Anforderungen an Teile und Komponenten des D-245-Dieselmotors
Der Zylinderblock ist die Basis des Gehäuseteils eines Dieselmotors und besteht aus einem starren Gusseisenguss.
In den vertikalen Bohrungen des Blocks sind vier abnehmbare Hülsen aus Spezialgusseisen eingebaut.
Die Laufbuchse wird entlang zweier Zentrierbänder im Zylinderblock installiert: oben und unten.
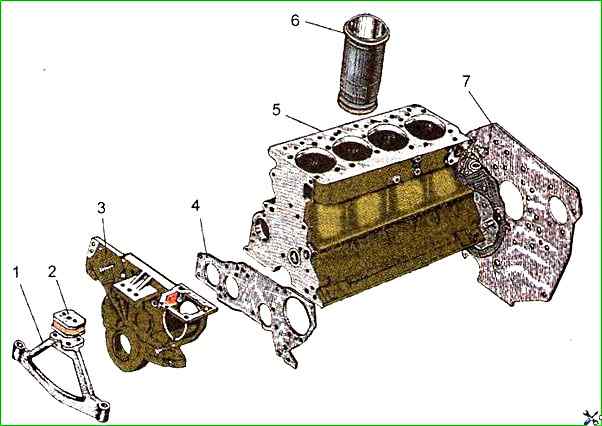
Im oberen Riemen ist die Laufbuchse mit einer Manschette befestigt, im unteren Riemen ist sie mit zwei Gummiringen abgedichtet, die in den Nuten des Zylinderblocks platziert sind.
Ärmel werden nach ihrem Innendurchmesser in drei Größengruppen eingeteilt: groß (B), mittel (S) und klein (M).
Die Gruppenmarkierung wird am Ende des Ärmelkragens angebracht. Dieselmotoren sind mit Hülsen der gleichen Größengruppe ausgestattet.
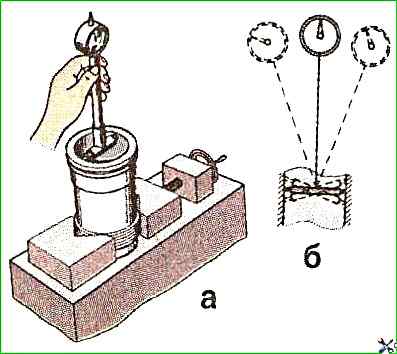
Das Diagramm zur Messung des Innendurchmessers einer Zylinderlaufbuchse ist in Abb. dargestellt. 2.
Kühlmittel zirkuliert zwischen den Wänden des Zylinderblocks und den Laufbuchsen.
Die Endwände und Quertrennwände des Zylinderblocks im unteren Teil verfügen über Vorsprünge, die die oberen Halterungen der Kurbelwelle bilden.
Auf diesen Vorsprüngen sind Abdeckungen angebracht, die als untere Stützen der Kurbelwelle dienen. Die Vorsprünge bilden zusammen mit den Abdeckungen Lager für die Hauptlager.
Die Lager der Hauptlagerschalen werden bei der Montage mit den Hauptlagerdeckeln zusammengebohrt, so dass die Deckel nicht ausgetauscht werden können.
Der Zylinderblock verfügt über einen Längskanal, von dem Öl durch Querkanäle zu den Hauptlagern der Kurbelwelle und den Nockenwellenlagern fließt.
Der Zylinderblock im zweiten und vierten oberen Kurbelwellenlager verfügt über Düsen, die dazu dienen, die Kolben mit einem Ölstrahl zu kühlen.
An den Außenflächen des Zylinderblocks befinden sich bearbeitete Passflächen zum Anbringen eines Zentrifugalölfilters, einer Flüssigkeitspumpe, eines Feinkraftstofffilters und eines Öleinfüllstutzens
Die Abweichung von der Ebenheit der Oberseite des Zylinderblocks sollte 0,15 mm nicht überschreiten (bei einem neuen Block - 0,05 mm).
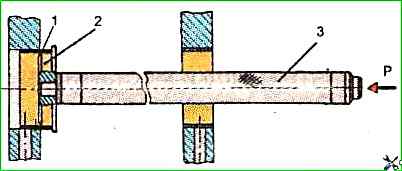
Der Durchmesser der Löcher im Zylinderblock für die Hauptlagerschalen sollte beim Anziehen der Deckelschrauben mit einem Drehmoment von 190-210 Nm 81+0022 mm betragen.
