Wartung der Bremsmechanismen und des pneumatischen Bremsantriebs von Kamaz
Die Wartung von Bremsmechanismen besteht aus der Schmierung der Einstellhebel und Buchsen der Expansionsnockenwellen;
- - bei der Regulierung der Hübe der Bremskammerstangen und der Sicherung der Bremskammern und ihrer Halterungen;
- - bei der Überprüfung des Zustands von Bremstrommeln, Bremsbelägen, Belägen, Zugfedern und Achsschenkeln (bei entfernten Naben).
Die Einstellhebel der Bremsmechanismen werden über Schmiernippel geschmiert, bis frisches Fett herausgedrückt wird.
Die Schmierung der Expansionsnockenwellenbuchsen erfolgt ebenfalls über Schmiernippel, es ist jedoch zu beachten, dass die Schmiermittelmenge moderat sein sollte (nicht mehr als fünf Hübe beim Schmieren mit einer manuellen Spritze), da überschüssiges Schmiermittel eindringen kann der Bremsmechanismus.
Der Hub der Bremszylinderstangen wird bei kalten Bremstrommeln und Nennluftdruck im pneumatischen Bremsantrieb eingestellt.
Die Feststellbremse muss gelöst werden. Die Arbeit wird von zwei Darstellern ausgeführt, von denen sich einer in der Fahrzeugkabine befinden muss.
Messen Sie den Hub der Stangen mit einem Lineal, indem Sie es parallel zur Stange platzieren und sein Ende gegen den Bremszylinderkörper legen. Markieren Sie die Position des äußersten Punktes der Stange auf der Skala des Lineals, drücken Sie das Bremspedal ganz durch und markieren Sie erneut die Position des gleichen Punktes der Stange auf der Skala.
Die Differenz der erhaltenen Ergebnisse ergibt den Wert des Stangenhubs.
Wenn der Stangenhub 40 mm überschreitet, ist es notwendig, die Verriegelungsschraube zu lösen und durch Drehen der Schneckenachse des Einstellhebels die Backen auseinander zu bewegen, bis sie die Bremstrommel berühren, d. h. Sie müssen Drehen Sie die Schneckenachse bis zum Anschlag.
Danach sollten Sie die Beläge zusammenbringen, indem Sie die Schneckenachse eine halbe Umdrehung in die entgegengesetzte Richtung drehen (2-3 Klicks des Schlosses), um so den kleinsten Hub der Stangen sicherzustellen, der 20 mm betragen sollte für KamAZ-4310, -43105, -5320, -5410 und -55102: für KamAZ-5511, -53212 und -54112 Fahrzeuge beträgt er 25 mm an der Zwischen- und Hinterachse und 20 mm an der Vorderachse.
Sie müssen sicherstellen, dass sich die Bremskammerstangen beim Ein- und Ausschalten der Druckluftversorgung schnell bewegen, ohne zu blockieren.
Überprüfen Sie die Drehung der Rollen. Sie sollten sich frei drehen lassen, ohne zu blockieren, ohne die Pads zu berühren.
Es ist notwendig, dass die Stangen der rechten und linken Kammer an jeder Achse einen möglichst gleichen Hub haben (der zulässige Unterschied beträgt nicht mehr als 2-3 mm), um die gleiche Bremswirkung der rechten und linken Kammer zu erzielen linke Räder.
Nachdem Sie überprüft haben, ob die Einstellung korrekt ist, ziehen Sie die Sicherungsschraube des Einstellhebels fest.
Die Inspektion der Bremsmechanismen ergab, dass einige Teile ausgetauscht werden müssen. Dabei ist zu berücksichtigen, dass der Verschleiß der Arbeitsfläche der Bremstrommel nicht mehr als 1 mm betragen darf; Späne, Risse und Absplitterungen der Bremsreibbeläge sind nicht akzeptabel; ihr Verschleiß muss dem Wert entsprechen, bei dem Es verbleiben mindestens 0,5 mm bis zu den Nietköpfen.
