Der Zylinderkopf besteht aus einem Gussteil aus Grauguss und ist über in den Block eingeschraubte Stehbolzen mit dem Block verbunden.
Die Stehbolzen bestehen aus Chrom-Nickel-Stahl und sind wärmebehandelt.
Zur Gewährleistung der Wärmeableitung verfügt der Zylinderkopf über einen Wassermantel, der mit dem Blockmantel kommuniziert. Um die Kraftstoffzufuhr zum Injektor sicherzustellen, befinden sich in der Seitenfläche Löcher für die Düsen.
Der Zylinderkopf enthält Ventile mit Federn und deren Befestigungsteilen, Kipphebel, Kipphebelwellen und Injektoren.
Die Ventilsitze werden eingesetzt.
Die Einlassventilsitze bestehen aus Spezialgusseisen, die Auslassventilsitze aus einer speziellen hitzebeständigen Legierung.
Die Sitze werden unter Spannung in die Buchsen gepresst.
Die Ventilsitze und Metallkeramik-Führungsbuchsen werden nach dem Einpressen in den Zylinderkopf abschließend bearbeitet.
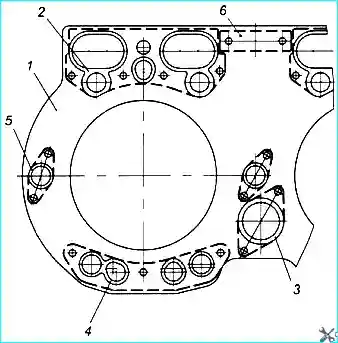
Die in den Motoren verbauten Zylinderköpfe weisen konstruktive Unterschiede auf:
Die Zylinderköpfe der YaMZ-236NE2,BE2-Motoren können Blockzylinder für jeweils drei Zylinder oder Einzelzylinder sein:
- — Blockzylinder für jeweils drei Zylinder. Die Passfläche ist geschliffen, und im Dichtbereich der Zylinderlaufbuchsen sind ringförmige Nuten eingearbeitet.
Die Verbindung von Zylinderkopf, Block und Laufbuchse wird mit einer Dichtung abgedichtet, die aus einer einzelnen Metalldichtung für drei Zylinder besteht, die die Gasverbindung abdichtet, und Gummidichtelementen, die die Öl-, Wasser- und Pleuelhohlräume abdichten.
Dichtelemente von fünf Typen, insgesamt 14 Stück. auf der Dichtung (Abb. 1).
Jeder Zylinder hat einen eigenen Zylinderkopf, der mit sechs 209 mm und 248 mm langen Bolzen am Block befestigt ist.
In den Zylinderkopf ist ein gusseiserner Düsenbecher eingepresst.
Der Becher ist oben mit einem Gummiring abgedichtet.
Die Dichtfläche im Dichtbereich der Zylinderlaufbuchsen weist drei ringförmige Nuten auf.
Die Verbindung zwischen Zylinderkopf, Block und Zylinderlaufbuchse (Abb. 2) ist mit einer Dichtung abgedichtet, die aus einer Metalldichtung für die Gasverbindung und einer Gummidichtung für die Öl-, Wasser- und Pleueldichtung besteht. Hohlräume.
Die Metall- und Gummidichtungen werden auf den Blockbolzen montiert.
Die Metalldichtung ist in vier Stärken (1,1 mm; 1,3 mm; 1,5 mm; 1,7 mm) erhältlich und wird bei der Motormontage individuell ausgewählt, um den optimalen Arbeitsablauf in jedem Zylinder zu gewährleisten.
Eine 1,7 mm dicke Dichtung wird als Ersatzteil geliefert.
Die Zylinderköpfe der YaMZ-236N; (B; NE; BE)-Motoren sind Blockmotoren mit jeweils drei Zylindern. Konstruktiv ähneln sie im Wesentlichen dem vorherigen Block.
Der Zylinderkopf darf nur zur Fehlerbehebung an der Zylinder-Kolben-Gruppe, der Zylinderkopfdichtung, den Ventilen oder zum Austausch des Kopfes selbst abmontiert werden.
Zylinderkopf in der folgenden Reihenfolge abmontieren:
- 1. Kühlmittel aus dem Motorkühlsystem ablassen.
- 2. Alle Leitungen vom Zylinderkopf trennen und deren Innenräume vor Staub und Schmutz schützen.
- 3. Zylinderkopfhaube demontieren.
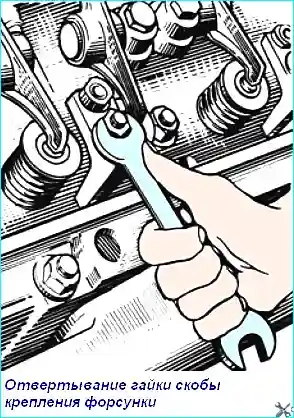
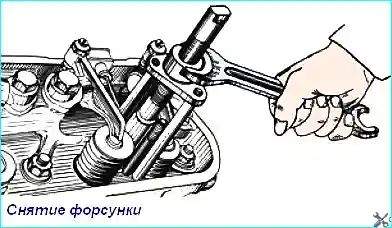
- 4. Die Muttern der Injektorhalterung lösen (Abb. 3) und die Injektoren ausbauen (Abb. 4). Dabei den Zerstäuber vor Stößen und Verstopfung der Löcher schützen.