Wenn die Oberflächen der Hauptlager auf einen Durchmesser von mehr als 81,03 mm abgenutzt sind, wird empfohlen, die Laufbuchse wieder auf einen größeren Außendurchmesser zu bringen.
Das Verdrehen oder Umstellen der Hauptlagerdeckel ist nicht gestattet.
Die Oberflächenrauheit der Löcher für die Hauptlagerschalen muss Ra≤0,63 Mikrometer betragen.
Der Unterschied in der Tiefe der Bohrungen für den Zylinderlaufbuchsenbund sollte 0,04 mm nicht überschreiten.
Die Öffnungen der Ölkanäle müssen frei von Schmutz sein.
Der vom Kühlmittel umspülte Hohlraum des Zylinderblocks und die Ölkanäle müssen 1 Minute lang mit Wasser unter einem Druck von mindestens 0,4 MPa auf Undichtigkeiten überprüft werden.
Unbehandelte Oberflächen müssen mit einer Grundierung beschichtet werden.
Beim Einpressen der vorderen, mittleren und hinteren Nockenwellenbuchsen müssen die Öllöcher in der Buchse und im Block übereinstimmen.
Die hintere Nockenwellenbuchse muss bis zu einer Tiefe von 7 mm relativ zur hinteren Ebene in den Block gedrückt werden, und die vordere muss bündig mit der vorderen Ebene des Blocks abschließen.
Die Buchsen müssen mit einem Satz Spezialdornen eingepresst werden (Abb. 3).
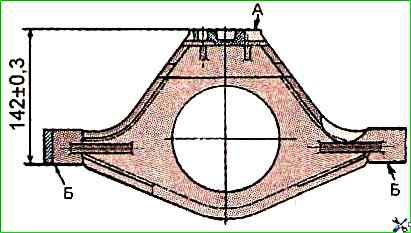
Die Abweichung von der Ebenheit der Passfläche der Ölwanne sollte 0,25 mm nicht überschreiten.
Bei der Prüfung der Ölwanne mit einer Flüssigkeit unter einem Druck von mindestens 0,1 MPa dürfen keine Leckagen oder Tropfen auf der gesamten Oberfläche auftreten.
Die Abweichung von der Ebenheit der Flächen „A“ und (Abb. 4) der vorderen Stütze des Dieselmotors sollte nicht größer sein Sticken 0,1 mm.
Die Abweichung von der Parallelität der Flächen „B“ relativ zur Fläche „A“ sollte auf einer Länge von 100 mm 0,2 mm nicht überschreiten.
Flächen „B“ müssen in derselben Ebene liegen; erlaubt
Der genietete Teil des Begrenzers sollte nicht mehr als 0,5 mm über die Ebene der Stoßdämpferplatte hinausragen.
Das Gummi des Stoßdämpfers darf keine Risse oder Risse aufweisen.
