Das Beschleunigerventil versorgt die Energiespeicher mit Druckluft und soll die Ansprechzeit des Feststell- und Ersatzbremsantriebs verkürzen, indem es die Länge der Druckluft-Einlassleitung in die Federenergiespeicher verkürzt und von dort in die abgibt Atmosphäre
Es besteht aus einer Steuerkammer 2, einem Kolben 3, einem Auslassventil 1 und einem Einlassventil 4 sowie einer Einlassventilfeder 5. Der Anschluss III.
wird ständig mit Druckluft aus dem Empfänger versorgt
Klemme IV ist mit dem Handbremsventil verbunden, Klemme I ist mit den Hohlräumen der Zylinder von Federspeichern verbunden, Klemme II > ist mit der Atmosphäre verbunden.
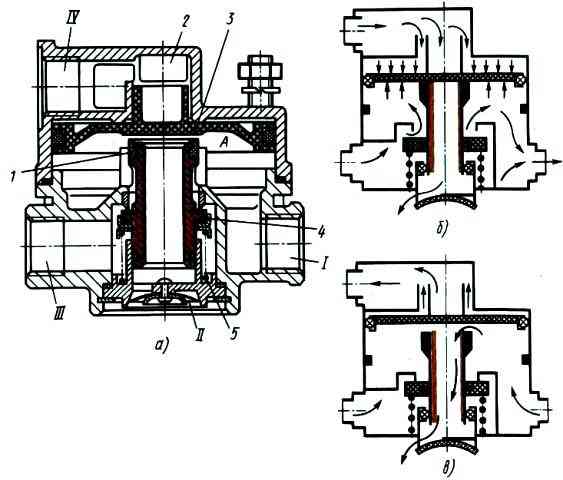
In der Ausgangsstellung, wenn das Auto losgelassen wird (Abb. b), befindet sich Kolben 3 in der unteren Position, unter dem Einfluss von Druckluft ist das Auslassventil 1 geschlossen, das Einlassventil 4 ist geöffnet, da das Die Fläche des oberen Teils des Kolbens 3 ist größer als die Fläche des unteren, und der Druck in Hohlraum A und Kammer 2 ist gleich.
Der Ausgang I ist vom atmosphärischen Ausgang II getrennt und die Kolben der Federspeicher stehen unter Druckluftdruck und wirken nicht auf die Bremszylinderstangen .
Beim Bremsen (Abb. 1c) wird Druckluft aus Kammer 2 durch den atmosphärischen Auslass des Handbremsventils in die Atmosphäre abgegeben.
Wenn der Druck in Kammer 2 sinkt, bewegt sich Kolben 3 nach oben, Einlassventil 4 schließt unter der Wirkung der Feder 5 und Auslassventil 1 öffnet.
Über den Auslass I und das geöffnete Auslassventil 1 kommunizieren die Hohlräume der Federenergiespeicher mit dem atmosphärischen Auslass II.
Der Druck in den Zylinderräumen von Federspeichern nimmt ab, die Federn dehnen sich aus und die Bremsmechanismen werden abgebremst.
Die Freigabe erfolgt durch Zufuhr von Druckluft vom Hahn zum Anschluss IV und dann in Kammer 2.
Der sich nach unten bewegende Kolben 3 öffnet zuerst das Auslassventil 1 und dann das Einlassventil 4.
Druckluft gelangt vom Empfänger in den Hohlraum der Federspeicher.
Der Druck in den Hohlräumen der Zylinder von Federspeichern steigt, die Federn werden komprimiert und die Bremsmechanismen werden gelöst.
Die Proportionalität zwischen dem Steuerdruck im Anschluss IV und dem Druck in den Hohlräumen der Federspeicher (im Anschluss I) wird durch Kolben 3 aufrechterhalten.
Wenn im Auslass I ein bestimmter Druck erreicht ist, bewegt sich der Kolben 3 unter der Wirkung der Feder 5 bis zum geschlossenen Einlassventil 4 und der weitere Druckanstieg stoppt.
Wenn der Druck im Anschluss IV abnimmt, bewegt sich Kolben 3 unter dem Einfluss des höheren Drucks im Anschluss I nach oben und löst sich vom Auslassventil 1.
Druckluft aus den Hohlräumen von Federenergiespeichern entweicht durch das geöffnete Ventil 1 und den atmosphärischen Auslass II in die Atmosphäre, der Druck im Hohlraum A sinkt.