Wenn Sie einen der linken oder rechten Bremsbeläge ersetzen müssen, tauschen Sie alle Beläge an beiden Bremsmechanismen (linkes und rechtes Rad) aus.
Nach dem Austausch der Bremsbeläge ist der Bremsmechanismus vollständig eingestellt.
Dazu lösen Sie die Muttern, mit denen die Schuhachsen befestigt sind, und bringen die Exzenter näher zusammen, indem Sie die Achsen der Schuhe so drehen, dass sie mit den abgeschrägten Seiten ihrer äußeren Enden zueinander ausgerichtet sind, und dann die Achse drehen Drücken Sie die Schnecke des Einstellhebels, drücken Sie die Bremsbacken an die Trommel. Drehen Sie anschließend die Exzenterachsen auf die eine oder andere Seite und montieren Sie die Bremsbeläge. Achten Sie dabei darauf, dass sie genau an der Trommel anliegen.
Der Sitz der Beläge wird mit einer 0,1 mm dicken Fühlerlehre überprüft, die nirgendwo über die gesamte Belagbreite reichen sollte. Ziehen Sie bei dieser Position der Beläge die Achsmuttern fest und stellen Sie den Mindesthub der Bremszylinderstange ein.
Nach der angegebenen Einstellung werden folgende Abstände zwischen Bremstrommel und Belägen erreicht: an der Spreizfaust – 0,4 mm, an den Achsen der Beläge – 0,2 mm.
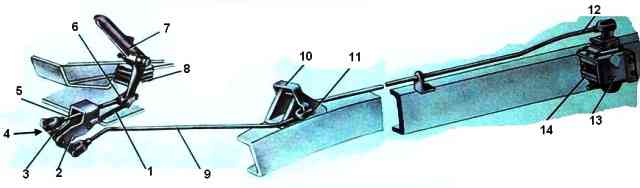
Der Bremspedalweg muss mindestens 100–130 mm betragen, davon sind 20–30 mm freies Spiel.
Bei vollständiger Betätigung sollte das Pedal den Kabinenboden nicht um 10...30 mm erreichen. Der Pedalweg wird mit einem Lineal im Abstand von 210-220 mm von der Drehachse gemessen.
Das Ende des freien Spiels gilt als dieser Moment der Beginn des Ausfahrens der Bremszylinderstangen oder der Moment, in dem die Bremslichter aufleuchten.
Passen Sie bei Bedarf den Pedalweg an, indem Sie die Länge der Stange 6 (siehe Abb. 1) mit der Einstellgabel 5 ändern.
Bei vollem Pedalweg sollte der Bremsventilhebel 31,1–39,1 mm betragen.
Die tägliche Wartung des Bremsantriebs erfordert nur wenige Arbeitsgänge, um einen störungsfreien Betrieb zu gewährleisten.
Hierbei handelt es sich hauptsächlich um Kontroll- und Diagnosearbeiten, die keinen Einsatz von Instrumenten erfordern; Sie werden vom Fahrer durchgeführt, wenn er das Fahrzeug für die Abfahrt vorbereitet und während der Arbeit an der Strecke arbeitet.
Um die Funktionstüchtigkeit der Kontrollventile auf dem Armaturenbrett zu überprüfen, drücken Sie die Testtaste. Alle Kontrolllampen sollten aufleuchten; sie leuchten auch dann auf, wenn der Druck in den Empfängern weniger als 480–520 kPa beträgt.
Um die Funktionsfähigkeit des Antriebs zu überprüfen, sollten Sie die Bremssteuerung des Fahrzeugs aktivieren: Bremspedal betätigen, Feststellbremse ein- und ausschalten, Taste des Hilfsbremsventils drücken, Energiespeicher mit der Taste zum Lösen der Notbremse entriegeln.
Jeden Tag wird am Ende des Arbeitstages das Kondensat aus den Sammelbehältern abgelassen.
