К основным дефектам головки блока цилиндров, которые можно устранить ремонтом, относятся: коробление плоскости прилегания к блоку цилиндров, износ седел и направляющих втулок клапанов
Непрямолинейность плоскости головки, соприкасающейся с блоком, при проверке ее на контрольной плите щупом не должна быть более 0,05 мм.
Незначительное коробление головки (до 0,3 мм) устраняйте шабровкой плоскости по краске. При короблениях, превышающих 0,3 мм, головку необходимо шлифовать.
Восстановление герметичности клапанов и замена втулок клапанов
Нарушение герметичности клапанов при правильных зазорах между стержнями клапанов и коромыслами, а также при исправной работе карбюратора и системы зажигания обнаруживается по характерным хлопкам из глушителя и карбюратора.
Двигатель при этом работает с перебоями и не развивает полной мощности.
Восстановление герметичности клапанов осуществляйте притиркой рабочих фасок клапанов к их седлам.
При наличии на рабочих фасках клапанов и седел раковин, кольцевых выработок или рисок, которые нельзя вывести притиркой, прошлифуйте фаски с последующей притиркой клапанов к седлам.
Клапаны с покоробленными головками замените.
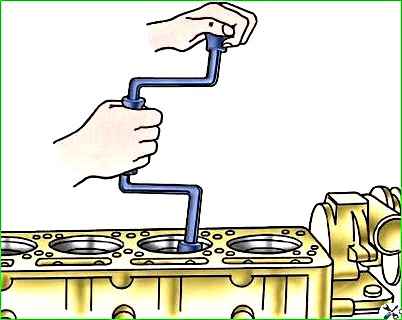
Фаски клапанов притирайте пневматической или электрической дрелью модели 2213, 2447 ГАРО или вручную при помощи коловорота.
Притирку производите возвратно-вращательными движениями, при которых клапан проворачивается в одну сторону несколько больше, чем в другую.
На время притирки под клапан установите отжимную пружину с небольшой упругостью.
Внутренний диаметр пружины должен быть около 10 мм.
Пружина должна несколько приподнимать клапан над седлом, а при легком нажатии клапан должен садиться на седло.
Связь инструмента с клапаном осуществляется резиновым присосом, как показано на рис. 2.
Для лучшего сцепления присоса с клапаном их поверхности должны быть сухими и чистыми.
Для ускорения притирки используйте притирочную пасту, составленную из одной части микропорошка марки М20 и двух частей моторного масла.
Смесь перед применением тщательно перемешайте.
Притирку ведите до появления на рабочих поверхностях седла и тарелки клапана равномерной матовой фаски по всей окружности.
К концу притирки уменьшайте содержание микропорошка в притирочной пасте.
Заканчивайте притирку на одном чистом масле. Вместо притирочной пасты можно использовать наждачный порошок № 00, смешанный с моторным маслом.
Для шлифовки рабочих фасок клапанов рекомендуется применять шлифовальные станки типа Р–108 или ОПР–1841 ГАРО.
При этом стержень клапана зажмите в центрирующем патроне бабки, устанавливаемой под углом 44°30' к рабочей поверхности шлифовального камня.
Уменьшение на 30' угла наклона рабочей фаски головки клапана по сравнению с углом фаски седел ускоряет приработку и улучшает герметичность клапанов.
При шлифовке снимайте с фаски головки клапана минимальное количество металла.
Высота цилиндрического пояска рабочей фаски головки клапана после шлифовки должна быть не менее 0,7 мм, а соосность рабочей фаски относительно стержня в пределах 0,03 мм общих показаний индикатора.
Биение стержня клапана – не более 0,02 мм. Клапаны с большим биением замените новыми.
Не перешлифовывайте стержни клапана на меньший размер, так как возникнет необходимость в изготовлении новых сухариков тарелок клапанных пружин.
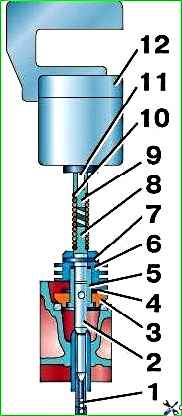
Фаски седел шлифуйте под углом 45° соосно отверстию во втулке. Ширина фаски должна быть 1,6–2,4 мм.
Для шлифовки седел рекомендуется применять приспособление, изображенное на рис. 2.
Седло шлифуйте без притирочной пасты или масла до тех пор, пока камень не станет обрабатывать всю рабочую поверхность.
После грубой обработки смените камень на мелкозернистый и произведите чистовую шлифовку седла.
Биение фаски относительно оси отверстия втулки клапана не должно превышать 0,03 мм.
Изношенные седла замените новыми.
В запасные части поставляются седла клапанов, имеющие наружный диаметр больше номинального на 0,25 мм.
Изношенные седла извлекайте из головки с помощью зенкера.
После извлечения седел расточите в головке гнезда для выпускного клапана до диаметра 38,75+0,025 мм и для впускного клапана до диаметра 49,25+0,25 мм.
Перед запрессовкой седел нагрейте головку блока цилиндров до температуры 170°С, а седла охладите сухим льдом.
Запрессовку производите быстро, не давая возможности седлам нагреться. Остывшая головка плотно охватывает седла.
Для увеличения прочности посадки седел зачеканьте их по наружному диаметру при помощи плоской оправки, добиваясь заполнения фаски седла.
