Disassembly of the engine is presented in the article - "Disassembly of the VAZ-21126 engine"
After disassembly, thoroughly clean, rinse and dry all parts
Clean the piston head from carbon deposits.
If the piston has scuff marks, burn marks, deep scratches, cracks, replace the piston.
Clean the piston ring grooves.
Clean the oil drain holes with a suitable piece of wire.
Check the gaps between the rings and the grooves on the piston, after cleaning the rings from carbon deposits.
Nominal clearance, mm:
- 0.04–0.075 - top compression ring 1;
- 0.03–0.065 - lower compression ring 2;
- 0.02–0.055 - oil scraper ring 3.
The maximum allowable gap for all rings is 0.15 mm.
The most accurate clearances can be determined by measuring the rings and grooves on the piston.
To do this, measure the thickness of the rings with a micrometer in several places around the circumference, then use a set of feelers to measure the width of the grooves also in several places around the circumference.
Calculate the average gaps (difference between ring thickness and groove width).
If at least one of the gaps exceeds the maximum allowable, replace the piston with rings.
Measure the gaps in the locks of the rings by inserting the ring into a special mandrel.
If there is no mandrel, insert the ring into the cylinder in which it worked (or will work if the ring is new), slide the ring into the cylinder like a mandrel so that it is installed in the cylinder evenly, without distortions and measure the gap in the ring lock with a feeler gauge.
The nominal gap should be 0.25–0.45 mm, the maximum allowable (due to wear) - 1.0 mm.
If the gap exceeds the limit, replace the ring.
If the gap is less than 0.25 mm, carefully grind off the ends of the ring with a needle file.
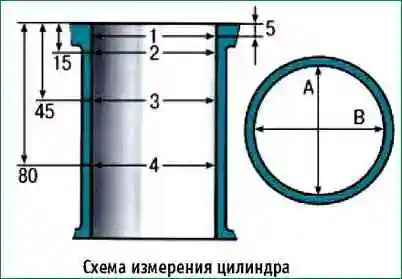
Measure the cylinder diameters in two perpendicular planes (Fig. 7) (B - along, A - across the cylinder block) and in four belts (1, 2, 3 and 4).
For this, you need a special device - a caliper.
Nominal cylinder size (see table), ovality and taper should not exceed 0.05 mm.
If the maximum wear value is greater than 0.15 mm or the ovality exceeds the specified value, bore the cylinders to the nearest oversize of the pistons, leaving an allowance of 0.03 mm for the honing diameter.
Then honing the cylinders, maintaining such a diameter that when installing the piston, the estimated clearance between it and the cylinder is 0.025–0.045 mm.
Troubleshooting, boring and honing of the block should be carried out in workshops with special equipment.
Nominal sizes of cylinders and pistons
Check the flatness of the cylinder head connector surface.
Attach a caliper (or ruler) to the plane:
- - in the middle of the block;
- -in the longitudinal and transverse directions;
- – along the diagonals of the plane.
In each position, use a feeler gauge to determine the gap between the ruler and the plane.
This is the deviation from the plane.
If the deviation exceeds 0.1 mm, replace the block.
Check the clearances between pistons and cylinders.
Clearance is defined as the difference between the measured piston and cylinder diameters.
The nominal gap is 0.025–0.045 mm, the maximum allowable gap is 0.15 mm.
If the gap does not exceed 0.15 mm, you can select pistons from subsequent classes so that the gap is as close as possible to the nominal.
If the gap exceeds 0.15 mm, bore the cylinders and install pistons of the appropriate oversize.
Measure the piston diameter at a distance of 10 mm from the lower edge of the skirt in a plane perpendicular to the piston pin.
When replacing parts of the connecting rod and piston group, it is necessary to select pistons for cylinders by class and one group by weight, as well as piston pins for pistons by class and connecting rods by weight.
To match pistons to cylinders, calculate the gap between them.
For the convenience of selecting pistons for cylinders, they are divided depending on the diameters into five classes through 0.01 mm: A, B, C, D, E (table).
Class - cylinder diameter, mm - piston diameter, mm:
- A - 82.00-82.01 - 81.965-81.975;
- B - 82.01-82.02 - 81.985-81.995;
- C - 82.02-82.03 - 82.005-82.015;
- D - 82.03-82.04
- E - 82.04-82.05
Pistons of nominal size of three classes are supplied as spare parts: A, C, E and two repair sizes (1st repair size - increased by 0.4 mm, 2nd - by 0.8 mm).</p >
By weight, the pistons are divided into three groups: normal, increased by 5 g and reduced by 5 g.
Pistons of the same group must be installed on the engine.
For oversized pistons, spare parts are supplied with rings oversized by 0.4 and 0.8 mm.
On the rings of the 1st repair size, the number "40" is engraved, on the 2nd - "80".
Cylinder class designations are engraved on the lower plane of the block (the mating surface for the oil sump) opposite each cylinder.
The following data is stamped on the piston crown:
- 1 – piston class by diameter;
- 2 - an arrow showing the direction of piston installation;
- 3 – engine model.
Replace cracked fingers.
The finger should easily enter the piston with the force of the thumb.
Insert your finger into the piston.
If play is felt when the finger is wiggled, replace the piston. When replacing a piston, match your finger to it according to the class.
Replace broken rings and oil ring expander
Replace cracked fingers.
The finger should easily enter the piston with the force of the thumb.
Insert your finger into the piston.
If play is felt when shaking the finger, replace the piston.