Bei einer Lufttemperatur von -(- 5 °C) und darunter gießen Sie (einmal pro Woche oder nach einer Laufleistung von 1000 km) eine frische Portion Ethylalkohol in den Frostschutzschutz. Vor dem Hinzufügen von Alkohol muss das Kondensat aus der Sicherung abgelassen werden.
Stellen Sie beim Ankuppeln des Anhängers sicher, dass die Anschlussköpfe richtig angeschlossen sind und die Trennventile geöffnet sind.
Bei der Wartung des pneumatischen Antriebs der Autobremsen müssen Sie auch darauf achten, dass dieser fest sitzt. Besonderes Augenmerk sollte auf die Dichtheit der Verbindungen von Rohrleitungen und flexiblen Schläuchen gelegt werden, da hier am häufigsten Luftlecks auftreten.
Viele starke Luftlecks werden mit dem Gehör festgestellt, schwache mit einer Seifenemulsion.
Luftlecks an den Anschlüssen der Bremssystemleitungen werden durch Anziehen beseitigt und undichte Rohrleitungen und flexible Schläuche werden ersetzt.
Überprüfen Sie die Splinte der Bremskammerstangen und die Stifte des zweiteiligen Kranantriebs. Die Schutzabdeckungen der Bremszylinder und des Bremsventils dürfen nicht beschädigt werden.
Bei der zweiten Wartung wird die Funktionsfähigkeit des pneumatischen Bremsantriebs über die Steuerauslassventile mittels Manometern überprüft.
Überprüfen Sie den festen Sitz der Muttern, mit denen der Kompressor am Motor befestigt ist, und den festen Sitz der Muttern, mit denen der Zylinderkopf des Kompressors befestigt ist.
Das Anziehen erfolgt gleichmäßig über Kreuz in zwei Schritten. Überprüfen Sie die Befestigung der Bremskammerklemmen, die Befestigung der Bremskammerhalterungen und die Kammern selbst an den Halterungen.
Besonderes Augenmerk sollte auf die Befestigung von Energiespeichern gelegt werden. Spiel in ihrer Befestigung ist nicht akzeptabel, da dies zur Trennung des Geräts von der Halterung führt.
Durch Kompressor
Während der saisonalen Wartung muss der Kompressorkopf entfernt werden, um die Kolben, Ventile und Sitze zu reinigen. Kompressorventile, die keine Dichtheit gewährleisten, müssen in Sitze eingeschliffen oder ersetzt werden.
Im Druckregler muss das Filterelement, das sich unter der unteren Abdeckung befindet, gewaschen oder ausgetauscht werden.
Beim Einschrauben des Deckels ist Vorsicht geboten, da das Gewinde konisch ist und Verformungen beim Einbau nicht akzeptabel sind. Sie führen zu einem Thread-Fehler, der dann nicht wiederhergestellt werden kann.
Vor dem Einbau empfiehlt es sich, das Gewinde mit Graphitschmiermittel zu schmieren, um ein „Festkleben“ zu verhindern.
Während der Kompressor läuft, verschleißt die Zylinder-Kolben-Gruppe und die Ventildichtheit wird beeinträchtigt.
Bei diesen Störungen überschreitet die Füllzeit des pneumatischen Systems (bevor die Warnleuchten erlöschen) bei einer Kurbelwellendrehzahl von 2200 U/min die eingestellten 8 Minuten oder der Kompressor baut überhaupt nicht den vorgegebenen Druck auf (700- 750 kPa).
Außerdem führt der Verschleiß der Zylinder-Kolben-Gruppe dazu, dass Öl in das Pneumatiksystem gesaugt wird.
Nachdem das Pneumatiksystem mit Luft gefüllt ist, öffnet sich das Entlastungsventil im Druckregler und das Öl, das zusammen mit der Luft in das Pneumatiksystem gelangt ist, wird herausgeschleudert und setzt sich auf dem Regler und dem Rahmen ab. Dies ist ein äußeres Anzeichen für eine Fehlfunktion des Kompressors.
