Los principales defectos de la culata que se pueden eliminar mediante reparación incluyen: deformación del plano de contacto con el bloque de cilindros, desgaste de asientos y guías de válvulas
La no rectitud del plano del cabezal en contacto con el bloque, al comprobarlo en la placa de control con una galga de espesores, no debe ser superior a 0,05 mm.
Las deformaciones menores del cabezal (hasta 0,3 mm) deben eliminarse raspando la superficie contra la pintura. Para deformaciones superiores a 0,3 mm, el cabezal debe rectificarse.
Restaurar la estanqueidad de la válvula y reemplazar los casquillos de la válvula
La violación de la estanqueidad de las válvulas con las holguras correctas entre los vástagos de las válvulas y los balancines, así como con el funcionamiento correcto del carburador y el sistema de encendido, se detecta mediante sonidos característicos del silenciador y el carburador.
El motor funciona de forma intermitente y no desarrolla toda su potencia.
Restaurar la estanqueidad de las válvulas rectificando los chaflanes de trabajo de las válvulas hasta sus asientos.
Si hay cavidades, ranuras de anillo o rayones en los chaflanes de trabajo de las válvulas y los asientos que no se pueden eliminar lapeando, esmerile los chaflanes y luego esmerile las válvulas hasta los asientos.
Reemplace las válvulas con cabezas deformadas.
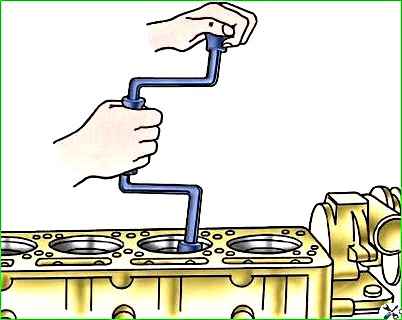
Limpiar los chaflanes de las válvulas con taladro neumático o eléctrico modelo 2213, 2447 GARO o manualmente mediante una férula.
Realice el rectificado mediante movimientos de rotación recíprocos, en los que la válvula gira en una dirección ligeramente más que en la otra.
Durante el período de rectificado, instale un resorte de liberación con una ligera elasticidad debajo de la válvula.
El diámetro interior del resorte debe ser de unos 10 mm.
El resorte debe levantar ligeramente la válvula por encima del asiento y, cuando se presiona ligeramente, la válvula debe asentarse en el asiento.
La herramienta se conecta a la válvula mediante una ventosa de goma, como se muestra en la Fig. 2.
Para una mejor adherencia de la ventosa a la válvula, sus superficies deben estar secas y limpias.
Para acelerar el pulido, utilice una pasta de pulido compuesta por una parte de micropolvo M20 y dos partes de aceite de motor.
Mezclar bien antes de usar.
Comience a pulir hasta que aparezca un chaflán mate uniforme en las superficies de trabajo del asiento y la placa de la válvula a lo largo de toda la circunferencia.
Hacia el final del lapeado, reduzca el contenido de micropolvo en la pasta de lapeado.
Termine de moler con un aceite limpio. En lugar de pasta para pulir, puedes utilizar polvo de esmeril 00 mezclado con aceite de motor.
Para rectificar los chaflanes de trabajo de las válvulas se recomienda utilizar rectificadoras tipo R-108 u OPR-1841 GARO.
Al mismo tiempo, sujete la varilla de la válvula en el cartucho de centrado del cabezal, instalado en un ángulo de 44°30' con respecto a la superficie de trabajo de la piedra de amolar.
Reducir el ángulo de inclinación del chaflán de trabajo de la cabeza de la válvula en 30' en comparación con el ángulo del chaflán de los asientos acelera el rodaje y mejora la estanqueidad de las válvulas.
Al rectificar, retire una cantidad mínima de metal del chaflán de la cabeza de la válvula.
La altura de la correa cilíndrica del chaflán de trabajo del cabezal de la válvula después del rectificado debe ser de al menos 0,7 mm, y la coaxialidad del chaflán de trabajo con respecto a la varilla debe estar dentro de 0,03 mm de las lecturas totales del indicador.
