The gearbox is mechanical, with manual shifting, has five forward gears and one reverse gear, all forward gears are synchronized
The body parts of the gearbox - the clutch housing, the gearbox housing itself and the rear cover - are cast from aluminum alloy and pulled together with studs and nuts.
The joints are sealed with cardboard gaskets (sealant can be used during repairs). The gearbox housing surface is finned for improved heat dissipation.
The bottom of the housing is covered with a stamped steel cover with a gasket (fastened with studs).
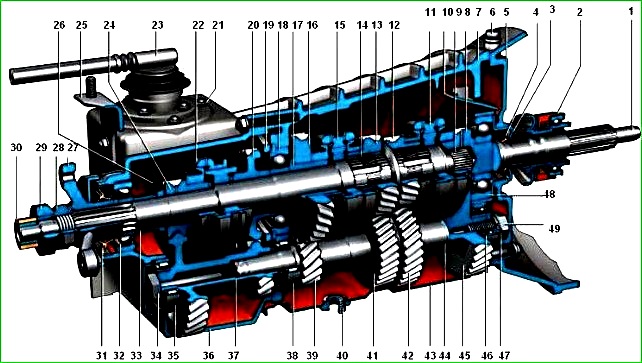
BA3-2123 gearbox: 1 - primary shaft; 2 - clutch release sleeve; 3 - front cover with guide sleeve; 4 - primary shaft oil seal; 5 - clutch housing; 6 - breather; 7 - gearbox housing; 8 - primary shaft constant mesh gear; 9 - secondary shaft needle bearing; 10 - oil collection and drain tray; 11 - synchronizer of 3rd and 4th gears; 12 - 3rd gear pinion; 13 - 2nd gear pinion; 14 - secondary shaft; 15 - synchronizer of 1st and 2nd gears; 16 - 1st gear pinion; 17 - 1st gear pinion sleeve; 18 - secondary shaft intermediate bearing; 19 - intermediate bearing lock plate; 20 - reverse gear; 21 - gear selection mechanism fastening nut; 22 - 5th gear synchronizer; 23 - gear selection mechanism; 24 - 5th gear pinion; 25 - support plate fastening bracket; 26 - oil deflector washer; 27 - flange of elastic coupling of cardan transmission; 28 - nut; 29 - centering ring seal; 30 - centering ring; 31 - secondary shaft oil seal; 32 - secondary shaft rear bearing; 33 - spacer sleeve; 34 - gear block bolt; 35 - gear block bearing; 36 - gearbox rear cover; 37 - 5th and reverse gear block; 38 - intermediate shaft rear bearing; 39 - intermediate shaft 1st gear pinion; 40 - drain plug; 41 - intermediate shaft 2nd gear pinion; 42 - intermediate shaft 3rd gear pinion; 43 - gearbox lower cover; 44 - intermediate shaft; 45 - intermediate shaft constant mesh gear; 46 - intermediate shaft front bearing; 47 - intermediate shaft bearing clamp washer; 48 - clamp washer bolt; 49 - rear bearing of the primary shaft
The clutch housing is bolted to the engine block.
To ensure the alignment of the crankshaft and the primary shaft of the gearbox, the housing is centered on two bushings (grooves are made for them in the mounting holes of the block and housing).
The third support of the power unit is installed on the rear cover of the gearbox. It is attached to the crossmember, and the latter is attached to the floor of the body (on welded bolts).
On the left side of the gearbox housing there is a filler (inspection) hole, in its lower cover there is a drain hole.
The holes are closed with plugs with conical threads. There is a magnet in the drain plug.
It traps steel particles that get into the oil when parts wear out. A breather is screwed into the upper part of the clutch housing.
It prevents pressure buildup in the gearbox when it heats up.
If the breather is faulty (the cap is jammed), a strong oil leak through the seals is possible. There are three shafts in the gearbox: primary, secondary and intermediate.
The primary shaft rests on two ball bearings - in the rear end of the crankshaft and in the front wall of the gearbox housing (the latter takes up the bulk of the load).
