Betrachten wir die Montage eines Dieselmotors in einer bestimmten Reihenfolge und berücksichtigen dabei, dass unsere Teile und Baugruppen zuvor vormontiert und getestet wurden
Für die Montage benötigen Sie spezielle Dorne und Vorrichtungen, die nach den in den Zeichnungen angegebenen Maßen angefertigt werden können.
Zylinderblock-Unterbaugruppe
Wir montieren den Zylinderblock auf einem Ständer (siehe Bild), Befestigen Sie es mit Befestigungsstiften für die vier Löcher des Blocks.
Wenn Sie den Zylinderblock zusammenbauen, drücken Sie die Ausrichtungsstifte unter die Zylinderköpfe, installieren Sie die Steuerradabdeckung und das Schwungradgehäuse.
Wir pressen die Stifte mit einem Dorn, der dafür sorgt, dass sie nicht mehr als 10 mm über die Passebenen des Zylinderblocks hinausragen.
Wir reinigen die Ölkanäle des Blocks mit Borstenbürsten und einem Baumwolltuch, zu diesem Zweck verwenden wir einen Reinigungsstab.
Die Stopfen der horizontalen und vertikalen Ölkanäle müssen mit Nitrospachtel oder dickem Nitrolack eingeschraubt werden.
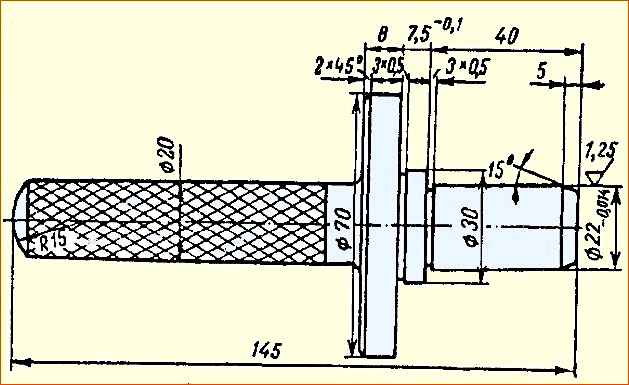
Wir drücken die vordere Buchse der Schubachse so in das Loch im Block, dass sichergestellt ist, dass das Loch in der Buchse mit dem Ölversorgungskanal im Zylinderblock übereinstimmt.
Die Buchse wird mit einem Dorn eingepresst (Abb. 1), der eine Größe von 7,5 mm vom vorderen Ende des Zylinderblocks bis zum vorderen Ende der Buchse gewährleistet.
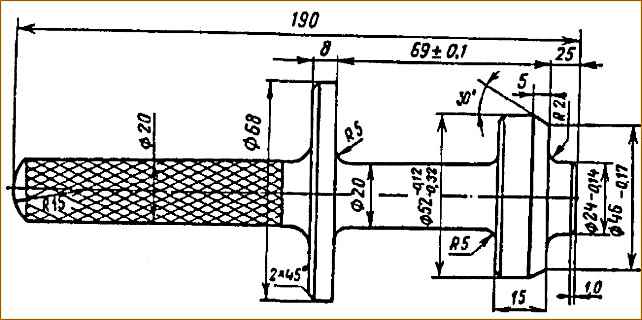
So drücken Sie die Wellendichtung des angetriebenen Zahnrads des Hochdruck-Kraftstoffpumpenantriebs ein:
- - Installieren Sie die Öldichtung am Dorn (Abb. 2);
- - Schmieren Sie die Außenfläche mit Dieselöl und drücken Sie es in die Bohrung des Zylinderblocks. Halten Sie dabei einen Abstand von 69 mm vom vorderen Ende des Zylinderblocks bis zum Ende der Öldichtung (bereitgestellt durch einen Dorn) ein.
Einbau des Einspritzpumpenantriebs und der Stößel
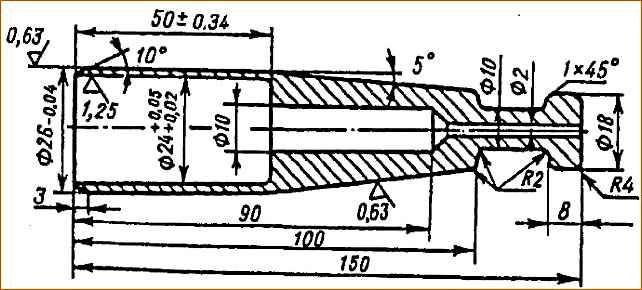
Wir bauen den Einspritzpumpenantrieb von vorne in die Bohrung im oberen Teil des Zylinderblocks ein.
