La culata es una pieza única de fundición gris y está fijada al bloque mediante espárragos atornillados al bloque.
Los espárragos son de acero al cromo-níquel y están tratados térmicamente. Para garantizar la disipación del calor, la culata cuenta con una camisa de agua que se comunica con la camisa del bloque. Para asegurar el suministro de combustible al inyector, existen orificios para las boquillas en la superficie lateral.
La culata contiene válvulas con resortes y sus piezas de fijación, balancines, ejes de balancines e inyectores.
Se insertan los asientos de las válvulas.
Los asientos de las válvulas de admisión están hechos de hierro fundido especial, y los de las válvulas de escape, de una aleación especial resistente al calor.
Los asientos se presionan en los alojamientos mediante tensión.
Los asientos de las válvulas y los casquillos guía metalocerámicos se procesan finalmente después de presionarlos en la culata.
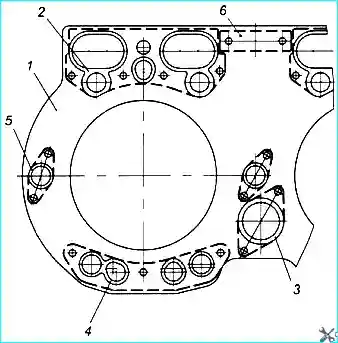
Las culatas instaladas en los motores presentan diferencias de diseño:
Las culatas de los motores YaMZ-236NE2 y BE2 pueden ser de tipo bloque para tres cilindros cada una o individuales:
- — Culata de bloque para tres cilindros cada una. La superficie de contacto está rectificada y se realizan ranuras anulares en la zona de sellado de las camisas de los cilindros.
La unión de la culata, el bloque y la camisa se sella con una junta que consta de una junta metálica para tres cilindros, que sella la junta de gas, y elementos de sellado de goma que sellan las cavidades de aceite, agua y biela.
Elementos de sellado de cinco tipos en una cantidad de 14 unidades. En la junta (Fig. 1).
Se instala una culata individual en cada cilindro, fijada al bloque mediante seis pernos de 209 mm y 248 mm de longitud.
Se inserta a presión en la culata una copa de boquilla de hierro fundido.
La copa está sellada en la parte superior con un anillo de goma.
La superficie de contacto en la zona de sellado de las camisas de cilindro presenta tres ranuras anulares.
La unión de la culata, el bloque y la camisa de cilindro (Fig. 2) está sellada con una junta compuesta por una junta metálica, que sella la junta de gas, y una junta de goma. Sellado de las cavidades de aceite, agua y bielas.
Las juntas metálicas y de goma se instalan en los pasadores del bloque.
La junta metálica está disponible en cuatro espesores (1,1 mm; 1,3 mm; 1,5 mm; 1,7 mm) y se selecciona individualmente durante el montaje del motor para lograr un funcionamiento óptimo en cada cilindro.
Se suministra una junta de 1,7 mm de espesor como repuesto.
Las culatas de los motores YaMZ-236N (B; NE; BE) son de tipo bloque, con tres cilindros cada una. Su estructura es básicamente similar a la del bloque anterior.
Desmonte la culata solo para solucionar problemas en las piezas del grupo cilindro-pistón, la junta de la culata, las válvulas o para sustituir la propia culata.
Desmonte la culata en el siguiente orden:
- 1. Vacíe el refrigerante del sistema de refrigeración del motor.
- 2. Desconecte todos los tubos de la culata y proteja sus cavidades internas del polvo y la suciedad.
- 3. Retire la tapa de la culata.
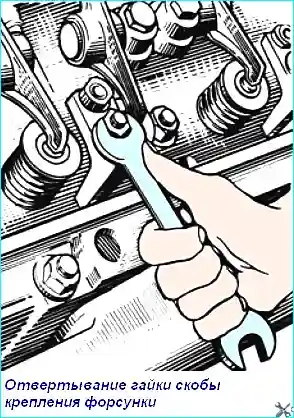
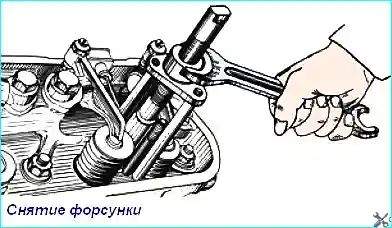
- 4. Desenrosque las tuercas del soporte de montaje del inyector (Fig. 3) y retire los inyectores (Fig. 4), protegiendo así el pulverizador de impactos y la obstrucción de los orificios.
- 5. Afloje las tuercas de montaje del eje del balancín, retire los ejes del balancín junto con los balancines y retire las varillas.
