До основних дефектів головки блоку циліндрів, які можна усунути ремонтом, відносяться: короблення площини прилягання до блоку циліндрів, знос сідел та напрямних втулок клапанів
Непрямолінійність площини головки, що торкається блоку, при перевірці її на контрольній плиті щупом не повинна бути більше 0,05 мм.
Незначне викривлення головки (до 0,3 мм) усувайте шабровкою площини по фарбі. При коробленнях, що перевищують 0,3 мм, головку потрібно шліфувати.
Відновлення герметичності клапанів та заміна втулок клапанів
Порушення герметичності клапанів при правильних зазорах між стрижнями клапанів і коромислами, а також при справній роботі карбюратора та системи запалення виявляється за характерними бавовнами з глушника та карбюратора.
Двигун працює з перебоями і не розвиває повної потужності.
Відновлення герметичності клапанів здійснюйте притиранням робочих фасок клапанів до їх сідл.
При наявності на робочих фасках клапанів і сідел раковин, кільцевих виробок або рисок, які не можна вивести притиранням, прошліфуйте фаски з наступним притиранням клапанів до сідл.
Клапани з пошкодженими головками замініть.
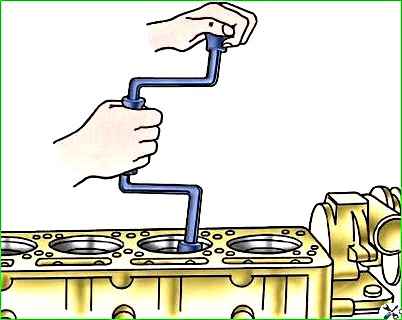
Фаски клапанів притирайте пневматичним або електричним дрилем моделі 2213, 2447 ГАРО або вручну за допомогою коловороту.
Притирання виконуйте поворотно-обертальними рухами, при яких клапан провертається в один бік дещо більше, ніж в інший.
На час притирання під клапан встановіть віджимну пружину з невеликою пружністю.
Внутрішній діаметр пружини має бути близько 10 мм.
Пружина повинна трохи піднімати клапан над сідлом, а при легкому натисканні клапан повинен сідати на сідло.
Зв'язок інструмента з клапаном здійснюється гумовим присосом, як показано на рис. 2.
Для кращого зчеплення присоса з клапаном їхньої поверхні повинні бути сухими та чистими.
Для прискорення притирання використовуйте пасту для притирання, складену з однієї частини мікропорошку марки М20 і двох частин моторного масла.
Зміш перед ретельно перемішайте.
Притирання ведіть до появи на робочих поверхнях сідла та тарілки клапана рівномірної матової фаски по всьому колу.
До кінця притирання зменшуйте вміст мікропорошку в притиральній пасті.
Закінчуйте притирання на чистому маслі. Замість притиральної пасти можна використовувати наждачний порошок № 00, змішаний із моторним маслом.
Для шліфування робочих фасок клапанів рекомендується застосовувати шліфувальні верстати типу Р-108 або ОПР-1841 ГАРО.
При цьому стрижень клапана затисніть у патроні бабки, що встановлюється під кутом 44°30' до робочої поверхні шліфувального каменю.
Зменшення на 30' кута нахилу робочої фаски головки клапана в порівнянні з кутом фаски сідел прискорює приробіток та покращує герметичність клапанів.
При шліфуванні знімайте з фаски головки клапана мінімальну кількість металу.
Висота циліндричного пояска робочої фаски головки клапана після шліфування має бути не менше 0,7 мм, а співвісність робочої фаски щодо стрижня в межах 0,03 мм загальних показань індикатора.
Биття стрижня клапана – не більше 0,02 мм. Клапани з великим биттям замініть на нові.
Не перешліфовуйте стрижні клапана на менший розмір, тому що виникне потреба у виготовленні нових сухариків тарілок клапанних пружин.
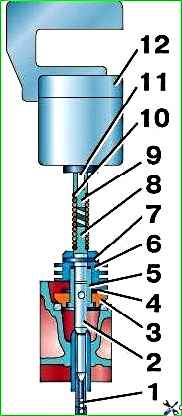
Фаски сідел шліфуйте під кутом 45° співвісно отвору у втулці. Ширина фаски має бути 1,6–2,4 мм.
Для шліфування сідел рекомендується застосовувати пристосування, зображене на рис. 2.
Сідло шліфуйте без пасти чи олії, доки камінь не буде обробляти всю робочу поверхню.
Після грубої обробки змініть камінь на дрібнозернистий і зробіть чистове шліфування сідла.
Биття фаски щодо осі отвору втулки клапана не повинно перевищувати 0,03 мм.
Зношені сідла замініть на нові.
У запасні частини поставляються сідла клапанів, що мають зовнішній діаметр більший за номінальний на 0,25 мм.
Зношені сідла витягайте з головки за допомогою зенкера.
Після вилучення сивел розточіть у головці гнізда для випускного клапана до діаметра 38,75+0,025 мм та для впускного клапана до діаметра 49,25+0,25 мм.
Перед запресуванням сідел нагрійте головку блоку циліндрів до температури 170°С, а сідла охолодіть сухим льодом.
Запресовку робіть швидко, не даючи можливості сідлам нагрітися. Охолола голівка щільно охоплює сідла.
Для збільшення міцності посадки сідел зачеканьте їх по зовнішньому діаметру за допомогою плоскої оправки, домагаючись заповнення фаски сідла.