Um die Öldichtung vor Beschädigungen zu schützen, haben wir einen Sicherheitsdorn auf das freie Ende der Welle gesteckt (Abb. 3).
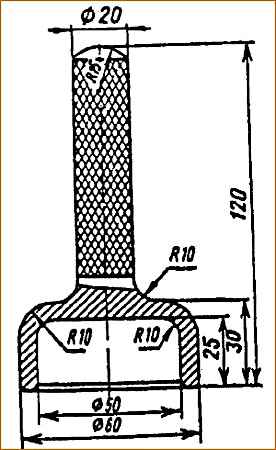
Verwenden Sie beim Einbau des Antriebs einen Dorn (Abb. 4) und nach dem Einbau sollten die Außenringe der Kugellager an den Leisten der Zylinderblocksockel anliegen.
Nachdem Sie das Loch im Druckflansch zur Befestigung der Antriebe mit den Löchern im Zylinderblock ausgerichtet haben, schrauben Sie die Schrauben mit den Sicherungsscheiben ein und biegen Sie ihre Kanten an den Kanten der Schraubenköpfe, sodass Sie sie fest gegen die Kanten drücken.
Nach dem Festziehen der Schrauben sollte sich die Antriebswelle der Kraftstoffpumpe leicht drehen lassen, ohne zu blockieren.
Dann drehen wir den Block um 180˚ – die Position mit dem Kurbelgehäuse nach oben – und installieren die Drücker.
Die Stößel werden mit einem Spalt von 0,012 mm auf der Achse montiert.
Wenn das Spiel nicht eingehalten wird, führt dies zu einem abnormalen Motorbetrieb.
Bei einem größeren Spalt verziehen und klopfen die Drücker, bei einem kleinen Spalt verklemmen sie sich.
Pusher-Installationssequenz
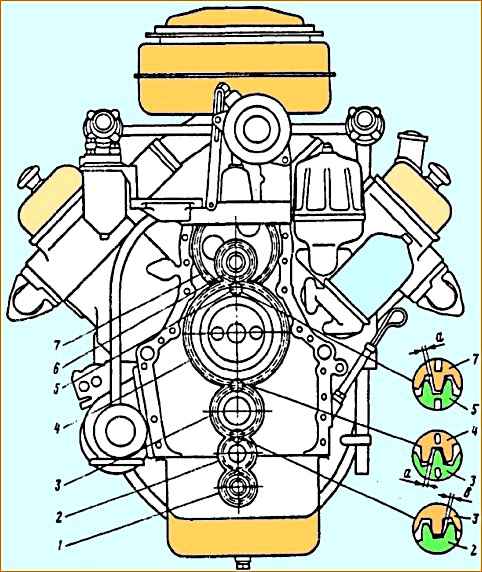
Setzen Sie die äußerste Achse der Drückerbaugruppe mit dem verschlossenen Ende nach außen in die vordere Buchse ein und bewegen Sie die Achse in den Zylinderblock.
Wir installieren nacheinander die Drücker des ersten und vierten Zylinders für den YaMZ-236-Motor (den ersten und fünften Zylinder für den YaMZ-238-Motor) und eine Distanzhülse.
Montieren Sie die verbleibenden Pusher-Achsenbuchsen und die verbleibenden zwei Pusher an der Außenachse.
In die Buchse des dritten Blockträgers Zylinder, installieren Sie die Mittelachse der Drücker, installieren Sie die Drücker, die Distanzhülse und die Drücker in Reihe.
Gleichzeitig installieren wir Drücker für zwei Zylinder auf einer Achse entsprechend der Nummerierung der Zylinder: für YaMZ-238-Motoren - 2-6, 3-7, 4-8 und für YaMZ-236-Motoren - 25, 36.
Wir montieren die Drücker so, dass die Ferse des Drückers zum Fenster im Zylinderblock unter der Drückerstange zeigt.
Die Drücker müssen sich leicht und ohne Blockierung auf den Achsen drehen lassen und die axiale Verschiebung muss durch Distanzbuchsen begrenzt werden. Alle Teile müssen vor dem Einbau abgewischt und mit Dieselöl geschmiert werden.
