Zweiachsiger Sattelanhänger (Abb. 1) für allgemeine Zwecke, mit einer Tragfähigkeit von 20 Tonnen, mit offener Plattform, mit klappbaren Seiten- und Rückwänden aus Metall
Um die Ladung vor Niederschlag zu schützen, wird eine Markise mit Gestell montiert. Der Sattelanhänger ist für den Einsatz auf Straßen der Kategorien I und II ausgelegt.
Der Durchmesser des Kupplungsbolzens beträgt 50,8 mm.
Das Hauptzugfahrzeug zum Abschleppen ist der Traktor MAZ-504V.
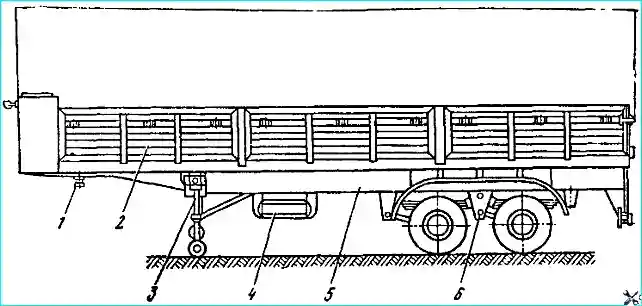
Der Sattelaufliegerrahmen ist geschweißt und besteht aus Längsträgern, Seitenträgern, Querträgern, einem Sicherheitspuffer und Konsolen zur Befestigung der Aggregate.
Das beste Verhältnis zwischen Biegefestigkeit und Gewicht weisen Seitenteile mit I-Profil auf. Durch die Verwendung geschweißter Seitenteile im Vergleich zu gewalzten Teilen kann der Querschnitt an Stellen mit geringerer Belastung reduziert werden, während gleichzeitig die Festigkeit gewährleistet und das Gewicht reduziert wird.
Auf Grundlage dieser Überlegungen wurden die Seitenteile des Sattelanhängers MAZ-5205A hergestellt.
Die Verjüngung der Längsträger in der Höhe oberhalb der Sattelkupplung der Zugmaschine wird durch eine Rollplatte ausgeglichen, die die Steifigkeit und Festigkeit des Rahmenprofils erhöht.
Zusätzlich ist die Stelle des Übergangs vom verengten Teil des Seitenteils zum mittleren Teil durch das Anschweißen einer Verkleidung an die untere Ablage verstärkt.
Die Querträger oberhalb der Rollplatte sind sowohl mit der Platte als auch mit den Seitenteilen verschweißt, wodurch die Möglichkeit einer Verbiegung der Platte durch die Sattelkupplung der Zugmaschine ausgeschlossen wird.
Zwischen den Querträgern ist an der Rollplatte eine Buchse zur Befestigung eines Königszapfens angeschweißt.
Die Mittelquerträger dienen der Verbindung der Längsträger und sorgen für eine gleichmäßige Verteilung der Torsionsspannungen, verleihen den Längsträgerwänden gleichzeitig Steifigkeit und dienen der Bodenbefestigung.
Auskragende, gestanzte Querträger in variabler Höhe verbinden die Längsträger mit den Seitenträgern des Rahmens. Dabei kommt ein gewalztes U-Profil mit einem Querschnitt von 140x60x6 mm aus 09G2-Stahl zum Einsatz.
Halterungen zur Befestigung von Stützvorrichtungen, Federung, Bremse und elektrischer Ausrüstung sind am Rahmen angeschweißt.
Das hintere Ende des Rahmens ist mit einem Sicherheitspuffer und Abschleppösen ausgestattet.
Der vordere Querträger des Rahmens ist ein gestanzter U-Profilabschnitt in Kugelform, um die Festigkeit der Befestigung und die Steifigkeit der Vorderseite der Plattform zu erhöhen.
Bevor die Längsträger in der Höhe verjüngt werden, wird an ihnen ein Rahmen zur Befestigung stationärer Stützvorrichtungen angeschweißt, der aus einem Querträger und Längsquerstreben besteht.
Die Halterungen für die Reserveradhalterung sind am rechten Längsträger im Vorderwagen angeschweißt.
Zur Montage der Plattformpfosten sind an den Seitenträgern zwei Muffen angeschweißt, deren Seiten an den Trägern, vorderen und hinteren Querträgern befestigt werden.
Der Plattformboden ist an den Balken und Querstreben des Rahmens befestigt.
Der Rahmen ist somit zugleich die Basis der Sattelaufliegerplattform.
Die wichtigsten tragenden Teile des Rahmens bestehen aus niedriglegiertem Stahl, was eine gute Schweißbarkeit und Leistung in allen Klimazonen gewährleistet.
Im mittleren Teil des Rahmens (entlang der Länge) ist die Querstrebe mit den Seitenteilen nur an deren Wänden verschweißt, was eine zuverlässige Verbindung und Torsionsbeständigkeit gewährleistet.
Die Abschlepphaken sind am Heckteil, an der Innenseite der Längsträger, angeschweißt.
Der vordere Teil des Sattelanhängerrahmens ist mit Anschlussmaßen gemäß GOST 12105-74 gefertigt, d. h. die Kontur von der Achse des Kupplungsbolzens nach vorne passt in einen Radius mit einer Größe von 1680 mm und geht vom Bolzen bis zu den Stützvorrichtungen über den Radius mit einer Größe von 1900 mm hinaus, was die Haftung des Sattelanhängers MAZ-5205A an allen zweiachsigen Sattelzugmaschinen gewährleistet.
Der Sattelzug-Königszapfen wird in die Aufnahme eingepresst und mit Kronenmutter und Splint gesichert. Der Durchmesser des Königszapfens für die Sattelkupplungsgriffe der Zugmaschine beträgt 50,8 mm.
Die Wartung und Reparatur des Rahmens ähnelt der Wartung und Reparatur des Rahmens des Sattelaufliegers MAZ-5245.
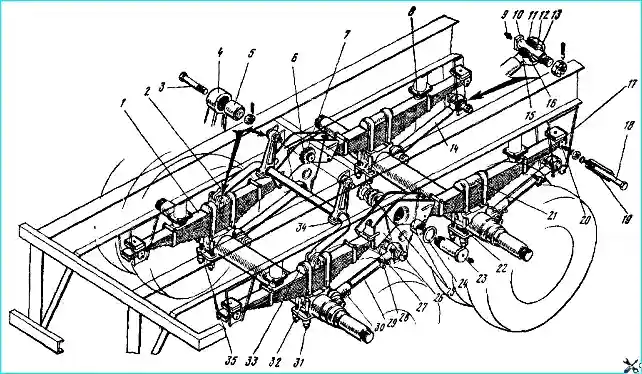
Aufhängevorrichtung
Aufgrund der Geschwindigkeitssteigerung der Fernverkehrszüge und einer deutlichen Erhöhung der Ladekapazität sind die Anforderungen an die Federung von Sattelaufliegern gestiegen.
