Zylinderköpfe und Ventilkipphebel einbauen und Ventilspiel einstellen
Die Zylinderkopf-Befestigungsbolzen werden in die rechte und linke Reihe des Zylinderblocks eingeschraubt, nachdem zuvor die Gewindelöcher für die Stehbolzen im Block mit Dieselöl geschmiert wurden
Die Bolzen werden über die gesamte Gewindelänge mit einem Drehmoment von 80-100 Nm (8-10 kgcm) eingeschraubt; Sie sollten 122 mm über die Blockebene hinausragen, was mit einer Buchse überprüft wird (Abb. 1).
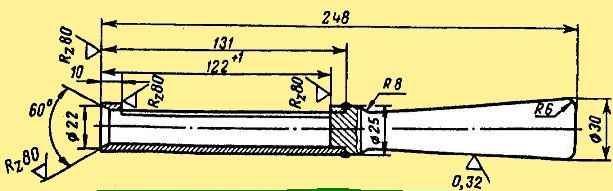
Vor dem Einbau des Zylinderkopfes muss die Passebene abgewischt werden.
Wir montieren die Zylinderkopfdichtung so auf den Stehbolzen, dass sie auf den Stiften sitzt, und die Kante der Dichtung wird auf die Kragen der Zylinderlaufbuchsen gelegt.
Die Zylinderkopfbaugruppe muss frei und ohne Stöße auf die Stehbolzen und Fixierstifte passen.
Dann schrauben wir die Zylinderkopfmuttern auf die Stehbolzen und ziehen sie fest.
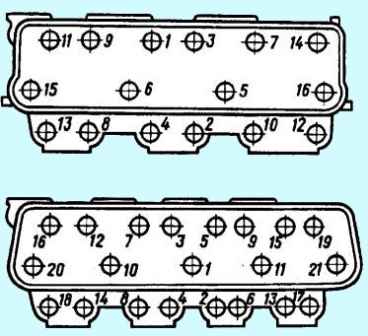
Ziehen Sie die Muttern in aufsteigender Reihenfolge der Zahlen an (siehe Abb. 2).
Nach dem ersten Anziehen mit einem Drehmomentschlüssel muss das erforderliche Drehmoment von 220–250 Nm (22–25 kgcm) an jeder Mutter erneut überprüft werden, wobei die angegebene Reihenfolge einzuhalten ist.
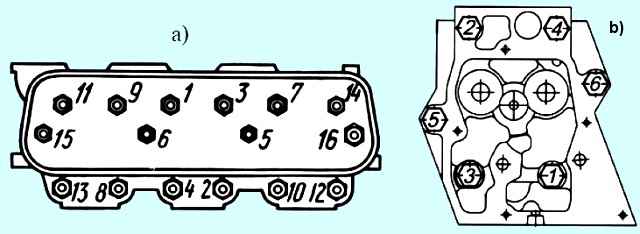
Stößelstangen werden in den Fenstern des Zylinderblocks installiert und gleichzeitig wird die Spitze der Stange mit der Ferse des Stössels ausgerichtet.
Die Stange wird zuerst abgewischt und die Spitze mit Dieselöl geschmiert.
Die rechten und linken Ventilkipphebel mit der Achsbaugruppe werden so montiert, dass die Achspassstifte in die Löcher im Zylinderkopf passen und die Kugel der Einstellschraube mit der Spitze der Stange ausgerichtet ist.
Die Einstellschraube muss bis zum Anschlag in die Wippe eingeschraubt werden.
Schrauben Sie dann die Befestigungsschrauben der Kipphebelachse in die Zylinderköpfe und ziehen Sie sie mit einem Drehmoment von 120–150 Nm (12–15 kgcm) fest.
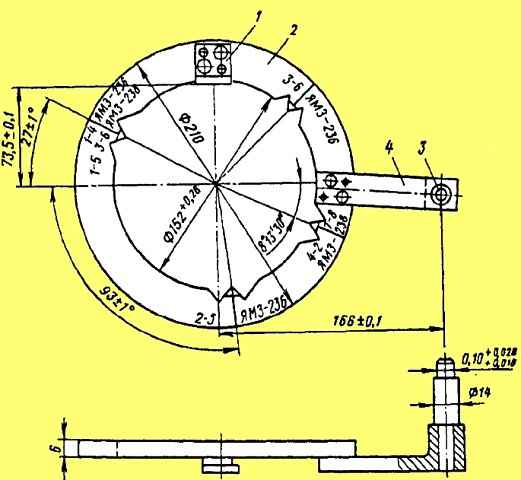
Das Ventilspiel wird an zwei Zylindern gleichzeitig eingestellt und ein Einstellrad verwendet (Abb. 4).