Einbau der Nockenwelle und Kurbelwelle
Wir bauen die Nockenwelle komplett mit Zahnrädern in den Zylinderblock ein, nachdem wir zuvor die Position der Stößel überprüft haben.
Die Reparaturmaße der Nockenwellenzapfen müssen mit den Reparaturmaßen der Löcher der in den Zylinderblock eingepressten Buchsen übereinstimmen.
Vor dem Einbau der Nockenwellenwelle diese großzügig mit Dieselöl schmieren und die Einbaumarkierung „P“ (siehe Abb. 5) am Zahn des Antriebsrads 5 des Kraftstoffpumpenantriebs mit der Markierung „P“ auf der Länge ausrichten des Zahns des Abtriebsrads 7 des Einspritzpumpenantriebs.
Beim Ausrichten der Löcher des Druckflansches mit den Löchern im Zylinderblock ist es notwendig, den Flansch so zu platzieren, dass er das Loch abdeckt, und zwar unter der Achse der Stößel im Zylinderblock.
Wir schrauben zwei Schrauben mit Sicherungsscheiben in die ausgerichteten Löcher. Die Antennen der Sicherungsscheiben sollten in die Löcher des Druckflansches passen und die Enden der Unterlegscheiben sollten nach dem Anziehen der Schrauben gebogen und gegen die Kanten gedrückt werden.
Nach dem endgültigen Anziehen der Schrauben sollte sich die Nockenwelle leicht drehen lassen, ohne zu blockieren.
Das Umfangsspiel im Zahneingriff sollte im Bereich von 0,09 - 0,22 mm liegen; Wir überprüfen den Spalt an drei gleichmäßig verteilten Punkten, wobei der Motorblock mit dem Kurbelgehäuse nach unten positioniert ist.
Bauen Sie die Motorkurbelwelle ein. Ausführliche Informationen zum Einbau der Kurbelwelle finden Sie im Artikel „Einbau der Kurbelwelle in den Motor“.
Montage der Steuerradabdeckung, des Lüfterantriebs, der vorderen Motorhalterung und der Kurbelwellenriemenscheibe.
Bevor Sie die Steuerradabdeckung anbringen, wischen Sie die Passfläche ab, schmieren Sie sie mit Dichtmittel und bringen Sie die rechten und linken Abdeckungsdichtungen an.
Beim Einbau von Dichtungen dürfen Falten, Risse und Dichtungen die Verbindungskanäle nicht überlappen.

Um die Kurbelwellen-Öldichtung im Deckel vor Beschädigungen zu schützen, setzen Sie einen Sicherheitsdorn auf das vordere Ende der Kurbelwelle (Abb. 6) und schmieren Sie die Öldichtung mit Dieselöl.
Wir montieren die Steuerradabdeckung auf den Stiften des Zylinderblocks, nachdem wir zuvor die Passflächen abgewischt haben, und befestigen sie mit zehn Schrauben mit Unterlegscheiben und Federscheiben.
Wir montieren den Lüfterantrieb auf den Stehbolzen der Steuerradabdeckung, nachdem wir zuvor die Dichtung montiert haben. In diesem Fall muss das Lüfterantriebsrad mit dem Nockenwellenrad in Eingriff stehen.
Wir sichern den Lüfterantrieb mit vier Muttern und Unterlegscheiben.
Wir montieren die obere Abdeckung des Zylinderblocks auf den Stehbolzen und befestigen sie mit zwei Schrauben und fünf Muttern mit Unterlegscheiben und Federscheiben.
Vor dem Anbringen der Abdeckung ist es notwendig, die Passfläche abzuwischen und eine Dichtung auf den Bolzen anzubringen. Ziehen Sie beim Anbringen der Abdeckung die Schraube und Mutter unter der Generatorhalterung nicht vollständig fest.
Dann montieren wir die Lukenstopfendichtung und den Stopfen selbst an der oberen Abdeckung, die wir mit vier Schrauben mit angebrachten Federscheiben befestigen.