Wenn der Stoßdämpfer mit einer Kraft von 2 kN zusammengedrückt wird, sollte seine Höhenverformung 2,5 ± 0,5 mm betragen.
Montageverbindungen von Karosserieteilen
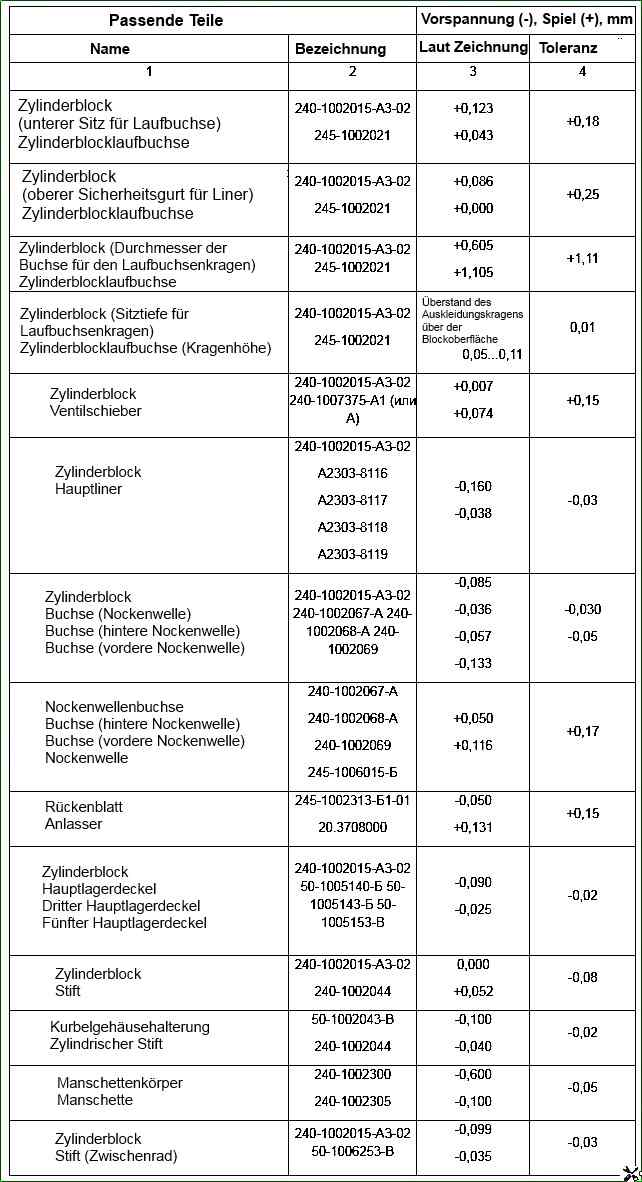
Die Hauptteile des Kurbelmechanismus sind: Kurbelwelle 5, Kolben 11 mit Kolbenringen und -bolzen, Pleuelstangen 8, Haupt- und Pleuellager, Schwungrad 15.
Die Kurbelwelle besteht aus Stahl und hat fünf Hauptzapfen und vier Pleuelzapfen.
Die Kurbelwellen-Pleuellagerzapfen verfügen über Hohlräume für eine zusätzliche Zentrifugalölreinigung. Die Hohlräume der Hälse werden mit Gewindestopfen verschlossen.
Die Axialkraft der Kurbelwelle wird von vier Halbringen 14 aus Aluminiumlegierung aufgenommen, die in den Bohrungen des Zylinderblocks und des fünften Hauptlagerdeckels eingebaut sind.
Um die Belastung der Lager durch Trägheitskräfte zu verringern, sind auf der ersten, vierten, fünften und achten Wange der Kurbelwelle Gegengewichte 7 angebracht.
Die Kurbelwelle ist vorne und hinten mit Manschetten abgedichtet.
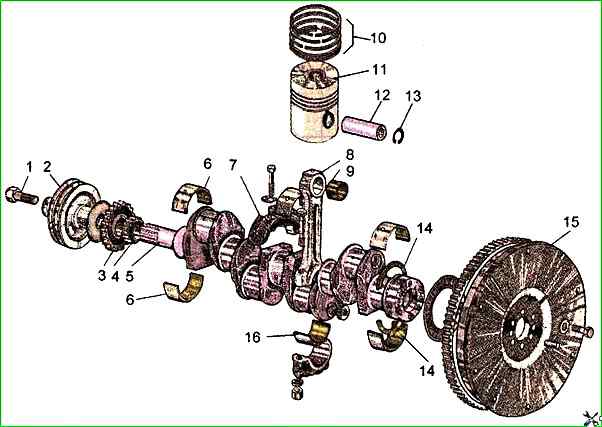
Am vorderen Ende der Welle sind Zahnrad 4 des Gasverteilungsantriebs, Zahnrad 3 des Ölpumpenantriebs, Riemenscheibe 2 des Antriebs der Flüssigkeitspumpe und des Generators montiert.
Schwungrad 15 ist am hinteren Flansch der Welle befestigt.
Die Kurbelwelle kann in zwei Produktionsgrößen (Nenngrößen) hergestellt und in einen Dieselmotor eingebaut werden.
Die Kurbelwelle, deren Pleuel bzw. Hauptzapfen nach dem zweiten Nennmaß gefertigt sind, weist auf der ersten Wange zusätzliche Markierungen auf.
Die Bestimmung des Rundlauffehlers der Kurbelwellenzapfen und die Messung ihres Durchmessers ist in Abb. dargestellt. 2 und 3.
Der Kolben besteht aus einer Aluminiumlegierung.
Die Brennkammer befindet sich am Boden des Kolbens.
Im oberen Teil hat der Kolben vier Nuten (Seit 1999 können Dieselkolben mit drei Ringnuten, also mit zwei Kompressionsringen, eingebaut werden) – in den ersten drei sind Kompressionsringe und ein Ölabstreifring verbaut ist im vierten installiert.