Das Zifferblatt wird an der Kurbelwellenriemenscheibe angebracht und Stift 3 wird in das Gewindeloch an der Steuerradabdeckung eingeführt.
Die thermischen Abstände des YaMZ-326-Motors werden in der folgenden Reihenfolge angepasst:
- Drehen Sie die Kurbelwelle mit einem Schraubenschlüssel mithilfe der Befestigungsschraube der Riemenscheibe im Uhrzeigersinn, beobachten Sie die Bewegung des Einlassventils des ersten Zylinders und stellen Sie den Moment ein, in dem es vollständig geschlossen ist.
Danach wird die Welle in die gleiche Richtung gedreht, bis die Markierungen auf der Kurbelwellenriemenscheibe mit der Markierung 1-4 YAM3-236 auf dem Zifferblatt übereinstimmen;
- Stellen Sie den Abstand zwischen den Spitzen der Kipphebel und den Enden der Ventile des ersten und vierten Zylinders ein.
Nach dem Anziehen der Kontermutter der Einstellschraube sollte die 0,25 mm dicke Fühlerlehre frei in die 0,30 mm dicken Lücken passen – mit Kraft.
Nach dem Drehen der Kurbelwelle darf der Spalt um 0,20 bis 0,35 mm verändert werden.
- Kombinieren Sie beim Kompressionshub in der Reihenfolge der Betätigung der Zylinder (1-4-2-5-3-6) die Markierung auf der Riemenscheibe mit den Markierungen 1-4, 2-5, 3-6 YaMZ- 236 auf dem Zifferblatt, passen Sie die Abstände für die verbleibenden Zylinder an.
Beim Anpassen der thermischen Abstände des YaMZ-238-Motors werden die gleichen Techniken und Methoden wie beim YaMZ-236-Motor verwendet:
- - Kombinieren Sie die Abbildung 3 auf der Riemenscheibe beim Kompressionshub mit der Markierung 1-5 YaMZ-238 auf dem Gliedmaßen;
- - Stellen Sie das Ventilspiel des ersten und fünften Zylinders ein;
Kombinieren Sie beim Kompressionshub in der Reihenfolge der Betätigung der Zylinder (1-5-4-2-6-3-7-8) die Markierung auf der Riemenscheibe mit den Markierungen 4-2, 6-3 und 7- 8 YaMZ-238 auf dem Zifferblatt, regulieren Sie die Ventile der verbleibenden Zylinder.
Die Stößelstangen des Steuerventils müssen sich frei von Hand drehen lassen.
Der Spalt wird mit einer Einstellschraube eingestellt; Befestigen Sie die Schraube nach der Einstellung sicher mit einer Mutter und prüfen Sie den Spalt.
Einbau von Einspritzdüsen, Kraftstoffleitungen und Verbindungsrohr.
Am Motor ist ein Satz Einspritzdüsen derselben Sprühgruppe installiert.
Die Sprühgruppe wird auf die Oberfläche des Düsenkörpers aufgebracht.
Bevor Sie die Düsen installieren, wischen Sie die Innenfläche der Gläser ab und legen Sie eine Kupfer-Dichtungsscheibe auf das Spritzgerät.
Die Einspritzdüsen werden so eingebaut, dass die passende Dichtung in die Aussparung des Zylinderkopfes passt.
Einspritzdüsen-Befestigungshalterungen werden auf den Zylinderkopfbolzen montiert, Unterlegscheiben aufgesetzt und Muttern eingeschraubt, die mit einem Drehmoment von 50–60 Nm (5–6 kgf·m) angezogen werden.
Ablassrohre werden am linken und rechten Zylinderkopf installiert, nachdem zuvor die Transportstopfen von den Einspritzdüsen entfernt wurden.