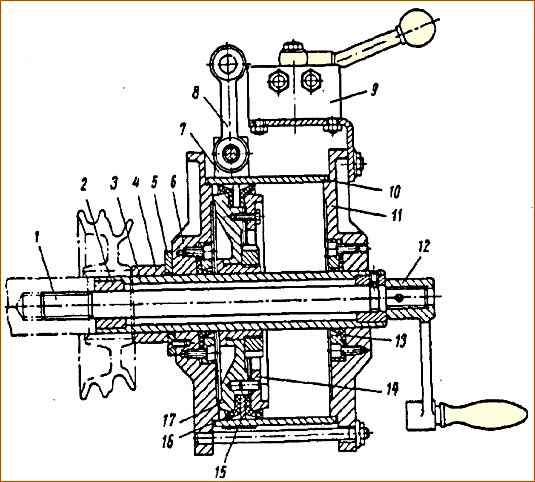
Wir montieren die vordere Motorhalterung an der Steuerradabdeckung und befestigen sie mit vier Schrauben mit angebrachten Federscheiben.
Die Schrauben müssen mit einem Drehmoment von 90–110 Nm (9–11 kgcm) angezogen werden. Bevor Sie die vordere Stütze installieren, müssen Sie die Passflächen abwischen.
Beim Einbau der Kurbelwellenriemenscheibe ist es notwendig, die Kurbelwelle in die Position zu drehen, in der der Segmentkeil gedrückt werden kann, und ihn in die Keilnut am vorderen Ende der Kurbelwelle zu drücken.
Dann Wir wischen die Sitzflächen ab und drücken die Riemenscheibe auf das vordere Ende der Kurbelwelle, bis sie am Bund anliegt, und befestigen sie mit einer Schraube und einer Unterlegscheibe.
Um die Riemenscheibe auf das vordere Ende der Kurbelwelle zu drücken, verwenden Sie eine pneumatische Vorrichtung (Abb. 7).
Befestigen Sie dazu eine Riemenscheibe am Rohr 3 und schrauben Sie die Stange 1 mit dem Griff 12 in das Loch in der Kurbelwelle unter der Riemenscheiben-Befestigungsschraube.
Richten Sie die Nut in der Riemenscheibe mit der Passfeder am vorderen Ende der Kurbelwelle aus und versorgen Sie Zylinder 10 mit Luft, indem Sie Ventil 9 öffnen.
Wenn sich der Kolben zusammen mit Rohr 3 und Buchse 4 bewegt, wird die Riemenscheibe angedrückt.
Zur einfacheren Bedienung hängen wir das Gerät am Ohrring 8 am Balancer auf.
Der Luftdruck im System muss innerhalb von 0,5–0,6 MPa (5–6 kgf/cm 2) gehalten werden.
Montage des Schwungradgehäuses, des Schwungrads und des Entlüftungsrohrs.
Um das Schwungradgehäuse zu installieren, ist es notwendig, den Zylinderblock mit der Rückseite nach oben um 90° zu drehen, die Passfläche des Zylinderblocks unter dem Schwungradgehäuse abzuwischen und mit Dichtmittel zu schmieren.
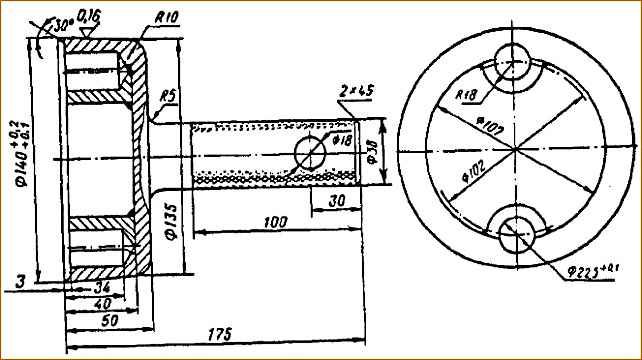
Dann montieren wir die Schwungradgehäusedichtung auf den Fixierstiften am Zylinderblock und den Sicherungsdorn (Abb. 8) am hinteren Ende der Kurbelwelle.
Die Oberfläche des Dorns und die Arbeitskante der Öldichtung müssen mit Dieselöl geschmiert werden.
Wir montieren das Schwungradgehäuse auf den Passstiften des Zylinderblocks und befestigen es mit Schrauben mit angebrachten Federscheiben, die wir mit einem Drehmoment von 80-100 Nm (8-10 kgf·m) festziehen.
