Reparación e inspección de la bomba de dirección asistida, la válvula de control y el cilindro de potencia
Para realizar reparaciones o inspeccionar el estado de las piezas, es necesario desmontar la bomba de dirección asistida, la válvula de control y el cilindro de potencia.
Desmontaje y comprobación de la bomba de dirección asistida
Antes de desmontar, se debe retirar la bomba (Fig. 1) del vehículo, drenar el aceite y limpiar y lavar la superficie exterior de la bomba.
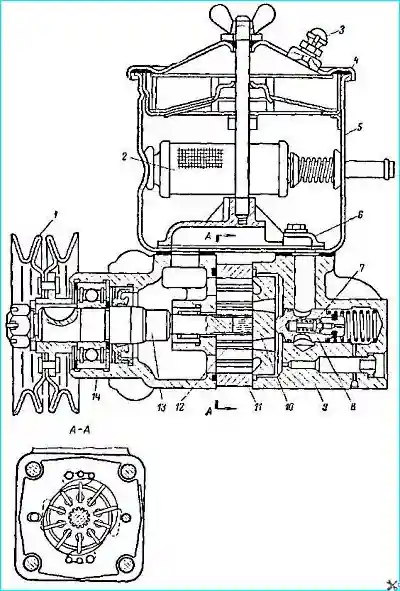
Figura. 1. Bomba de dirección asistida: 1. Polea. 2. Filtro. 3. 4. Tapa del tanque. 5. Tanque.6. Coleccionista. 7. Válvula de seguridad. 8. Válvula de derivación. 9. Tapa de la bomba. 10. Disco de distribución. 11. Estator. 12. Rotor. 13. Val. 14. Cuerpo de la bomba.
Procedimiento para desmontar y comprobar la bomba:
- 1. Retire la tapa del tanque y los filtros.
- 2. Retire el tanque 5.
- 3. Instale la bomba de manera que su eje quede en posición vertical y la polea en la parte inferior, y retire la tapa de la bomba 9. Al retirar la cubierta, sujete la válvula de derivación 8 para que no se caiga.
- 4. Marcar la posición del disco de distribución respecto al estator 11 y retirarlo de los pasadores.
- 5. Marque la posición del estator 11 con respecto a la carcasa de la bomba 14 y retire el estator (la flecha en el estator indica la dirección de rotación del eje de la bomba).
- 6. Retire el rotor 12 junto con las cuchillas. El estator, el rotor y las paletas de la bomba se seleccionan individualmente en la fábrica, por lo que su integridad no se puede violar durante el desmontaje.
- 7. 8. Retire la polea 1 (si es necesario), el anillo de retención y el eje 13 de la bomba junto con el cojinete delantero. Compruebe que la válvula de derivación en la tapa de la bomba se mueva libremente y que no presente muescas ni desgaste. La válvula y la tapa de la bomba se seleccionan individualmente en fábrica, por lo que no se debe violar su integridad durante el desmontaje.
- 9. 10. Compruebe la estanqueidad del asiento de la válvula de seguridad 7 y apriételo si es necesario. Revise los canales de las piezas de la bomba y límpielos.
- 11. Verifique si hay rayas o desgaste en las superficies de los extremos del rotor, la carcasa y el disco de distribución. En caso de pequeños rayones o desgaste, frote estas superficies sobre la placa y luego lave bien las piezas.
- 12. Compruebe si las cuchillas 4 se mueven libremente en las ranuras y si están desgastadas.
- 13. Inspeccione los sellos de goma. Reemplace los sellos endurecidos con grietas y otros defectos.
El estado técnico correcto de la bomba se determina mediante dos indicadores:
- La presión máxima que crea la bomba.
- El ruido durante el funcionamiento.
**Nota:**
El desgaste de piezas individuales, salvo rayaduras evidentes, no puede servir como motivo para su sustitución. Durante el montaje en fábrica, el rotor, el estator y las palas se clasifican en tres grupos según su longitud. En la bomba sólo se instalan partes de un grupo. Al reparar una bomba, también se sustituyen el rotor, el estator y las paletas como un conjunto.
**Las dimensiones para clasificar el rotor, el estator y las palas se dan en la tabla. 1.**
**El carrete de la válvula de derivación y la tapa de la bomba también se seleccionan como un conjunto, clasificados en tres grupos según los diámetros del orificio y el cuello. Los tamaños para la clasificación se dan en la tabla. 2.**
**Si la bomba hace ruido:**
Reemplace el cojinete de bolas del eje de la bomba.
**Nota:**
La bomba está unificada con la bomba del vehículo ZIL-130, a excepción de la polea y el resorte de la válvula de derivación.