- 5. Die Befestigungsmuttern der Kipphebelachse lösen, die Kipphebelachsen zusammen mit den Kipphebeln ausbauen und die Stangen ausbauen.
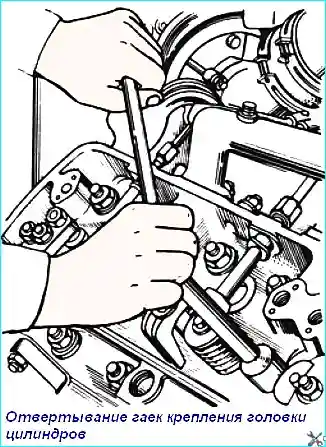
6. Lösen Sie die Zylinderkopf-Befestigungsmuttern (Abb. 5) in umgekehrter Reihenfolge wie beim Anziehen (Abb. 6).
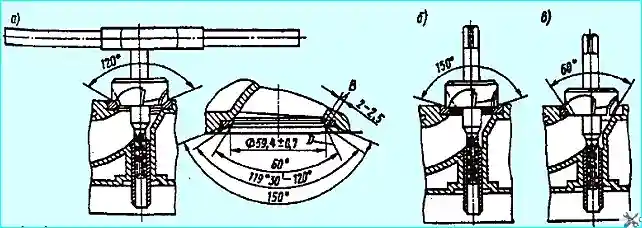
Die Befestigungsmuttern der einzelnen Zylinderköpfe in mindestens drei Schritten lösen:
- 1. Schritt: Bis zu 147…118 Nm (15…12 kgf/cm)
- 2. Schritt: Bis zu 49…39 Nm (5…4 kgf/cm)
- 3. Schritt: Muttern lösen.
- 7. Den Zylinderkopf vom Motor abmontieren und seinen Zustand prüfen.
- 8. Gegebenenfalls die Zylinderkopfdichtung vorsichtig entfernen.
- 9. Den Zustand der Zylinderlaufbuchsen prüfen und die Zylinderbohrungen verschließen, um sie vor Staub zu schützen. und Schmutz.
Montieren Sie den Zylinderkopf in umgekehrter Reihenfolge am Motor.
Wischen Sie vor dem Einbau die Passflächen des Zylinderblocks, den Flansch der Zylinderlaufbuchse und den Zylinderkopf mit einem sauberen Lappen ab.
Die Wiederverwendung der Zylinderkopfdichtung ist nur mit demselben Zylinderkopf zulässig, wenn die Position der Laufbuchsen im Zylinderblock unverändert bleibt und keine Anzeichen von Gasdurchbruch oder Zerstörung der Kanten der Gasfuge vorliegen.
Achten Sie auf die korrekte Montage der Zylinderkopfdichtung an den Bolzen und den Dichtungskanten – an den Flanschen der Zylinderlaufbuchsen.

Ziehen Sie die Zylinderkopfbefestigungsmuttern in aufsteigender Reihenfolge (siehe Abb. 7) mit einem Drehmoment von 240–260 Nm (24–26 kgfm) an.
Wiederholen Sie den Vorgang nach dem ersten Anziehen, um das erforderliche Drehmoment jeder Mutter zu überprüfen. Beachten Sie dabei die angegebene Reihenfolge.
Ziehen Sie die Muttern nicht mit einem höheren Drehmoment als angegeben an, da dies unweigerlich zur Zerstörung der Gasverbindungsteile führt.
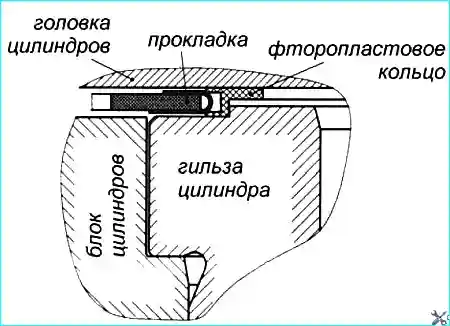
Die Verbindung von Zylinderkopf, Block und Zylinderlaufbuchse (Abb. 8) ist mit einer Dichtung aus Sandwichmaterial abgedichtet, die die Zylinderbohrungen und die Kühlmitteldurchlassöffnungen umschließt.
In die Zylinderbohrungen sind geteilte Fluorkunststoff-Dichtringe eingelegt.
Die Befestigung am Block erfolgt über 16 Stehbolzen mit Unterlegscheiben und Muttern.
Einläppen der Ventile
Bevor Sie die Zylinderköpfe zerlegen, reinigen Sie diese von Öl- und Kohlenstoffablagerungen und markieren Sie die Seriennummern der Ventile auf den Platten, damit sie bei der Montage an ihren Plätzen eingebaut werden können.
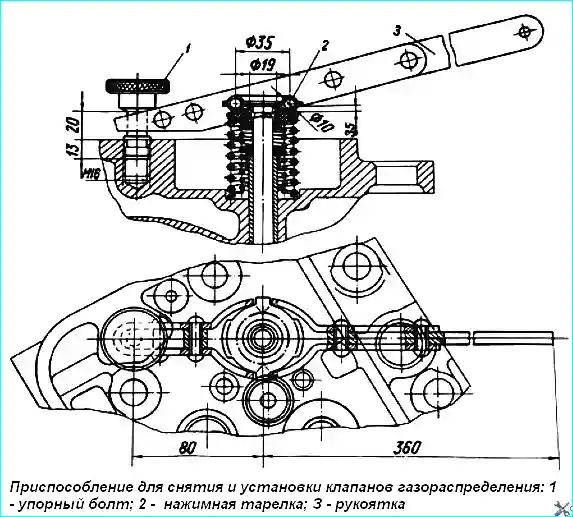
Zum Niederdrücken der Ventile muss der Zylinderkopf ohne Einspritzdüsen, Kipphebel, Kipphebelachsen und Kipphebelachsen-Befestigungsbolzen mit der Passfläche auf der Platte montiert werden, um einen Anschlag für die Ventile zu gewährleisten.