Es ist zu beachten, dass der Ölverbrauch durch den Kompressor aufgrund einer Verstopfung des Luftfilters steigen kann.
Wenn es zu Verstopfungen kommt, erhöht sich das Vakuum am Einlass und der Kompressor saugt auch bei funktionierender Kolbengruppe Ölnebel aus dem Kurbelgehäuse an und wirft ihn dann am Auslass in den pneumatischen Antrieb.
Undichte Stellen an der Zylinderkopfdichtung des Kompressors, innere Risse im Kopf oder Block führen dazu, dass Flüssigkeit aus dem Kühlsystem in die Zylinder gesaugt wird und dann zusammen mit Luft in den pneumatischen Antrieb gelangt.
Der Kühlmittelstand im Ausgleichsbehälter sinkt und die Flüssigkeit darin bildet Blasen. Dies geschieht, weil der Kolben beim Kompressionshub Luft in den Kühlmantel des Kompressors drückt und dann Die Luft und die Flüssigkeit werden in den Ausgleichsbehälter abgeleitet.
Es gibt eine weitere gefährliche Folgeder betrachteten Fehlfunktionen
Die Flüssigkeit, die in die Kompressorzylinder gelangt, sickert durch die Spalte zwischen Zylinder, Kolben und Ringen in das Kurbelgehäuse des Kompressors und fließt von dort in die Ölwanne des Motors. Daher muss bei der Suche nach der Stelle, an der das Kühlmittel in das Öl gelangt, auch der Kompressor im Auge behalten werden.
Bremsstörungen werden in den meisten Fällen durch Fehlfunktionen pneumatischer Antriebsvorrichtungen verursacht.
Die wahrscheinlichsten Störungen, die ein Fahrer ohne den Einsatz von Diagnosegeräten erkennen und beheben kann, werden im Folgenden besprochen
Wenn die pneumatischen Antriebsbehälter nicht gefüllt sind und der Druckregler Luft in die Atmosphäre abgibt, kann diese Fehlfunktion mehrere Gründe haben: Die Rohrleitung zwischen dem Regler und den Sicherheitsventilen ist verstopft; Der Druckregler ist defekt – meistens ist das Filterelement mit Öl oder Eiskristallen verstopft (im Winter).
Wenn sich die Behälter langsam füllen und der Druck in ihnen nicht den Nennwert erreicht (ohne Undichtigkeiten), ist entweder der Kompressor oder der Druckregler defekt.
Wenn die Behälter eines separaten Kreislaufs schlecht gefüllt sind, sollten Sie zunächst auf den Abschnitt des Sicherheitsventils dieses Kreislaufs achten.
Eine wirkungslose Abbremsung des Fahrzeugs durch die Betriebsbremse liegt vor, wenn der Antrieb falsch ausgerichtet ist oder das zweiteilige Bremsventil defekt ist.
Wenn beim Bremsen der Druck in den Bremskammern den Nennwert erreicht, sind die Bremsmechanismen falsch reguliert oder defekt.
Wenn beim Bremsen mit der Betriebsbremse nur in den Bremskammern der Vorderachse der Druck unter dem Normalwert liegt, kann entweder der untere Teil des Bremsventils oder der Druckbegrenzer defekt sein.
Wenn der Druck in den Bremskammern normal ist und die Bremswirkung nicht wirksam ist, kann die Ursache dieser Fehlfunktion ein großer Hub der Bremskammerstangen oder beispielsweise verölte Bremsbelagbeläge sein.
Wenn beim Betätigen des Bremspedals die Bremsung der Räder des hinteren Trolleys wirkungslos ist oder überhaupt nicht erfolgt, während die Vorderräder normal bremsen, liegt möglicherweise eine Fehlfunktion im pneumatischen Teil des Antriebs vor Der obere Teil des Bremsventils oder der Bremskraftregler ist defekt.
In diesem Fall sind Störungen bei der Einstellung der Bremsmechanismen oder dem Antrieb des Bremskraftreglers möglich.