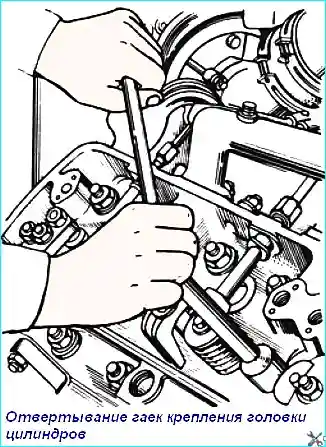
6. Afloje las tuercas de montaje de la culata (Fig. 5), siguiendo el orden inverso al de apriete (Fig. 6).
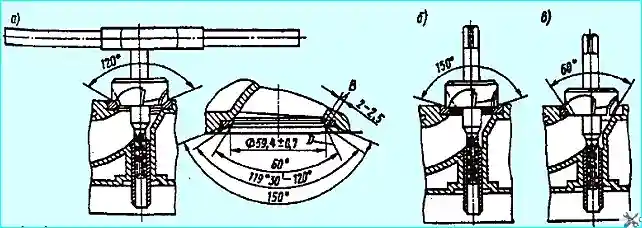
Desatornille las tuercas de fijación de cada culata en al menos tres pasos:
- 1 – paso - hasta 147...118 Nm (15...12 kgf/cm)
- 2 – paso - hasta 49...39 Nm (5...4 kgf/cm)
- 3 – paso - desenrosque las tuercas.
- 7. Retire la culata del motor e inspeccione su estado.
- 8. Si es necesario, retire con cuidado la junta de la culata.
- 9. Compruebe el estado de las camisas de los cilindros y cierre la tapa. Los orificios de los cilindros para protegerlos del polvo y la suciedad.
Instale la culata en el motor en orden inverso.
Antes de la instalación, limpie las superficies de contacto del bloque de cilindros, la brida de la camisa del cilindro y la culata con un paño limpio.
Se permite reutilizar la junta de culata con la misma culata solo si la posición de las camisas en el bloque de cilindros no cambia y no hay signos de fuga de gas ni daños en los bordes de la junta de gas.
Preste atención a la correcta instalación de la junta de culata en los pasadores y en los bordes de las juntas, es decir, en las bridas de las camisas del cilindro.

Apriete las tuercas de fijación de la culata en orden ascendente, como se muestra en la Fig. 7, a un par de 240-260 Nm (24-26 kgfm).
Después del primer apriete, repita la operación para comprobar el par de apriete necesario en cada tuerca, siguiendo la secuencia especificada.
No apriete las tuercas con un par superior al especificado, ya que esto provocará inevitablemente la destrucción de las piezas de la junta de gas.
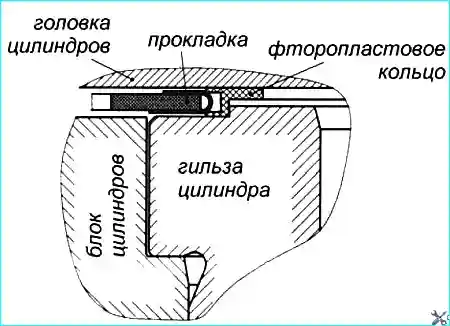
La unión de la culata, el bloque y la camisa (Fig. 8) está sellada con una junta de material sándwich con bordes para los orificios del cilindro y orificios para el paso del refrigerante.
Se insertan anillos de sellado fluoroplásticos partidos en los bordes de los orificios del cilindro.
La fijación al bloque se realiza mediante 16 espárragos con arandelas y tuercas.
Lapeado de las válvulas
Antes de desmontar las culatas, límpielas de aceite y depósitos de carbonilla y marque los números de serie de las válvulas en sus placas para que puedan instalarse en sus lugares durante el montaje.
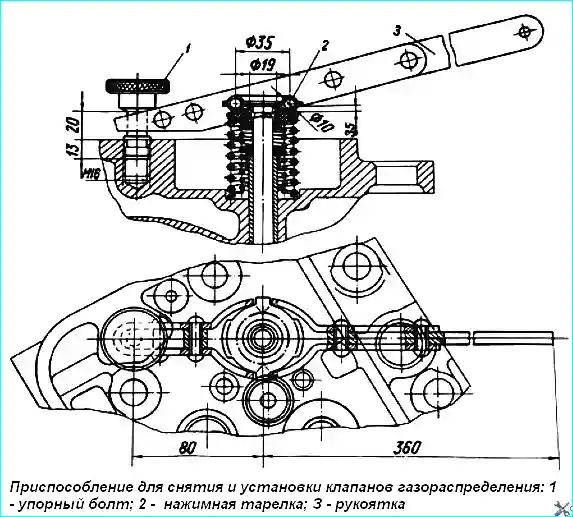
Para descomprimir las válvulas, es necesario instalar la culata sin inyectores, los balancines, los ejes de los balancines y los pernos de montaje de los ejes de los balancines con la superficie de contacto en la placa para proporcionar un tope para las válvulas.