El descentramiento del vástago de la válvula no supera los 0,02 mm. Reemplace las válvulas con gran descentramiento por otras nuevas.
No vuelva a rectificar los vástagos de las válvulas a un tamaño más pequeño, ya que esto requerirá fabricar nuevos retenedores de resortes de válvulas.
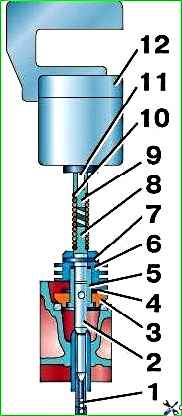
Afilar los chaflanes de los asientos en un ángulo de 45° coaxialmente con el orificio del casquillo. El ancho del chaflán debe ser de 1,6 a 2,4 mm.
Para rectificar asientos, se recomienda utilizar el dispositivo que se muestra en la Fig. 2.
Muela el asiento sin pasta de lapear ni aceite hasta que la piedra llegue a toda la superficie de trabajo.
Después del procesamiento aproximado, cambie la piedra por una de grano fino y termine de pulir la silla.
El descentramiento del chaflán en relación con el eje del orificio del manguito de la válvula no debe exceder los 0,03 mm.
Reemplace los asientos desgastados por otros nuevos.
Los asientos de válvula con un diámetro exterior mayor que el diámetro nominal en 0,25 mm se suministran como repuestos.
Retire los asientos desgastados de la cabecera utilizando un avellanador.
Después de eliminar el sed Taladré los casquillos en la cabeza para la válvula de escape hasta un diámetro de 38,75+0,025 mm y para la válvula de admisión hasta un diámetro de 49,25+0,25 mm.
Antes de presionar los asientos, calentar la culata a una temperatura de 170°C y enfriar los asientos con hielo seco.
Realice el prensado rápidamente, sin permitir que los asientos se calienten. La cabeza enfriada cubre firmemente los sillines.
Para aumentar la resistencia de los asientos, sellelos a lo largo del diámetro exterior utilizando un mandril plano, asegurándose de que el chaflán del asiento esté lleno.
Luego muela hasta obtener las dimensiones y vueltas requeridas.
Si el desgaste del vástago de la válvula y el casquillo guía es tan grande que el espacio en su unión supera los 0,25 mm, restablezca la estanqueidad de la válvula solo después de reemplazar la válvula y su casquillo.
Los repuestos se suministran con válvulas de tamaño nominal únicamente y casquillos guía con un diámetro interno reducido en 0,3 mm para su posterior escariado hasta el tamaño final después de presionar en la culata.
Extender los casquillos prensados hasta un diámetro de 9+0,022 mm.
El vástago de la válvula de admisión tiene un diámetro de 9 –0,050 –0,075 mm, la válvula de escape tiene un diámetro de 9 –0,075 –0,095 mm, por lo tanto, los espacios entre los vástagos y casquillos de las válvulas de admisión y escape deben ser de 0,050–0,097 mm y 0,075–0,117 mm, respectivamente.
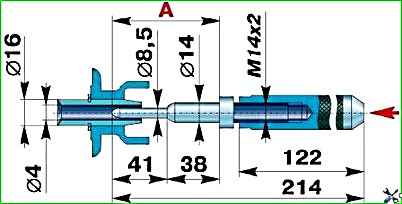
Presione los casquillos guía desgastados para sacarlos de la culata utilizando el punzón que se muestra en la Fig. 3.
Presione el nuevo casquillo desde el lado del balancín usando el mismo punzón hasta que se detenga en el anillo de retención del casquillo.
En este caso, al igual que cuando se presionan los asientos de las válvulas, calentar la culata a una temperatura de 170°C y enfriar el manguito con hielo seco.
Después de reemplazar los casquillos de las válvulas, esmerile los asientos (centrados en los orificios de los casquillos) y luego esmerile las válvulas hasta ellos.
