Requirements for parts and assemblies of the D-245 diesel engine
The cylinder block is the main body part of the diesel engine and is a rigid cast iron casting.
Four removable liners made of special cast iron are installed in the vertical bores of the block.
The liners are installed in the cylinder block along two centering belts: upper and lower.
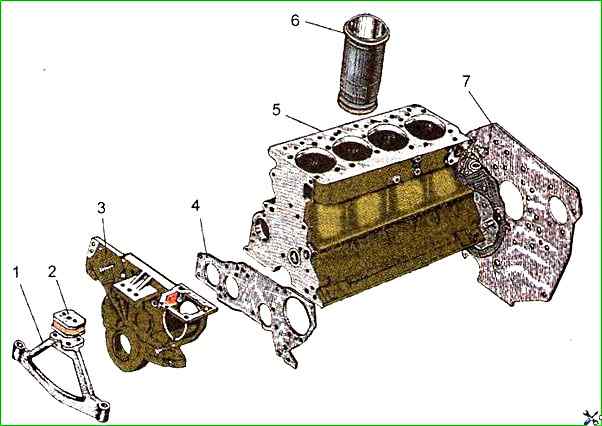
In the upper belt, the liner is secured with a flange, in the lower belt it is sealed with two rubber rings placed in the grooves of the cylinder block.
By internal diameter, the liner is sorted into three size groups: large (B), medium (M) and small (M).
The group marking is applied to the end of the liner flange. The diesel engine is equipped with cylinder liners of the same size group.
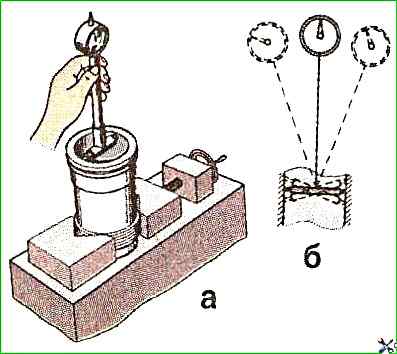
The diagram of measuring the inner diameter of a cylinder liner is shown in Fig. 2.
Coolant circulates between the cylinder block walls and the liners.
The end walls and cross partitions of the cylinder block have bosses in the lower part, designed to form the upper supports of the crankshaft.
These bosses are fitted with covers, which serve as the lower supports of the crankshaft. The bosses together with the caps form the beds for the main bearings.
The beds for the main bearing shells are bored together with the main bearing caps, so the caps cannot be swapped.
The cylinder block has a longitudinal channel, from which oil flows through transverse channels to the main bearings of the crankshaft and the camshaft bearings.
The cylinder block has nozzles in the second and fourth upper bearings of the crankshaft, which serve to cool the pistons with an oil jet.
On the outer surfaces of the cylinder block there are machined mating surfaces for fastening a centrifugal oil filter, a liquid pump, a fine fuel filter, an oil filler neck.
The deviation from the flatness of the upper surface of the cylinder block should not exceed 0.15 mm (for a new block - 0.05 mm).
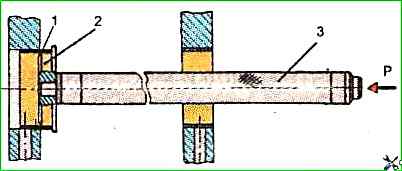
The diameter of the holes in the cylinder block for the main bearing shells when tightening the cap fastening bolts with a torque of 190-210 Nm should be 81+0022 mm.
If the main bearing surfaces are worn to a diameter of more than 81.03 mm, it is recommended to restore them to a shell with an increased outer diameter.
Turning over and rearranging the main bearing caps is not allowed.
The roughness of the surfaces of the holes for the main bearing shells should be Ra≤0.63 μm.
The difference in the values of the bore depths for the cylinder liner flange should not exceed 0.04 mm.
The oil channel holes must be cleaned of dirt.
The cylinder block cavity washed by the coolant, and oil channels must be checked for leaks with water under a pressure of at least 0.4 MPa for 1 min.