Wenn nach dem Niedertreten des Bremspedals nicht alle Räder des Fahrzeugs die Bremsen lösen, ist möglicherweise das zweiteilige Bremsventil defekt (der Drücker oder der obere Kolben ist blockiert) oder der Bremsventilantrieb ist möglicherweise falsch ausgerichtet (Es gibt kein freies Spiel des Pedals).
Wenn nach Loslassen des Bremspedals nicht nur Luft aus den hinteren Bremskammern austritt, ist möglicherweise der Bremskraftregler oder der obere Teil des Bremsventils defekt.
Diese Fehlfunktionen führen zu einer Verzögerung beim Ablassen der Luft aus den vorderen Bremskammern. Wenn beim Lösen der Bremsen nicht nur Luft aus den vorderen Bremskammern abgelassen wird, ist der Druckbegrenzer oder der untere Teil des Bremsventils defekt.
Die Ursache für Luftlecks durch den atmosphärischen Auslass eines zweiteiligen Bremsventils können nicht nur die Dichtringe und Ventile im Ventil selbst sein, sondern auch andere Geräte des Bremssystems.
Wenn beim Loslassen des Pedals und angezogener Feststellbremse eine Undichtigkeit festgestellt wird, ist das Bremsventil defekt.
Mit einem handelsüblichen Zwei-Zeiger-Manometer können Sie genau bestimmen, welcher Abschnitt des Ventils undicht ist: Wenn die obere Nadel des Manometers „abfällt“, wenn der Motor nicht läuft, dann ist dies auch im unteren Abschnitt des Ventils der Fall undicht; Der untere Pfeil „fällt“ – der obere Bereich ist undicht.
Wenn eine Luftleckage durch den atmosphärischen Auslass des Bremsventils nur dann beobachtet wird, wenn die Feststellbremse gelöst ist und beim Einschalten stoppt, dann ist das Anhängerbremssteuerventil mit einem Zweidrahtantrieb oder einem der Energiespeicher ist defekt.
Sie können ein fehlerhaftes Gerät feststellen, indem Sie den Energiespeichern Luft aus dem Notbremslösekreis zuführen:
- Wenn beim Drücken des Notbremslöseknopfs die Undichtigkeit des Bremsventils weiterhin besteht, dann ist die Drückerdichtung im Energiespeichergehäuse undicht, und wenn keine Undichtigkeit vorhanden ist, dann ist die Membran in der Anhängerbremssteuerung undicht Ventil ist defekt.
Wenn die Räder des hinteren Wagens die Bremsen nicht lösen, wenn die Feststellbremse gelöst ist, kann die Ursache für diese Fehlfunktion das Feststellbremsventil, das Gas- oder Zweileitungsventil und die Energiespeicher sein.
Möglicherweise ist eine der Leitungen im Feststellbremskreis verstopft, eingefroren oder eingeklemmt.
Wenn einer der Energiespeicher beim Bewegen des Griffs des Feststellbremsventils nicht funktioniert, kann die Ursache an Dellen am Gehäuse oder einem Festklemmen des Drückers liegen. Es ist auch möglich, dass die Rohrleitung, über die die Luft dem nicht funktionsfähigen Energiespeicher zugeführt wird, verstopft ist.
Wenn sich die Bremskammerstangen beim Einschalten der Energiespeicher lösen und das Fahrzeug nicht effektiv genug bremst, müssen der Hub der Stangen und die Funktionsfähigkeit der Bremsmechanismen und Räder überprüft werden.
Die häufigsten Störungen im Feststellbremskreis sowie im gesamten pneumatischen Antrieb sind Druckluftlecks aufgrund von Schäden an Dichtringen und Manschetten.
Luftleckage unter dem Griff des Feststellbremsventils beim Lösen der Bremse wird durch eine undichte Stangendichtung in der Führung verursacht.