Abflussrohre werden mit Verbindungsmuttern und -schrauben an den Düsen befestigt, nachdem zuvor Unterlegscheiben unter die Rohrspitzen und unter die Köpfe der Schrauben gelegt wurden.
Um in allen Fällen eine zuverlässige Abdichtung zu gewährleisten, ist es notwendig, die Unterlegscheiben so auszurichten, dass die Kegelspitzen von den Rohrspitzen nach außen weisen.
Kraftstoffauslassleitungen werden im Sturz zwischen den Zylindern verlegt und am rechten und linken Zylinderkopf verschraubt.
Um eine stabilere Befestigung zu gewährleisten, wird an jeder Kraftstoffleitung eine Schelle angebracht und am Flanschbolzen des linken Ansaugrohrs befestigt.
Hochdruck-Kraftstoffleitungen werden in einer bestimmten Reihenfolge an die Anschlüsse der Hochdruck-Kraftstoffpumpe und der Einspritzdüsen angeschlossen, entsprechend der Betriebsreihenfolge der Abschnitte der Hochdruck-Kraftstoffpumpe.
Die Betriebsreihenfolge der YaMZ-236-Motorpumpe entspricht der Betriebsreihenfolge der Motorzylinder (1-4-2-5-3-6).
Die Betriebsreihenfolge der Pumpenabschnitte des YaMZ-238-Motors unterscheidet sich von der Betriebsreihenfolge der Zylinder dieses Motors.
Wenn die Betriebsreihenfolge der Motorzylinder 1-5-4-2-6-3-7-8 ist, dann arbeiten die Pumpenabschnitte in der Reihenfolge 1-3-6-2-4-5-7- 8.
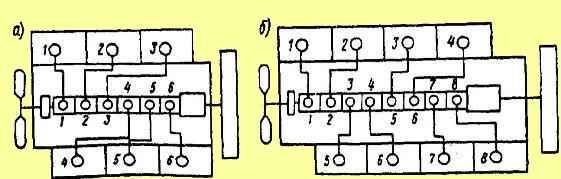
Die Anschlusspläne der Pumpenabschnitte mit den Zylindern der YaMZ-236- und YaMZ-238-Motoren sind in Abb. dargestellt. 5.
Das Verbindungsrohr der Ansaugrohre wird so montiert, dass der Flansch für den Kompressorluftkanal zur Vorderseite des Zylinderblocks zeigt.
Das Rohr wird an den Flanschen der Einlassleitungen befestigt, nachdem zuvor Dichtungen mit zusammengebautem Netz und Gummidichtungen auf die Flansche gelegt und mit Schrauben und Unterlegscheiben befestigt wurden.
Der Ölmessstab wird nach vorherigem Abwischen in das Führungsrohr eingebaut.
Anschließend montieren Sie die Zylinderkopfhauben, die mit Schrauben an einem oder zwei Gewinden befestigt sind, und nehmen den Motor vom Ständer ab.
Dübel werden in die technologischen Löcher eingebaut und mit Schrauben befestigt.
Unter den Dübeln müssen Abstandshalter aus Pappe angebracht werden.
Das Einfahren und Testen der Motoren nach der Reparatur erfolgt auf STE-160-1500-Ständern mit elektrischen Bremsen.
An diesen Ständen können Sie YaMZ-236- und YaMZ-238-Motoren aller Modifikationen testen.
Die Eigenschaften der elektrischen Bremsen für Prüfstände sind in der Tabelle angegeben
Elektrische Bremse AKB-104-4:
- - Leistung 160 kW;
- - Synchrondrehzahl 1500 min -1;
- - Drehmoment 1070 Nm (107 kgcm);
- - maximale Motorkurbelwellendrehzahl beim Betrieb im Generatormodus mit Nenndrehmoment - 3000 min -1
Elektrische Bremse AK-102-4:
- - Leistung 160 kW;
- - Synchrondrehzahl 1500 min -1;
- - Drehmoment 1100 Nm (110 kgcm);
- - maximale Motorkurbelwellendrehzahl beim Betrieb im Generatormodus mit Nenndrehmoment - 2500 min -1
Der Einlauf- und Prüfstand des Motors muss über die erforderliche Ausrüstung verfügen, um die Motorleistung, die Kurbelwellendrehzahl, den stündlichen Kraftstoffverbrauch, die Temperatur des aus dem Motor austretenden Wassers (aus den rechten und linken Wasserleitungen) und die Öltemperatur im Motorsumpf zu messen , Drucköl in der Leitung, Vorwinkel der Kraftstoffeinspritzung in Grad Kurbelwellendrehwinkel.