Der Kolben unter dem trapezförmigen oberen Kompressionsring verfügt über einen Einsatz aus Spezialgusseisen. Die Kolbennaben haben Bohrungen für den Kolbenbolzen.
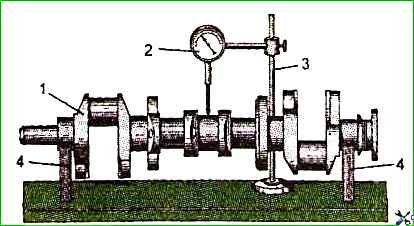
Kolben werden nach dem Außendurchmesser des Schaftes in drei Größengruppen (B, S, M) eingeteilt.
Die Gruppenmarkierung ist auf dem Kolbenboden angebracht. Beim Einbau in einen Dieselmotor müssen Laufbuchsen und Kolben derselben Größengruppe angehören.
Kolbenringe bestehen aus Gusseisen.
Der obere Kompressionsring besteht aus hochfestem Gusseisen, ist verchromt, hat im Querschnitt die Form eines gleichschenkligen Trapezes und wird beidseitig in die Nut eingebaut.
Der zweite und dritte Kompressionsring sind konisch und oben auf der Endfläche des Schlosses markiert.
Kastenförmiger Ölabstreifring mit spiralförmigem Stahlexpander.
Der Kolbenbolzen ist hohl und besteht aus Chrom-Nickel-Stahl.
Die axiale Bewegung des Bolzens in den Kolbennaben wird durch Sicherungsringe begrenzt.
Pleuelstange – Stahl, I-Profil. In seinen oberen Kopf ist eine Buchse eingepresst.
Am oberen Ende der Pleuelstange und der Buchse befinden sich Löcher zum Schmieren des Kolbenbolzens.
Das Bohren des Bettes im unteren Kopf der Verbindungsstange für die Liner erfolgt bei der Montage mit der Abdeckung. Daher ist der Austausch von Pleueldeckeln nicht zulässig.
Auf der Oberfläche der Pleuelstange und der Abdeckung sind die gleichen Nummern aufgedruckt.
Darüber hinaus haben die Pleuel Gewichtsgruppen, die auf der Masse des oberen und unteren Kopfes basieren.
Die Bezeichnung der Massengruppe ist auf der Stirnfläche des oberen Pleuelkopfes angebracht.
Bei Dieselmotoren muss eingebaut werden Pleuel der gleichen Gruppe.
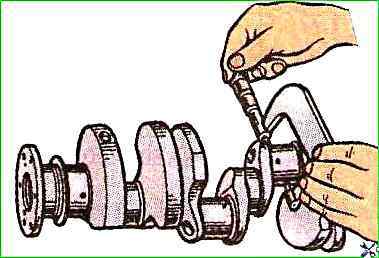
Die Haupt- und Pleuellager der Kurbelwelle bestehen aus Stahl-Aluminium.
Dieselmotoren verwenden Haupt- und Pleuellagerschalen in zwei Größen entsprechend der Nennleistung der Kurbelwellenzapfen.
Für die Dieselreparatur sind außerdem vier Reparaturgrößen an Einsätzen im Lieferumfang enthalten.
Das Schwungrad besteht aus Gusseisen und ist mit dem Kurbelwellenflansch verschraubt. Auf das Schwungrad ist ein Zahnkranz aus Stahl aufgepresst.
Kolben eines Satzes an einem Dieselmotor müssen derselben Größengruppe angehören, entsprechend der Größengruppe der Zylinderlaufbuchsen.
Der Unterschied in der Masse der Kolben eines Satzes sollte 10 g nicht überschreiten.
Der Massenunterschied zwischen Pleuel und Kolben darf 30 g nicht überschreiten.
Die Unrundheit und Toleranz des Profils des Längsschnitts des Lochs in der Buchse des oberen Kopfes der Pleuelstange beträgt 0,005 mm.
Beim Einpressen der Buchse ist auf deren symmetrische Lage zur Mittelebene des Pleuels zu achten.
Nach dem Bohren sollte die Oberfläche des oberen Kopfbuchsenlochs keine Markierungen oder Grate aufweisen, die Rauheit der bearbeiteten Oberfläche sollte Ra≤0,63 µm betragen.
Auf der Oberseite der Buchse ist eine spiralförmige oder radiale Markierung mit einer Breite von nicht mehr als 0,1 mm zulässig.
Auf der Oberfläche des Pleuelbolzens sind keine Risse und Risiken zulässig. Das Bolzengewinde muss sauber sein, ohne Kerben oder Grate.