Die Ursache für Luftlecks am atmosphärischen Auslass des Feststellbremsventils ist nicht immer ein Leck in den Dichtungen im Ventil selbst.
Eine Undichtigkeit kann beispielsweise aufgrund einer Fehlfunktion des Zweidraht-Anhängerbremssteuerventils auftreten.
Um das defekte Gerät zu ermitteln, füllen Sie den pneumatischen Antrieb mit Druckluft, aktivieren Sie die Feststellbremse und trennen Sie den Steuerleitungsschlauch vom Wasserhahn.
Wenn weiterhin Luft aus dem atmosphärischen Auslass austritt, ist das Feststellbremsventil defekt. Wenn am abgeklemmten Schlauch ein Leck festgestellt wird, ist das Bremssteuerventil des Anhängers defekt.
Wenn beim Bremsen und beim Lösen der Feststellbremse Luft aus dem atmosphärischen Auslass des Gasventils austritt, ist der Dichtring des atmosphärischen Auslasses des Ventils undicht.
Luftleckagen durch den atmosphärischen Auslass dieses Geräts werden beim Bremsen mit der Feststellbremse durch den Verlust der Dichtheit des Einlassventils und beim Lösen der Bremse durch das Auslassventil verursacht. Im letzteren Fall werden die Hinterräder nicht freigegeben.
Manchmal wird ein Luftleck durch das Gaspedalventil beobachtet, wenn die Feststellbremse angezogen ist und gleichzeitig das Pedal gedrückt wird.
In diesem Fall ist einer der Energiespeicher defekt – Luft aus der Bremskammer gelangt durch die Dichtung des Schubrohrs in den Energiespeicher und dann durch das Beschleunigerventil in die Atmosphäre.
Beim Betrieb in Energiespeichern verschleißen und versagen die Dichtungen des Kolbens im Zylinder und des Schubrohrs im Gehäuse.
Beim Lösen der Feststellbremse strömt Druckluft von unterhalb des Kolbens durch eine undichte Dichtung in den Hohlraum oberhalb des Kolbens und durch den Verbindungsschlauch auf der Geräteseite unter der Bremskammermembran und von dort in die Atmosphäre durch das Abflussloch. In diesem Fall stoppt die Leckage, wenn die Feststellbremse angezogen wird.
Wenn die Dichtung des Druckrohrs im Energiespeicherkörper versagt, gelangt beim Anziehen der Feststellbremse Druckluft aus der Unterseite des Kolbens in den Hohlraum über der Membran und entweicht über den Bremskraftregler in die Atmosphäre.
Befindet sich der Reglerhebel in der oberen Position, entweicht die Luft durch den atmosphärischen Auslass des Bremsventils in die Atmosphäre.
Um einen defekten Energiespeicher zu erkennen, müssen Sie die Feststellbremse lösen und nacheinander die Rohrleitungen trennen, die die hinteren Bremskammern mit Druckluft versorgen: Bei einem defekten Gerät tritt Druckluft aus dem Hohlraum der Bremskammer aus .
Wenn der Notbremslöseknopf gedrückt wird; Die Energiespeicher werden nicht freigegeben (bei einem Druck im pneumatischen Antrieb von mehr als 500 kPa), und nach der Freigabe tritt ein kleiner Teil der Druckluft aus dem atmosphärischen Auslass des Pneumatikventils aus, was bedeutet, dass der Kreuz- Der Rohrleitungsabschnitt zwischen dem Ventil und dem Zweileitungsventil ist verstopft. Wenn nach dem Loslassen der Taste keine Luft aus dem atmosphärischen Auslass austritt, ist das Ventil selbst defekt.
Wenn beim Drücken der Zapftaste Luft durch das Beschleunigerventil in die Atmosphäre entweicht, ist das Zweileitungsventil defekt.
Luftlecks aus dem atmosphärischen Auslass können aufgrund einer Fehlfunktion sowohl des Wasserhahns selbst als auch des Zweileitungsventils auftreten.