Descomprima las válvulas utilizando el dispositivo que se muestra en la Fig. 9
Para ello, enrosque el perno de tope 1 del dispositivo en el orificio para el perno de montaje del eje de los balancines, instale la placa de presión 2 del dispositivo en la placa de los resortes de la válvula correspondiente y, presionando la manija 3 de la palanca del dispositivo, presione los resortes de la válvula, extraiga los craqueadores y retire todas las piezas del conjunto de válvulas.
Del mismo modo, descomprima secuencialmente Todas las demás válvulas y retire los resortes de válvula y las piezas asociadas. Gire la culata y retire las válvulas de los casquillos guía. Limpie a fondo las válvulas y los asientos para eliminar la suciedad, los depósitos de carbón y los depósitos de aceite. Lávelos con queroseno o una solución de limpieza especial, séquelos e inspecciónelos para determinar el grado de reparación. La estanqueidad de la válvula se puede restaurar mediante el lapeado solo si presenta desgaste leve y pequeñas cavidades en el chaflán de trabajo, y solo si la placa y el vástago no están deformados ni hay quemaduras locales en los chaflanes de la válvula y los asientos. Si existen tales defectos, el lapeado debe ir precedido del rectificado de los asientos y las válvulas o la sustitución de las piezas defectuosas. Para el lapeado de las válvulas, utilice una pasta de lapeado especial preparada mezclando a fondo tres partes (en volumen) de micropolvo de carburo de silicio verde con dos partes de aceite de motor y una parte de diésel. Combustible.
Antes de usar, mezcle bien la mezcla de pulido, ya que, en ausencia de mezclado mecánico, el micropolvo puede asentarse.
Instalar Atornille la culata a una placa o dispositivo especial con la superficie de contacto hacia arriba. Aplique una capa fina y uniforme de pasta de pulido al chaflán de la válvula, lubrique el vástago de la válvula con aceite de motor limpio e instálelo en la culata. Realice el pulido mediante movimientos de vaivén y rotación de las válvulas con un dispositivo especial o un taladro con ventosa. Presione la válvula con una fuerza de 20-30 N (2-3 kgf), gírela ⅓ de vuelta en una dirección y, aflojando la fuerza, ¼ de vuelta en la dirección opuesta. No realice el rectificado con movimientos circulares.
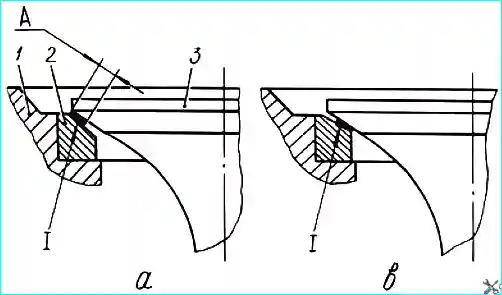
Levantando periódicamente la válvula y aplicando pasta al chaflán, continúe lapeando como se describe arriba hasta que aparezca una banda mate continua de ancho "A" de al menos 1,5 mm en los chaflanes de la válvula y el asiento (Fig. 10).
No se permiten roturas en la banda mate ni rayones transversales.
Con un lapeado correcto, la banda mate "A" en el chaflán y el asiento de la válvula debe comenzar en la base mayor del cono, como se muestra en la Figura 10.
Después del lapeado, lave bien las válvulas y la culata con queroseno o una solución de limpieza especial y séquelas.
Instale las válvulas, los resortes y sus piezas de fijación en la culata y seque las válvulas con el dispositivo que se muestra en la Fig. 9.
Compruebe la calidad del lapeado para detectar fugas entre la válvula y Limpie el asiento vertiendo queroseno o diésel, vertiéndolo alternativamente en los puertos de entrada y salida. Las válvulas bien lapeadas no deben dejar pasar queroseno ni diésel durante un minuto.
Se puede comprobar la calidad del lapeado con un lápiz. Para ello, trace de 10 a 15 líneas a intervalos iguales en el chaflán de la válvula limpia lapeada con un lápiz de grafito blando. A continuación, inserte con cuidado la válvula en el asiento y, presionando con fuerza contra él, gírela ¼ de vuelta.
Si la calidad del lapeado es buena, se deben borrar todas las líneas del chaflán de trabajo de la válvula. Si los resultados del control de calidad del lapeado no son satisfactorios, se debe continuar con este.