Coating of untreated surfaces must be done with a primer.
When pressing in the front, middle and rear camshaft bushings, the oil holes in the bushing and block must match.
The rear camshaft bushing must be pressed into the block to a depth of 7 mm relative to the rear plane, and the front one must be flush with the front plane of the block.
Pressing in of the bushings must be done using a set of special mandrels (Fig. 3).
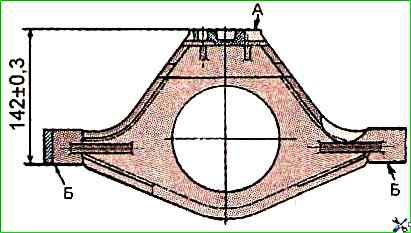
Deviation from flatness of the mating surface of the oil pan shall not exceed 0.25 mm.
When testing the oil pan with liquid under a pressure of at least 0.1 MPa, leakage or the appearance of drops over the entire surface is not allowed.
Deviation from flatness of surfaces "A" and (Fig. 4) of the front support of the diesel engine shall not exceed exceed 0.1 mm.
The deviation from parallelism of surfaces "B" relative to surface "A" should not exceed 0.2 mm over a length of 100 mm.
Surfaces "B" should lie in the same plane; permissible
The riveted part of the limiter should not protrude above the plane of the shock absorber plate by more than 0.5 mm.
The shock absorber rubber should not have cracks or tears.
When the shock absorber is compressed with a force of 2 kN, its deformation in height should be 2.5±0.5 mm.
Mounting joints of body parts
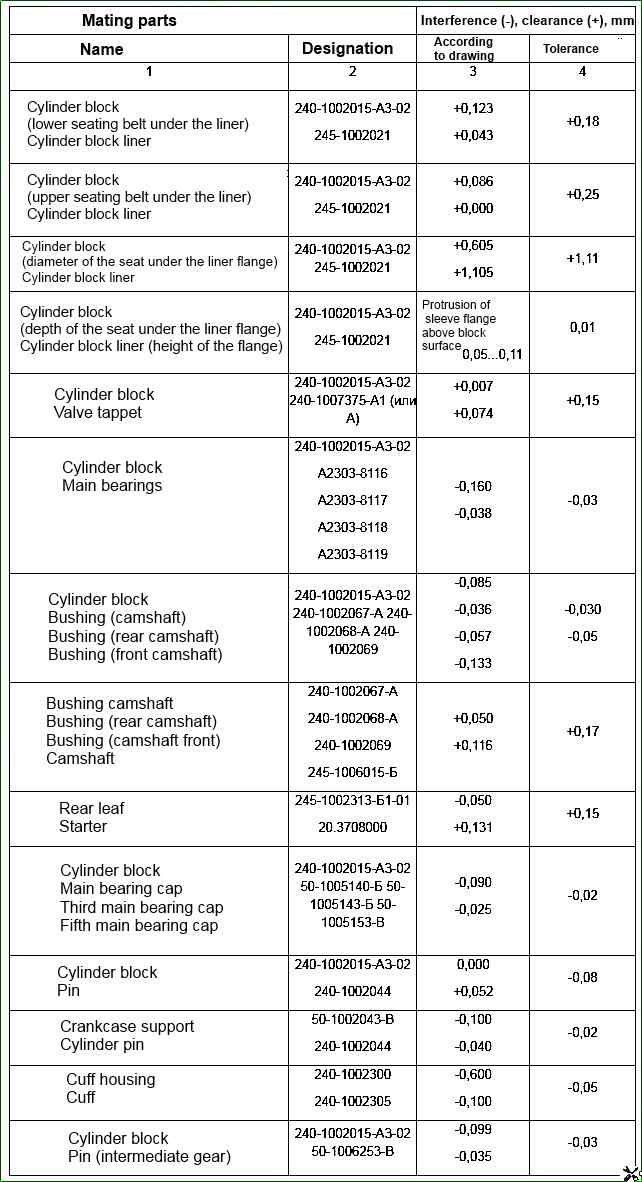
The main parts of the crank mechanism are: crankshaft 5, pistons 11 with piston rings and pins, connecting rods 8, main and connecting rod bearings, flywheel 15.
