Malfunctions of pneumatic drive power supplies
When servicing the pneumatic drive of the car brakes, you must first of all make sure that the system is tight
Particular attention should be paid to the tightness of connections of pipelines and flexible hoses, since this is where air leaks most often occur
Lots of strong air leakage are determined by ear, and weak ones - using a soap emulsion.
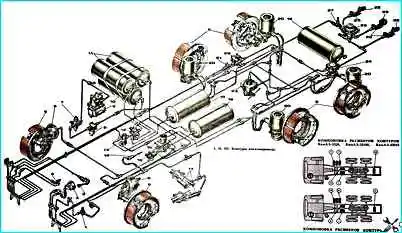
Brake diagram: 1 - Auxiliary brake control valve; 2 - Parking brake control valve; 3 - Two-pointer pressure gauge; 4 - Emergency parking brake release edge; 5 - Brake mechanism; 6 - Brake chamber type 24; 7 - Pressure regulator; 8 - Frost protection; 9 - Compressor; 10 - Condensation receiver; 11 - Receivers for circuit II of the rear bogie service brake drive; 12 - Triple safety valve; 13 - Double safety valve; 14 - Pneumatic cylinder for driving the engine stop lever; 15 - Pressure limitation valve; 16 - Two-section brake valve; 17 - Pneumatic cylinders for driving the auxiliary brake flaps; 18 - Receiver of circuit I of the front axle service brake drive; 19 - Receiver of circuit III of the spare and parking brakes; 20 - Brake chamber with spring energy accumulator type 20/20; 21 - Double-line bypass valve; 22 - Accelerator valve; 23 - Aromatic brake force regulator; 24 - Trailer brake control valve with two-wire drive; 25 - Disconnect valve; 26 - Trailer brake control valve with single-line drive; 27 - Single safety valve; 28 - Palm type connection head;
Air leaks from connections of pipelines and brake system devices are eliminated by tightening them, and leaking pipelines and flexible hoses are replaced.
You must remember that on cars manufactured since March 1986, pipeline connections are sealed using rubber rings, so the tightening torques of the fittings should be less (Table 1).
If the air cylinders of the pneumatic brake drive are not filled and the pressure regulator releases air into the atmosphere, there may be several reasons:
- - the pipeline between the regulator and the safety valves is blocked;
- - the pressure regulator is faulty - most often the filter element is clogged with oil or ice crystals.
If the air cylinders fill slowly and the air pressure does not reach the nominal pressure, then either the compressor or the pressure regulator is faulty.
A malfunction of the compressor cylinder-piston group is also indicated by an increased oil content in the condensate.
The cylinders of a separate circuit are often poorly filled. Air enters each circuit of the brake system through a section of its “own” safety valve.
Probably, the safety valve does not allow air into the cylinder or the air supply line to this circuit is clogged. It is also possible that the standard two-pointer pressure gauge is faulty.
Malfunctions of the service brake system
Ineffective braking of the car when you press the brake pedal occurs if the brake valve drive is out of adjustment or the two-section brake valve is faulty.
If, when braking, the pressure in the brake chambers is nominal, then the wheel brake mechanisms are misaligned or faulty.
If, when braking with the service brake, the pressure is below normal only in the brake chambers of the front axle, then either the lower section of the brake valve or the pressure limiter is faulty.
If the pressure in the brake chambers is normal, but braking is not effective, then the stroke of the brake chamber rods is greater than normal, or, for example, the brake linings are oily.
When you press the brake pedal, the braking of the wheels of the rear cart is ineffective or does not occur at all (the front wheels brake normally).
In the pneumatic part of the drive, the upper section of the brake valve or the brake force regulator may be faulty.
In the mechanical part, the brake mechanisms or the drive of the brake force regulator lever are faulty or misaligned.
If, after releasing the brake pedal, all the wheels of the car do not release the brakes, then the two-section brake valve is faulty (the pusher or the upper piston is jammed).
It is possible that the brake valve drive is out of adjustment (there is no free play of the brake pedal).