Die Oberfläche des Kolbenbolzens sollte frei von Flecken, Kerben und Rissen sein.
Der Unterschied in der Masse der Finger eines Dieselmotors sollte 10 g nicht überschreiten.
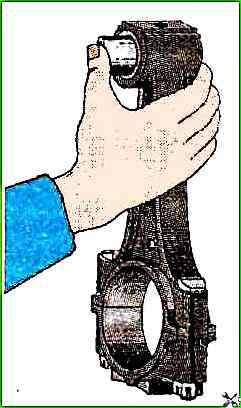
Der Finger, der nicht mit Öl geschmiert ist, sollte sich durch Handkraft leicht in der Pleuelstange drehen lassen, kein seitliches Schwingen aufweisen und nicht unter dem Einfluss seines Eigengewichts aus der Pleuelstange fallen (Abb. 4).
Die Pleuellagerschalen müssen entsprechend den Abmessungen der Kurbelwellenzapfen ausgewählt werden.
Die Laufbuchsen müssen mit einer Presspassung von 0,22 bis 0,08 mm in den Lagern der Pleuelstangen und -kappen sitzen.
Der radiale Spalt (Spiel) zwischen dem Kolbenring und dem Kontrollkaliber 70-8618-3515 (Abb. 5) für den oberen Kompressionsring sollte 0,02 mm auf nicht mehr als 10 % der Oberfläche und nicht weniger als 0,02 mm überschreiten 20° von der Schleuse entfernt; und bei Ölabstreifringen sollte die Ovalität im Bereich von 0,15–0,65 mm liegen.
Der Spalt an der Verbindungsstelle der Ringe muss zwischen 0,3 und 0,6 mm liegen. Eine Anpassung dieses Spalts ist nicht zulässig.
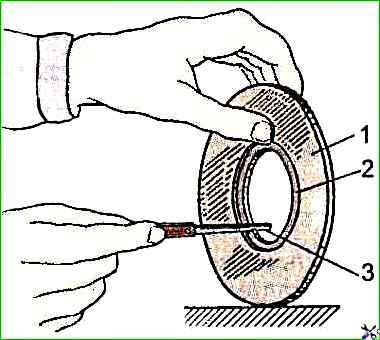
Die Zugfestigkeit der Ringe beim Biegen des Rings beträgt nicht weniger als 441 Nm.
Kurbelwelle
Das Nachbearbeiten von Wellen während der Bearbeitung und nach dem Hochfrequenzhärten ist nicht zulässig.
Bearbeiten ist erst möglich, nachdem die Filets gerollt wurden. Die Wellendurchbiegung beim Richten sollte nicht mehr als 1 mm betragen.
Beim Schleifen von Pleuelzapfen ist es notwendig, die ursprünglichen Radien der Kurbel (62,5 ± 0,04 mm) und Kehlen (4 + 0,3 mm) beizubehalten.
Die Rauheit der bearbeiteten Oberflächen der Pleuelstange und der Hauptlagerzapfen muss Ra≤0,32 µm entsprechen.
Die Unrundheit und Toleranz des Längsschnittprofils der Pleuelstange und der Hauptlagerzapfen beträgt 0,01 mm.
Die Härte der Zapfenoberflächen nach dem Schleifen muss mindestens 46 HRCe betragen. Das Härten von Filets ist nicht zulässig.
Nach dem Schleifen auf die Reparaturgröße sollte der Schlag des mittleren Zapfens im Verhältnis zu den äußeren nicht mehr als 0,07 mm betragen (bei einer neuen Welle - 0,03 mm).
Die Abweichung von der Parallelität der Formflächen der Pleuelzapfen relativ zur Achse der auf den äußeren Hauptzapfen montierten Welle sollte auf einer Länge von 100 mm 0,03 mm nicht überschreiten.
Die Verschiebung aller Pleuelzapfen relativ zur diametralen Ebene des 3. Haupt- und 3. Pleuelzapfens (Wölbung der Zapfen) nach dem Schleifen sollte 0,3 mm nicht überschreiten.
Die Unrundheit der Zylinder- und Endflächen des Schwungrad-Montageflansches an den äußersten Punkten relativ zu den Flächen der äußeren Hauptzapfen ist bis zu 0,05 mm zulässig (bei einer neuen Welle nicht mehr als 0,03 mm).
