When servicing each injector, check and adjust in the following order:
1. Adjust each nozzle to the injection start pressure:
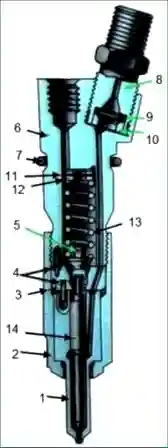
Adjustment is recommended to be carried out on a special stand of the KI-3333 type (Fig. 2), which meets GOST 10579-88.
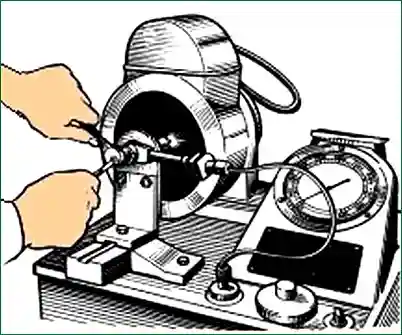
The injection start pressure of the injectors of models 267-02, 261-11 is adjusted by the screw with the injector cap removed and the lock nut unscrewed.
When the screw is screwed in, the pressure increases, when it is turned out, it decreases.
The injection start pressure of the injectors of models 204-50.01 and 51-01 is adjusted using shims.
With an increase in their total thickness, the pressure increases, with a decrease, it decreases.
2. Check the tightness of the atomizer on the locking cone of the needle and the absence of leaks in the places of the seals of the high pressure line.
To do this, create a fuel pressure in the nozzle 1-1.5 MPa (10-15 kgf / cm 2) below the injection start pressure.
At the same time, there should be no leakage of fuel from the spray holes for 15 seconds; it is allowed to moisten the nozzle of the atomizer without tearing off the fuel in the form of a drop.
Check the tightness of the high-pressure line seals by holding under pressure for 2 minutes; on the upper end of the atomizer nut (when the nozzle is installed at an angle of 15 ° to the horizontal surface), there should not be a detached drop of fuel.
3. Check the mobility of the needle by pumping fuel through the nozzle, adjusted to the predetermined injection start pressure on the pressure test stand, at an injection frequency of 30-40 per minute.
It is allowed to check the mobility of the needle at the same time as checking the quality of spraying.
After a long engine operation, it is allowed to reduce the injection start pressure of the injectors by 8%.
4. The quality of atomization is checked on a pressure test stand by pumping fuel through a nozzle adjusted to a predetermined injection start pressure at a frequency of 60-80 injections per minute.
The atomization quality is considered satisfactory if the fuel is injected into the atmosphere in a foggy state and is evenly distributed both over all the jets and over the cross section of each jet.
The beginning and end of the injection must be clear.
After the end of the injection, it is allowed to moisten the spray nozzle without forming a drop.
The fuel injection of the new injector is accompanied by a characteristic sharp sound.
The absence of a sharp sound from used injectors does not mean a decrease in the quality of their work.
5. The tightness of the seal, connection and outer surfaces of the low-pressure cavity must be checked by pressure testing with air at a pressure of 0.45±0.05 MPa (4.5±0.5 kgf/cm 2).
Air passage for 10 seconds is not allowed when air is supplied from the side of the spray nozzle.
6. The tightness of the “atomizer-atomizer nut” connections should be checked by pressing with air at a pressure of 0.5 ± 0.1 MPa (5 ± 1 kgf / cm 2 ) for 10 seconds when air is supplied from the side of the atomizer nozzle.
The passage of air bubbles along the thread of the atomizer nut when it is immersed in diesel fuel is not allowed.
In case of coking or clogging of one or more spray holes of the sprayer, disassemble the nozzle, clean the nozzle parts and rinse thoroughly in filtered diesel fuel.
If there is a leak in the locking cone, the atomizer assembly must be replaced. Replacement of parts in the atomizer is not allowed.
Disassemble the nozzle in the following sequence:
Nozzles models 267-02, 204-50.01, 261-11:
- 1. unscrew the nozzle cap;
- 2. unscrew the lock nut and unscrew the adjusting screw as far as it will go;
- 3. unscrew the spring nut one and a half to two turns;
- 4. unscrew the atomizer nut;
- 5. remove the atomizer, protecting the needle will spray spruce from falling out.
Nozzle model 51-01:
- 1. unscrew the atomizer nut;
- 2. remove the atomizer, protecting the atomizer needle from falling out.
Clean off carbon deposits from the sprayer body with a metal brush or sandpaper with a grain size not coarser than "M40".
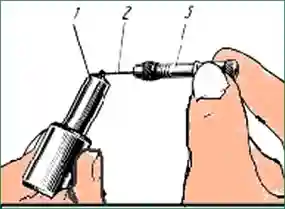
Clean the spray holes (Fig. 3) with a steel wire 0.3 mm in diameter (for nozzle nozzles models 267-02, 204-50.01, 261-11) and 0.28 mm in diameter (for nozzle nozzle model 51-01) .
It is not allowed to use hard materials and sandpaper to clean the internal cavities of the sprayer body and needle surfaces.
Before assembling, rinse the atomizer and needle thoroughly in filtered diesel fuel.
The needle should move easily: extended from the atomizer body by one third of the guide length, when the atomizer is tilted at an angle of 45 ° from the vertical, the needle should smoothly, without delay, completely lower under its own weight.
Assemble the nozzle in the reverse order of disassembly.
When tightening the nut, turn the atomizer against the direction of screwing the nut until it stops against the locking pins and, holding it in this position, screw the nut on by hand, then finally tighten the nut.
The tightening torque of the spray nut is 60-70 Nm (6-7 kgfm), the nozzle fitting is 80-100 Nm (8-10 kgf m).
After assembly, adjust the injector to the injection start pressure and check the quality of the fuel atomization and the clarity of the atomizer.
The installation of injectors or nozzles that do not match this engine is strictly prohibited.