Потім прошліфуйте до необхідних розмірів і притріть.
Якщо знос стрижня клапана та напрямної втулки настільки великий, що зазор у їх зчленуванні перевищує 0,25 мм, то герметичність клапана відновлюйте тільки після заміни клапана та його втулки.
У запасні частини поставляються клапани тільки номінальних розмірів, а напрямні втулки – з внутрішнім діаметром, зменшеним на 0,3 мм, для подальшого розгортання під остаточний розмір після запресування в головку блоку циліндрів.
Запресовані втулки розгортайте до діаметра 9+0,022 мм.
Стержень впускного клапана має діаметр 9 –0,050 –0,075 мм, випускного 9 –0,075 –0,095 мм, отже, зазори між стрижнями впускного та випускного клапанів та втулками повинні бути відповідно дорівнюють 0,050–0,097 мм та 0,077.
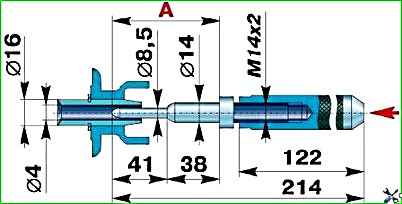
Зношені напрямні втулки випресовуйте з головки блоку циліндрів за допомогою вибивання, показаної на рис. 3.
Нову втулку запресовуйте з боку коромисел за допомогою того ж таки вибивання до упору в стопорне кільце, що є на втулці.
При цьому, як і при запресуванні сідел клапанів, голівку блоку циліндрів нагрійте до температури 170°С, а втулку охолодіть сухим льодом.
Після заміни втулок клапанів зробіть шліфування сідел (центруючись по отворах у втулках) і потім притріть до них клапани.
Після шліфування сідел та притирання клапанів усі канали та місця, куди міг би потрапити абразив, ретельно промийте та продуйте стиснутим повітрям.
Втулки клапанів – металокерамічні, пористі.
Після остаточної обробки та промивання просочіть їх маслом. Для цього в кожну втулку вставте на кілька годин просочений у веретеному маслі повстяний гніт.
Стержні клапанів перед збиранням змастіть тонким шаром суміші, приготовленої із семи частин масляного колоїдно-графітного препарату та трьох частин моторного масла.
Заміна клапанних пружин
Можливими несправностями клапанних пружин, що з'являються в процесі експлуатації, можуть бути: зменшення пружності, обломи або тріщини на витках.
Пружність клапанних пружин перевіряйте при розбиранні клапанного механізму.
Зусилля, необхідне для стиснення нової клапанної пружини до 46 мм за висотою, має бути 267–310 Н (27,3–31,7 кгс), а до 37 мм – 686–784 Н (70–80 кгс).
Якщо зусилля стиснення пружини до 46 мм за висотою менше 235 Н (24 кгс), а до 37 мм менше 558,6 Н (57 кгс), то таку пружину замініть на нову.
Пружини з обломами, тріщинами та слідами корозії замініть на нові.
Заміна штовхачів
Напрямні отвори в блоці під штовхачі зношуються незначно, тому номінальний зазор у цьому поєднанні відновлюйте заміною зношених штовхачів.
У запасні частини поставляються штовхачі лише номінального розміру.
Тлумачі підбирайте до отворів із зазором 0,040–0,015 мм.
Товкачі в залежності від розміру зовнішнього діаметра розбиті на дві групи і маркуються тавруванням: цифрою 1 – при діаметрі штовхача 25 –0,008 –0,015 мм та цифрою 2 – при діаметрі штовхача 25 –0,015 –0,022 мм.
Правильно підібраний штовхач, змащений рідкою мінеральною олією, повинен плавно опускатися під власним тягарем у гніздо блоку і легко прокручуватися в ньому.
Товкачі, що мають на торцях тарілок променеві задираки, знос або фарбування робочої поверхні, замініть новими.
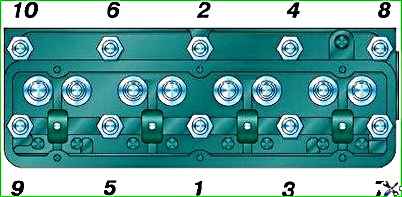
Підтягніть гайки кріплення головки блоку циліндрів після обкатки автомобіля, через 1000 км пробігу та після кожного зняття головки.
Затяжку гайок проводьте лише на холодному двигуні в послідовності, вказаній на рис. 4 у два прийоми.
Остаточний момент затягування 71,5–76,5 Нм (7,3–7,8 кгс·м).
При необхідності очищайте від нагару головку блоку циліндрів, днища поршнів та впускні клапани.
На справному незношеному двигуні при застосуванні високоякісного палива та олії та дотримуюсьдії належного теплового режиму нагар буває малий.
Під час зносу двигуна, особливо його поршневих кілець, в камери згоряння потрапляє багато масла і утворюється великий шар нагару.
Наявність нагару визначають щодо посилення детонації, перегріву, падіння потужності та збільшення витрати палива.
При появі цих ознак зніміть головку блоку циліндрів та видаліть нагар за допомогою металевих скребків та щіток.
Не допускайте потрапляння нагару в зазор між головками поршнів та циліндрами.
Якщо двигун працював на етильованому бензині, попередньо змочіть нагар гасом, щоб під час очищення виключити можливість вдихання отруйного пилу.