Затем прошлифуйте до требуемых размеров и притрите.
Если износ стержня клапана и направляющей втулки настолько велик, что зазор в их сочленении превышает 0,25 мм, то герметичность клапана восстанавливайте только после замены клапана и его втулки.
В запасные части поставляются клапаны только номинальных размеров, а направляющие втулки – с внутренним диаметром, уменьшенным на 0,3 мм, для последующей их развертки под окончательный размер после запрессовки в головку блока цилиндров.
Запрессованные втулки развертывайте до диаметра 9+0,022 мм.
Стержень впускного клапана имеет диаметр 9 –0,050 –0,075 мм, выпускного 9 –0,075 –0,095 мм, следовательно, зазоры между стержнями впускного и выпускного клапанов и втулками должны быть соответственно равны 0,050–0,097 мм и 0,075–0,117 мм.
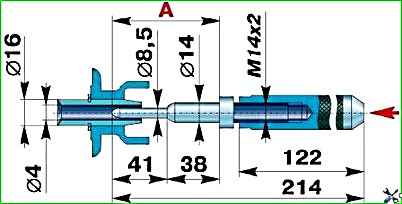
Изношенные направляющие втулки выпрессовывайте из головки блока цилиндров с помощью выколотки, показанной на рис. 3.
Новую втулку запрессовывайте со стороны коромысел с помощью той же выколотки до упора в стопорное кольцо, имеющееся на втулке.
При этом, как и при запрессовке седел клапанов, головку блока цилиндров нагрейте до температуры 170°С, а втулку охладите сухим льдом.
После замены втулок клапанов произведите шлифовку седел (центрируясь по отверстиям во втулках) и затем притрите к ним клапаны.
После шлифовки седел и притирки клапанов все каналы и места, куда мог бы попасть абразив, тщательно промойте и продуйте сжатым воздухом.
Втулки клапанов – металлокерамические, пористые.
После окончательной обработки и промывки пропитайте их маслом. Для этого в каждую втулку вставьте на несколько часов пропитанный в веретенном масле войлочный фитиль.
Стержни клапанов перед сборкой смажьте тонким слоем смеси, приготовленной из семи частей масляного коллоидно-графитного препарата и трех частей моторного масла.
Замена клапанных пружин
Возможными неисправностями клапанных пружин, появляющимися в процессе эксплуатации, могут быть: уменьшение упругости, обломы или трещины на витках.
Упругость клапанных пружин проверяйте при разборке клапанного механизма.
Усилие, необходимое для сжатия новой клапанной пружины до 46 мм по высоте должно быть 267–310 Н (27,3–31,7 кгс), а до 37 мм – 686–784 Н (70–80 кгс).
Если усилие сжатия пружины до 46 мм по высоте менее 235 Н (24 кгс), а до 37 мм менее 558,6 Н (57 кгс), то такую пружину замените новой.
Пружины с обломами, трещинами и следами коррозии замените новыми.
Замена толкателей
Направляющие отверстия в блоке под толкатели изнашиваются незначительно, поэтому номинальный зазор в этом сопряжении восстанавливайте заменой изношенных толкателей.
В запасные части поставляются толкатели только номинального размера.
Толкатели подбирайте к отверстиям с зазором 0,040–0,015 мм.
Толкатели в зависимости от размера наружного диаметра разбиты на две группы и маркируются клеймением: цифрой 1 – при диаметре толкателя 25 –0,008 –0,015 мм и цифрой 2 – при диаметре толкателя 25 –0,015 –0,022 мм.
Правильно подобранный толкатель, смазанный жидким минеральным маслом, должен плавно опускаться под собственной тяжестью в гнездо блока и легко проворачиваться в нем.
Толкатели, имеющие на торцах тарелок лучевые задиры, износ или выкрашивание рабочей поверхности, замените новыми.
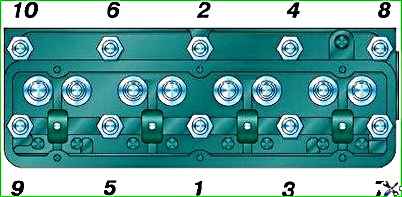
Подтяните гайки крепления головки блока цилиндров после обкатки автомобиля, через 1000 км пробега и после каждого снятия головки.
Затяжку гаек проводите только на холодном двигателе в последовательности, указанной на рис. 4 в два приема.
Окончательный момент затяжки 71,5–76,5 Нм (7,3–7,8 кгс·м).
По мере необходимости очищайте от нагара головку блока цилиндров, днища поршней и впускные клапаны.
На исправном неизношенном двигателе при применении высококачественного топлива и масла и соблюдении надлежащего теплового режима нагар бывает мал.
При износе двигателя, особенно его поршневых колец, в камеры сгорания попадает много масла и образуется большой слой нагара.
Наличие нагара определяют по усилению детонации, перегреву, падению мощности и увеличению расхода топлива.
При появлении этих признаков снимите головку блока цилиндров и удалите нагар при помощи металлических скребков и щеток.
Не допускайте попадания нагара в зазор между головками поршней и цилиндрами.
Если двигатель работал на этилированном бензине, то предварительно смочите нагар керосином, чтобы во время очистки исключить возможность вдыхания ядовитой пыли.