A needle bearing is installed in the rear end of the primary shaft, which is the front support of the secondary shaft and ensures the alignment of the shafts.
The secondary shaft also rests on a ball bearing in the rear wall of the gearbox housing and a roller bearing in its rear cover.
The intermediate shaft rotates in two bearings: the front one is a double-row ball bearing, located in the front wall of the gearbox housing, and the rear one is a roller bearing, located in its rear wall.
Through the reverse gear block and 5th gear, the intermediate shaft also rests on a roller bearing in the rear cover. gearbox.
The axle of the intermediate reverse gear is also fixed to the rear wall of the gearbox housing.
The primary shaft has two toothed rims.
The helical toothed rim, located closer to the front wall of the housing, is in constant engagement with the front gear of the intermediate shaft (thus, these shafts always rotate together).
The spur toothed rim of the primary shaft is the rim of the synchronizer of the fourth gear (when it is engaged, the torque is transmitted directly from the primary shaft to the secondary shaft, bypassing the intermediate shaft, which is why this gear is often called "direct »).
The intermediate shaft is a block of four helical gears.
When any gear except IV is engaged, torque is transmitted to the secondary shaft through the intermediate shaft.
The gears of the intermediate shaft are arranged in the following order (from its front end): a gear of constant engagement with the primary shaft, gears of III, II, I gears.
A block of two gears is attached to the rear end of the shaft with a bolt: reverse (spur) and V gear (helical).
It additionally rests on a roller bearing in the rear cover of the gearbox.
The secondary shaft contains driven gears of III, II, I gears, reverse and V gear (in order, counting from the front end of the shaft) and synchronizers.
The driven gears of the forward gears are in constant engagement with the corresponding gears of the intermediate shaft.
The gears of the III and II gears rotate on the hardened journals of the secondary shaft, the gears of the I and V gears - on the bushings.
The driven gear of the reverse gear is rigidly fixed to the shaft with a key.
The rims of their synchronizers are made together with the helical gears of the forward gears - spur gears of a smaller diameter.
They are directed towards the corresponding synchronizer (III, I, V - forward, II - backward).
At the rear end of the secondary shaft, a flange of the elastic coupling is secured with a nut.
Previously, the nut was fixed from unscrewing with a lock washer placed under it - its edges were bent to the edge of the nut. Now an anaerobic sealant is applied to the threads, and the washer is not installed.
The synchronizer consists of a hub rigidly fixed to the secondary shaft, a sliding clutch, a retaining ring, a blocking ring and a spring with a washer.
The hubs of the synchronizers of III-IV and I-II gears enter the grooves on the secondary shaft with their internal projections, and the hub of the synchronizer of the V gear is held by the same key as the driven reverse gear.
On the outer surface of the hubs there are splines along which the sliding clutches move. The couplings have recesses into which the forks of the gearshift rods enter.
The blocking rings are connected with their inner rims to the rims of the synchronizers of the corresponding gears and are pressed by springs towards the sliding couplings.
The springs rest on the side surface of the driven gears through washers. The reverse gear does not have a synchronizer.
To engage it, you need to engage the intermediate gear with the driven gear of the secondary shaft and with the reverse driving gear in the rear gear block on the intermediate shaft.
The gearbox control drive consists of three rods connected to forks.
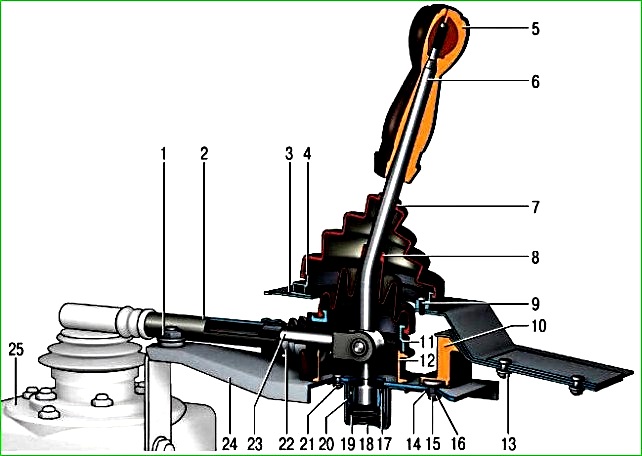
The forward gear engagement forks fit into the grooves of the synchronizer sliding clutches, and the reverse gear engagement fork fits into the groove on the intermediate gear.