Relaisventil austauschen
Das Relaisventil muss ausgetauscht werden, wenn folgende Störungen auftreten:
- - Verletzung der Ventildichtheit. Ein äußeres Zeichen ist Luftleckage durch die Anschlüsse, an denen die Abdeckung am Ventilgehäuse befestigt ist;
- - mechanische Beschädigung des Ventilkörpers, der Abdeckung und der Kolben, die den Betrieb beeinträchtigt
Benötigte Werkzeuge: Schraubenschlüssel 22x24, 17x19, 12x13, Schraubenschlüssel 13x17, Schraubstock
Relaisventil ausbauen
Wir bereiten das Auto vor und entlüften die Empfänger des 19. Kreises des Parksystems
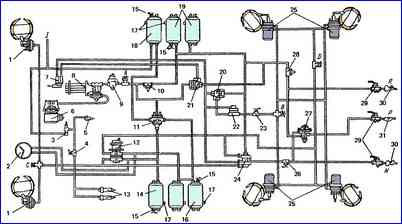
Diagramm des pneumatischen Antriebs der Bremssysteme: 1 - Bremskammern Typ 24; 2 - Manometer; 3 - Steuerventil des Hilfsbremssystems; 4 - pneumoelektrischer Schalter für das Anhängermagnetventil; 5 - Pneumatikzylinder zum Antrieb des Motorstopphebels; 6 - Kompressor; 7 - Steuerventil des Feststellbremssystems; 8 - Wasserabscheider; 9 - Druckregler; 10, 28 - einzelne Schutzventile; elf - dreifaches Sicherheitsventil; 12 - zweiteiliges Bremsventil; 13 - Pneumatikzylinder zum Antrieb der Klappen des Hilfsbremssystemmechanismus; 14 - Schaltungsempfänger; 1.15 - Schalter der Druckabfall-Warnleuchte; 16 - Schaltungsempfänger; 11.17 - Kondensatablasshähne; 18 - Verbraucherempfänger; 19 Empfänger der Schaltung III; 20 – Zweileitungs-Bypassventil zum Lösen der Notbremse; 21 - Zweileitungs-Bypassventil; 22 - Beschleunigerventil; 23 - Schalter für die Warnleuchte der Feststellbremsanlage; 25 - Bremskammern; 24 - Steuerventil für die Bremssysteme eines Anhängers mit Zweiradantrieb; 26 - Schalter für Bremssignal-Warnleuchte; 27 - Steuerventil für Anhängerbremsanlagen mit Einzelantrieb; 29 - Trennventile; 30 - Verbindungsköpfe vom Typ „Palm“; 31 - Verbindungskopf Typ A; A, B, C, D – Ventile der Steueranschlüsse; P - zur Versorgungsleitung des Zweiradantriebs; R - zur Verbindungsleitung des Einzelantriebs; N - zur Brems(steuer)leitung des Zweiradantriebs
Schrauben Sie die Überwurfmuttern der Rohrleitungen ab, die an die Anschlüsse des Beschleunigungsventils 22 und des Zweileitungsventils 20 angeschlossen sind
Lösen Sie die Muttern, mit denen die Beschleunigerventilhalterung am Rahmen befestigt ist. Trennen Sie die Rohrleitungen von den Ventilinseln und entfernen Sie Ventil 22 zusammen mit Ventil 20 und Halterung
Trennen Sie das Beschleunigerventil von der Halterung, indem Sie die Halterungsmuttern lösen
Ventil 20 mit Durchgangsverschraubung vom Ventil 22 trennen
Einbau des Relaisventils
Montieren Sie die Halterung am Ventil und befestigen Sie sie mit Muttern. Befestigen Sie das Zweileitungsventil 20 zusammen mit der Durchführungsverschraubung
Montieren Sie das zusammengebaute Ventil mit Halterung am Rahmen und befestigen Sie es mit Muttern
Führen Sie die Rohrleitungen in die Ventilinseln ein, ziehen Sie die Überwurfmuttern der Rohrleitungen fest und befestigen Sie das Ventil mit der Halterung am Rahmen
Überwurfmuttern der Rohrleitungen an den Ventilinseln festziehen
Starten Sie den Motor und erzeugen Sie Druck im pneumatischen Antrieb der Bremssysteme