Los principales defectos de la culata son:
- - grietas, desgaste, arañazos y cavidades en los asientos de las válvulas de escape y admisión, rotura del sello de la copa del inyector;
- - desgaste de los orificios en los casquillos guía de las válvulas, aflojamiento del ajuste de los casquillos guía en la culata;
- - grietas en la superficie de contacto de la culata con el bloque de cilindros y deformación de esta superficie, así como flexión y aflojamiento del ajuste de los espárragos en la culata o daños en las roscas de los espárragos.
La culata se reemplaza si presenta grietas que atraviesan los orificios de los casquillos guía de las válvulas, los orificios de las copas de los inyectores y los asientos de las válvulas, y grietas en las paredes de la camisa de refrigeración en lugares inaccesibles para Reparación.
La presencia de grietas se determina mediante inspección visual, así como mediante la comprobación de fugas de las culatas con agua a una presión de 0,4 MPa (4 kgf/cm²).
La estanqueidad de la camisa de refrigeración de la culata se puede comprobar suministrando aire comprimido y sumergiendo la culata en agua.
Las grietas serán visibles por las burbujas de aire que escapan.
No se permiten grietas ni agujeros en la culata; solo se permiten pequeñas grietas en la superficie de contacto entre los orificios del inyector y las válvulas, que no afecten al chaflán de trabajo de la válvula de admisión ni alteren la estanqueidad.
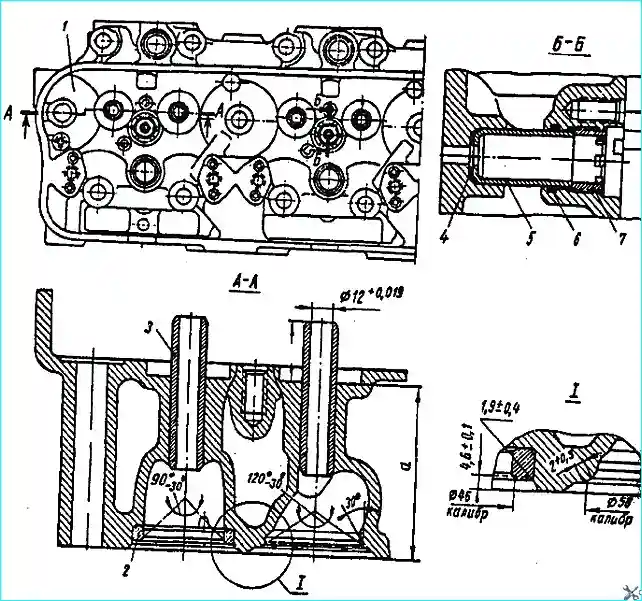
Si al comprobar la culata en busca de fugas se detecta una fuga en el sello de la copa del inyector, se debe apretar la tuerca de montaje de la copa. Si no se elimina la fuga, retire la copa y reemplace el anillo de sellado y la arandela, y si es necesario, la copa.
Para instalar la copa, coloque la arandela 4 en la parte inferior del casquillo, debajo de la copa de la boquilla (Fig. 11).
Instale el anillo de sellado de goma 6 en el casquillo, habiéndolo lubricado previamente con grasa. Introduzca la copa de la boquilla 5 con una referencia hasta el tope y enrosque la tuerca 7 de la copa de la boquilla con la cabeza (Fig. 12), apretando la tuerca con un par de 90-110 Nm (9-11 kgf.m).
A continuación, repita las pruebas de estanqueidad de la junta de la copa de la boquilla.
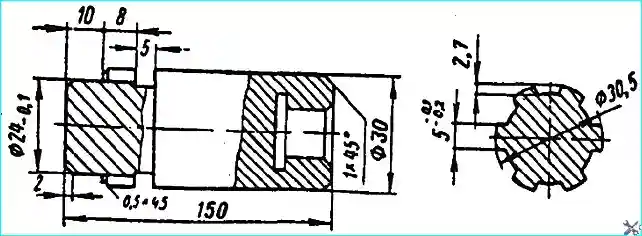
Se permite el montaje de culatas sin necesidad de reparación si:
- - la irregularidad de la superficie adyacente al bloque no supera los 0,1 mm en toda su longitud ni los 0,05 mm en una longitud de 100 mm;
- - si el ancho del chaflán de trabajo del asiento de la válvula de admisión es de 2,0-2,8 mm, el de la válvula de escape es de 1,5-2,3 mm;
- - la recesión de la válvula de admisión con respecto al plano inferior de la culata es de 0,1 mm. Más de 2,2 mm, y la salida, no más de 2,7 mm;
- - si el diámetro de las superficies internas de los casquillos de la guía de la válvula no supera los 12,060 mm y si no hay más de dos roscas desgastadas en la rosca de los espárragos.