Die Ventile werden mit der in Abb. 9 gezeigten Vorrichtung niedergedrückt.
Dazu wird die Anschlagschraube 1 der Vorrichtung in die Bohrung für den Achsbolzen der Kipphebel gedreht. Die Druckplatte 2 der Vorrichtung wird auf der Federplatte des entsprechenden Ventils montiert. Durch Drücken des Griffs 3 des Hebels der Vorrichtung werden die Ventilfedern gedrückt, die Ventilknacker entfernt und alle Teile der Ventileinheit entfernt.
Auf die gleiche Weise werden nacheinander alle anderen Ventile entknackt und die Ventilfedern sowie die dazugehörigen Teile entfernt.
Den Zylinderkopf drehen und die Ventile von den Führungsbuchsen lösen.
Ventile und Ventilsitze gründlich von Schmutz, Kohlenstoffablagerungen und Ölrückständen reinigen, mit Kerosin oder einer speziellen Reinigungslösung waschen, trocknen und prüfen, um den Reparaturgrad zu bestimmen.
Die Dichtheit des Ventils kann nur bei geringem Verschleiß und kleinen Hohlräumen an der Arbeitsfase durch Läppen wiederhergestellt werden, sofern Platte und Stange nicht verzogen sind und keine lokalen Ausbrennungen an den Fasen von Ventil und Ventilsitzen vorhanden sind.
Bei solchen Defekten sollten vor dem Läppen die Ventilsitze und Ventile geschliffen oder die defekten Teile ausgetauscht werden.
Verwenden Sie zum Läppen der Ventile eine spezielle Läpppaste, die durch gründliches Mischen von drei Volumenteilen grünem Siliziumkarbid-Mikropulver mit zwei Teilen Motoröl und einem Teil Dieselkraftstoff hergestellt wird.
Die Läppmischung vor Gebrauch gründlich mischen, da ohne mechanisches Mischen Das Mikropulver kann sich absetzen.
Installieren Schrauben Sie den Zylinderkopf mit der Passfläche nach oben auf eine Platte oder eine spezielle Vorrichtung.
Tragen Sie eine dünne, gleichmäßige Schicht Läpppaste auf die Ventilfase auf, schmieren Sie den Ventilschaft mit sauberem Motoröl und setzen Sie ihn in den Zylinderkopf ein.
Läppen Sie die Ventile mit einer speziellen Vorrichtung oder einer Bohrmaschine mit Saugnapf, indem Sie hin- und hergehende Bewegungen ausführen.
Drücken Sie mit einer Kraft von 20–30 N (2–3 kgf) auf das Ventil, drehen Sie es ⅓ Umdrehung in die eine Richtung und dann, indem Sie die Kraft lösen, ¼ Umdrehung in die entgegengesetzte Richtung. Schleifen Sie nicht in kreisenden Bewegungen.
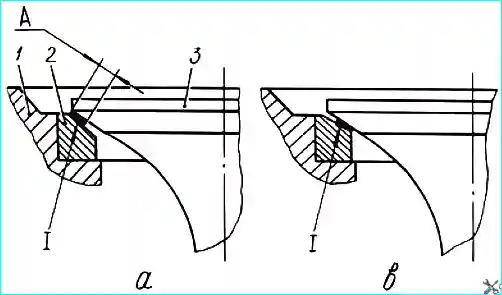
Heben Sie das Ventil regelmäßig an und geben Sie Paste auf die Fase. Setzen Sie den Läppvorgang wie oben beschrieben fort, bis sich an Ventil- und Ventilsitzfase ein durchgehender matter Streifen mit einer Breite „A“ von mindestens 1,5 mm bildet (Abb. 10).
Brüche im matten Streifen und Querkratzer sind nicht zulässig.
Bei korrektem Läppen sollte der matte Streifen „A“ an Ventilfase und Ventilsitz an der größeren Kegelbasis beginnen, wie in Abbildung 10 dargestellt.
Nach dem Läppen Ventile und Zylinderkopf gründlich mit Kerosin oder einer speziellen Reinigungslösung waschen und trocknen.
Montieren Sie Ventile, Federn und deren Befestigungsteile am Zylinderkopf und trocknen Sie die Ventile mit der in Abbildung 9 gezeigten Vorrichtung.
Überprüfen Sie die Qualität des Läppens auf Undichtigkeiten zwischen Ventil und Ventilsitz. Durch abwechselndes Einfüllen von Kerosin oder Dieselkraftstoff in die Einlass- und Auslassöffnungen. Gut geläppte Ventile sollten mindestens eine Minute lang kein Kerosin oder Dieselkraftstoff durchlassen.
Die Läppqualität kann mit einem Bleistift überprüft werden. Dazu werden mit einem weichen Graphitstift 10–15 Striche in gleichmäßigen Abständen über die Fase des geläppten, sauberen Ventils gezogen. Anschließend wird das Ventil vorsichtig in den Ventilsitz eingesetzt und mit festem Druck um eine Vierteldrehung gedreht.