Überprüfen Sie die Dichtheit der Rohrleitungen und des Relaisventils. Luftlecks sind nicht zulässig
Überprüfung der Funktion des Gaspedalventils beim Bremsen und Loslassen des Fahrzeugs
Reparatur des Beschleunigerventils
Benötigte Werkzeuge: ein Schraubstock mit weichen Backen, ein 13x17-Steckschlüssel, Spezialzange I801.23.000-01, Utensilien zum Waschen von Teilen
Demontage des Beschleunigerventils
Einbau des Ventils in einen Schraubstock
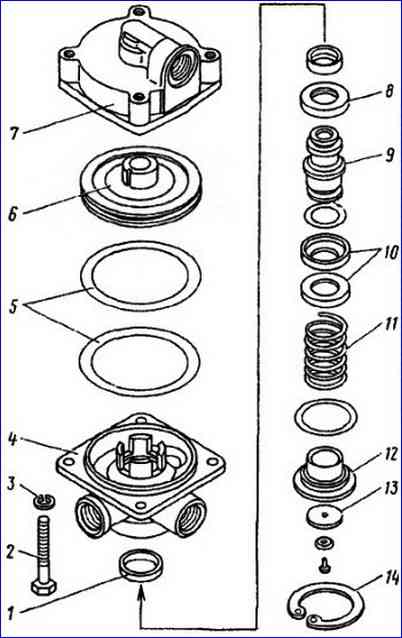
Schrauben Sie die Schrauben 2 mit Unterlegscheiben 3 ab, mit denen das obere Gehäuse 7 am unteren Gehäuse 4 befestigt ist
Entfernen Sie den Oberkörper aus dem Schraubstock
Entfernen Sie den Druckring 14 vom unteren Gehäuse 4, Gehäuse 9 mit Einlass- und Auslassventilen, Feder 11, Führungskappe 12
Entfernen Sie den Unterkörper 4 aus dem Schraubstock
Kolben 6 mit Dichtringen 5 aus dem oberen Gehäuse 7 entfernen
Hinweis: Beaufschlagen Sie den Ventildeckel mit Druckluft und entfernen Sie den Kolben
Wir waschen die Ventilteile in Dieselkraftstoff und blasen mit Druckluft
Zusammenbau des Relaisventils
Befestigen Sie den unteren Körper 4 in einem Schraubstock
In Gehäuse 4 Führungskappe 12, Feder 11, Gehäuse 9, Ring 8, Kappe 10, Ventil 13, Druckring 14 einbauen
Komplett mit Kolben 6 in Gehäuse 7 einbauen
Wir schrauben die Schrauben 2 ein, mit denen das Gehäuse 7 der Abdeckung am Gehäuse 4 mit Federscheiben 3 befestigt ist
Entfernen Sie das Ventil aus dem Schraubstock
Wir prüfen das Relaisventil auf Funktionsfähigkeit und Dichtheit
Reihenfolge der Tests:
- Schließen Sie das Gerät gemäß dem in der Abbildung gezeigten Diagramm an
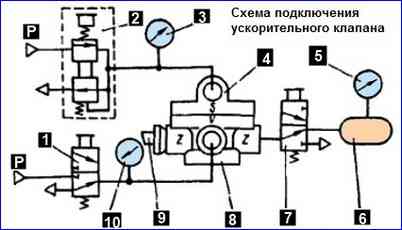
- - Öffnen Sie Ventil 7. Stellen Sie mit dem Präzisionsregelventil 2 den Druck am Manometer 3 auf 736 kPa (7,5 kgf/cm 2) ein.
Es darf keine Luftleckage aus dem Auslassfenster 8 des Geräts 4 und durch das eingeschaltete Ventil 7 auftreten. Ventil 2 Feinregulierung schließen
- - Wasserhahn 1 öffnen. Luft tritt aus Auslassfenster 8, Gerät 4 und durch Hahn 7 sollte nicht eingeschaltet sein. Schließen Sie den Hahn 7
- - Öffnen und schließen Sie Ventil 2 dreimal schnell für eine präzise Steuerung. In diesem Fall sollte sich der Druck am Manometer 5 von 0 auf 736 kPa (7,5 kgf/cm 2) und zurück ändern
- - Erhöhen Sie den Druck am Manometer 3 langsam über das Feinregulierventil 2. Wenn der Druck auf Manometer 3 29,4–44,1 kPa (0,3–0,45 kgf/cm 2) erreicht, sollte Manometer 5 anfangen, Druck anzuzeigen
- - Erhöhen Sie den Druck am Manometer 3 auf 736 kPa (7,5 kgf/cm 2). In diesem Fall sollte der Druck am Manometer 5 synchron ansteigen. Bei einem Druck am Manometer 3 von 647–687 kPa (6,6–7,0 kgf/cm 2) sollte der Druck am Manometer 5 716,1 kPa (7,3 kgf/cm 2 )
- - Mit Hilfe des Präzisionsregelventils 2 reduzieren wir den Druck am Manometer 3 langsam auf 0, am Manometer 5 sollte der Druck synchron auf 0 sinken
Die schrittweise Druckänderung während aller Tests sollte 19,6 kPa (0,2 kgf/cm 2) nicht überschreiten.
Während des Tests sollte es bei keinem Druck am Anschluss S zu Luftlecks aus den Geräten 4 kommen.