Maintenance of Kamaz vehicle axles
The main axle maintenance operations are checking the tightness of connections, lubricating gearboxes and adjusting bearings and gear engagement.
During maintenance, check the level and, if necessary, add oil to the drive axle housing. Check the oil level using the inspection hole.
If necessary, oil can be added through the same hole.
The used oil is drained after preheating the main gear through the drain holes in the axle housing.
Before adding fresh oil, it is necessary to flush the breathers and clean the magnets of the drain plugs from metal deposits.
In order to reduce their axial movement, the bearings of the main gear drive gear are installed with preload during assembly, which helps maintain the correct engagement of the bevel gear teeth under load and increases the service life of the main gear parts.
High demands are placed on the control accuracy of preloaded bearings. These works must be performed by sufficiently qualified specialists.
The correct adjustment of bearings is determined by the amount of torque that must be applied to the shafts mounted on the bearings to rotate them.
The turning torque can be determined in the absence of special torque wrenches using a spring balance, which is attached to the shaft being tested on an arm of a certain radius.
The main gears also provide the ability to adjust the engagement of the bevel gears.
However, it must be borne in mind that it is not advisable to regulate the working pair during operation.
It is carried out when replacing a worn pair.
Adjustment of bearings and engagement of bevel gears is carried out with the main gear removed from the vehicle.
The preload of the bearings is adjusted by selecting the thickness of the package of two adjusting washers located between the inner races of each pair of bearings on which the bevel gears rotate.
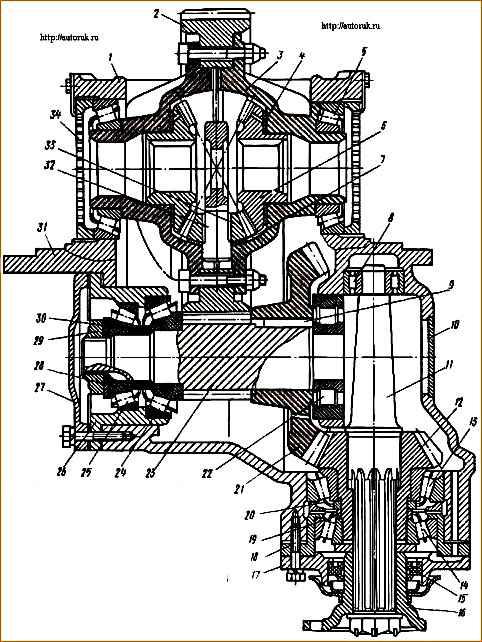
The tapered bearings of the differential housing are adjusted using adjusting nuts 34 (Fig. 1), which are tightened until the distance between the surfaces of the bearing caps increases by 0.1-0.15 mm.
After this, the cover bolts are finally tightened, which creates the required amount of preload on the bearings.
The correctness of the adjustment of the bearings is checked while the vehicle is running by checking the heating temperature of the bearing installation sites. Heating should not exceed 70-80°C.
Maintenance of front axles includes monitoring the condition of the pivot joints.
To maintain the angle of inclination of the kingpins of the front drive axle of off-road vehicles, check the adjustment of the tapered bearings on the ball joint studs; if necessary, they are adjusted by changing the thickness of the shim pack under the cover combined with the steering knuckle lever.
Pin joints of vehicles with a 6X4 wheel arrangement are checked with the wheels hanging so that they do not touch the floor.
The radial clearance, determined by the indicator when rocking the wheel, should not exceed 0.25 mm, the end clearance between the eye of the bridge beam and the steering knuckle should not exceed 0.25 mm.
Pin joints must be periodically lubricated through grease nipples until fresh grease is squeezed out through the gaps between the ends of the beam eye and the steering knuckle.
In this case, to ensure the release of lubricant between the lower end of the eye and the fist, it is necessary to hang the wheel above the floor.