If air does not come out of the rear brake chambers after releasing the brake pedal, the brake force regulator or the upper section of the brake valve is faulty.
These malfunctions lead to a delay in the release of air from the front brake chambers.
If, when releasing the brakes, air is not released only from the front of the brake chambers, then the pressure limiter or the lower section of the brake valve is faulty.
Air leaks from the atmospheric outlet of the pressure limiter or brake force regulator during braking indicate malfunctions of these devices.
The cause of air leaks from the atmospheric outlet of a two-section brake valve can be not only the sealing rings and valves in the valve itself, but also other devices of the brake system.
If air leakage from the atmospheric outlet of the brake valve is observed when the pedal is released and the parking brake is applied, then the brake valve is faulty.
When the engine is not running, using the standard two-pointer pressure gauge, you can accurately determine which section of the valve is leaking: if the upper arrow of the pressure gauge falls, the lower section of the valve is leaking; the lower arrow falls - the upper section is leaking.
If air leakage from the atmospheric outlet of the brake valve is observed only when the parking brake is released, and stops when applied, then the trailer brake control valve with a two-wire drive or one of the energy accumulators is faulty.
You can determine a faulty device by supplying air to the energy accumulators from the emergency brake release circuit: if, when you press the emergency brake release valve button, the leakage from the brake valve continues, then the pusher seal in the energy accumulator body is leaking, and if there is no leak, then the diaphragm in the brake control valve is faulty trailer.
Air leakage from the atmospheric outlet of the brake valve during braking indicates leakage of valves or o-rings in the device itself.
Malfunctions of the pneumatic drive of the parking brake system and the emergency brake release circuit
If, when the parking brake is turned off, the wheels of the rear trolley do not release the brakes, then this may be caused by malfunctions in the parking brake valve, in the accelerator or dual-line valves, in energy accumulators.
It is possible that one of the pipes in the parking brake circuit is clogged, frozen or pinched.
In the parking brake valve, a breakdown of the guide plastic plate or unreliable attachment of the rod to this plate leads to the parking brake not braking.
In the accelerator valve in winter, the most likely reason for non-release is the freezing of condensate in the cavity above the piston.
If, when moving the parking brake valve handle, one of the energy accumulators does not work, then mechanical damage to this device is possible: dents in the body or jamming of the pusher.
There may also be a blockage in the pipeline through which air is supplied to an inoperative energy accumulator.
If the brake chamber rods come out when the energy accumulators are turned on, and the car does not brake effectively enough, then it is necessary to check the stroke of the rods (it should not exceed 40 mm) and the serviceability of the wheel brake mechanisms.
The brake pad linings must not be worn out or oily.
The most common malfunctions in the parking brake circuit, as well as in the entire pneumatic drive, are compressed air leaks due to faulty sealing rings and cuffs.
It is important to determine the cause of the leak and find the faulty device.
Air leakage from under the parking brake valve handle when the brake is released is caused by a leaky rod seal in the guide.
This seal fails the fastest because the rod reciprocates and rotates, and the diameter of the o-ring is small.
The cause of air leakage from the atmospheric outlet of the parking brake valve is not always a leak in the seals in the valve itself. The two-wire trailer brake control valve may be faulty.
How to identify a faulty device? Fill the pneumatic drive with compressed air, turn on the parking brake, disconnect the control line tube from the valve; if air leakage from the atmospheric outlet continues, then the parking brake valve is faulty; If a leak is observed from the disconnected control line, the trailer brake control valve is faulty.
If air leaks from the atmospheric outlet of the accelerator valve both during braking and when releasing the parking brake, the sealing ring of the atmospheric outlet of the valve is leaking.
Air leakage through the atmospheric outlet of the device when braking with the parking brake is caused by the loss of tightness of the inlet valve, and when the brake is released, by the exhaust valve. In the latter case, the rear wheels are not released.
Sometimes air leakage through the accelerator valve is observed when the parking brake is on and the brake pedal is pressed at the same time.