Wenn unabhängig von der Position des Feststellbremsventilgriffs ein Luftleck festgestellt wird, ist das Ventil selbst defekt.
Wenn die Undichtigkeit jedoch nur beim Lösen der Feststellbremse auftritt und beim Bremsen stoppt, dann ist das Zweileitungsventil undicht
In beiden Fällen ist es verboten, den atmosphärischen Auslass im Notbremslöseventil mit einem Stopfen zu verstopfen, da in diesem Fall ein spontanes Lösen der Feststellbremse beobachtet wird und die Ersatzbremse des Fahrzeugs nicht zufriedenstellend funktioniert.
Dies wird dadurch erklärt. dass beim Betätigen der Not- oder Feststellbremse durch Drehen des Griffs des Feststellbremsventils das Ablassen der Luft aus den Energiespeichern schwierig oder unmöglich sein wird.
Wenn beim Drücken des Zusatzbremsventilknopfs der Motor nicht stoppt (die Klappen in den Auspuffrohren drehen sich nicht) und der Anhänger nicht bremst, kann dieses Phänomen mehrere Gründe haben: Es ist keine Luft vorhanden Versorgung des Hilfsbremsventils, die Leitung vom Hahn zu den Pneumatikzylindern ist eingeklemmt oder verstopft, der Hahn selbst ist defekt. Die Störung wird durch sequenzielles Abschalten der Pipelines festgestellt.
Wenn, wenn das Hilfsmittel Wenn bei betätigter Abgasbremse der Kraftstoff nicht abgestellt wird und die Dämpfer in den Abgasrohren aktiviert sind, sollten Sie prüfen, ob dem Pneumatikzylinder der Kraftstoffpumpe Druckluft zugeführt wird. Auch bei der Montage des Pneumatikzylinders kann es zu einer Fehlfunktion kommen.
Der Dämpfermechanismus und die ihn steuernden Pneumatikzylinder arbeiten unter den ungünstigsten Bedingungen.
Deshalb versagen sie häufiger als andere und Dämpfer blockieren am häufigsten. Geschieht dies bei beiden Dämpfern, springt der Motor nicht an; bei einem startet der Motor zwar, raucht aber und entwickelt keine Leistung.
Auch bei pneumatischen Zylindern des Dämpferantriebs kann es zu Problemen kommen, am häufigsten kommt es zu einem Verlust der Dichtheit der Kolbenmanschette.
Der Aktivierungssensor des Magnetventils des Anhängers befindet sich innen am linken Rahmenlängsträger neben dem Kupplungsgehäuse.
Wenn der Sensor oder die elektrische Verkabelung ausfällt und die Zusatzbremse aktiviert ist, bremst der Anhänger nicht und der Lastzug kann ins Schleudern geraten und zusammenbrechen.
Wenn nach dem Loslassen des Hilfsbremsventilknopfs die Luft aus den Pneumatikzylindern und dem Sensor nicht freigegeben wird, d. h. die Hilfsbremse nicht abschaltet, müssen Sie den atmosphärischen Auslass im Ventil überprüfen.
Im Winter gefriert es oft und im atmosphärischen Auslass bildet sich ein Schlammeispfropfen, der verhindert, dass Luft den Kreislauf verlässt.
Wenn in diesem Fall das Einlassventil im Hilfsbremsventil seine Dichtung verliert, schaltet sich die Bremse spontan ein und der Motor stoppt ohne ersichtlichen Grund.
Wenn im Hilfsbremskreis keine Luft vorhanden ist, kann der Motor gestartet werden, stoppt jedoch nach einigen Minuten spontan aufgrund der Luftzufuhr über ein defektes Ventil zum Kraftstoffabsperr-Pneumatikzylinder.
Dieser Wasserhahn muss ausgetauscht werden. Wenn es zu keinem spontanen Motorstopp kommt, er aber nach dem Loslassen des Zusatzbremsventilknopfs während der Fahrt nicht anspringt, reicht es aus, den atmosphärischen Auslass des Ventils zu reinigen.