Die Rohre müssen fest in die Kurbelzapfen der Kurbelwelle gedrückt werden; Das Spielen in den Röhren ist nicht gestattet.
Die Kanten der aufgeweiteten Rohre sollten gegenüber der Oberfläche der Hälse um 1,3 mm zurückversetzt sein.
Die Stopfen müssen mindestens 2 mm im Gewinde verankert und gesichert sein.
Das Kurbelwellenrad muss mit der Markierung nach außen gedrückt werden, bis es am Ende des Hauptwellenzapfens anschlägt.
Die Kurbelwelle muss di sein chemisch ausgeglichen, indem Metall von der Peripherie aller Wangen entfernt wird. Restunwucht – nicht mehr als 900 g-mm an jedem Ende der Welle.
Die Kurbelwellenbaugruppe mit Gegengewichten muss dynamisch ausgewuchtet sein.
Die Masse sollte durch Bohren von Gegengewichten in radialer Richtung von Löchern mit einem Durchmesser von 10 mm bis zu einer Tiefe von nicht mehr als 25 mm eingestellt werden.
Restunwucht – nicht mehr als 650 g/mm an jedem Ende der Welle.
Nach der Endbearbeitung müssen Kurbelwellen mit einem magnetischen Fehlerprüfgerät auf das Fehlen von Oberflächenfehlern überprüft werden. Nach der Prüfung müssen die Wellen entmagnetisiert werden.
Schwungradbaugruppe
Risse und Abplatzungen der Arbeitsfläche der Zähne des Schwungradrings sind nicht zulässig.
Eine Reduzierung der Länge der Zähne der Krone (ohne die Länge der Fase) ist bis zu 16 mm zulässig (die Länge der Zähne der neuen Krone beträgt 18 mm).
Der Verschleiß der Zähne des Schwungradrings ist bis zu einer Dicke von 3,2 mm zulässig, bei einer Einbauhöhe des Messschiebers von 2,4 mm (die Zahndicke des neuen Rings entspricht 4,73 mm).
Die Schwungradkrone muss vor dem Pressen auf eine Temperatur von 195–200 °C erhitzt werden. Die Sitze des Schwungrads und der Felge dürfen keine Kerben oder Grate aufweisen.
Der zulässige Spalt in der Schnittstelle zwischen der Endfläche der Felge und dem Schwungrad beträgt an einer Stelle des Bogens nicht mehr als 0,5 mm, nicht mehr als 60°.
Das Schwungrad und die Krone müssen als Baugruppe mit einer vorgewuchteten Kurbelwelle durch Bohren radialer Löcher dynamisch ausgewuchtet werden.
Die Restunwucht an jedem Ende der Welle beträgt nicht mehr als 350 g/mm. Nach dem Auswuchten ist eine Depersonalisierung von Teilen nicht zulässig.
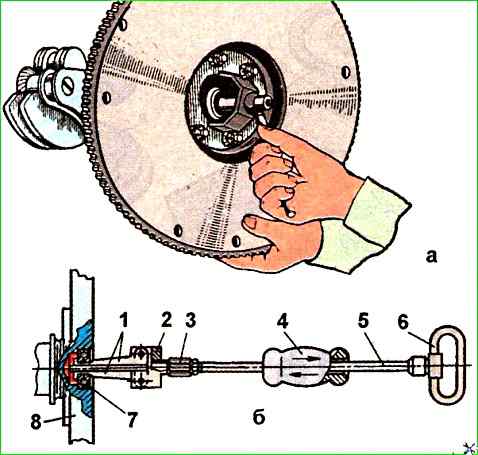
Wenn das vordere Lager der Getriebeeingangswelle ausgetauscht werden muss, sollte es vor dem Entfernen des Schwungrads von der Welle mit einem Schraubenzieher Mod. herausgedrückt werden. Und 803.16.000 (Abb. 6, a) oder nach Ausbau des Schwungrads das Lager mit einem Schlagabzieher Mod. herausdrücken. 2476 (Abb. 6,b).
Nachdem die Klemmen an den Enden der Lagerringe angebracht sind, werden diese mit einem Gewindeanschlag 3 auseinander bewegt und dann, wenn die Last auf den Anschlag der Welle 5 trifft, wird das Lager herausgedrückt.
Die Schwungradoberfläche, die mit der Oberfläche der Kupplungsscheibe zusammenpasst, ist geschliffen. Die Oberflächenrauheit darf nicht kleiner als Ra≤1,0 sein.