In this case, one of the energy accumulators is faulty - air from the brake chamber goes through the seal of the pusher pipe into the energy accumulator and then through the accelerator valve n into the atmosphere.
During operation in energy accumulators, the seals of the piston in the cylinder and the pusher pipe in the housing wear out and fail.
When the parking brake is released, compressed air from under the piston flows through a leaky seal into the cavity above the piston and through the connecting hose on the side of the device under the brake chamber diaphragm, and from there into the atmosphere through the drain hole.
When the parking brake is applied, the leakage stops.
If the seal of the pusher pipe in the accumulator body fails, then when the parking brake is turned off, compressed air from under the piston enters the cavity above the diaphragm and escapes into the atmosphere through the brake force regulator.
If the regulator lever is “tied” in the upper position or the car is fully loaded, then the air escapes into the atmosphere through the atmospheric outlet of the brake valve.
To detect a faulty energy accumulator, you need to release the parking brake and one by one disconnect the pipelines supplying compressed air to the rear brake chambers: for a faulty device, compressed air will come out of the cavity of the brake chamber.
The springs in energy accumulators can be compressed mechanically using screws located on top.
When the screw is unscrewed, the force is transmitted through the thrust bearing to the piston, and the spring is compressed.
If the threaded connection of the screw and the boss are not lubricated, and the screw is not screwed tightly into the boss, and moisture gets into the threaded connection, the thread rusts, and it becomes difficult, and sometimes impossible, to remove such a screw.
Energy accumulators can be released using the emergency brake release circuit.
When you press the emergency brake release valve button, compressed air from the service brake cylinders is supplied through a two-line valve to the energy accumulators.
If, when the tap button is pressed, the energy accumulators are not released, and after releasing it, a small portion of compressed air comes out of the atmospheric outlet, then the cross-section of the pipeline between the tap and the two-line valve is blocked.
If, after releasing the valve button, there is no air coming out of the atmospheric outlet, then the valve itself is faulty.
If, when you press the tap button, air escapes into the atmosphere through the accelerator valve, the dual-line valve is faulty; its sealing washer is leaking.
An air leak from the atmospheric outlet of the emergency brake release valve may be due to a malfunction of both the valve itself and the two-line valve.
If an air leak is observed regardless of the position of the parking brake valve handle, then the valve itself is faulty.
And if the leak occurs only when the parking brake is released, and stops when braking, it means that the dual-line valve is leaking.
In both cases, it is forbidden to plug the atmospheric outlet in the emergency brake release valve with a plug, since in this case spontaneous release of the parking brake of the vehicle is observed and the spare brake does not work satisfactorily.
This is explained by the fact that when you turn on the emergency or parking brake by turning the parking brake valve handle, air is not always released from the energy accumulators.
The release of air is prevented by a two-line valve, and a faulty emergency brake release valve creates air pressure in the energy accumulators sufficient to release the parking brake.
The most likely malfunctions that can be detected and eliminated by a driver without the use of diagnostic equipment are discussed below
If the pneumatic drive receivers are not filled and the pressure regulator releases air into the atmosphere then there may be several reasons for this malfunction:
- - the pipeline between the regulator and the safety valves is blocked;
- - the pressure regulator is faulty - most often the filter element is clogged with oil or ice crystals (in winter).
If the receivers fill slowly and the pressure in them does not reach the nominal value (in the absence of leaks), then either the compressor or the pressure regulator is faulty.
If the receivers of a separate circuit are poorly filled, then first of all you should pay attention to the safety valve section of this circuit.
Ineffective braking of the vehicle by the service brake occurs if the drive is misaligned or the two-section brake valve is faulty.
If, when braking, the pressure in the brake chambers is nominal, then the brake mechanisms are misregulated or faulty.
If, when braking with the service brake, the pressure is below normal only in the brake chambers of the front axle, then either the lower section of the brake valve or the pressure limiter may be faulty.
If the pressure in the brake chambers is normal, and braking is ineffective, then the cause of this malfunction may be the large stroke of the brake rods measures or, for example, oily brake pad linings.