Signs of a malfunction of the drive axle mechanisms are increased noise from the main gear when the vehicle is moving. There may also be an oil leak in the card connectors ers and through the cuffs.
When the vehicle is moving in various modes, serviceable main gears should operate almost silently.
The temperature of the oil in the crankcase should not exceed the ambient temperature by more than 60-70 °C.
The appearance of noise during the operation of the main gear usually indicates a malfunction of the bevel gears due to wear or loosening of the bearings, as well as the appearance of excessively large lateral clearance between the teeth.
One of the reasons for increased noise when driving is a lack of oil in the main gear housing.
Noise that occurs when cornering often indicates a malfunction in the cross-axle differential.
Faulty knocking noises in the main gear are associated with chipped or chipped gear teeth or damaged bearings.
In the front axle of KamAZ-4310 vehicles, this phenomenon may be associated with the destruction of parts of the cam cardan joint of the front wheel drive.
Continuous noise from the final drive when the vehicle is moving at high speed is usually associated with severe wear of the gears, bearings, or lack of oil in the crankcase.
You can check the main gear malfunction based on noise using the following method.
Accelerate the car on the highway from a speed of 20 to 80 km/h, and then reduce the speed by reducing the fuel supply.
Note in which modes the noise appears, reaches its greatest value, and disappears.
After this, accelerate the car to 80 km/h and then coast with the gearbox in neutral until it stops.
A noise noticed during the first test and not repeated during the second test indicates problems with the final drive, differential, and drive axle bearings.
If, with the engine running at different frequencies, when the car is stopped in place, the noises detected during the first test are heard, then it can be stated that these noises do not relate to axles.
At service 2:
- - check the tightness of the drive axles;
- - check and, if necessary, bring the oil level in the crankcases of the drive axles to normal; — clean the breathers of the drive axles from dirt and wash them in diesel fuel.
At service C:
- - tighten the nuts securing the drive axle gearboxes;
- - check the fastening of the flanges on the splined ends of the drive shafts;
- - check the operation of the center differential locking mechanism;
- - check the condition of the hub bearings (with the wheel hubs of the drive axles removed);
- - change the oil in the axle housings.
To check axles for leaks, supply air through the threaded hole under the axle crankcase breather with an excess pressure in the crankcase of 19.6-24.5 kPa (0.2-0.25 kgf/cm 2) . Oil leakage through the cuffs, joints and welds on the beam is unacceptable (slight formation of oil stains on surfaces in the above areas, except for welds, without drop formation is not a rejection sign). To check the oil level in the axle housings, unscrew the control plug on the axle housing. If there is no oil leakage from the inspection hole, then add oil through the filler hole in the gearbox housing to the level of the inspection hole.
To check the fastening of the flanges on the splined ends of the drive axle shafts, place the car on an inspection hole or overpass and place stands under the wheels.
Then release the parking brake, set the gear lever to neutral and disengage the center differential lock.
With your hands, rock the shaft flange in the longitudinal and transverse directions.
If there is a noticeable gap, disconnect the corresponding end of the propeller shaft and, loosening the fastening nuts, tighten them, ensuring the nut tightening torques:
- - center differential flange and intermediate axle outlet flange - 245-294 Nm (25-30 kgcm);
- - rear axle drive flange - 235-353 Nm (24-36 kgcm).
After tightening the nuts, tighten (pin).
To check the operation of the center differential locking mechanism, move the valve lever for engaging the locking mechanism to the “SLIPPERY ROAD” position. In this case, the indicator lamp for turning on the center differential on the instrument panel should light up. If the warning light does not light up, try turning on the lock when the car is moving slowly. If the lock does not engage, correct the problem. When changing the oil, flush the crankcases with diesel fuel and clean the magnets of the drain plugs from metal deposits. Wash the breathers of the drive axles with diesel fuel and blow them with compressed air.
Drain the oil by unscrewing the control and filler plugs. Before draining the oil, warm up the axle with the vehicle's mileage.