The crankshaft is steel, has five main and four connecting rod journals.
The connecting rod journals of the crankshaft have cavities for additional centrifugal cleaning of the oil. The cavities of the journals are closed with threaded plugs.
The axial force of the crankshaft is perceived by four half rings 14 made of aluminum alloy, installed in the bores of the cylinder block and the cover of the fifth main bearing.
To reduce the loads on the bearings from inertial forces, counterweights 7 are installed on the first, fourth, fifth and eighth cheeks of the crankshaft.
The crankshaft is sealed with cuffs at the front and rear.
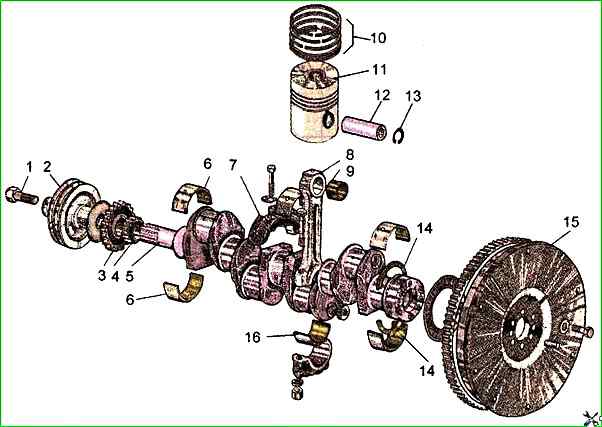
The front end of the shaft is fitted with timing gear 4, oil pump drive gear 3, and pulley 2 for the liquid pump and generator drive.
The flywheel 15 is attached to the rear flange of the shaft.
The crankshaft can be manufactured and installed on a diesel engine in two production sizes (nominals).
The crankshaft, the connecting rod or main journals of which are manufactured according to the second nominal size, has an additional marking on the first cheek.
Determining the runout of the crankshaft journals and measuring their diameter is shown in Fig. 2 and 3.
The piston is made of aluminum alloy.
The combustion chamber is located at the bottom of the piston.
The piston has four grooves in the upper part (Since 1999, pistons with three grooves for rings, i.e. with two compression rings, can be installed on diesel engines) - compression rings are installed in the first three, and an oil scraper ring is installed in the fourth.
The piston has a trapezoidal insert made of special cast iron under the upper compression ring. The piston bosses have bored holes for the piston pin.
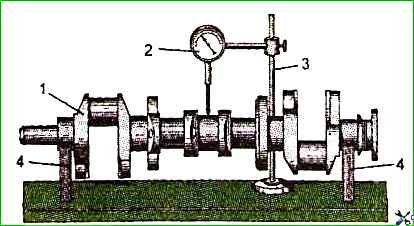
Pistons are sorted into three size groups (B, C, M) by the outer diameter of the skirt.
The group marking is applied to the piston bottom. When installing on a diesel engine, the cylinder liners and pistons must be of the same size group.
The piston rings are made of cast iron.
The upper compression ring is made of high-strength cast iron, chrome-plated, has an isosceles trapezoid in cross-section and is installed in the groove on any side.
The second and third compression rings are conical, and are marked top on the end surface near the lock.
Box-type oil scraper ring with a spiral steel expander.
Piston pin - hollow, made of chromium-nickel steel.
Axial movement of the pin in the piston bosses is limited by retaining rings.
Connecting rod - steel, I-section. A bushing is pressed into its upper head.
There are holes in the upper head of the connecting rod and the bushing for lubricating the piston pin.
The bed in the lower head of the connecting rod is bored for the liners in assembly with the cover. Therefore, replacing the connecting rod covers is not allowed.
The connecting rod and cover have the same numbers applied to their surfaces.
In addition, the connecting rods have weight groups by the weight of the upper and lower heads.
The designation of the weight group is applied to the end surface of the upper head of the connecting rod.