If, when the brake pedal is pressed, the braking of the wheels of the rear trolley is ineffective or does not occur at all, while the front wheels brake normally, then the pneumatic part of the drive may have a malfunction in the upper section of the brake valve or the brake force regulator may be faulty. In this case, malfunctions in the adjustment of the brake mechanisms or the drive of the brake force regulator are possible.
If, after lowering the brake pedal, all the wheels of the car do not release the brakes, the two-section brake valve may be faulty (the pusher or the upper piston is jammed) or the brake valve drive may be misaligned (there is no free play of the pedal).
If, after releasing the brake pedal, air does not come out only from the rear brake chambers, then it is possible that the brake force regulator or the upper section of the brake valve is faulty.
These malfunctions lead to a delay in the release of air from the front brake chambers. If, when releasing the brakes, air is not released only from the front brake chambers, then the pressure limiter or the lower section of the brake valve is faulty.
The cause of air leaks through the atmospheric outlet of a two-section brake valve can be not only the sealing rings and valves in the valve itself, but also other devices of the brake system.
If leakage is observed when the pedal is released and the parking brake is on, then the brake valve is faulty.
Using a standard two-pointer pressure gauge, you can accurately determine which section of the valve is leaking: if the upper needle of the pressure gauge “falls” when the engine is not running, then the lower section of the valve is leaking; The lower arrow “falls” - the upper section is leaking.
If air leakage through the atmospheric outlet of the brake valve is observed only when the parking brake is released, and when it is turned on, it stops, then the trailer brake control valve with a two-wire drive or one of the energy accumulators is faulty.
You can determine a faulty device by supplying air to the energy accumulators from the emergency brake release circuit: if, when you press the emergency brake release button, the leak from the brake valve continues, then the pusher seal in the energy accumulator body is leaking, and if there is no leak, then the membrane in the trailer brake control valve is faulty .
If, when the parking brake is turned off, the wheels of the rear trolley do not release the brakes then the cause of this malfunction may be the parking brake valve, accelerator or dual-line valve and energy accumulators.
It is possible that one of the pipes in the parking brake circuit is clogged, frozen or pinched.
If one of the energy accumulators does not operate when moving the parking brake valve handle, then the cause may be dents on the body or sticking of the pusher.
It is also possible that the pipeline through which air is supplied to an inoperative energy accumulator is clogged.
If the brake chamber rods come out when the energy accumulators are turned on, and the car does not brake effectively enough, then it is necessary to check the stroke of the rods and the serviceability of the brake mechanisms and wheels.
The most common malfunctions in the parking brake circuit, as well as in the entire pneumatic drive, are compressed air leaks due to damage to the sealing rings and cuffs.
Air leakage from under the parking brake valve handle when the brake is released is caused by a leaky rod seal in the guide.
The cause of air leakage from the atmospheric outlet of the parking brake valve is not always a leak in the seals in the valve itself.
For example, a leak may occur due to a malfunction of the two-wire trailer brake control valve.
To determine the faulty device, fill the pneumatic drive with compressed air, turn on the parking brake, and disconnect the control line tube from the tap.
If air leakage from the atmospheric outlet continues, then the parking brake valve is faulty; If a leak is observed from the disconnected tube, then the trailer brake control valve is faulty.
If air leaks from the atmospheric outlet of the accelerator valve during braking and when releasing the parking brake, then the sealing ring of the atmospheric outlet of the valve is leaking.
Air leakage through the atmospheric outlet of this device when braking with the parking brake is caused by the loss of tightness of the inlet valve, and when the brake is released, by the exhaust valve. In the latter case, the rear wheels are not released.
Sometimes an air leak through the accelerator valve is observed when the parking brake is on and the pedal is pressed at the same time.
In this case, one of the energy accumulators is faulty - air from the brake chamber through the seal of the pusher pipe enters the energy accumulator and then through the accelerator valve into the atmosphere sphere.
During operation in energy accumulators, the seals of the piston in the cylinder and the pusher pipe in the housing wear out and fail.