Der Kraftstoffverbrauch sollte auf einer Waage mit einer Messgrenze von bis zu 15 kg gemessen werden, die Zeit wird mit einer Stoppuhr mit einem Teilungswert von 0,1 s gezählt; Messung der Drehzahl – mit einem manuellen Tachometer oder Tachoskop mit einem Teilungswert von nicht mehr als 10 Minuten.
Das Fassungsvermögen des Vorratstanks muss 10 - 12 l betragen, der Pegel des Messtankbodens muss mindestens 500 mm von der Achse des Einlasses der Kraftstoffpumpe entfernt sein, der Innendurchmesser des Einlasses und Auslasses muss mindestens 500 mm betragen Kraftstoffleitungen müssen mindestens 8 mm dick sein.
Brennstoffleitungen dürfen den Messtank nicht berühren und dürfen bis zu einer Tiefe von höchstens ⅓ der Höhe des Tanks ab seinem Boden in Kraftstoff eingetaucht sein.
Am eingetauchten Ende der Kraftstoffleitung, die den Kraftstoff vom Motor wegführt, ist ein Reflektor installiert, der die direkte Richtung des Strahls verhindert Der Kraftstoff fließt zum Boden des Tanks und trägt dazu bei, die Temperatur des Kraftstoffs im Tank auszugleichen.
Der auf dem Stand installierte Motor muss vollständig sein (mit Ausnahme von Lüfterrad, Generator, Kompressor).
Der Motor wird mit Dieselkraftstoff der Klasse L eingefahren und getestet.
Während der Einlaufphase wird Dieselöl bis zur oberen Markierung der Ölstandsanzeige in die Motorwanne, das Gehäuse der Einspritzpumpe und das Reglergehäuse eingefüllt.
Die Luftfilter sind mit Dieselöl in einer Menge von 1,6 Litern für den YaMZ-236-Motor und 1,4 Litern für den YaMZ-238-Motor gefüllt.
Die Öltemperatur wird durch technologische Ölkühler aufrechterhalten (zu Beginn des Einlaufs nicht unter 50 °C).
Das Einfahren und Testen des Motors erfolgt in speziellen Modi und umfasst Kalt- und Heißeinfahren sowie Kontrollabnahme.
Kalter Motor läuft
Vor dem Starten des Ständers muss die Kurbelwelle mehrmals von Hand gedreht werden, um sicherzustellen, dass der Motor in gutem Zustand ist und korrekt auf dem Ständer montiert ist, und um die thermischen Spiele im Ständer zu überprüfen und gegebenenfalls anzupassen Ventilmechanismus.
Während des Einlaufvorgangs werden der Öldruck im System, die Ölversorgung der Kipphebellager und die Dichtheit der Einspritzventildichtungen in den Zylinderköpfen überprüft.
Das Stethoskop wird verwendet, um auf Geräusche und Schläge von Steuerrädern, Pleuel- und Hauptlagern, Kolbenbolzen und Kolben zu achten.
Bei festgestellten Mängeln muss der Einlauf gestoppt und nach der Beseitigung fortgesetzt werden.
Der Kaltlaufmodus ist in der Tabelle dargestellt.
Am Ende der Kalteinfahrphase wird empfohlen, das Öl in der Motorwanne zu wechseln und die Ölfilter zu waschen.