Für die Sicherheit des Transportgutes bei unterschiedlicher Beladung spielt die Laufruhe der Federung eine wichtige Rolle.
Die genannten Anforderungen werden durch eine Vierfeder-Schwebebalkenfederung erfüllt, die an zweiachsigen Sattelanhängern verbaut ist (Abb. 2).
Der Wechsel der asymmetrischen halbelliptischen Federn 1 mit gleitenden Enden, die eine möglichst gleichmäßige Änderung der Federungssteifigkeit je nach Belastungsgrad und Unebenheit der Straßenoberfläche ermöglichen, erforderte die Einführung von Reaktionsstangen 14, 29 zur Übertragung der Schubkräfte auf die Räder und der Bremsmomente von diesen auf den Rahmen.
Die Gleichmäßigkeit der Belastung der Achsen wird durch einen gleichschenkligen Ausgleichsbalken 26 gewährleistet, der die kurzen Enden der Federn umfasst.
Bei Beladung des Sattelanhängers bis zur maximal zulässigen Gesamthöhe wird die Seitenstabilität durch den Einbau von Gummipuffern 8 über jeder Feder und jedem Stabilisator 2 erreicht.
Die Federhalterung und die Ausgleichshalterungen sind gestanzt und geschweißt und mit der unteren Ablage der Seitenteile verschweißt.
Die Enden der Federn gleiten zwischen austauschbaren Linern 17, 20, 27 und Buchsen 19 in Halterungen und Ausgleichsstücken 26, wobei das dritte Hauptblatt an den Enden gebogen ist, um ein Herausrutschen der Federn zu verhindern.
Auswechselbare Liner bestehen aus Stahl St. 3 und sollen die Seitenwangen der Halterungen und Ausgleichswellen vor Verschleiß schützen und den Verschleiß des oberen Hauptblatts der Federn verringern.
Die Federn sind auf an die Achsen geschweißten Polstern montiert und mit zwei Bügeln 32 durch die oberen Polster 21, 33 der Federn und die unteren Polster 22 und 35 befestigt.
Die Reaktionsstangen sind mit Stift 10, einer Mutter und einem Splint an den unteren Belägen und Halterungen des Ausgleichsgetriebes und der Federn befestigt.
Neben der Übertragung von Schubkräften dienen die Reaktionsstangen auch der Regulierung der Position der Radachsen relativ zur Längsachse des Sattelanhängers, wobei zu diesem Zweck an jeder Achse eine der Stangen verstellbar ausgeführt ist.
Die komplexe Kinematik der Bewegung der Reaktionsstangen während des Federungsbetriebs wird durch sphärische Lager 16 (ШС-50) gewährleistet, die in die Köpfe der Reaktionsstangen eingepresst und mit Sicherungsringen 15 befestigt sind.
Die horizontale Bewegung des Stangenkopfes auf der Achse wird durch Buchsen 11 begrenzt.
Dichtungen 13, gesichert durch Federringe 12, schützen die Lager vor Verschmutzung.
Die Schmierung der reibenden Teile der Reaktionsstangen erfolgt über Schmiernippel 9 an den Befestigungsachsen.
Der gleicharmige Waagebalken 26 ist gestanzt, geschweißt, durch ein Scharnier an der Achse 23 an der Halterung befestigt und dreht sich frei in Bronzebuchsen 25.
Um einen Abrieb der Halterungswangen zu verhindern, sind auf beiden Seiten des Balancers Dichtungen 24 angebracht.
Die Schmierung der Buchsen und der Ausgleichswelle erfolgt über den auf der Welle angebrachten Schmiernippel 22.
Die Ausgleichsachse wird mit Muttern 6 und Sicherungsscheibe 7 befestigt, wobei sich der Ausgleicher mit der Kraft der Hand drehen sollte.
Der Stabilisator 2 wird eingebaut, um die Seitenstabilität des Sattelanhängers beim Abbiegen und Spurwechsel zu erhöhen.
Der Stabilisator ist eine Welle mit gebogenen Enden, die mittels Stiften 3 an den oberen Belägen 33 der hinteren Federn befestigt sind.
Die Befestigung am Sattelanhängerrahmen erfolgt über Hebel 4 mit Deckel 34 in Gummi-Metall-Buchsen 5.
Wenn sich die linke und rechte Seite der Aufhängung gleichzeitig und gleichmäßig bewegen, dreht sich der Stabilisator in den Hebeln und beeinträchtigt die Funktion der Aufhängung nicht.
Bei einem Unterschied im Hub der rechten und linken Seite wird das Ende des Stabilisators im Verhältnis zum mittleren Teil der Welle verdreht, wodurch die Steifigkeit der Aufhängung erhöht und der Federweg und damit die seitliche Neigung des Sattelanhängers verringert wird.
Die Gummifederwegbegrenzer 8 (Puffer) tragen neben dem Stabilisator maßgeblich zur Erhöhung der Seitenstabilität des Sattelaufliegers bei.
Bei zunehmender Belastung der Feder, etwa beim Rollen des Aufliegers oder bei Bergauffahrten, verringert der Gummipuffer die aktive Länge der Feder und erhöht dadurch deren Steifigkeit.
Die größte Effizienz des Stabilisators und Federpuffers zeigt sich beim Transport von Ladung mit hohem Schwerpunkt.
Die Wartung der Aufhängung besteht in der Überprüfung der Festigkeit aller Gewindeverbindungen.
Um zu verhindern, dass die Mittelschraube der Federn abgeschnitten wird, müssen die Muttern 31 der U-Bolzen regelmäßig mit einem Anzugsdrehmoment von 60–65 kgf cm angezogen werden, wobei der Sattelanhänger voll beladen sein muss.
Diese Anforderung muss auch erfüllt werden, um den Reifenverschleiß zu reduzieren, der bei Achsfehlstellungen zunimmt.
Das Lösen der Befestigung der Trittleitern führt außerdem zu einer Erhöhung der dynamischen Belastungen der Lager 16 der Reaktionsstangen 14, 29, zu vorzeitigem Verschleiß der Sitzflächen und zur Zerstörung der Lager.