Montaje de la bomba de dirección asistida
- 1. Antes del montaje, lave y seque bien todas las piezas. No limpie las piezas con cabos o trapos que dejen hilos, pelusas, etc. en las piezas.
- 2. Instalar el estator, rotor con álabes y disco de distribución de acuerdo con las marcas realizadas durante el desmontaje y la flecha que indica el sentido de giro. El chaflán del orificio estriado debe estar orientado hacia el cuerpo de la bomba.
- 3. Instale la tapa con la válvula de derivación. El hexágono del asiento debe mirar hacia el interior del orificio.
- 4. Apriete los pernos de montaje de la cubierta de manera uniforme. Par de apriete de los tornillos: 2,1–2,8 kgf m.
- 5. Par de apriete de los tornillos que fijan el depósito: 0,8–1 kgf m.
- 6. Par de apriete de la tuerca de fijación de la polea de la bomba: 5–6,5 kgf m.
- 7. El eje de la bomba debe girar libremente, sin atascarse.
Desmontaje de la válvula de control
- 1. Drene el aceite del sistema de dirección asistida.
- 2. Desconecte los tubos y mangueras de la válvula de control.
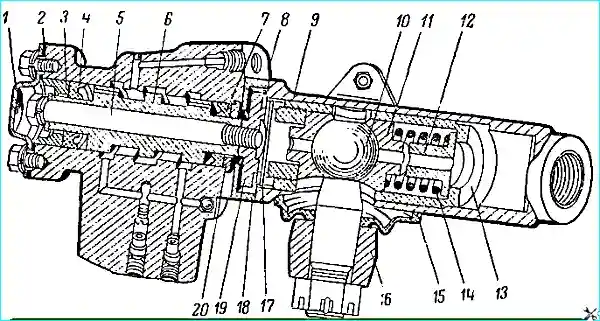
Figura. 2. Vбlvula de control de direcciуn asistida: 1. Portada. 2. Junta. 3. Tapa dorada ica.4. Puсo. 5. Perno de montaje de la vбlvula. 6. Carrete. 7. Puсo. 8. Cuerpo de la vбlvula de control. 9. Punta de tracciуn longitudinal. 10. Pasador de bola. 11. Cascanueces con forma de bola. 12. Limitador. 13. Vidrio.14. Primavera. 15. Sello de dedo. 16. Muсуn de direcciуn. 17. Alfiler. 18. Adaptador. 19. Tuerca. 20. Portada.
- **Procedimiento de desmontaje:**
1. Retire la tapa 1 de la válvula de control.
2. Desatornille el perno central 5.
3. Afloje los pernos que sujetan el cuerpo de la válvula de control a la varilla longitudinal y retire la válvula de control.
4. Afloje el tornillo de montaje del adaptador y retire el adaptador 18.
5. Retire las tapas y los sellos de ambos lados de la válvula.
6. Retire la válvula de carrete 6 de la válvula de control.
7. Si los asientos de bronce están muy abollados y deformados, presiónelos para sacarlos y coloque unos nuevos. - **Determinación del estado técnico de las piezas de la válvula:**
- No debe haber mellas, rebabas ni arañazos profundos en los muñones de trabajo de la válvula. Si es necesario, limpie con un bloque de acabado, sin dañar los bordes afilados.
- El carrete de la válvula debe moverse libremente en el cuerpo de la válvula sin atascarse. - Limpiar los dos orificios de los cuellos de las válvulas.
- Los manguitos de sellado 4 y 7 deben permanecer elásticos y no presentar grietas, enganches u otros defectos.
- Enjuagar a fondo las cavidades y canales internos del cuerpo de la válvula.
**Nota:**
El carrete y el cuerpo de la válvula se clasifican en tres grupos según el diámetro de los cuellos y el orificio. Las dimensiones de las piezas por grupos se dan en la tabla. 3.
Montaje de la válvula de control
- 1. Instalar el adaptador 18 en la barra longitudinal y apretar su tornillo de fijación. Asegúrese de que no haya muescas ni suciedad en los extremos de acoplamiento.
- 2. Ensamble la válvula 6, los sellos 4 y 7 y las tapas 3 y 20 en el cuerpo de la válvula.
- 3. Antes de la instalación, lubrique el núcleo de la válvula y los sellos con aceite para turbinas o husillos.
- 4. Inserte el núcleo de la válvula en la carcasa sin distorsionarlo y sin aplicar fuerza.
- 5. Ensamble el cuerpo de la válvula y el carrete de acuerdo con el diámetro de acoplamiento de un solo grupo.
- 6. Asegúrese de que el cuello exterior de la válvula de mayor diámetro esté orientado hacia la varilla longitudinal.