La falta de planitud de la superficie adyacente al bloque se corrige mediante rectificado, asegurando la falta de planitud requerida y una altura de la culata al nervio anular de al menos 131,5 mm; tamaño nominal: 132-0,26 mm.
Si las roscas en los orificios de la culata están desgastadas o desgastadas, se cortan roscas de un tamaño de reparación o se instalan insertos.
Se cortan roscas en la culata para los espárragos de reparación de los siguientes tamaños: tubería de distribución de agua: M10 x 1,5T a una profundidad de 14 mm; tuberías de admisión y salida: M12 x 1.75T a una profundidad de 15 mm; soportes de inyector — M14x2T a una profundidad de 22 mm.
Al reparar orificios roscados mediante la instalación de insertos, taladre el orificio con la rosca defectuosa y corte una rosca para el inserto.
Luego, lubrique el inserto con plomo rojo o vidrio líquido y enrósquelo en el orificio roscado hasta el tope. Lime el extremo a ras del plano de la cabeza, perfore el inserto en tres puntos y calibre la rosca del inserto.
El orificio para el perno de montaje del inyector no se puede restaurar.
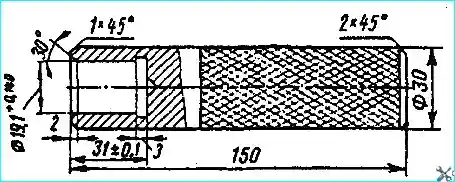
Si el diámetro interior de los casquillos de guía de válvula presenta un desgaste superior a 12,06 mm, se sustituyen por unos nuevos.
Con un mandril (Fig. 13), los casquillos de guía de válvula se introducen a presión en el orificio de la culata y se procesan con un escariador hasta obtener las dimensiones nominales de 12 ± 0,019 mm o las de reparación de 11,6 ± 0,019 mm.
Los casquillos de guía de válvula se introducen a presión con un ajuste de interferencia de 0,03-0,05 mm. Deben sobresalir de la superficie de apoyo del resorte de válvula (31 ± 0,5).
Antes de introducirlos a presión, los casquillos de guía se sumergen en aceite durante tres horas y la culata se calienta a una temperatura de 160-170 °C.
Si el desgaste del orificio de la culata debajo del casquillo de guía supera 19,03 mm, se instala un casquillo guía de reparación. Para ello, se escaria el orificio a un diámetro de 19,2 ± 0,023 mm y se introduce a presión el casquillo de reparación.
Los asientos de válvula se restauran según la naturaleza del defecto. Los chaflanes de trabajo de los asientos de válvula se procesan solo después de que se hayan restaurado los orificios en los casquillos guía de válvula.
Los arañazos en la superficie de trabajo de los asientos de las válvulas de admisión y escape, el desgaste y las abolladuras se eliminan mediante avellanado o rectificado del chaflán del asiento, garantizando al mismo tiempo la mínima eliminación de metal necesaria hasta obtener una superficie limpia del chaflán del asiento.
La recesión máxima permitida del nuevo plato de válvulas respecto al plano de la culata con los chaflanes del asiento de la culata restaurados es de 2,5 mm para la válvula de admisión y 3,0 mm para la de escape.
La herramienta de corte para restaurar el chaflán debe orientarse a lo largo del diámetro interior de la guía de válvula para garantizar la coaxialidad de la misma. El chaflán y el diámetro interior de la guía de la válvula deben estar dentro de 0,025 mm (excentricidad: 0,05 mm).
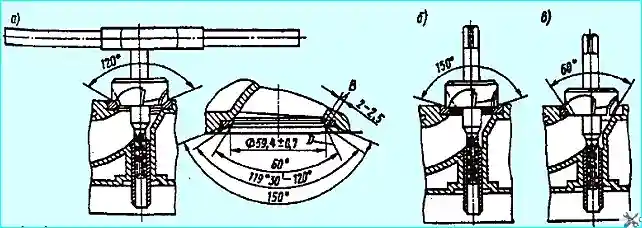
El mecanizado del chaflán del asiento de la válvula de admisión se realiza en el siguiente orden:
- - Fresar el chaflán de trabajo con un avellanador en un ángulo de 120° (Fig. 14, a) hasta obtener una superficie limpia y plana;
- - Fresar el borde inferior del chaflán de trabajo con un avellanador en un ángulo de 150° (Fig. 14, b). Manteniendo el ancho de chaflán requerido dentro del diámetro de 59,4 ± 0,7 mm;
- - Fresar el borde superior del chaflán con un avellanador en un ángulo de 60° (Fig. 14, c) hasta obtener un ancho de chaflán de 2,0-2,5 mm.