Bei guter Läppqualität sollten alle Striche auf der Ventilfase entfernt werden. Wenn die Ergebnisse der Läppprüfung nicht zufriedenstellend sind, muss diese fortgesetzt werden.
Die wichtigsten Mängel am Zylinderkopf sind:
- – Risse, Verschleiß, Kratzer und Hohlräume an den Sitzen der Auslass- und Einlassventile, eine beschädigte Dichtung der Einspritzdüsen;
- – Verschleiß der Bohrungen in den Ventilführungsbuchsen, Lockerung der Passung der Führungsbuchsen im Zylinderkopf;
- – Risse an der Oberfläche des Zylinderkopfs, die mit dem Zylinderblock zusammenpasst, und Verformung dieser Oberfläche sowie Verbiegung und Lockerung der Passung der Stehbolzen am Zylinderkopf oder Beschädigung der Gewinde an den Stehbolzen.
Der Zylinderkopf wird ausgetauscht, wenn Risse in den Bohrungen der Ventilführungsbuchsen, den Bohrungen der Einspritzdüsen und den Sitzen der Ventilsitze sowie Risse an den Wänden des Kühlmantels an für den Motor unzugänglichen Stellen vorhanden sind. Reparatur.
Das Vorhandensein von Rissen wird durch Sichtprüfung sowie durch Dichtheitsprüfung der Zylinderköpfe mit Wasser unter einem Druck von 0,4 MPa (4 kgf/cm²) festgestellt.
Die Dichtheit des Zylinderkopfkühlmantels kann durch Zufuhr von Druckluft und Eintauchen des Kopfes in ein Wasserbad überprüft werden.
Risse sind an den austretenden Luftblasen erkennbar.
Risse und Löcher im Zylinderkopf sind nicht zulässig. Lediglich kleine Risse an der Passfläche zwischen den Löchern für die Einspritzdüse und die Ventile sind zulässig, sofern sie die Arbeitsfase des Einlassventils nicht beeinträchtigen und die Dichtheit nicht verletzen.
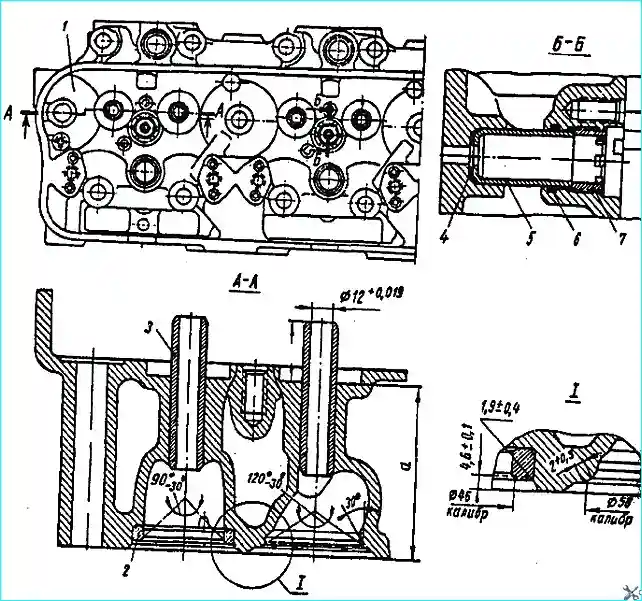
Wird bei der Dichtheitsprüfung des Zylinderkopfs ein Leck in der Dichtung des Einspritzdüsenbechers festgestellt, sollte die Befestigungsmutter des Bechers nachgezogen werden. Wenn die Undichtigkeit dadurch nicht behoben ist, entfernen Sie den Becher und ersetzen Sie Dichtring und Unterlegscheibe sowie gegebenenfalls den Becher.
Zum Einbau des Bechers legen Sie die Unterlegscheibe 4 auf den Boden der Aufnahme unter dem Düsenbecher (Abb. 11).
Setzen Sie den zuvor mit Fett gefetteten Gummidichtring 6 in die Aufnahme ein, setzen Sie den Düsenbecher 5 mit einer Referenz bis zum Anschlag ein und schrauben Sie die Mutter 7 des Düsenbechers mit dem Kopf (Abb. 12) mit einem Drehmoment von 90–110 Nm (9–11 kgf.m) fest.
Wiederholen Sie anschließend die Dichtheitsprüfung der Düsenbecherdichtung.
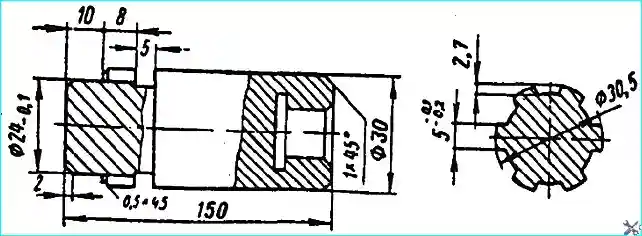
Zylinderköpfe dürfen ohne Reparatur montiert werden, wenn:
- - die Unebenheit der Oberfläche am Zylinderkopf beträgt nicht mehr als 0,1 mm über die gesamte Länge und nicht mehr als 0,05 mm über eine Länge von 100 mm;
- - die Breite der Arbeitsfase des Einlassventilsitzes 2,0–2,8 mm und die des Auslassventilsitzes 1,5–2,3 mm beträgt;
- - der Abstand des Einlassventils zur unteren Ebene des Zylinderkopfes nicht mehr als 2,2 mm beträgt und Auslass: maximal 2,7 mm;
- – wenn der Durchmesser der Innenflächen der Ventilführungsbuchsen maximal 12,060 mm beträgt und das Gewinde der Stehbolzen maximal zwei überdrehte Gewindegänge aufweist.