- 7. Los pernos de montaje del cuerpo de la válvula deben apretarse finalmente después de apretar el perno central 5.
- 8. Compruebe la libertad de movimiento de la válvula en la carcasa.
- 9. Instale la tapa 1, reemplazando la junta de corcho 2.
- 10. Si las mangueras no están conectadas inmediatamente a la válvula, tape los puntos de conexión con tapones.
Desmontaje del cilindro de potencia
Antes de desmontar el cilindro de potencia, se recomienda comprobar la libertad de movimiento del vástago con el pistón desde una posición extrema a otra.
Figura. 3. Cilindro de direcciуn asistida: 1. Cilindro. 2. Biela con pistуn. 3. Pezуn. 4. Perno de montaje. 5. Tuerca de seguridad para fijaciуn de la cabeza. 6. Tuerca de fijaciуn de la cabeza. 7. Culata. 8. Resorte del manguito. 9. Copa de resorte. 10. Puсo. 11. Portada. 12. Ajuste de arandelas. 13. Anillo de retenciуn. 14. Glбndula de fieltro. 15. Anillos de sellado.
- **Procedimiento de desmontaje:**
1. Afloje la contratuerca 5.
2. Desatornille la tuerca 6 que fija la culata 7.
3. Retire la cabeza 7 del cilindro junto con la varilla 2.
4. Retire la varilla de la cabeza.
5. Si la rótula está desgastada, desmóntela y reemplace las piezas desgastadas. - **Determinación del estado técnico de las piezas del cilindro:**
- No debe haber ninguna rayadura en la superficie interior del cilindro.
- Los anillos del pistón deben ajustarse alrededor de toda la circunferencia del cilindro o en un orificio cilíndrico con un diámetro de 50 mm.
- Los anillos del pistón deben girar libremente en las ranuras del pistón.
- No debe haber desgaste en la superficie cromada de la varilla.
- No debe haber ninguna rayadura en el orificio para la varilla en la cabeza 7 del cilindro.
- Las arandelas de latón 12 no deben estar deformadas.
- El manguito de goma 10 debe ser elástico y no tener ningún daño.
- La junta de fieltro 14 debe comprimir la varilla. Si la junta está sucia o no comprime el vástago del pistón, debe sustituirse.
- Los anillos de sellado de goma de la culata deben permanecer elásticos.
Montaje del cilindro de potencia
- 1. Durante el montaje, lubrique el vástago del pistón y la superficie interior del cilindro con aceite para turbinas o husillos.
- 2. Instale los anillos del pistón en el pistón con las cerraduras orientadas en diferentes direcciones.
- 3. Atornillar la tuerca 6 para fijar la culata hasta que haga tope contra el extremo del cilindro y asegurar con la contratuerca 5.
- 4. Verifique la libertad de movimiento de la varilla en el cilindro. La varilla debe moverse uniformemente, sin atascarse, bajo una ligera fuerza (no más de 6 kgf).
- 5. Si la instalación está disponible, verifique que el cilindro no tenga fugas de aceite a través de los anillos del pistón. La fuga normal de aceite no debe superar los 360 g por minuto.
Tablas de tallas
**Tabla 1. Dimensiones de rotor, estator y álabes por grupos:**
Nombre de la pieza | Número de grupo | Longitud de la pieza, mm |
---|---|---|
Rotor | 1 | 22,000–21,996 |
2 | 21,996–21,992 | |
3 | 21,992–21,988 | |
Estator | 1 | 22,017–22,013 |
2 | 22,013–22,009 | |
3 | 22,009–22,005 | |
Cuchilla | 1 | 21,998–21,992 |
2 | 21,992–21,988 | |
3 | 21,988–21,984 |
**Tabla 2. Diámetros de las aberturas de tapa y cuello de la válvula por grupos:**
Nombre de la pieza | Número de grupo | Diámetro, mm |
---|---|---|
Tapa | 1 | 20,015–20,010 |
2 | 20,010–20,005 | |
3 | 20,005–20,000 | |
La válvula bañada en oro | 1 | 19,992–19,987 |
2 | 19,987–19,982 | |
3 | 19,982–19,977 |
**Tabla 3. Diámetros del orificio y del cuello del carrete y del cuerpo de la válvula por grupos:**
Nombre del tamaño | Número de grupo | Diámetro, mm |
---|---|---|
Agujero en el cuerpo | 1 | 27,012–27,008 |
2 | 27,008–27,004 | |
3 | 27,004–27,000 | |
Cuellos de válvula grandes | 1 | 27,003–26,999 |
2 | 26,999–26,995 | |
3 | 26,995–26,991 |