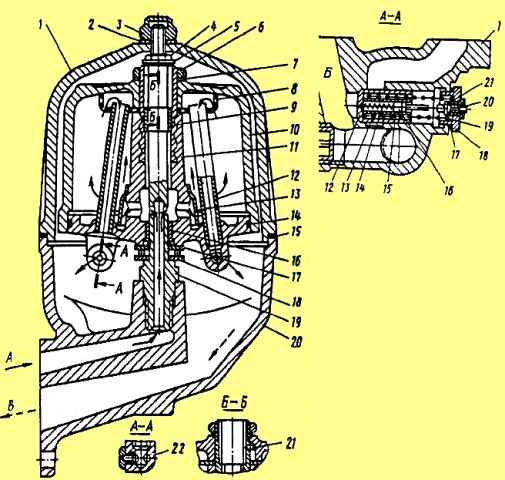
Um den Zentrifugalfilterrotor zu waschen, schrauben Sie die Mutter 3 (siehe Abb. 6) der Filterkappe ab, entfernen Sie Kappe 1 und die Rotorbaugruppe.
Der Rotor wird zerlegt, Sedimente werden von der Kappe 10 und dem Rotor 11 entfernt und in Dieselkraftstoff gewaschen.
Der Zusammenbau des Filters erfolgt in umgekehrter Reihenfolge. Dabei werden der Zustand der Dichtung 15, die Sauberkeit der Düsenlöcher 22, der Zustand der Unterlegscheibe 2 und die Position des Netzes 8 überprüft.
Um den Grobölfilter zu waschen, müssen Sie das Öl aus dem Filtergehäuse durch das mit Stopfen 2 verschlossene Loch ablassen (siehe Abb. 7), die Schraube 11 lösen, mit der die Filterkappe befestigt ist, und die Kappe 7 oben entfernen Abdeckung 8 und das Filterelement 5.
Das aus dem Motor ausgebaute Filterelement wird 3 Stunden lang in ein Bad mit einem Lösungsmittel (Benzin oder Tetrachlorkohlenstoff) gelegt.
Nach 3 Stunden wird das Element mit einer weichen Haarbürste gewaschen, in sauberem Benzin oder Tetrachlorkohlenstoff gespült und mit Druckluft ausgeblasen.
Während der Waschzeit werden technologisch austauschbare Filterelemente installiert.
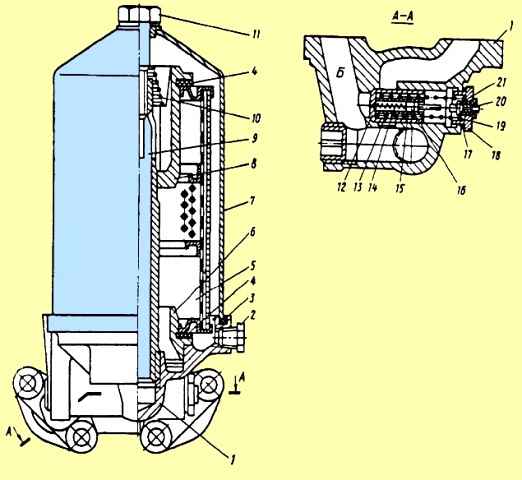
Kaltlaufmodus des Motors
Kaltlaufmodus der Motoren YaMZ-236, YaMZ-238, YaMZ-2Z8A, YaMZ-238G, YaMZ-238K
Kurbelwellendrehzahl, min -1 / Einlaufzeit des Motors, min:
- 600 / 10;
- 800 / 10;
- 1000 / 5;
- 1500 / 5
- insgesamt / 40
Kaltlaufmodus der YaMZ-238I-Motoren
- 600 / 10;
- 800 / 15;
- 1000 / 15;
- 1500 / -
- insgesamt / 40
Heißer Motoreinlauf
Vor dem Anlassen des Motors muss der Vorwinkel der Kraftstoffeinspritzung eingestellt werden.
Überprüfen Sie dazu die relative Position der Markierungen auf der Kupplung für die Kraftstoffeinspritzung und der Antriebshälfte der Antriebswellenkupplung der Kraftstoffpumpe (die Markierungen sollten auf einer Seite liegen);
- - Entfernen Sie das Hochdruckrohr des ersten Abschnitts der Einspritzpumpe;
- - Am Anschlussstück des ersten Abschnitts der Pumpe ist ein Momentoskop angebracht.
Nachdem Sie sichergestellt haben, dass sich die Reglerhalterung in der Position „Kraftstoffzufuhr eingeschaltet“ befindet, pumpen Sie mit einer manuellen Druckerhöhungspumpe 2–3 Minuten lang Kraftstoff in das Motorstromversorgungssystem und drehen Sie die Motorkurbelwelle im Uhrzeigersinn (vom Lüfter aus gesehen), bis Kraftstoff erscheint im Glasrohr .