Das Lösen der Muttern der Schrauben, die die Position der Reaktionsstange 29 in den Köpfen 28 und 30 sichern, kann ebenfalls eine Änderung der Position der Achsen bewirken.
Ein knarrendes Geräusch in den Federn deutet auf eine mangelnde Schmierung zwischen den Blättern hin, was die Reibung zwischen den Blättern erhöht und den Verschleiß der Blätter steigert.
Um ein Knarzen der Federn bei der Wartung zu verhindern, sollten die Bleche an den Kontaktstellen untereinander mit einer dünnen Fettschicht bestrichen werden.
Stifte und Achsen zur Befestigung von Aufhängungsteilen und unterliegen im Betrieb einem Verschleiß, der zu dynamischen Stößen in den Verbindungen und zu deren vorzeitigem Ausfall führen kann.
Um die Haltbarkeit der Verbindungen zu erhöhen, ist es notwendig, das Schmiermittel, insbesondere in den Ausgleichsachsen und den Befestigungsbolzen der Drehmomentstangen, regelmäßig zu wechseln und festzuziehen, bis kein axiales Spiel mehr vorhanden ist.
Der Hauptgrund für den Bruch von Federblättern ist eine Überladung des Sattelaufliegers.
Es ist zu beachten, dass ein gebrochenes Federblatt nicht funktioniert und somit die Belastung der verbleibenden Federblätter zunimmt, was zum Bruch der gesamten Feder führen kann.
Besonders gefährlich ist der Bruch der Großschoten, über die die direkte Verbindung zum Rahmen hergestellt wird.
Wenn gerissene Großschoten nicht rechtzeitig ausgetauscht werden, kann es während der Fahrt zu einer Achsdrehung und einem Unfall kommen.
Reparatur
Um die Demontage der Aufhängung zu erleichtern, empfiehlt es sich, Stützböcke unter den Rahmen des Aufliegers zu stellen, nachdem die Federn zuvor vom Eigengewicht des Rahmens entlastet wurden. Heben Sie dazu den vorderen Teil des Aufliegers mit Stützvorrichtungen und den hinteren Teil mit einem Wagenheber (aus dem Traktorsatz) unter den hinteren Puffer.
Um die Feder zu entfernen und zu zerlegen, müssen Sie:
- - Die Muttern der Zugbolzen 18 (siehe Abb. 2) im Ausgleichsgetriebe abschrauben, die Bolzen und Buchsen 19 entfernen;
- - Muttern 31 der Bügel abschrauben, Bügel, obere Polster 21 und 33 der Feder entfernen;
- - Lösen Sie die Muttern der Mittelschraube und der Klemmschrauben, entfernen Sie die Schrauben und Buchsen.
Während des Betriebs kann es an der Feder zu folgenden Problemen kommen: Brüche und Risse in den Blechen, Abscheren des Mittelbolzens, Brüche und Risse in den Klemmen, Verschleiß an den Enden des oberen Hauptblechs, Verschleiß an den Enden der Gegenbleche, Risse in den Bügeln oder Abscheren des Gewindes, Abscheren der Zugbolzen in den Halterungen und im Balancer.
Federblätter mit Rissen oder Abnutzungen größer als 1 mm sollten aussortiert und wenn möglich zu kürzeren Blättern umgearbeitet werden.
Wenn das Ende der oberen Großschot mehr als 60 % seiner ursprünglichen Dicke abgenutzt ist, sollte die Schot ersetzt oder gegen die zweite Großschot ausgetauscht werden.
Bleche mit Restverformung (Durchbiegung) werden auf ihre ursprüngliche Größe gerichtet.
Gebrochene Mittelbolzen und Klemmen sowie Federbügel mit Rissen und ausgerissenen Gewinden unterliegen dem Austausch.
Risse an Klemmen können verschweißt und anschließend bündig mit der Hauptoberfläche gereinigt werden.
Um den Ausgleicher zu entfernen, lösen Sie die Muttern 6 (siehe Abb. 2), mit denen die Ausgleichsachsen befestigt sind, schlagen Sie die Achse 23 heraus, entfernen Sie die Dichtungen 24 und den Ausgleicher 26.
Nach der Demontage müssen die bronzenen Unruhbuchsen von Fett gereinigt und mit Schmirgelleinen geschliffen werden.
Der Arbeitsdurchmesser der Buchse beträgt 90+0,14 mm (es ist zulässig, Buchsen ohne Reparatur mit einem Durchmesser von 90,2 mm zu verwenden). Reinigen Sie die Ausgleichswelle von Rost und Bronzeablagerungen.
Die oberen und seitlichen austauschbaren Liner in den Federhalterungen und im Balancer müssen ausgetauscht werden, wenn sie verschleißen.
Wenn der Austausch nicht rechtzeitig erfolgt, verschleißen die Wände der Halterung und des Ausgleichers. Der zulässige Verschleiß der Wände durch die Dicke beträgt nicht mehr als 2 mm.
Bei stärkerem Verschleiß müssen Halterungen und Ausgleichswelle ausgetauscht oder durch Metallschweißen mit anschließender Reinigung an der Hauptebene repariert werden.
Um den Stabilisator zu entfernen, müssen Sie:
- - Lösen Sie die Schrauben, mit denen die Abdeckungen 34 an den Hebeln 4 befestigt sind, und entfernen Sie die Abdeckungen und Gummimetallbuchsen.
- - Schrauben Sie die Splinte ab und schrauben Sie die Muttern der Stifte 3 ab, die die Hebel 4 an den Halterungen am Rahmen befestigen. Entfernen Sie die Hebel und schlagen Sie die Stifte 4 heraus.
- - Die Splinte abschrauben und die Muttern der Stabilisatorwellen-Befestigungsstifte 2 an den oberen Belägen 33 abschrauben, die Stabilisatorwelle entfernen.
Um die Reaktionsstangen zu entfernen und zu zerlegen, müssen Sie:
- - Die Splinte abschrauben und die Muttern der Stifte 10 abschrauben, die die Reaktionsstangen 14 und 29 sichern, die Stifte herausschlagen, ohne die Gewinde zu beschädigen, die Reaktionsstangen entfernen;
- - Entfernen Sie den Sicherungsring 15 des Kugellagers und drücken Sie das Lager 16 heraus. Dieser Vorgang wird nur empfohlen, wenn das Lager beschädigt ist.
- - Schrauben Sie die Köpfe 28 und 30 der verstellbaren Stangen 29 ab und lösen Sie so die Zugbolzen.