When replacing a piston, match it with a finger according to the class.
Replace broken rings and oil ring expander.
Replace any broken or cracked circlips holding the piston pin.
The ends of the retaining rings must be in the same plane.
Replace bent rings.
Replace bent connecting rods.
Replace the connecting rod if there are scores and deep scratches in the sleeve 1 of the upper head.
Replace the connecting rod if it is found during disassembly of the engine that the connecting rod bearings have rotated in the connecting rod.
Warning. The connecting rods are processed together with the covers, so they cannot be dismantled.
Insert your finger into the upper end of the connecting rod.
If play is felt when you wiggle your finger, replace the connecting rod.
Connecting rods with caps are divided into classes according to the mass of the upper and lower heads.
Connecting rods of the same class must be installed in the engine.
The connecting rod marking is on the bottom head and connecting rod cap.
If there are deep scratches, scratches, nicks on the surfaces on which the seals work, the crankshaft must be replaced.
Measure the main and connecting rod journals of the crankshaft.
Nominal diameters of crankshaft journals, mm:
- - Indigenous - 50.799–50.819;
- - connecting rod - 47.830–47.850. If wear or ovality of the journals exceeds 0.03 mm, they must be ground to the nearest repair size.
There are four repair sizes with a decrease in the diameter of the necks, mm:
- - first - 0.25;
- - second - 0.5;
- - third - 0.75;
- - fourth - 1.00.
If there are minor scuffs, risks, scratches on the main and connecting rod journals 1, you need to grind them to the nearest repair size.
This work is recommended to be carried out in a specialized workshop.
After grinding, polish the journals and dull the sharp edges of the chamfers of the oil channels 2 with an abrasive cone.
Rinse the crankshaft and blow out the oil passages with compressed air.
The ovality and taper of all necks after grinding should not exceed 0.005 mm.
After grinding the necks, install the bearings of repair sizes.
If the working surfaces of the thrust half-rings have scuffs, marks and delaminations, replace the half-rings. It is forbidden to carry out any fitting work on the half rings
Measure the end clearance of the crankshaft.
To do this, install the crankshaft and thrust washers in the cylinder block and tighten the bolts securing the main bearing caps.
Install the indicator so that its leg rests against the shaft flange.
Move the crankshaft away from the indicator until it stops and set the indicator needle to zero.
Move the shaft in the opposite direction.
The indicator will show the amount of clearance.
The nominal axial clearance of the crankshaft is 0.06–0.26 mm, the maximum allowable is 0.35 mm.
If the gap exceeds the maximum allowable, replace the thrust half rings.
The spare half rings are supplied in two sizes: nominal - 2.31–2.36 mm and repair (increased by 0.127 mm) - 2.437–2.487 mm.
Inspect the connecting rod and main bearings.
Replace liners with cracks, scuffs, chipping.
It is forbidden to carry out any fitting work on the liners.
Nominal thickness of liners, mm:
- - Indigenous- 1.824-1.831;
- - connecting rod - 1.723-1.730.
The liners are supplied as spare parts in four repair sizes, increased thickness, mm:
- - first - by 0.25;
- - second - by 0.50;
- - third - by 0.75;
- - fourth - by 1.00.
Check the clearances between the main bearing shells and the crankshaft journals.
This work is recommended to be carried out in a specialized workshop.
Measure the diameters of the journals and main bearings by placing the bearing caps on the block and tightening them to the correct torque. Calculate the clearance.
Gaps between bearings and crankshaft journals:
- - main bearings (nominal 0.026–0.073 mm, maximum allowable 0.15 mm);
- - connecting rod bearings (nominal 0.02-0.07 mm, maximum allowable 0.1 mm).
If the gap exceeds the maximum allowable, the crankshaft must be ground to the next repair size.
When regrinding the connecting rod and main journals of the crankshaft and on the repair size on the first cheek of the crankshaft, it is necessary to put the appropriate stamp, for example, W 0.25 and K 0.25, respectively.
A specialist workshop can measure the runout of the crankshaft journals.
The runout should be:
- - main journals and seating surface for the oil pump drive gear no more than 0.03 mm;
- - landing surface for the flywheel no more than 0.04 mm;
- - seating surface for pulleys and seals no more than 0.05 mm.
Thoroughly clean and flush the crankshaft oil passages.
It is not recommended to press out the plugs yourself, for this, contact a specialized workshop
Thoroughly clean the surfaces of the cylinder block from the remnants of old gaskets.
Inspect the block carefully. If cracks are found, the block must be replaced complete with main bearing caps.
Check the tightness of the cylinder block cooling jacket.
To do this, plug the hole for the water pump (by installing the pump with a gasket) and pour antifreeze into the cooling jacket.
If a leak is noticeable in any place, then the block is leaky and needs to be replaced.
Inspect the cylinders.
If there are scratches, scuffs, shells and other defects on the cylinder mirror, bore the cylinders to the repair size (this work is recommended to be done in a specialized workshop) or replace the cylinder block.
For various defects with a depth of more than 0.8 mm, the unit cannot be repaired and must be replaced.
Clean the carbon from the top of the cylinders. If a belt has formed there due to cylinder wear, remove it with a scraper
Check the presence of nozzles for cooling the piston bottom and the tightness of their fit in the holes in the beds of the cylinder block.
After fault detection and fitting of engine parts, you can start assembling the engine.
The engine assembly is presented in the article - "Assembly of the VAZ-21126 engine".