The gear selection mechanism consists of a guide plate with eight rectangular cutouts in the center, upper and lower washers, a gearshift lever and its housing, and a reverse gear locking bracket.
These parts are pulled together by three bolts that secure the gear selection mechanism to the rear cover of the gearbox.
The "neutral" position of the lever between III and IV gears is set by two pairs of spring-loaded guide strips installed in the grooves of the guide plate and acting on the lower end of the lever.
Accidental engagement of reverse instead of V gear is impossible due to the bent petal of the locking bracket, which rests on the protrusion on the lever.
To engage reverse gear, you need to press the lever down - while its protrusion falls below the petal of the bracket.
The gearbox parts are lubricated by splashing.
The primary and secondary shafts are sealed with oil seals, and on the secondary shaft behind the driven gear of the 5th gear there is an oil deflector washer.
The gearbox is filled with transmission oil with a viscosity of 75W80 to 85W90 and a quality class of at least GL-4.
Its level should be at the lower edge of the filler hole (first make sure that the car is horizontal).
Gearbox malfunction diagnostics
Reason for malfunction
Remedy
Noise in the gearbox. The noise decreases or disappears when the clutch is depressed
The transfer case is in neutral
- Low oil level in the gearbox housing
Check the level, add oil if necessary.
Check for leaks.
Clean the breather
- Wear or damage to bearings, gear teeth
Replace worn bearings, gears
- Gearbox shafts are shifted in the axial direction
Tighten the nuts, replace broken fixing parts
Gears are difficult to engage, no extraneous noise
- Too thick oil in the gearbox
Use oil in accordance with climatic conditions
- Wear or deformation of the gear shift lever
Straighten or replace the lever
Jamming of the spherical joint of the gear shift lever
Replace the deformed parts, put LSC-15, Litol-24 or SHRUS-4 grease into the joint
- The fork rods move with difficulty (jammed locking crackers, burrs on the rods, dirt in the sockets)
Clean the parts, replace worn and deformed ones
- The sliding sleeve on the hub splines moves with difficulty
Clean the splines from dirt, file off burrs with a needle file, replace parts with crushed splines
- The gear shift forks are deformed
Replace the forks
Gears spontaneously disengage
- The locking springs have lost their elasticity, the balls and/or rod seats are worn out
Replace worn parts
- Damage or wear of the synchronizer locking rings
Replace the rings
- Damage or wear of the clutch teeth or synchronizer ring gear
Replace the clutch or gear
- The synchronizer spring is broken
Replace the spring
Noise, crackling, squealing of gears when engaging a gear
Not enough oil in the gearbox housing
Add oil.
Check for leaks.
Clean or replace breather
- Wear or breakage of gear teeth and/or synchronizers
Replace parts
- Wear or deformation of the synchronizer ring of the gear being engaged
Replace the ring
- Axial play of the gearbox shafts
Tighten the bearing mounts, replace worn bearings
Oil leak
- Wear of oil seals
Replace the oil seals.
If necessary, clean or replace the gearbox breather
- Heavy wear, nicks on the surfaces of the shafts on which the oil seals operate
Sand minor damage with fine-grained sandpaper and polish.
When installing a new oil seal, you can slightly under-press it, not allowing skew (if necessary, place spacers up to 1 mm thick under it) so that the edge of the seal works on the unworn part of the shaft.
In case of significant damage - replace the shafts and seals
- Increased pressure in the gearbox due to clogging of the breather
Clean or replace the gearbox breather
- Loose fastenings of the gearbox housing and clutch housing covers. Damage to the gaskets
Tighten the threaded connections.
Replace the gaskets (you can use a sealant when installing them)
- The plugs are not tightly screwed in
Tighten the plugs (you can put them on a sealant)