Unebenheiten der Oberfläche am Block werden durch Schleifen korrigiert. Dabei wird die erforderliche Unebenheit und ein Abstand vom Kopf zur Ringrippe von mindestens 131,5 mm (Nenngröße: 132–0,26 mm) sichergestellt.
Bei verschlissenen oder überdrehten Gewinden in den Zylinderkopfbohrungen werden Reparaturgewinde geschnitten oder Einsätze eingesetzt.
Im Zylinderkopf werden Gewinde für Reparaturstehbolzen folgender Größen geschnitten: Wasserverteilerrohr: M10 x 1,5T bis zu einer Tiefe von 14 mm; Einlass- und Auslassleitungen: M12 x 1,75T bis zu einer Tiefe von 15 mm; Injektor Halterungen — M14x2T bis zu einer Tiefe von 22 mm.
Bei der Reparatur von Gewindebohrungen durch den Einbau von Einsätzen bohren Sie die Bohrung mit dem defekten Gewinde auf und schneiden ein Gewinde für den Einsatz.
Anschließend schmieren Sie den Einsatz mit Mennige oder Flüssigglas und schrauben ihn bis zum Anschlag in die Gewindebohrung ein. Feilen Sie das Ende bündig mit der Kopfebene ab, lochen Sie den Einsatz an drei Punkten und kalibrieren Sie die Gewindebohrung des Einsatzes.
Die Bohrung für den Injektor-Befestigungsbolzen kann nicht wiederhergestellt werden.
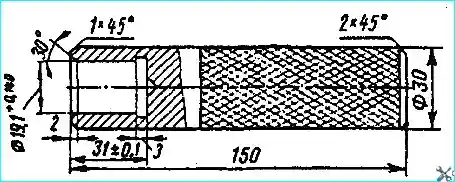
Ist der Innendurchmesser der Ventilführungsbuchsen um mehr als 12,06 mm abgenutzt, werden sie durch neue ersetzt.
Mithilfe eines Dorns (Abb. 13) werden die Ventilführungsbuchsen in die Zylinderkopfbohrung eingepresst und mit einer Reibahle auf das Nennmaß von 12 + 0,019 mm bzw. das Reparaturmaß von 11,6 + 0,019 mm bearbeitet.
Die Ventilführungsbuchsen werden mit einer Presspassung von 0,03–0,05 mm eingepresst. Sie sollten die Auflagefläche der Ventilfeder um (31 ± 0,5 mm) überragen.
Vor dem Einpressen werden die Führungsbuchsen drei Stunden in Öl eingeweicht, und der Zylinderkopf wird auf eine Temperatur von 160–170 °C erhitzt.
Wenn der Verschleiß der Zylinderkopfbohrung unter der Führungsbuchse mehr als 19,03 mm, wird eine Reparaturführungsbuchse eingebaut. Dazu wird die Bohrung auf einen Durchmesser von 19,2 + 0,023 mm aufgerieben und die Reparaturbuchse eingepresst.
Die Ventilsitze werden je nach Art des Defekts wiederhergestellt. Die Arbeitsfasen der Ventilsitze werden erst nach der Wiederherstellung der Bohrungen in den Ventilführungsbuchsen bearbeitet.
Kratzer auf der Arbeitsfläche der Einlass- und Auslassventilsitze, Verschleiß und Dellen werden durch Senken oder Schleifen der Sitzfasen beseitigt. Dabei wird der minimal erforderliche Metallabtrag sichergestellt, bis eine saubere Sitzfasenoberfläche entsteht.
Der maximale Abstand der neuen Ventilplatte von der Kopfebene mit wiederhergestellten Kopfsitzfasen beträgt 2,5 mm für das Einlassventil und 3,0 mm für das Auslassventil.
Das Schneidwerkzeug zum Wiederherstellen der Fase muss entlang des Innendurchmessers der Ventilführung ausgerichtet sein, um die Koaxialität der Die Fase und der Innendurchmesser der Ventilführung müssen innerhalb einer Toleranz von 0,025 mm liegen (Rundlauf 0,05 mm).
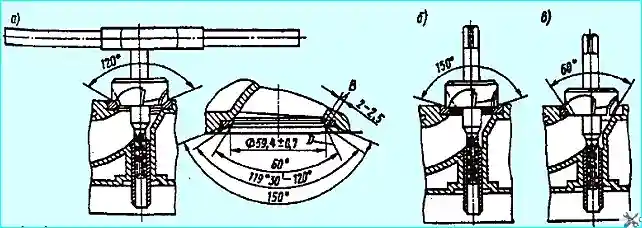
Die Bearbeitung der Fase des Einlassventilsitzes erfolgt in der folgenden Reihenfolge:
- – Fräsen der Arbeitsfase mit einem Senker im Winkel von 120° (Abb. 14, a), bis eine saubere, ebene Oberfläche entsteht;
- – Fräsen der Unterkante der Arbeitsfase mit einem Senker im Winkel von 150° (Abb. 14, b). Die erforderliche Fasenbreite muss innerhalb des Durchmessers von 59,4 + 0,7 mm liegen.