Sie können die Kurbelwelle mit der Schraube drehen, mit der die Kurbelwellenriemenscheibe befestigt ist, oder mit einem Brecheisen, indem Sie die Löcher im Schwungrad verwenden, wenn der Lukendeckel des Schwungradgehäuses entfernt ist.
Als nächstes gießen Sie überschüssigen Kraftstoff aus dem Glasröhrchen, schütteln Sie ihn mit dem Finger, drehen Sie die Kurbelwelle etwa 118 Umdrehungen gegen den Uhrzeigersinn und überwachen Sie sorgfältig den Kraftstoffstand im Glasröhrchen, indem Sie die Kurbelwelle langsam im Uhrzeigersinn drehen.
Sobald sich der Kraftstoffstand im Rohr zu bewegen beginnt, stoppen Sie die Drehung der Welle und überprüfen Sie die relative Position der Markierungen:
- Die Markierung auf der Kurbelwellenriemenscheibe sollte mit der Markierung mit der Nummer 20 auf der Abdeckung 1 des Steuerzahnrads (Abb. 8, a) übereinstimmen oder die Markierung mit der Nummer 20 auf dem Schwungrad 4 sollte mit dem Zeiger übereinstimmen 3 am Schwungradgehäuse (Abb. 8, b) .
Für den YaMZ-238K-Motor werden die Einstellmarkierungen mit Markierung 14 kombiniert.
Wenn die Markierungen in dem Moment, in dem sich der Kraftstoff im Rohr zu bewegen beginnt, noch nicht übereinstimmen, müssen die Schrauben gelöst, die Antriebswellenkupplung an ihrem Flansch entgegen der Drehrichtung gedreht und die Befestigung festgezogen werden Ziehen Sie die Schrauben fest und überprüfen Sie den Einspritzzeitpunkt erneut.
Die Abweichung zwischen den Noten sollte nicht mehr als eine Teilung betragen.
Wenn das Risikorohr in dem Moment, in dem sich der Kraftstoff in Bewegung setzt, die ausgerichtete Position bereits überschritten hat, muss die Antriebsrollenkupplung in ihre Drehrichtung gedreht werden.
Die Verschiebung der Antriebswellenkupplung relativ zu ihrem Flansch um eine Teilung entspricht vier Teilungen am Schwungrad oder am Steuerraddeckel.
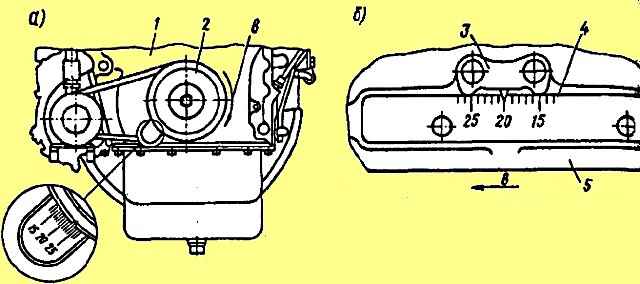
Überprüfen Sie nach dem Starten des Motors die Dichtheit aller Anschlüsse des Kraftstoffsystems des Motors.
Die Temperatur des aus dem Motor austretenden Wassers sollte 75–95 °C betragen, während der Temperaturunterschied des aus dem rechten und linken Rohr austretenden Wassers 5 °C nicht überschreiten sollte.
Es wird empfohlen, die Temperatur mithilfe eines Prozesskühlers innerhalb der angegebenen Grenzen zu halten.
Der Öldruck in der Leitung sollte bei einer Temperatur von 80–90 °C 0,5–0,7 MPa (5–7 kgf/cm 2) bei Nenndrehzahl der Kurbelwelle und nicht weniger als 0 betragen .1 MPa (1 kgf/cm 2) bei einer Rotationsgeschwindigkeit von 500 min -1.
Das Austreten und Austreten von Öl, Wasser und Kraftstoff sowie das Durchbrechen von Gasen an den Verbindungsstellen sind nicht zulässig.