The diesel engine must be equipped with connecting rods of one group.
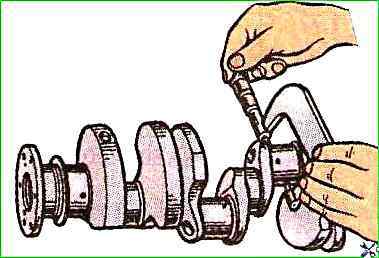
The crankshaft main and connecting rod bearing shells are made of steel-aluminum.
On diesel engines, two sizes of main and connecting rod bearing shells are used in accordance with the nominal value of the crankshaft journals.
Four repair sizes of liners are also provided for diesel engine repair.
The flywheel is made of cast iron and is attached to the flange crankshaft with bolts. A steel toothed ring is pressed onto the flywheel.
The pistons of one set on a diesel engine must be of the same size group, corresponding to the size group of the cylinder liners.
The difference in the mass of the pistons of one set must not exceed 10 g.
The difference in the mass of the connecting rods assembled with the pistons must not exceed 30 g.
The non-roundness and tolerance of the longitudinal section profile of the opening of the connecting rod upper head bushing is 0.005 mm.
When pressing in the bushing, its symmetrical location relative to the middle plane of the connecting rod must be ensured.
After boring, the surface of the opening of the upper head bushing must not have scratches and burrs, the roughness of the machined surface must be Ra≤0.63 μm.
One spiral or radial line is allowed on the upper surface of the bushing. risk no more than 0.1 mm wide.
Cracks and risks are not allowed on the surface of the connecting rod bolt. The bolt thread must be clean, without nicks and burrs.
The piston pin surface must be free of scratches, nicks and cracks.
The difference in the weight of the pins installed on one diesel engine must not exceed 10 g.
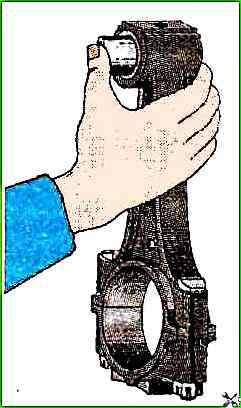
An unlubricated pin must easily rotate in the connecting rod with the force of a hand, must not have a transverse swing and must not fall out of the connecting rod under the action of its own weight (Fig. 4).
Connecting rod bearing shells must be selected in accordance with the dimensions of the crankshaft journals.
The shells must sit in the connecting rod beds and caps with an interference fit of 0.22 to 0.08 mm.
The radial clearance (gap) between the piston ring and the control gauge 70-8618-3515 (Fig. 5) for the upper compression ring must not exceed 0.02 mm on no more than 10% of the surface and no closer than 20° from the lock; and for oil scraper rings, the ovality should be within 0.15-0.65 mm.
The gap at the joint of the rings should be within 0.3-0.6 mm, and adjusting this gap is not allowed.
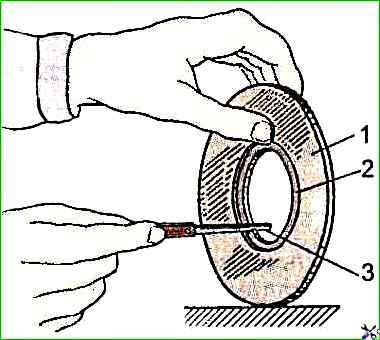
The tensile strength of the rings during ring bending is not less than 441 Nm.
Crankshaft
Straightening of shafts during mechanical processing and after high-frequency hardening is not allowed.
Straightening is allowed only after rolling the fillets. The shaft deflection during straightening should be no more than 1 mm.
When grinding the connecting rod journals, it is necessary to maintain the original radii of the crank (62.5±0.04 mm) and fillets (4+0.3 mm).
The roughness of the machined surfaces of the connecting rod and main journals should correspond to Ra≤0.32 μm.
The non-roundness and tolerance of the longitudinal section profile of the connecting rod and main journals is 0.01 mm.
The hardness of the journal surfaces after grinding should be at least 46 HRCэ. Hardening of fillets is not allowed.