- – Fräsen Sie die Oberkante der Fase mit einem Senker im Winkel von 60° (Abb. 14, c), bis eine Fasenbreite von 2,0–2,5 mm erreicht ist.
Bearbeiten Sie die Fase des Einlassventilsitzes in der folgenden Reihenfolge:
- – Fräsen Sie die Arbeitsfase mit einem Senker im Winkel von 90° (Abb. 15, a), bis die gewünschte Reinheit erreicht ist.
- – Fräsen Sie die Unterkante der Fase mit einem Senker im Winkel von 150° (Abb. 15, b), um sicherzustellen, dass die Größe der Arbeitsfase innerhalb von 1,5–2,0 mm liegt.
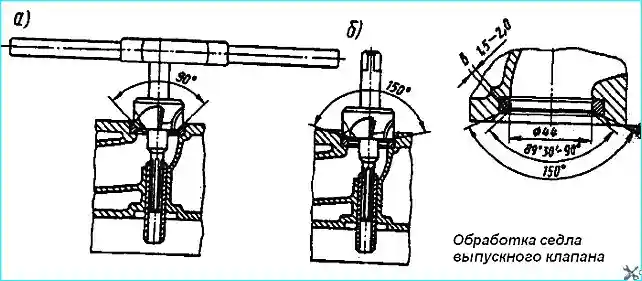
Kratzer und leichter Verschleiß an den Ventilsitzen werden durch Schleifen und anschließendes Läppen der Ventile beseitigt.
Wenn eine Arbeitsfasenbreite am Auslassventilsitz von 1,55–2,0 mm und am Einlassventilsitz von 2,0–2,5 mm nicht erreicht werden kann oder Ausbrennungen, Risse, Hohlräume oder andere Defekte vorliegen, die durch die Bearbeitung nicht behoben werden können, werden die Sitze ausgetauscht.
Der Reparatursitz des Einlassventils besteht aus Gusseisen, dessen chemische Zusammensetzung der des Gusseisens der Zylinderköpfe ähnelt. Das Auslassventil besteht aus Spezialgusseisen. Die Härte des Gussteils beträgt HRC 50–60.
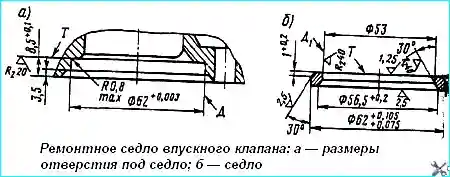
Die Nut für den Reparatursitz im Zylinderkopf wird auf einer Radialbohrmaschine gebohrt. Die Bearbeitung des Kopfes für den Reparatursitz des Einlassventils, die Sitzabmessungen und die Bearbeitung der Sitzfase im Zusammenbau mit dem Kopf sind in Abb. 16 dargestellt.
Nach dem Bohren sollte der Rundlauf der Fläche „D“ relativ zur Bohrung für die Ventilbuchse maximal 0,1 mm betragen. Die Nichtrechtwinkligkeit der Stirnfläche „T“ zur Fläche „D“ sollte 0,03 mm an den äußersten Punkten nicht überschreiten.
Beim Einpressen eines neuen Sitzes wird der Zylinderkopf in kochendem Wasser auf 90 °C erhitzt und mindestens 3 Minuten bei dieser Temperatur gehalten.
Der Sitz wird mit leichten Hammerschlägen durch ein Distanzstück aus Kupfer oder Messing eingepresst, wobei ein Übermaß von mindestens 0,02 mm eingehalten werden muss.
Die Passung des Sitzes zum Zylinderkopf wird mit einer Fühlerlehre geprüft. Eine Fühlerlehre mit einer Dicke von 0,05 mm sollte nicht durchgehen.
Nach dem Einpressen werden die Ventilsitze mit der oben beschriebenen Technologie bearbeitet, wodurch die erforderlichen geometrischen Abmessungen der Arbeitsfase der Ventile gewährleistet werden.
Die Ventile des Motorzylinderkopfes bestehen aus verschiedenen Materialien.
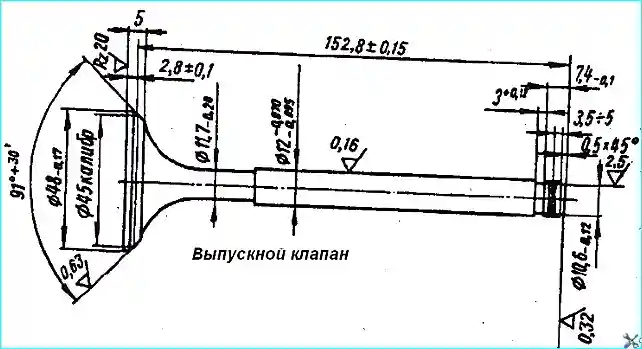
Das Ende des Auslassventilschafts (Abb. 17) besteht aus 40ХН-Stahl, der Ventilkopf mit Schaft aus 4Х14Н14В2М-Stahl. Das Ventil ist gehärtet und angelassen auf eine Kopfhärte von HRC 25-З0 und eine Schafthärte von HRC 50-57.