Gummipuffer 8 wird entfernt und ersetzt, wenn er delaminiert oder abgenutzt ist.
Die Montage der Aufhängung erfolgt in umgekehrter Reihenfolge.
Vor der Montage müssen alle Teile in Kerosin gewaschen und mit Druckluft ausgeblasen oder abgewischt und die Passstücke geschmiert werden. Gummibuchsen werden nicht geschmiert.
Beim Zusammenbau ist es notwendig, alle Teile sorgfältig zu befestigen.
Ziehen Sie die Muttern der Federbügel bei geraden Federn fest und achten Sie dabei auf ein Anzugsdrehmoment von 60–65 kgf/cm. Ziehen Sie außerdem die Achs- und Stiftmuttern fest, bis kein axiales Spiel mehr besteht. Die Stabilisatorwelle wird mit den abgeschnittenen Ecken an den Köpfen nach unten eingebaut.
Nach der Montage der Aufhängung ist es notwendig, die Position der Radachsen relativ zur Längsachse des Sattelanhängers einzustellen, wofür:
- - Installieren Sie den Sattelauflieger auf einer ebenen, horizontalen Fläche;
- - Finden und markieren Sie die Position des Achsschenkelbolzenzentrums auf der Baustelle mithilfe eines Lotes;
- - linke und rechte Punkte auf dem vorderen Teil des ersten Achsträgers anbringen, löschen Gemessen von den Bremssattelflanschen im Abstand von 20 ± 1 mm, messen Sie die Abstände vom gefundenen Achsschenkelbolzenmittelpunkt zu den markierten Punkten. Der Größenunterschied sollte 2 mm nicht überschreiten;
- - Installieren Sie die zweite Achse parallel zur ersten, indem Sie die Abstände zwischen ihnen messen und die Positionen der Achsen mit einstellbaren Reaktionsstangen 29 anpassen, indem Sie die Verbindungsschrauben der Köpfe 28 und 80 lösen.
Eine volle Drehung der Stange verlängert oder verkürzt die Reaktionsstange um 3 mm. Nach der Einstellung die Schrauben festziehen.
Um einen minimalen Reifenverschleiß während des Betriebs zu gewährleisten und die Fluchtung der Längsachsen von Auflieger und Zugmaschine bei Geradeausfahrt sicherzustellen, muss die vorgeschriebene Einstellung vorgenommen werden.
Achsen, Naben, Räder und Reifen
Der Sattelauflieger ist mit den gleichen Achsen, Naben, Rädern und Reifen wie der Sattelauflieger MAZ-5245 ausgestattet. Luftdruck in den Reifen 4,3 kgf/cm²
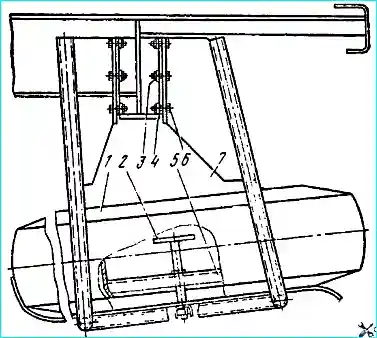
Das Reserverad (Abb. 3) wird mit der Halterung 7 am rechten Seitenteil des Rahmens befestigt. Das Reserverad wird auf der Halterebene montiert und mit Halter 5 und Schraube 2 befestigt.
Um den Kraftaufwand bei der Montage des Reserverades zu reduzieren, empfiehlt sich die Verwendung der im Traktorwerkzeugsatz enthaltenen Montageklingen.
Unterstützungsgerät
Die Stützvorrichtung (Abb. 4) besteht aus zwei Spindelhubelementen, die sich im vorderen Teil des Sattelanhängers befinden und durch eine Zwischenwelle miteinander verbunden sind.
Der rechte Heber der Stützvorrichtung (Abb. 5) unterscheidet sich vom linken durch das Vorhandensein eines zusätzlichen Zweiganggetriebes, das ein beschleunigtes Heben und Senken der Stützvorrichtungsrollen im Leerlauf (bevor die Rollen den Boden berühren) sowie ein Heben und Senken des Sattelanhängers gewährleistet.
Die äußerste obere Position des Stützgeräteständers wird durch die Mutter 5 der Schraube und den Schraubenflansch begrenzt, und die äußerste untere Position wird durch den Begrenzer 2 begrenzt.
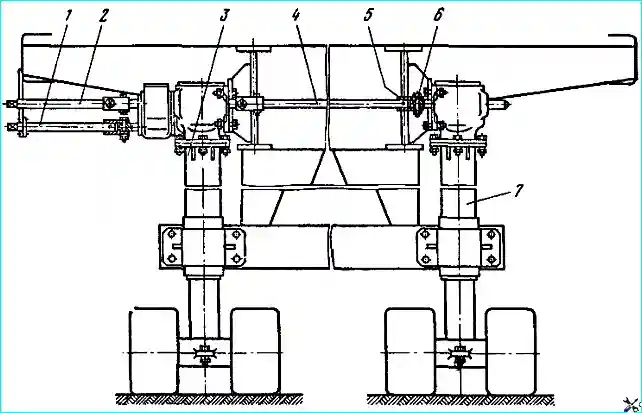
Zum Anheben des Sattelaufliegers ist es notwendig (siehe Abb. 4):
- - Stellen Sie den Sattelauflieger auf eine horizontale Plattform, setzen Sie den Griff auf das Ende der Antriebswelle 2 und - drehen Sie ihn im Uhrzeigersinn, sodass die Rollen der Stützvorrichtung abgesenkt werden, bis sie den Boden berühren;
- - Setzen Sie den Griff auf den Reitstock der Welle 1 des Lastgetriebes und heben Sie den Sattelanhänger an, indem Sie ihn im Uhrzeigersinn drehen. Ein starker Anstieg der Kraft am Griff zeigt an, dass sich der Stützgeräteständer in der Endposition befindet.
Das Absenken des Sattelanhängers bzw. das Zurückbringen der Stützvorrichtung in die Ausgangsposition erfolgt in umgekehrter Reihenfolge.