Procesar el chaflán del asiento de la válvula de entrada en el siguiente orden:
- - Fresar el chaflán de trabajo con un avellanador en un ángulo de 90° (Fig. 15, a) hasta obtener la limpieza requerida;
- - Fresar el borde inferior del chaflán con un avellanador en un ángulo de 150° (Fig. 15, b) para asegurar que el tamaño del chaflán de trabajo esté entre 1,5 y 2,0 mm.
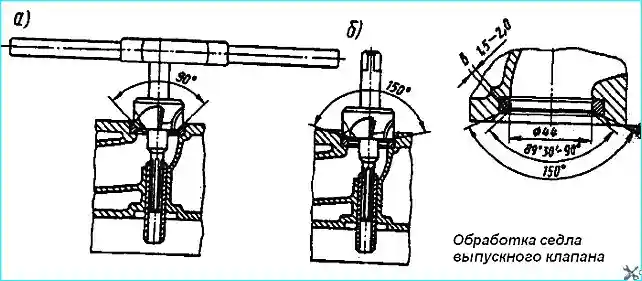
Los arañazos y el desgaste leve en los asientos de las válvulas se eliminan mediante el rectificado de los asientos y el posterior lapeado de las válvulas.
Si no es posible obtener un ancho de chaflán de trabajo en el asiento de la válvula de escape de 1,55 a 2,0 mm y en el de la válvula de admisión de 2,0 a 2,5 mm, así como si se presentan quemaduras, grietas, cavidades u otros defectos que no se puedan eliminar mediante el procesamiento, se sustituyen los asientos.
El asiento de reparación de la válvula de admisión está hecho de hierro fundido, cuya composición química es similar a la del hierro fundido de la culata. La válvula de escape está fabricada en fundición especial. La dureza de la pieza fundida es de HRC 50-60.
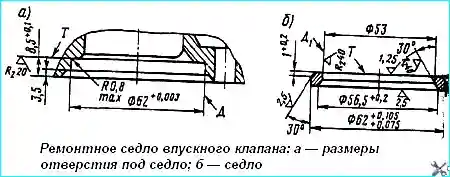
La ranura para el asiento de reparación en la culata se taladra con una taladradora radial. El mecanizado de la culata para el asiento de reparación de la válvula de admisión, las dimensiones del asiento y el mecanizado del chaflán del asiento en conjunto con la culata se muestran en la Fig. 16.
Después del taladrado, la excentricidad de la superficie "D" con respecto al orificio para el casquillo de la válvula no debe ser superior a 0,1 mm. La no perpendicularidad de la La distancia entre la cara frontal "T" y la superficie "D" no debe exceder los 0,03 mm en los extremos.
Al presionar un asiento nuevo, la culata se calienta en agua hirviendo a 90 °C y se mantiene a esta temperatura durante al menos 3 minutos.
Presione el asiento con ligeros golpes de martillo a través de un espaciador de cobre o latón, asegurando una interferencia de al menos 0,02 mm.
El ajuste del asiento a la culata se comprueba con una galga de espesores. Una galga de espesores con un grosor de 0,05 mm no debe pasar.
Después de presionar, los asientos de las válvulas se procesan utilizando la tecnología descrita anteriormente, lo que garantiza las dimensiones geométricas requeridas del chaflán de trabajo de las válvulas.
Las válvulas de la culata del motor están hechas de diversos materiales.
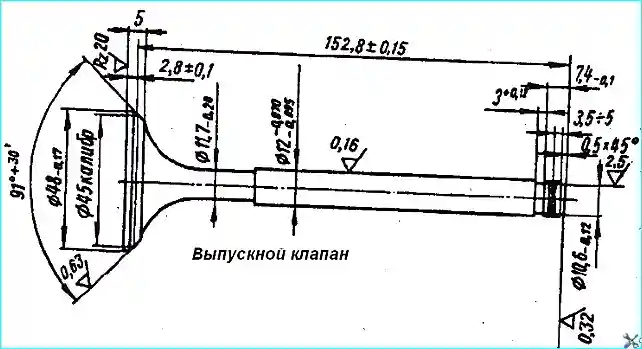
El extremo del vástago de la válvula de escape (Fig. 17) está fabricado en acero 40ХН, y la cabeza con el vástago está fabricada en acero 4Х14Н14В2М. La válvula está templada y revenida a una dureza de cabeza de HRC25-З0 y una dureza de extremo de vástago de HRC 50-57.
La válvula de admisión está fabricada en acero 4Х10СМ2 y tratada térmicamente a una dureza de HRC З5-40, y el extremo a una dureza de HRC 50-57, con una profundidad de 2-3 mm.