Das Einlassventil besteht aus 4Х10СМ2-Stahl und ist auf eine Härte von HRC З5-40, das Ventilkopfende auf eine Härte von HRC 50-57 bis zu einer Tiefe von 2-3 mm wärmebehandelt.
Die Hauptdefekte der Ventile sind Verschleiß oder Durchbrennen der Fase, Verbiegung oder Verschleiß des Schaftes entlang des Durchmessers sowie Verschleiß des Ventilschaftendes.
Um Verschleiß oder Ausbrennen der Arbeitsfase zu vermeiden, wird diese auf eine Rauheit von 0,63 μm sauber geschliffen. Dabei muss die Höhe des zylindrischen Teils des Kopfes mindestens 0,5 mm betragen. Liegt sie unter 0,5 mm, wird das Ventil aussortiert.
Die Fase des Auslassventils wird in einem Winkel von 45°, die des Einlassventils in einem Winkel von 60° geschliffen.
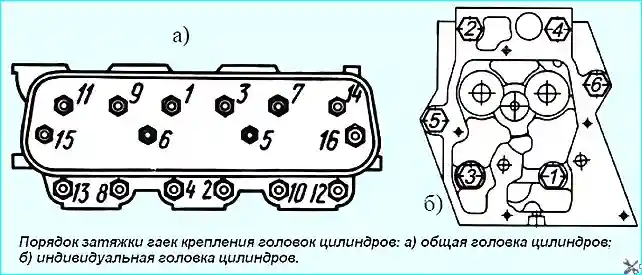
Die nachgeschliffene Arbeitsfase des Auslassventils muss folgende Parameter aufweisen:
- - Dicke der zylindrischen Mantelfläche der Platte mindestens 1,0 mm, Winkel 91–92°, Oberflächenrauheit 0,63 μm;
- - Rundlaufabweichung der Arbeitsfläche der Fase relativ zur Stange höchstens 0,03 mm. Für das Einlassventil gilt: Dicke der zylindrischen Mantelfläche der Platte mindestens 0,75 mm, Winkel 121–122°, Oberflächenrauheit mindestens 1,25 μm;
- - Rundlaufabweichung der Arbeitsfase relativ zur Stange höchstens 0,03 mm.
Normalerweise wird vor dem Schleifen des Ventils der Ventilschaft auf Biegung geprüft und gegebenenfalls gerichtet.
Zur Überprüfung auf Verbiegungen wird der Ventilschaft auf die Prüfprismen gelegt und die Nichtlinearität der Ventilschafterzeugenden geprüft. Diese sollte maximal 0,01 mm betragen. Der Rundlauf der Arbeitsfase relativ zur Erzeugenden sollte maximal 0,03 mm betragen.
Das Richten erfolgt mit leichten Schlägen eines Holz- oder Bleihammers.
Bei Verschleiß der Ventilschäfte werden diese auf folgende Durchmesser geschliffen: Einlass: 11,8–0,030 mm bzw. 11,6–0,030 mm und Auslass: 11,8–0,095 mm bzw. 11,6–0,070 mm.
Beim Schleifen auf einer spitzenlosen Keilwellenmaschine im Einstechverfahren ist es erforderlich, die Ringnut für die Cracker anschließend auf einen Durchmesser von 10,1–0,12 mm.
Beim Schleifen auf einer Rundschleifmaschine wird das Ventil stirnseitig in einen Dorn mit zylindrischer Bohrung eingesetzt und mit der Mitte seitlich am Ventilteller angedrückt.
Definition Das Werkzeug mit konischer Oberfläche wird in der Maschinenspindel fixiert. Nach dem Schleifen wird der Schaft auf eine Rauheit von 0,16 µm poliert.
Die Ovalität und Konizität der Schaftmantelfläche dürfen maximal 0,01 mm betragen.
Verschlissene Ventilschäfte werden durch Verzinnen und anschließendes Schleifen auf den Nenndurchmesser wiederhergestellt: Auslassventil: 12–0,070 mm, Einlassventil: 12–0,030 mm.
Ventilschäfte mit einem Verschleißdurchmesser von weniger als 11,45 mm werden aussortiert.
Das verschlissene Ende des Ventilschafts wird geschliffen und auf eine Rauheit von 0,32 µm poliert, anschließend wird eine Anfasung von 0,45 x 45° vorgenommen.
Wenn der Abstand von der Ringnut zum Ventilschaftende weniger als 7,2 mm beträgt, wird das Ende mit einer T-590-Elektrode oder einer U8-Hochkohlenstoffelektrode verschweißt. Draht.
Anschließend wird das Ende geschliffen, auf eine Härte von HRC 50–57 gehärtet und poliert. Dabei ist ein Maß von 7,4–0,1 mm einzuhalten und die Rechtwinkligkeit des Endes zur Mantellinie des Ventilschafts sicherzustellen; eine Abweichung von maximal 0,1 mm auf einer Länge von 100 mm ist zulässig (siehe Abb. 17).
Die Ventilfedern bestehen aus 50-KhFA-Stahl. Federn weisen üblicherweise folgende Mängel auf: Elastizitätsverlust, Windungsbrüche und Risse.
Bei Windungsbrüchen oder Rissen werden die Federn aussortiert.
Vor dem Einbau der Federn in den Motor werden diese mit einem hydraulischen Gerät auf Elastizität geprüft. Dadurch lässt sich die Federlänge in Abhängigkeit von der Belastung bestimmen.