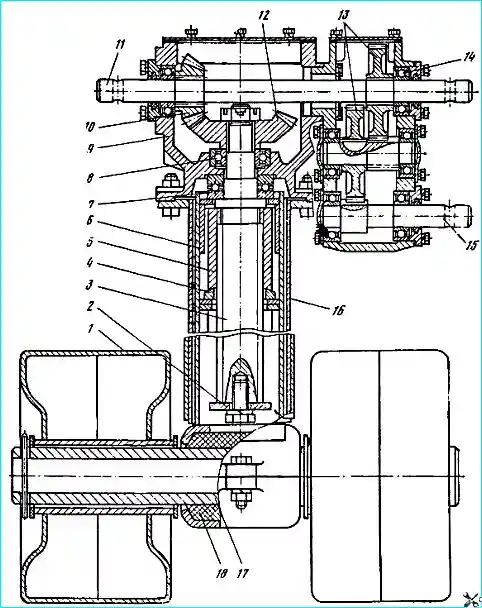
Das Arbeiten im Direktgang nach dem Aufsetzen der Walzen auf den Boden (unabhängig davon, ob der Sattelauflieger beladen oder unbeladen ist) ist nicht zulässig.
In Ausnahmefällen, wenn es notwendig ist, eine Zugmaschine auf unebenem Untergrund von einem Sattelanhänger abzukoppeln (wenn beim Absenken der Stützvorrichtungen die Rollen der linken Stützvorrichtung den Boden berühren und die rechte Stützvorrichtung den Boden nicht mehr als 50 mm erreicht), ist der Sattelanhänger mit der Möglichkeit einer unkoordinierten Bedienung der Stützvorrichtungen ausgestattet.
Um die Rollen der rechten Stützvorrichtung abzusenken, ist es notwendig:
- - Entfernen Sie den Stift 6 (siehe Abb. 4) und senken Sie durch Drehen des Griffs die rechte Stützvorrichtung ab, bis die Rollen den Boden berühren. Setzen Sie dann den Stift an seiner ursprünglichen Stelle ein und sichern Sie ihn mit einem Splint.
- - Durch Drehen des Griffs der Antriebswelle 11 den Sattelauflieger auf die gewünschte Höhe anheben.
Wenn die Rollen der rechten Stützvorrichtung den Boden berührt haben und die linke den Boden nicht mehr als 50 mm erreicht hat, müssen die Rollen der linken Stützvorrichtung in der folgenden Reihenfolge abgesenkt werden:
- - Stift 6 entfernen und durch Drehen der Welle 1 mit dem Griff die rechte Stützvorrichtung um einen Wert, der dem Abstand zwischen dem Boden und den Rollen der linken Stützvorrichtung entspricht, dann Bolzen 6 anbringen und mit einem Splint sichern;
- - Durch Drehen der Antriebswelle mit dem Griff senken Sie die Stützvorrichtung ab, bis sie den Boden berührt, und heben den Sattelanhänger dann auf die gewünschte Höhe an.
Nach dem Ankuppeln des Sattelanhängers an die Zugmaschine müssen die Rollen der Stützvorrichtungen in die Transportposition angehoben und mit der oben beschriebenen Methode ausgerichtet werden.
Das Bewegen eines Sattelaufliegers mit ausgefahrenen Stützvorrichtungen sowie das Rollen des Sattelaufliegers auf den Rollen der Stützvorrichtung ist nicht zulässig.
Zur Wartung der Stützvorrichtung gehört die rechtzeitige Schmierung und Kontrolle der Schraubverbindungen.
Im Winter empfiehlt es sich, beim Parken eines Sattelaufliegers ohne Zugmaschine Holzunterlagen unter die Rollen zu legen, um ein Einfrieren und einen anschließenden Bruch der Stützvorrichtungen zu verhindern.
Mögliche Fehlfunktionen des Unterstützungsgeräts und Methoden zu deren Beseitigung
- Zu viel Kraft auf den Antriebsgriff oder die Welle dreht sich nicht
Fehlendes Spiel beim Gangeinlegen - Spiel einstellen
Fehlendes Spiel im Axiallager durch zu starkes Anziehen der Muttern - Lageranzug anpassen
Reparatur
Die Stützvorrichtung wird üblicherweise zerlegt, um verschlissene oder beschädigte Teile auszutauschen und Schmiermittel hinzuzufügen oder zu ersetzen.
Um die Stützvorrichtung zu demontieren, müssen Sie:
- - Den vorderen Teil des Sattelaufliegers auf die Böcke stellen, die Stützvorrichtungen vom Sattelauflieger trennen und die Rollen entfernen;
- - durch das Loch im Schuh der Stützvorrichtung 6 (siehe Abb. 5) die Schraube des Begrenzers 2 lösen, den Begrenzer entfernen und durch Drehen der Antriebswelle 11 im Uhrzeigersinn die Stütze 6 vom Gehäuse 16 entfernen;
- - Entfernen Sie den Kurbelgehäusedeckel 9 und die Lagerdeckel der Antriebswelle 11. Nehmen Sie die Antriebswelle heraus, nachdem Sie zuvor den Sicherungsring entfernt haben.
- - Mutter der Schraube 3 des Wagenhebers abschrauben, Kegelrad 12 herausnehmen und mit einem Hammer von oben leicht auf das Ende der Schraube klopfen, um es aus dem Gehäuse 16 zu lösen, Axiallager herausnehmen.
Nach der Demontage alle Teile waschen, mit Druckluft ausblasen, großzügig schmieren und die Stützvorrichtung in umgekehrter Reihenfolge wieder montieren.
Nach der Montage den Eingriff der Zahnräder prüfen, ggf. mit Einstellscheiben nachstellen, den Kurbelgehäusehohlraum mit TSIA-TIM-201-Fett füllen und den Deckel schließen.
Bremssystem
Der Sattelauflieger ist mit zwei Bremssystemen ausgestattet: Arbeits- und Parkbremse. Beide Systeme wirken auf die Bremsbeläge der Räder.
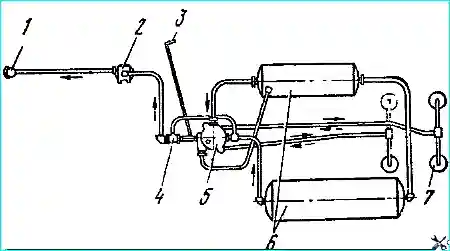
Der Bremsantrieb der Betriebsbremsanlage erfolgt pneumatisch über eine Einleiterschaltung (Abb. 6) und wird durch Betätigen des Bremspedals in der Traktorkabine betätigt.
Der Feststellbremsenantrieb ist mechanisch.
Die Konstruktion des Radbremsmechanismus des Sattelanhängers MAZ-5205A unterscheidet sich nicht grundsätzlich von der Konstruktion der Radbremsmechanismen des Anhängers MAZ-8926.