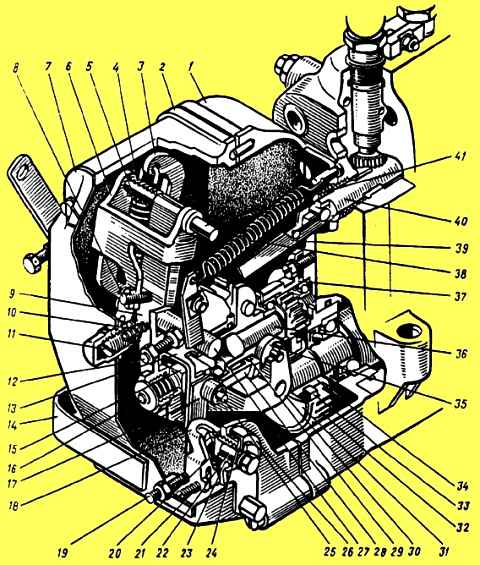
Nockenwellen-Drehzahlregler: 1 Gehäuse; 2, 7, 26 - Abdeckungen; 3, 9, 17 - Hebel; 4 - Ausgleichsfeder; 5, 10, 23. 24, 38 – Federn; 6 - Doppelarmhebel; 8 - Einstellschraube; 11 - Pufferfedergehäuse; 12 - Einstellschraube; 13 - Ohrring; 14 - Halterung; 15 - hartnäckiger Absatz; 16 - Korrektor; 18 - Kordelzug; 19 - Leistungseinstellschraube; 20 - Klemme; 21 - Kipphebelschraube; 22-Achse der Szenen; 25 - Achse der Schubferse; 27 - Hebelwelle; 28 - Frachtkupplung; 29 - Kugel; 30 - laden; 31 - Flansch der Antriebsradbuchse; 32 - Antriebsrad; 33 - Cracker; 34 - Buchse; 35-Rolle; 36 - Gewichtshalterrolle, 37 - Glas; 39 - Traktion; 40 - Schiene; 41 - Hebelachse
Anzeichen für Mängel sind kein Schwitzen, die Bildung von Ölflecken und einzelne Tropfen an den Stellen der Stopfbuchsdichtungen, wobei in jedem Motorbetriebsmodus innerhalb von 5 Minuten nicht mehr als ein Tropfen fallen darf;
- - leichtes Schwitzen ohne Tropfenbildung an Anschlüssen und Anschlüssen;
- - Abgabe von Öl und Kondensat durch das Auslassrohr des Kurbelgehäuseentlüftungssystems in einer Menge von nicht mehr als zwei Tropfen pro Minute bei Nenndrehzahl der Kurbelwelle;
- - Abgabe von Kraftstoff durch das Abflussrohr der Einspritzdüsen in Form von Tropfen sowie einer Mischung aus Kraftstoff und Öl aus dem Abflussrohr des Einspritzpumpengehäuses;
- - Die Freisetzung von Wasser und Schmiermittel aus der Ablassöffnung der Wasserpumpe beträgt nicht mehr als einen Tropfen pro 3 Minuten, ebenso wie Wassertropfen, wenn der Motor gestoppt ist;
- - leichtes Schwitzen, ohne dass Öl durch Mikroporen an der Ringrippe des Zylinderkopfes tropft.
Während der Einlaufphase dürfen einzelne Tropfen des Kraftstoff-Öl-Gemisches aus dem Auspuffrohr austreten.
Der Heißlauf der Motoren erfolgt in den in der Tabelle angegebenen Modi
Go-Modus Heißeinlauf von Motoren
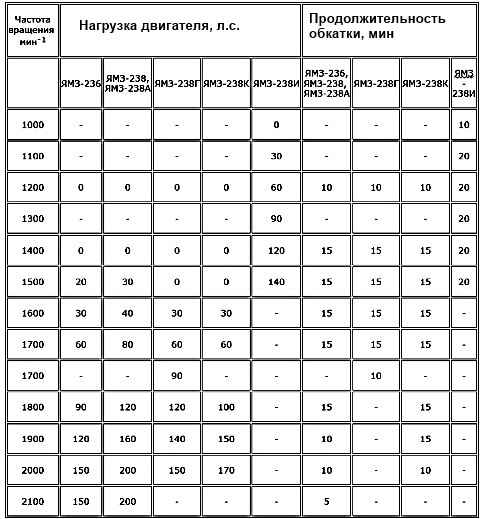
Am Ende des Heißlaufs ist es notwendig, die Motorleistung zu überprüfen und gegebenenfalls anzupassen.