Die äußere Feder gilt als einbaufähig, wenn ihre Länge im unbelasteten Zustand mindestens 74 mm und bei einer Belastung von 23,5–26,5 kgf mindestens 56 mm beträgt.
Die innere Feder ist im unbelasteten Zustand 63 mm lang und sollte bei einer Belastung von 12,5–13,5 kgf eine Länge von 50 mm aufweisen.
Der Ventilkipphebel (Abb. 19) besteht aus Stahl 45, die Buchse aus Bronze Br. OCS 4-4-2.5.
Die Oberfläche der Kipphebelnase ist 2–5 mm tief gehärtet und weist eine Härte von HRC 56–63 auf.
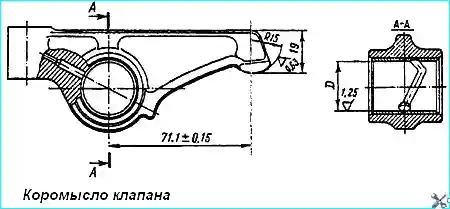
Die Hauptdefekte am Kipphebel sind: Verschleiß der Bohrung in der Buchse für die Kipphebelachse, Lockerung des Buchsensitzes im Kipphebel und Verschleiß der Nasenfläche.
Der Kipphebel wird ausgetauscht, wenn ein Riss oder Bruch festgestellt wird.
Ist die Bohrung für die Kipphebelachse bis auf einen Durchmesser von 25,15 mm verschlissen, wird nur die Buchse ausgetauscht. Zusätzlich wird die Buchse ausgetauscht, wenn ihr Sitz im Kipphebel locker ist.
Der Sitz wird durch leichte Schläge mit einem Kupferdorn überprüft.
Vor dem Einbau einer neuen Buchse ist der Durchmesser der Kipphebelnabenbohrung zu prüfen. Dieser sollte nicht größer als 27,028 mm sein. Die neue Buchse wird mit einer Presspassung von mindestens 0,7 mm in den Kipphebel eingepresst.
Beim Einbau einer neuen Buchse ist darauf zu achten, dass die Bohrungen in Buchse und Kipphebel deckungsgleich sind und die Stoßstelle der Buchse oben in der Bohrung liegt.
Die Ölnut in der Buchse sollte durch die fluchtende Bohrung verlaufen, wobei die Nutränder nicht über die Bohrung hinausragen dürfen. Die eingepresste neue Buchse sollte beidseitig 1 mm im Kipphebelkörper versenkt sein.
Die eingepresste Buchse wird mit einer Reibahle auf einen Durchmesser von 25 + 0,030 mm bearbeitet.
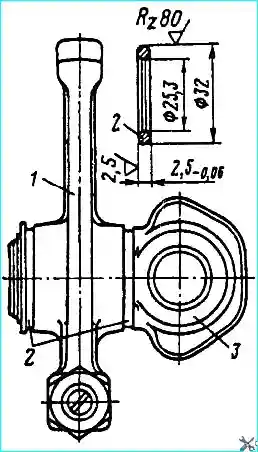
Der Verschleiß der Kipphebelnase wird mit einer Fühlerlehre und einer Schablone mit einem Radius der erzeugenden Kugel von 15 -0,1 mm geprüft. Eine 0,2 mm dicke Fühlerlehre darf nicht zwischen der Mantelfläche der Nase und der Schablone hindurchreichen.
Der angegebene Defekt wird durch Schleifen auf eine Größe (siehe Abb. 19) von mindestens 19 mm behoben. Dabei wird ein Radius von 15 mm und eine Rauheit von 0,63 µm sichergestellt, die durch Polieren mit GOI-Pasten erreicht wird.
Das Schleifen erfolgt manuell auf einer Schruppschleifmaschine mit einer Schleifscheibe, die auf einen Radius von 15 mm abgerichtet sein muss.
Wenn das Schleifen der Kipphebelnase keine Verschleißspuren entfernt, ohne die Größe von 19 mm zu überschreiten, wird die Oberfläche mit einer T-590-Elektrode geschweißt, die eine Härte von HRC 50 erreicht. Die weitere Bearbeitung der Nasenoberfläche erfolgt analog zu der oben beschriebenen.
Einige Motoren sind mit Kipphebeln mit einer reduzierten Nabenbreite von 34,9-0,14 mm ausgestattet, um 30-0,14 mm, die Länge der Kipphebelbuchse ändert sich von — 0,34-0,34 mm auf 29-0,28 mm.
Beim Einbau eines neuen Kipphebels 1 (Abb. 19) auf eine Achse 3 alter Bauart muss daher auf beiden Seiten der Kipphebelnabe je ein Distanzring 2 aus beliebigem Stahl entsprechend den in der Abbildung angegebenen Abmessungen eingebaut werden.
Beim Einbau eines alten Kipphebels auf eine Achse neuer Bauart muss die Nabe auf jeder Seite gleichmäßig um 2,5 mm gekürzt werden. Die Enden der Kipphebelnabe müssen senkrecht zur Achse des Innendurchmessers der Buchse stehen, mit einer Genauigkeit von 0,1 mm bei einem Durchmesser von 30 mm.
Eine neue Buchse ku kann zusammen mit dem alten Kipphebel eingepresst und bearbeitet werden, wenn die angegebenen Anforderungen erfüllt sind; bei Verwendung der alten Buchse mit dem neuen Kipphebel sollte diese beidseitig eingepresst und bearbeitet werden.