Der Unterschied liegt in der größeren Breite der Bremstrommeln und Bremsbeläge, einem längeren Spreiznocken und einem am Flansch der Radachse befestigten Gusssattel.
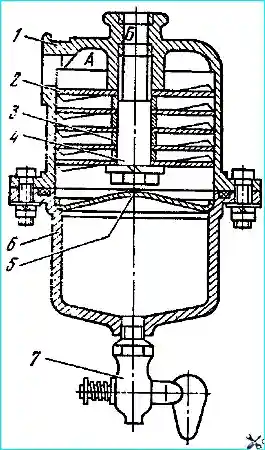
Die Konstruktion der pneumatischen Bremsantriebe und ihr Funktionsprinzip entsprechen denen des Anhängers MAZ-8926.
Die ursprüngliche Einheit ist der Feuchtigkeits-Öl-Abscheider (Abb. 7), der die Funktion hat, die vom Kompressor an das pneumatische System des Sattelanhängers gelieferte Luft von Öl und Wasserdampf zu reinigen.
Der Öl-Feuchtigkeitsabscheider wird vor dem Luftverteilventil in der Zuleitung installiert.
Die Laufräder 2 des Öl-Feuchtigkeitsabscheiders sind mittels Distanzbuchsen 3 und einem Zugbolzen 4 am Gehäuse befestigt.
Hahn 7 dient zum Ablassen von Kondensat.
Im Öl-Feuchtigkeitsabscheider wird die Luft durch die Einwirkung von Zentrifugalkräften von Öl und Feuchtigkeitsdampf gereinigt.
Luft tritt durch die Öffnung „A“ tangential zur Innenfläche des Gehäuses 1 ein und erhält durch die Öffnungen des Laufrads 2 eine Rotationsbewegung oh Bewegung.
Durch die Rotationsbewegung des Luftstroms und die Änderung seiner Bewegungsrichtung entstehende Zentrifugalkräfte schleudern Öl- und Feuchtigkeitspartikel an die Gehäusewände und an die Oberfläche des Reflektors 5.
Feuchtigkeit und Öl fließen von diesen Oberflächen durch die Löcher im Reflektor in die Schale 6.
Die gereinigte Luft gelangt durch Loch „B“ in das Luftverteilungsventil und dann in die Luftzylinder.
Der Sattelauflieger ist mit zwei Luftflaschen mit einem Fassungsvermögen von 23 und 42 Litern ausgestattet, die eine Druckluftreserve bilden, die vom Kompressor des Traktors geliefert wird.
Die Zylinder werden mit Klammern und Unterlegscheiben am Rahmen befestigt. Zum Ablassen des Kondensats befindet sich am Boden jedes Zylinders ein Hahn, der am Ende des Arbeitstages geöffnet werden sollte.
Der Antrieb der Feststellbremse ähnelt dem Antrieb des Anhängers MAZ-8926. Der Handbremshebel befindet sich auf der rechten Seite des Sattelanhängers.
Die Feststellbremse gewährleistet das Abbremsen eines voll beladenen Sattelaufliegers im abgekoppelten Zustand auf trockener Fahrbahn mit befestigtem Untergrund bei einer Steigung von maximal 20 %.
Die Kraft am Feststellbremshebel darf beim Vollbremsen des Sattelanhängers 40 kgf nicht überschreiten.
Die Wartung der Bremssystemeinheiten erfolgt wie beim Anhänger MAZ-8926.
Die Wartung des Öl-Feuchtigkeitsabscheiders besteht darin, ihn regelmäßig zu zerlegen, die Teile in Benzin zu waschen und mit Druckluft auszublasen.
Achten Sie beim Zusammenbau auf die korrekte Montage des Laufrades 2.
Nach der Montage muss die Dichtheit des Feuchtigkeits-Öl-Abscheiders unter einem Druck von 5 - 6 kgf/cm2 überprüft werden. Luftlecks sind nicht zulässig.
Die Reparatur der Bremsen des Sattelanhängers MAZ-5205A ähnelt der Reparatur der Bremsen des Anhängers MAZ-8926.
Nachfolgend finden Sie Empfehlungen zur Wiederherstellung zweier charakteristischer Teile: des Bremssattels und der Bremskammerhalterung.
Der Bremssattel besteht aus 40L-Stahlguss. Es wird wiederhergestellt, wenn das Loch für die Bremsbelagachse und das Loch für die Bremskammerhalterung verschlissen sind.
Wenn die Bohrung für die Bremsbelagachse auf eine Größe größer als 32,1 mm abgenutzt ist, wird eine Reparaturhülse eingebaut.
Hierzu wird die verschlissene Bohrung auf Ø 35,8 mm aufgebohrt, die Fase auf der Seite der Befestigung zum Bremsschildträger 1X45° angesenkt und die Bohrung auf Ø 36+005 mm aufgerieben.
Anschließend wird in die gefräste Bohrung eine Reparaturhülse eingepresst, durch die Bohrung im Bremssattel für die Bremsbelagachsen-Sicherungsschraube ein Loch Ø 8,7 mm in die Hülse gebohrt und ein Gewinde der Klasse M10x1 geschnitten. 2 in der Buchsenbohrung.
Die 1x45° Fase in der Buchsenbohrung auf der Seite der Befestigung zum Bremsschildträger ansenken und die Bohrung in der Buchse auf Ø 32+005 mm aufreiben.
Auch die auf 56,1 mm abgenutzten Bohrungen für die Bremszylinderhalterung werden durch den Einbau einer Reparaturbuchse wiederhergestellt.
Die verschlissene Bohrung wird auf Ø 59,8 mm aufgebohrt, die Fase auf der Seite der Befestigung zum Bremsschildträger 1X45° angesenkt und die Bohrung auf Ø 60+0,05 mm aufgerieben.
In die bearbeitete Bohrung wird eine Reparaturbuchse eingepresst, von der Seite der Befestigung zum Bremsschildträger her eine 1 x 45° Fase in die Buchsenbohrung eingesenkt und die Bohrung auf Ø 56+006 mm aufgerieben.
Bei der Bearbeitung von Bohrungen für die Bremsbelagachse und für den Bremszylinderhalter wird die Bohrungsfläche Ø 172 +0,08 mm als Basis genommen.
Die Achsen der Bohrungen für die Bremszylinderhalterung und für die Bremsbackenachse, sowie die Befestigungsbohrung Ø 172 +0,08 mm müssen parallel zueinander und senkrecht zur Passfläche mit dem Anhängerachsflansch mit einer Genauigkeit von 0,1 mm auf einer Länge von 100 mm verlaufen.