Die Leistung des YaMZ-236-Motors bei einer Kurbelwellendrehzahl von 2050+15 min sollte 178 -5 Liter betragen. Mit. Bei einem stündlichen Kraftstoffverbrauch von 33 kg/h beträgt der YaMZ-238-Motor 237,5 Liter. Mit. bei 44 kg/h, YaMZ-238A – 213-5 PS. bei 39 kg/h, YaMZ-238G bei einer Drehzahl von 1670 min -1 - 172-5 l. Mit. und stündlicher Kraftstoffverbrauch von 30,1 kg/h, YaMZ-238I – nicht weniger als 160 Liter. Mit. bei einer Drehzahl von 1500 min und 27 kg/h, YaMZ-238K – 190-5 PS. bei einer Drehzahl von 2100 min -1 und einem stündlichen Kraftstoffverbrauch von 36 kg/h.
Der stündliche Kraftstoffverbrauch wird durch dreimaliges Messen der Verbrauchszeit von 500 g Dieselkraftstoff ermittelt.
Der größte Unterschied zwischen wiederholten Messungen sollte nicht mehr als ±0,2 s relativ zum durchschnittlichen Zeitwert aller Messungen betragen.
Die Motorleistung wird mit der Leistungseinstellschraube 19 (siehe Abb. 9) bei der oben für jeden Motor angegebenen Kurbelwellendrehzahl und dem auf der Höchstgeschwindigkeitsbegrenzungsschraube ruhenden Reglerhebel eingestellt.
Last sanft auf Null reduzieren, maximale Leerlaufdrehzahl anpassen:
- - für Motoren YaMZ-236, YaMZ-238, YaMZ-238A und YaMZ-238K - 2200-2275 min -1 ;
- - für den YaMZ-238G-Motor – 1850-1950 min1 ;
- - Beim YaMZ-238I-Motor sollte die maximale Kurbelwellendrehzahl im Leerlauf die Nenndrehzahl nicht um mehr als 100 Minuten überschreiten.
Die Überprüfung der maximalen Drehzahl erfolgt, indem der Hebel auf dem Bolzen zur Begrenzung des Maximalgeschwindigkeitsmodus aufliegt und das Gehäuse der Pufferfeder 10-11 mm aus dem Ende der Sicherungsmutter herausgedreht wird.
Wenn die maximale Kurbelwellendrehzahl im Leerlauf der Motoren YaMZ-236, YaMZ-238, YaMZ-238A und YaMZ-238K unter 2225 min -1 liegt, bestimmen Sie den Wendepunkt Drehzahlkennlinie, die im Bereich 2100 +50 min -1
liegen sollte
Die minimale Kurbelwellendrehzahl im Leerlaufmodus wird innerhalb von 450-550 min1 eingestellt, wobei der Reglersteuerhebel auf der Schraube ruht.
Beim Eindrehen einer Schraube erhöht sich die Frequenz, beim Herausdrehen verringert sie sich.
Zuerst wird die Rotationsgeschwindigkeit schrittweise reduziert, bis Instabilität auftritt, und dann wird das Pufferfedergehäuse eingeschraubt, bis die Rotationsgeschwindigkeit um 10–20 Minuten zunimmt -1.
Der Motor muss im Leerlauf stabil laufen, mit Schwankungen von nicht mehr als 15 Minuten -1.
Die Stabilität in diesem Modus wird überprüft, indem die Kurbelwellendrehzahl auf 1200–1300 min -1 erhöht und der Hebel kräftig bis zum Bolzen 1 losgelassen wird.
Für den YaMZ-238I-Motor wird das Ausmaß der Drehzahlinstabilität (Abweichung vom Normalzustand) überprüft, die ± 15 min -1 bei 80 PS, 120 PS und 150 PS nicht überschreiten sollte .
Danach ziehen Sie die Zylinderkopfmuttern fest und stellen ggf. das Ventilspiel ein.