Después de pulir los asientos y las válvulas, enjuagar bien y soplar con aire comprimido todos los canales y lugares por donde pueda entrar abrasivo.
Los casquillos de válvula son metal-cerámicos, porosos.
Después de terminar y lavar, satúrelos con aceite. Para ello, inserte una mecha de fieltro empapada en aceite para husillos en cada casquillo durante varias horas.
Antes del montaje, lubrique los vástagos de las válvulas con una fina capa de una mezcla preparada a partir de siete partes de una preparación de grafito coloidal de aceite y tres partes de aceite de motor.
Reemplazo de resortes de válvula
Los posibles fallos de funcionamiento de los resortes de las válvulas que aparecen durante el funcionamiento pueden ser: disminución de la elasticidad, roturas o grietas en las espiras.
Compruebe la elasticidad de los resortes de las válvulas al desmontar el mecanismo de la válvula.
La fuerza necesaria para comprimir un resorte de válvula nuevo a 46 mm de altura debe ser de 267 a 310 N (27,3 a 31,7 kgf), y hasta 37 mm, de 686 a 784 N (70 a 80 kgf).
Si la fuerza de compresión de un resorte de hasta 46 mm de altura es inferior a 235 N (24 kgf) y hasta 37 mm es inferior a 558,6 N (57 kgf), reemplace dicho resorte por uno nuevo.
Reemplazar los resortes con roturas, grietas y signos de corrosión por otros nuevos.
Reemplazo de empujadores
Los orificios guía en el bloque para los empujadores se desgastan ligeramente, por lo tanto, restablezca el juego nominal a este respecto reemplazando los empujadores desgastados.
Solo se suministran como repuestos empujadores de tamaño nominal.
Seleccione empujadores para orificios con una separación de 0,040 a 0,015 mm.
Los empujadores, según el tamaño del diámetro exterior, se dividen en dos grupos y están marcados con un sello: número 1 - para un diámetro de empujador de 25 -0,008 -0,015 mm y número 2 - para un diámetro de empujador de 25 -0,015 -0,022 milímetros.
Un empujador correctamente seleccionado, lubricado con aceite mineral líquido, debe descender suavemente por su propio peso hasta el alojamiento del bloque y girar fácilmente en él.
Empujadores que presenten raspaduras radiales en los extremos de las placas, desgaste o desconchado de la superficie de trabajo, sustituirlos por otros nuevos.
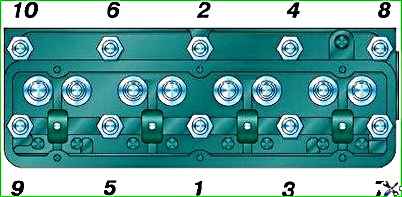
Apretar las tuercas de la culata después de circular en el vehículo, después de 1000 km y después de cada desmontaje de la culata.
Apriete las tuercas sólo con el motor frío en la secuencia que se muestra en la Fig. 4 en dos pasos.
Par de apriete final 71,5–76,5 Nm (7,3–7,8 kgf m).
Según sea necesario, limpie la culata, las coronas de los pistones y las válvulas de admisión de los depósitos de carbón.
En un motor reparable y en buen estado, utilizando combustible y aceite de alta calidad y observando Cuando se mantienen las condiciones térmicas adecuadas, los depósitos son pequeños.
Cuando el motor se desgasta, especialmente los aros del pistón, entra mucho aceite en las cámaras de combustión y se forma una gran capa de depósitos de carbón.
La presencia de depósitos de carbón está determinada por una mayor detonación, sobrecalentamiento, pérdida de potencia y aumento del consumo de combustible.
Si aparecen estos signos, retire la culata y elimine los depósitos de carbón utilizando raspadores y cepillos metálicos.
No permita que entren depósitos de carbón en el espacio entre las cabezas del pistón y los cilindros.
Si el motor funcionaba con gasolina con plomo, primero humedezca los depósitos de carbón con queroseno para evitar la posibilidad de inhalar polvo tóxico durante la limpieza.