Bremskammerhalterung. Das Halterungsrohr besteht aus 35er Stahl und die Buchsen für die Lagerzapfen der Spreiznocke sind aus KMC-3-1 Bronze gefertigt.
Die Halterung wird wiederhergestellt, wenn die Löcher in den Buchsen für die Lagerzapfen der Expansionsnocke und die Löcher im Flansch für die Befestigungsschrauben zum Bremssattel abgenutzt, der Lagerflansch verbogen und die Schweißnähte beschädigt sind.
Wenn die Löcher in den Buchsen für die Lagerzapfen der Expansionsnocken auf ein Maß größer als 38,10 mm abgenutzt sind, werden die Buchsen ausgetauscht.
Hierzu die verschlissenen Buchsen herausdrücken und neue einpressen: eine auf der Seite der Buchse unter den Dichtringen bündig mit dem Buchsenende und die zweite bündig mit dem Ende der Halterung.
Anschließend wird die Halterung in die Vorrichtung eingebaut und auf einer Vertikalbohrmaschine werden Löcher in den Buchsen auf Ø 38 mm gebohrt.
Der Rundlauf der Montagefläche im Bremssattel relativ zur Achse der Oberflächen der Löcher in den Buchsen für die Lagerzapfen der Spreiznocke sollte 0,1 mm nicht überschreiten.
Wenn die Löcher im Stützflansch für die Befestigungsschrauben an der Stütze auf eine Größe von mehr als 15,3 mm abgenutzt sind, werden sie auf Ø 17,0 mm gebohrt, mit einer durchgehenden Naht unter Verwendung einer UONI-13/45-Elektrode Ø 3 mm geschweißt, beide Oberflächen des Stützflansches werden nach unten gedreht, bis das abgelagerte Metall entfernt ist, und Löcher mit Ø 15 mm werden gebohrt, nachdem zuvor die Mitten der Löcher mit einer Schablone markiert wurden.
Die Ebene des Flansches muss senkrecht zur Oberfläche der Löcher in den Buchsen für die Stützzapfen stehen Spreiznocken mit einer Genauigkeit von 0,2 mm auf einer Länge von 100 mm.
Beschädigte Schweißnähte werden wiederhergestellt, indem sie in den beschädigten Bereichen mit einer Elektrode UONI-13/45 Ø 3 mm geschweißt werden.
Die elektrische Ausrüstung des Sattelanhängers ist nach der Einleiterschaltung ausgeführt (Abb. 8). Für den Anschluss an die Zugmaschine verfügt der Sattelauflieger über eine siebenpolige Steckdose.
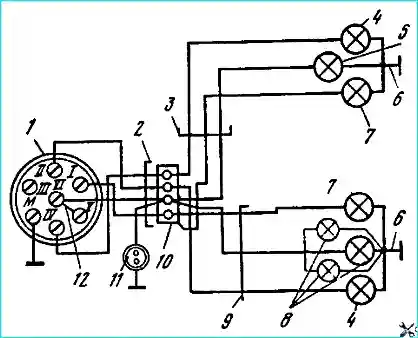
Die Sattelaufliegerplattform (Abb. 9) ist eine Pritsche.
Die Rück- und Seitenwände lassen sich an Scharnieren nach unten öffnen, die Seitenpfosten sind abnehmbar.
Die Vorderseite ist fest installiert. Auf der Plattform werden das Markisengestell und die Markise montiert.
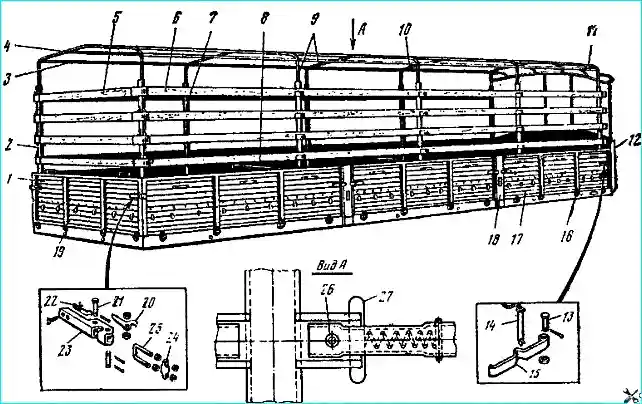
Der Plattformboden besteht aus Holz, die Seiten sind aus Metall. Das Markisengestell besteht aus Rohrprofilen mit Holzrosten.
Die Plattformbasis ist der Sattelaufliegerrahmen, auf dem die Bodenkassetten montiert werden.
Die Kassetten sind aus 34 mm starken Brettern zusammengesetzt, mit Nut und Feder verbunden und an den Enden von einem gestanzten Quadrat mit einem Querschnitt von 85 x 29 x 2 mm umschlossen.
Die Bretter werden mit M6-Schrauben an den Beschlägen befestigt. Die Kassetten bestehen aus zwei Teilen – rechts und links – und werden im zusammengebauten Zustand entlang der Längssymmetrieachse der Plattform verbunden.
Die äußersten Bodenbretter verfügen über eine Fräsung, die eine Montage unter dem Profil des Seitenrahmenträgers ermöglicht.
Die Kassetten werden mit M8-Schrauben durch die Endbeschläge an den Rahmenquerträgern befestigt. Die Bodenbretter werden in Längsrichtung auf den Rahmen aufgelegt und mit M8x55 Schrauben an den Rahmenquerträgern befestigt.
Die drei vorderen Bretter, die entsprechend dem halbrunden Profil des vorderen Querträgers des Rahmens bearbeitet sind, werden quer über den Rahmen montiert und unter den vorderen Querträger gesteckt. Die Befestigung erfolgt mit M8-Schrauben an den Halterungen am Rahmen.
Um Zugang zum abnehmbaren Königszapfen des Sattelaufliegers zu erhalten, befindet sich in der vorderen Bodenkassette eine mit einer Platte abgedeckte Luke. Die Platte wird mit M6x30 Schrauben an den Platinen befestigt.
Im Seitenbalken des Rahmens, dessen obere Ablage in einer Ebene mit den Bodenbrettern liegt, befinden sich fünf Löcher mit angeschweißten Rohrführungen zur Montage der Markisenrahmenpfosten.
Seitenwände sind dreiteilig, jeweils 3070 mm lang, metallisch verschweißt und bestehen aus einer 1,5 mm starken Wellplatte mit Längssicke.