After regrinding to the repair size, the runout of the middle main journal relative to the outer ones should not exceed 0.07 mm (for a new shaft - 0.03 mm).
Deviation from parallelism of the generating surfaces of the crank journals relative to the axis of the shaft installed on the outer main journals should not exceed 0.03 mm over a length of 100 mm.
The displacement of all crank journals relative to the diametrical plane of the 3rd main and 3rd crank journals (camber of the journals) after regrinding should not exceed 0.3 mm.
The runout of the cylindrical and end surfaces of the flywheel mounting flange at the extreme points relative to the surfaces of the outer main journals is allowed up to 0.05 mm (for a new shaft - no more than 0.03 mm).
The tubes must be tightly pressed into the crankshaft connecting rod journals; no play in the tubes is allowed.
The edges of the flared tubes must be recessed relative to the surface of the journals by 1.3 mm.
The plugs must be recessed in the threads by at least 2 mm and be locked.
The crankshaft gear must be pressed with the mark outward until it stops against the end of the main journal of the shaft.
The crankshaft must bedynamically balanced by removing metal from the periphery of any cheeks. Residual imbalance is no more than 900 g-mm at each end of the shaft.
The crankshaft assembly with counterweights must be balanced dynamically.
The mass should be adjusted by drilling holes in the counterweights in the radial direction with a diameter of 10 mm to a depth of no more than 25 mm.
Residual imbalance is no more than 650 g/mm at each end of the shaft.
After final processing, crankshafts must be checked with a magnetic flaw detector for surface defects. After checking, the shafts must be demagnetized.
Flywheel assembly
Cracks and chipping of the working surface of the flywheel ring gear teeth are not allowed.
Reduction in the length of the ring gear teeth (excluding the chamfer length) is allowed up to 16 mm (the length of the teeth of a new ring gear is 18 mm).
Wear of the flywheel ring gear teeth is allowed up to a thickness of 3.2 mm, with a height of installation of the vernier tooth gauge of 2.4 mm (the thickness of the tooth of a new ring gear corresponds to 4.73 mm).
Before pressing, the flywheel ring gear must be heated to a temperature of 195-200°C. The landing places of the flywheel and the ring gear must not have nicks or burrs.
A clearance of no more than 0.5 mm is allowed in the mating between the end surface of the ring gear and the flywheel. In one place on the arc no more than 60°.
The flywheel with the ring gear must be dynamically balanced in assembly with a pre-balanced crankshaft by drilling radial holes.
Residual imbalance at each end of the shaft is no more than 350 g/mm. After balancing, depersonalization of parts is not allowed.
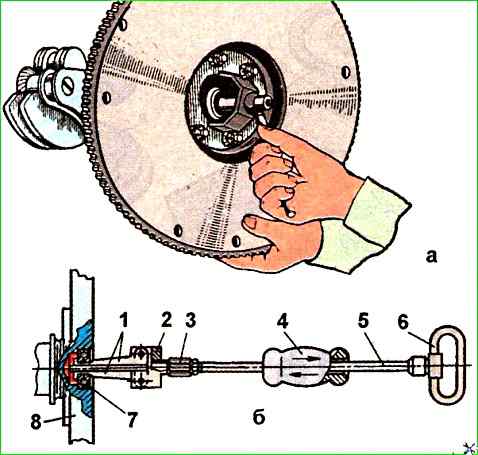
If it is necessary to replace the front bearing of the gearbox input shaft, then before removing the flywheel from the shaft, it should be pressed out using a screw puller mod. And 803.16.000 (Fig. 6,a) or, having removed the flywheel, press out the bearing using the impact puller mod. 2476 (Fig. 6,b).
Having installed the grips on the ends of the bearing rings, they are moved apart by the threaded stop 3, and then, when the weight hits the stop of the shaft 5, the bearing is pressed out.
The surface of the flywheel, conjugated with the surface of the driven disk of the clutch, is ground. The surface roughness should not be lower than Ra≤1.0.