When the parking brake is released, compressed air from under the piston flows through a leaky seal into the cavity above the piston and through the connecting hose on the side of the device under the brake chamber membrane, and from there into the atmosphere through the drain hole. In this case, when the parking brake is applied, the leakage stops.
If the seal of the pusher pipe in the energy accumulator body fails, then when the parking brake is applied, compressed air from under the piston enters the cavity above the membrane and escapes into the atmosphere through the brake force regulator.
If the regulator lever is in the upper position, then the air escapes to the atmosphere through the atmospheric outlet of the brake valve.
To detect a faulty energy accumulator, you need to release the parking brake and one by one disconnect the pipelines supplying compressed air to the rear brake chambers: for a faulty device, compressed air will come out of the cavity of the brake chamber.
If the emergency brake release button is pressed; the energy accumulators are not released (at a pressure in the pneumatic drive of more than 500 kPa), and after it is released, a small portion of compressed air comes out of the atmospheric outlet of the pneumatic valve, which means that the cross-section of the pipeline between the valve and the two-line valve is blocked.
If, after releasing the button, there is no air coming out of the atmospheric outlet, then the valve itself is faulty.
If, when you press the tap button, air escapes into the atmosphere through the accelerator valve, then the dual-line valve is faulty.
Air leakage from the atmospheric outlet may occur due to a malfunction of both the tap itself and the two-line valve.
If an air leak is observed regardless of the position of the parking brake valve handle, then the valve itself is faulty.
But if the leak occurs only when the parking brake is released, and stops when braking, it means the dual-line valve is leaking
In both cases, it is forbidden to plug the atmospheric outlet in the emergency brake release valve with a plug, since in this case spontaneous release of the parking brake is observed, and the car's spare brake does not work satisfactorily.
This is explained by this. that when you apply the emergency or parking brake by turning the parking brake valve handle, releasing air from the energy accumulators will be difficult or impossible.
If, when you press the auxiliary brake valve button, the engine does not stop (the flaps in the exhaust pipes do not turn) and the trailer does not brake, then there may be several reasons explaining this phenomenon: air is not supplied to the auxiliary brake valve, the pipeline is pinched or clogged , going from the crane to the pneumatic cylinders, the crane itself is faulty.
The malfunction is determined by sequential shutdown of the pipelines.
If the fuel does not turn off when the auxiliary brake is on, and the dampers in the exhaust pipes operate, you should check whether compressed air is supplied to the pneumatic cylinder on the fuel pump. A malfunction may also occur in the mounting of the pneumatic cylinder.
The damper mechanism and the pneumatic cylinders that control them operate under the most unfavorable conditions. Therefore, they fail more often than others, and dampers jam most often.
If this happens with both dampers, the engine will not start, if with one, then the engine starts, but smokes and does not develop power.
Pneumatic cylinders of the damper drive may also experience problems, the most common of which is loss of tightness of the piston cuff.
The trailer solenoid valve activation sensor is located on the left frame side member inside, next to the clutch housing.
If the sensor or electrical wiring fails and when the auxiliary brake is turned on, the trailer does not brake, and the road train may skid and fold.
If, after releasing the auxiliary brake valve button, the air from the pneumatic cylinders and the sensor is not released, i.e., the auxiliary brake does not turn off, then you need to check the atmospheric outlet in the valve.
In winter, it often freezes over, and a mud-ice plug forms in the atmospheric outlet, which prevents air from leaving the circuit.
If in this case the inlet valve in the auxiliary brake valve loses its seal, the brake will turn on spontaneously and the engine will stop for no apparent reason.
If there is no air in the auxiliary brake circuit, the engine can be started, but after a few minutes it spontaneously stops due to the supply of air through a faulty valve to the fuel shut-off pneumatic cylinder. This faucet requires replacement.
If there is no spontaneous engine stop, but it does not start after releasing the auxiliary valve button brake when the car is moving, it is enough to clean the atmospheric outlet of the valve.