Die Stabilität der Seite wird durch einen aus Vierkantrohren 40x40x2 geschweißten Rahmen mit zwei senkrechten Pfosten gewährleistet.
Am Unterrohr des Rahmens sind vier gestanzte Ösen angeschweißt, an denen die Seitenteile mittels Achsen aufgehängt werden.
Am oberen Rahmenrohr ist eine Verstärkung mit Fenstern zur Montage von Seitenaufsätzen angeschweißt.
Gegenüber den Fenstern sind Halterungen an der Seitenwand angeschweißt. Die Größe des Fensters und der Halterungen in der Leuchte beträgt 72 x 34 mm.
An der Seitenwand ist im Abstand von 410 mm von oben eine Platte mit bogenförmigen Schlaufen angeschweißt, durch die die Plattformplane befestigt wird. Der Abstand zwischen den Schlaufen beträgt maximal 200 mm, das lichte Schlaufenmaß beträgt 35x13 mm.
Unterhalb der Scharniere sind an der Blende zwischen den Pfosten drei gestanzte Haken zur Befestigung der Markisenspannschnur angeschweißt.
Im Abstand von 285 mm von oben sind an der Seitenwand im Bereich der äußeren Rahmenpfosten Halterungen mit Ösen zur Befestigung des 15er-Verschlussbügels angeschweißt.
An der Halterung ist an einer Kette ein Stift 14 mit Verriegelungsstange befestigt.
Der an der Zahnstange 18 befestigte Bügel 15 des Schlosses wird zwischen die Ösen gesteckt, in die der Stift 14 eingesteckt wird und den Bügel fixiert.
Das Herausfallen des Stiftes wird durch eine Sicherungsplatte verhindert, die auf einem Niet in der Nut des Stiftes 14 exzentrisch rotiert und durch ihr Eigengewicht stets dazu neigt, eine senkrechte Stellung zum Stift einzunehmen.
An der Unterkante der Seite ist ein gestanzter Winkel angeschweißt, der den Spalt zwischen den Seiten und dem Rahmen abdeckt und so das Eindringen von Feuchtigkeit in die Plattform verhindert.
Das hintere Seitenbrett unterscheidet sich vom vorderen Seitenbrett dadurch, dass es an der Außensäule befestigt ist, Anschließend an die Rückseite ist im Abstand von 260 mm von oben eine Halterung für die Verriegelungsleiter angeschweißt.
Die Heckseite 1 unterscheidet sich strukturell von den Seitenteilen durch Verriegelungen, zwei an der oberen Verstärkung angeschweißte Halterungen zum einfachen Einheben in die Karosserie und einen unterstützenden Klapptritt an der Innenseite der Seite.
Bei geöffneter Heckklappe dreht sich die Trittstufe durch ihr Eigengewicht um ihre Achse und ist senkrecht zur Heckklappenverkleidung montiert.
Stufenförmiges Heckklappenschloss.
Die Verriegelung erfolgt durch die Spannung der Leiter 25, die mit Muttern an der Halterung am Seitenbrett auf der Achse 24 befestigt ist.
Die Muttern dienen nicht nur zur Befestigung der Trittleiter, sondern auch zur Justierung der Leiter relativ zur Achse (Verlängerung oder Verkürzung).
Der Griff 23 des Schlosses ist über eine Achse an den Ösen der Schlosshalterung befestigt, die an der Seitensäule der Heckklappe angeschweißt ist.
Wir drehen den Griff senkrecht zur Seitenwand, greifen die Trittleiter 25 der Seitenwand mit der abgebildeten Aussparung des Griffs und bringen dann den Griff 23 in seine Ausgangsposition zurück, wobei wir ihn fest gegen die Seitenwand drücken.
In diesem Fall wandert die Stehleiterachse über die Mitte der Befestigungsachse hinaus und sorgt aufgrund der Exzentrizität für eine zuverlässige Verriegelung des Schlosses.
Eine zusätzliche Fixierung des Griffs 23 in der Schließstellung wird durch die Verriegelung 20 erreicht, die durch den Finger 21 im Griff gesichert und durch die Blattfeder 22 vom Griff weggedrückt wird.
Die Bordwände werden mittels Bolzen über Scharniere an den ausgestanzten Ösen 16 befestigt.
Die Öse ist mit zwei Schrauben an den Rahmenträgern befestigt und die Position der Öse entlang des Trägers kann mithilfe elliptischer Löcher am Träger eingestellt werden.
Zum Schutz vor Beschädigungen an Teilen und Aggregaten der Zugmaschine und des Aufliegers sowie der Bordwände sind am Rahmenträger und am hinteren Querträger Gummianschläge 19 mit Schrauben montiert.
Die vordere halbrunde Seite ähnelt in Design und Befestigungsmethode der Vorderseite des Sattelaufliegers MAZ-5245.
Die Seitenbretter sind über die Vordersäule und die Mittelsäulen miteinander und mit dem Vorderbrett verbunden. Die Vordersäule ist mit M10-Schrauben an der vorderen Seitenwand und den Rahmenträgern befestigt.
Das Rack verfügt über einen Omega-förmigen ungleichschenkligen Flanschabschnitt.
Einer der Böden ist an der Vorderseite befestigt, der zweite geht von der Innenseite der Plattform hinter die Seitenwand.
Die mittlere Säule 18 weist einen gleichschenkligen Omega-Abschnitt auf, dessen beide Böden über die Seitenbretter hinausragen und so die Lücke zwischen Brett und Säule schließen.
Die Mittelsäule verfügt unten über eine Schräge, mit der sie in die Aufnahme am Seitenholm des Rahmens passt.
Innenseitig ist das Rack mit einem aufgeschweißten Metallstreifen verstärkt, wodurch an den am stärksten beanspruchten Stellen ein kastenförmiger Abschnitt entsteht.
In den äußeren Ecken des Racks sind quadratische Aussparungen angebracht, in die die 15 Verriegelungswinkel eingesetzt werden. Die Halterungen werden mit dem Bolzen 13 an den an den Pfosten angeschweißten Ösen befestigt.
Um die Quersteifigkeit der Plattform zu erhöhen und die transportierte Ladung vor einer Verschiebung in Längsrichtung zu schützen, sind zwischen den gegenüberliegenden Pfosten 18 Spannketten installiert, die auf der einen Seite mit einem Haken an den Pfostenhalterungen befestigt sind und auf der anderen Seite mit dem gleichen Schloss wie beim Sattelanhänger MAZ-5245.