Los principales defectos de las válvulas son el desgaste o Quemaduras del chaflán de trabajo, flexión o desgaste del vástago a lo largo del diámetro, así como desgaste del extremo del vástago de la válvula.
Para eliminar el desgaste o la quema del chaflán de trabajo, este se rectifica limpiamente hasta una rugosidad de 0,63 μm. En este caso, la altura de la parte cilíndrica de la culata debe ser de al menos 0,5 mm; si la altura es inferior a 0,5 mm, la válvula se rechaza.
El chaflán de la válvula de escape se rectifica a un ángulo de 45° y el de la válvula de admisión a un ángulo de 60°.
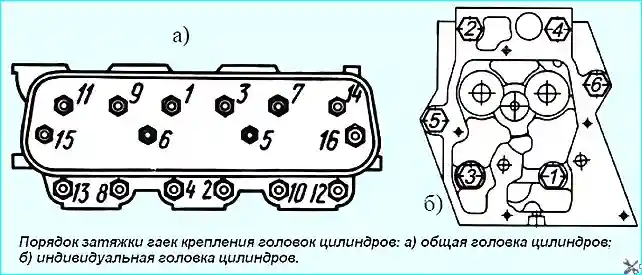
El chaflán de trabajo rectificado de la válvula de escape debe tener los siguientes parámetros:
- - El espesor de la banda cilíndrica de la placa no debe ser inferior a 1,0 mm, ángulo de 91-92°, rugosidad superficial de 0,63 μm;
- - El descentramiento de la superficie de trabajo del chaflán con respecto al vástago no debe ser superior a 0,03 mm; y, por consiguiente, para la válvula de admisión: El espesor de la banda cilíndrica de la placa no debe ser inferior a 0,75 mm, ángulo de 121-122°, rugosidad superficial de 1,25 μm;
- - El descentramiento del chaflán con respecto al vástago no debe ser superior a 0,03 mm.
Normalmente, antes de rectificar la válvula, se comprueba si el vástago está doblado y, si es necesario, se endereza.
Para comprobar si está doblado, el vástago de la válvula se coloca sobre los prismas indicadores y se comprueba la no linealidad de la generatriz del vástago de la válvula, que no debe ser superior a 0,01 mm, y el descentramiento del chaflán de trabajo con respecto a la generatriz no debe ser superior a 0,03 mm.
El enderezamiento se realiza con ligeros golpes de un mazo de madera o plomo.
Cuando los vástagos de las válvulas están desgastados, se rectifican a un tamaño de reparación con los siguientes diámetros: para la admisión: 11,8-0,030 mm o 11,6-0,030 mm, y para el escape: 11,8-0,095 mm o 11,6-0,070 mm.
Al rectificar en una máquina de ranurado sin centro utilizando En el método de inmersión, es necesario profundizar posteriormente la ranura anular para los crackers hasta un diámetro de 10,1-0,12 mm.
Al rectificar en una rectificadora cilíndrica, la válvula se inserta de extremo en un mandril con un orificio cilíndrico y se presiona con el centro desde el lateral de la cabeza de la válvula.
Definición La herramienta con superficie cónica se fija en el husillo de la máquina. Tras el rectificado, el vástago se pule hasta una rugosidad de 0,16 µm. La ovalidad y la conicidad de la superficie de generación del vástago no pueden superar los 0,01 mm. Los vástagos de válvula desgastados se restauran mediante estañado y rectificado posterior hasta su diámetro nominal: válvula de escape: 12-0,070 mm y válvula de admisión: 12-0,030 mm. Se rechazan los vástagos de válvula con un diámetro de desgaste inferior a 11,45 mm. El extremo desgastado del vástago de la válvula se rectifica y pule hasta una rugosidad de 0,32 µm, seguido de un biselado de 0,45 x 45°. Si la distancia desde la ranura anular hasta el extremo del vástago de la válvula es inferior a 7,2 mm, el extremo se suelda con un electrodo T-590 o un electrodo de alto carbono U8. Alambre.
A continuación, el extremo se rectifica, se templa a una dureza de HRC 50-57 y se pule. En este caso, es necesario mantener un diámetro de 7,4-0,1 mm y asegurar la perpendicularidad del extremo con respecto a la generatriz del vástago de la válvula; se permite una desviación máxima de 0,1 mm en una longitud de 100 mm (véase la Fig. 17).
Los resortes de válvula están fabricados en acero 50KhFA. Los resortes suelen presentar los siguientes defectos: pérdida de elasticidad, espiras rotas y grietas.
Si presentan espiras rotas o grietas, los resortes se rechazan.
