange darf keinen Verschleiß aufweisen.
- Die Bohrung für die Stange im Zylinderkopf 7 darf keine Riefen aufweisen.
- Die Messingscheiben 12 dürfen nicht verformt sein.
- Die Gummimanschette 10 darf elastisch und unbeschädigt sein.
- Die Filzdichtung 14 muss die Stange zusammendrücken. Wenn die Dichtung verschmutzt ist oder die Kolbenstange nicht mehr zusammendrückt, muss sie ausgetauscht werden.
- Die Gummidichtringe am Zylinderkopf müssen elastisch bleiben.
Zusammenbau des Arbeitszylinders
- 1. Schmieren Sie bei der Montage die Kolbenstange und die Innenfläche des Zylinders mit Turbinen- oder Spindelöl.
2. Montieren Sie die Kolbenringe mit den Sperrklinken in unterschiedliche Richtungen auf dem Kolben.
3. Mutter 6 zur Zylinderkopfbefestigung bis zum Anschlag auf die Zylinderstirn aufschrauben und mit Kontermutter 5 fixieren.
4. Überprüfen Sie die Bewegungsfreiheit der Stange im Zylinder. Die Stange muss sich bewegen gleichmäßig, ohne zu verklemmen, mit leichter Kraft (nicht mehr als 6 kgf).
5. Wenn die Installation verfügbar ist, überprüfen Sie den Zylinder auf Öllecks durch die Kolbenringe. Der normale Ölverlust sollte 360 g pro Minute nicht überschreiten.
**Tabelle 1. Abmessungen von Rotor, Stator und Schaufelblättern nach Gruppen:**
Teilename | Gruppennummer | Länge des Teils, mm |
---|---|---|
Ротор | 1 | 22,000–21,996 |
2 | 21,996–21,992 | |
3 | 21,992–21,988 | |
Stator | 1 | 22,017–22,013 |
2 | 22,013–22,009 | |
3 | 22,009–22,005 | |
Klinge | 1 | 21,998–21,992 |
2 | 21,992–21,988 | |
3 | 21,988–21,984 |
**Tabelle 2. Durchmesser der Deckel- und Halsöffnungen des Ventils nach Gruppen:**
Teilename | Gruppennummer | Durchmesser, mm |
---|---|---|
Deckel | 1 | 20,015–20,010 |
2 | 20,010–20,005 | |
3 | 20,005–20,000 | |
Das vergoldete Ventil | 1 | 19,992–19,987 |
2 | 19,987–19,982 | |
3 | 19,982–19,977 |
**Tabelle 3. Durchmesser der Öffnung und des Halses der Ventilspule und des Ventilkörpers nach Gruppen:**
Größenbezeichnung | Gruppennummer | Durchmesser, mm |
---|---|---|
Loch im Körper | 1 | 27,012–27,008 |
2 | 27,008–27,004 | |
3 | 27,004–27,000 | |
Große Ventilhälse | 1 | 27,003–26,999 |
2 | 26,999–26,995 | |
3 | 26,995–26,991 |