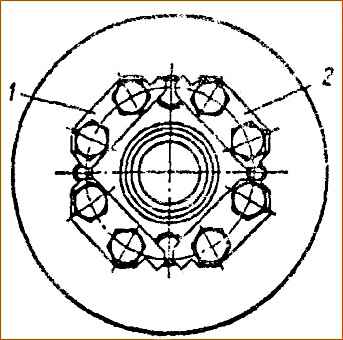
Wir befestigen das Schwungrad mithilfe einer Aufhängung an den Passstiften der Kurbelwelle.
Ziehen Sie die Befestigungsschrauben des Schwungrads mit einem Drehmoment von 200–220 Nm (20–22 kgf·m) an, sichern Sie sie mit Sicherungsplatten, die unter dem Kopf jedes Schraubenpaars angebracht sind, und biegen Sie sie an der Kante der Schrauben wie folgt siehe Abbildung 9.
Um den Einbau des Schwungrads in der richtigen Position relativ zur Kurbelwelle zu erleichtern, sind die Zahlen 2 auf der Schwungradnabe und am Ende der Welle eingeprägt, die bei der Montage ausgerichtet werden müssen.
Wir befestigen das Entlüftungsrohr mit zwei Schrauben mit Gravurscheiben am Zylinderblock.
Führen Sie dazu Schrauben mit Unterlegscheiben in die Löcher des Lüftungsrohrs ein, legen Sie eine Dichtung auf die Schrauben und montieren Sie sie am Zylinderblock, indem Sie die Schrauben von Hand mit 1-2 Gewindegängen einschrauben und dann eine Schelle anbringen Entlüftungsrohr und befestigen Sie es mit einer Schraube am Schwungradgehäuse.
Danach ziehen Sie abschließend die Schrauben fest, mit denen das Lüftungsrohr befestigt ist.
Einbau von CMO-Filtern und Kraftstoffeinspritzpumpe
Beim Einbau von Zentrifugal- und Grobölfiltern müssen die Oberflächen des Zylinderblocks abgewischt, mit Dichtmittel geschmiert und Dichtungen aufgetragen werden.
Wir montieren die Hochdruck-Kraftstoffpumpe auf den Plattformen zwischen den Zylinderkammern und drehen die Kurbelwelle in die Position, in der der Schlüssel in die angetriebene Zahnradwelle der Kraftstoffpumpe gedrückt werden kann.
Um die Welle zu schützen, installieren Sie einen Ständer darunter und drücken Sie den Schlüssel mit einem Dorn hinein.
Dann montieren wir die Halbkupplungsbaugruppe auf der Welle des Abtriebsrads des Einspritzpumpenantriebs. Vor der Installation müssen Sie die Ausrichtung der mit „O“ gekennzeichneten Markierungen auf dem Flansch und der Kupplungshälfte überprüfen.
Wir montieren die Kraftstoffeinspritzpumpenbaugruppe mit dem Geschwindigkeitsregler und der automatischen Einspritzvorlaufkupplung am Block und befestigen sie mit vier Schrauben, nachdem wir zuvor Unterlegscheiben darauf angebracht haben.
Wir verbinden die automatische Einspritzvorlaufkupplung der Einspritzpumpe mit einer Textolith-Unterlegscheibe mit der Halbkupplung der angetriebenen Getriebewelle.
In diesem Fall muss sichergestellt werden, dass das axiale Spiel zwischen einem Nocken der Antriebshalbkupplung und dem Ende der automatischen Einspritzvorlaufkupplung innerhalb von 0,5 bis 0,6 mm liegt und das Spiel zwischen dem zweiten Nocken und dem Ende von Die Kupplung beträgt mindestens 0,5 mm.
Wir überprüfen die Lücken mit einem Satz Fühlerlehren.
Außerdem ist darauf zu achten, dass die Markierungen auf der Antriebshalbkupplung und der automatischen Einspritzvorlaufkupplung übereinstimmen. Ziehen Sie die Mutter der Kupplungshälfte der Abtriebswelle an und sichern Sie sie mit einem Splint.
Wir werden die Fortsetzung der Dieselmontage in den folgenden Artikeln betrachten, die Folgendes behandeln:
- - Technologie zur Montage der Zylinder-Kolben-Gruppe;
- - Einbau der Ölpumpe;
- - Einbau von Zylinderköpfen, Ventilkipphebeln und Einstellung des Ventilspiels;
- - Installation von Einspritzdüsen, Kraftstoffleitungen und Verbindungsrohren;
- - Einfahren und Testen des Motors;
- - Kaltlauf des Motors Körper;
- - heißer Motor eingelaufen.