Antes de instalar los resortes en el motor, se prueba su elasticidad en un dispositivo hidráulico que permite determinar su longitud en función de la carga.
El resorte exterior se considera apto para su instalación si su longitud en estado libre es de al menos 74 mm y, con una carga de 23,5 a 26,5 kgf, de al menos 56 mm.
El resorte interior en estado libre mide 63 mm y debe tener una longitud de 50 mm con una carga de 12,5 a 13,5 kgf.
El balancín de válvula (Fig. 19) está fabricado en acero 45 y el casquillo es de bronce Br. OCS 4-4-2.5.
La superficie de la punta del balancín está templada a una profundidad de 2-5 mm con una dureza de HRC 56-63.
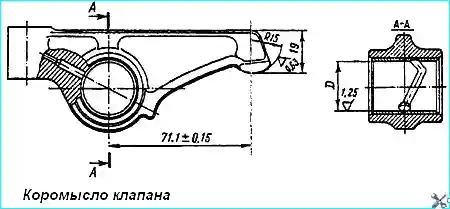
Los principales defectos del balancín son: desgaste del orificio del buje del eje, aflojamiento del ajuste del buje en el balancín y desgaste de la superficie frontal.
El balancín se reemplaza si se detecta una grieta o rotura.
Si el orificio del eje del balancín está desgastado hasta un diámetro de 25,15 mm, solo se reemplaza el buje. Además, se reemplaza el buje si su ajuste en el balancín está flojo.
El ajuste se comprueba mediante ligeros golpes con un punzón de cobre.
Antes de instalar un buje nuevo, verifique el diámetro del orificio del cubo del balancín, que no debe ser superior a 27,028 mm. El nuevo buje se presiona en el balancín con un ajuste de interferencia de al menos 0,7 mm.
Al instalar un buje nuevo, es necesario asegurarse de que los orificios del buje y del balancín coincidan, y que la unión del buje esté en la parte superior del orificio.
La ranura de aceite en el buje debe pasar a través del orificio alineado, mientras que los bordes de la ranura no deben sobresalir del orificio. El casquillo nuevo, una vez introducido a presión, debe estar empotrado 1 mm en el cuerpo del balancín a ambos lados.
El casquillo introducido a presión se procesa con un escariador hasta un diámetro de 25 +0,030 mm.
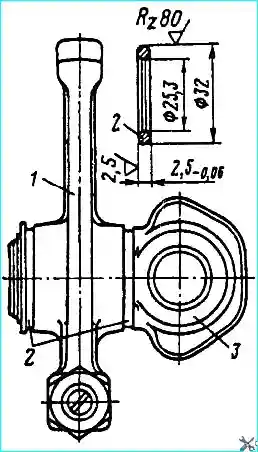
El desgaste de la superficie frontal del balancín se comprueba con una galga de espesores, utilizando una plantilla con un radio de esfera generadora de 15 -0,1 mm. Una galga de espesores de 0,2 mm de grosor no debe pasar entre la superficie generatriz de la punta y la plantilla.
El defecto especificado se elimina mediante el rectificado a un tamaño (véase la Fig. 19) de al menos 19 mm, asegurando un radio de 15 mm y una rugosidad de 0,63 µm, que se obtiene mediante pulido con pastas GOI.
El rectificado se realiza manualmente en una rectificadora de desbaste con una muela abrasiva, que debe estar revestida con un radio de 15 mm.
Si el rectificado de la punta del balancín no permite eliminar los rastros de desgaste sin violar el tamaño de 19 mm, la superficie se suelda con un electrodo T-590, que proporciona una dureza de HRC 50. El procesamiento posterior de la superficie de la punta es similar al descrito anteriormente.
Algunos motores están equipados con balancines con un ancho de cubo reducido de 34,9 a 0,14 mm. 30-0,14 mm, respectivamente, la longitud del buje del balancín se modifica de — 0,34-0,34 mm a 29-0,28 mm.
Por lo tanto, al instalar un balancín nuevo 1 (Fig. 19) en un eje 3 del diseño anterior, es necesario instalar un anillo espaciador 2 a ambos lados del cubo del balancín, hecho de cualquier acero, según las dimensiones que se muestran en la figura.
Al instalar un balancín antiguo en un eje de nuevo diseño, es necesario recortar su cubo uniformemente a cada lado en 2,5 mm; los extremos del cubo del balancín deben ser perpendiculares al eje del diámetro interior del buje con una precisión de 0,1 mm en un diámetro de 30 mm.
Un buje nuevo El buje ku se puede presionar y mecanizar junto con el balancín antiguo, si se cumplen los requisitos especificados; cuando se utiliza el buje antiguo con el balancín nuevo, se debe presionar y recortar en ambos lados.