На двигуні встановлюють дві головки циліндрів. Кожна головка центрується двома фіксуючими втулками-штифтами, що запресовані в блок циліндрів
У головках циліндрів запресовані напрямні втулки та сідла клапанів.
Втулки клапанів – металокерамічні. Внутрішній діаметр втулки впускного клапана 9 +0,022 мм, а випускного 11 +0,022 мм.
Допустиме знос отвору напрямних втулок клапанів не повинно перевищувати 0,05 мм. При більшому збільшенні внутрішнього діаметра втулки слід замінити.
Для запасних частин клапани випускають стандартного розміру, а втулки — із внутрішнім діаметром, зменшеним на 0,3 мм, тобто з припуском під розгортання після запресування в головку циліндрів.
Зношену втулку випресовують за допомогою вибивання. Нову втулку запресовують за допомогою завзятої оправки з боку коромисел.
Втулка над площиною під пружину клапана має виступати не більше ніж на 22 мм.
Після запресування отвір втулки клапана розгортають до відповідного стандартного розміру.
Сідла клапанів виготовлені з чавуну.
Дрібні дефекти робочої поверхні сідла можна усунути в процесі притирання клапана до сідла, а глибокі ризики та інші великі дефекти — шліфуванням сідла з наступним притиранням клапана до сідла.
Щільність посадки клапана в сідлі залежить також від концентричності робочої фаски сідла та отвору напрямної втулки.
Концентричність сідла заміряють індикаторним пристроєм.
Базою є отвір напрямної втулки клапана, а ніжка індикатора ковзає по робочій поверхні сідла.
Неконцентричність, допустима без ремонту, не повинна перевищувати 0,06 мм.
При заміні сідла клапанів видаляють за допомогою твердосплавних зенкерів.
Перед встановленням сідла ремонтного розміру його гніздо в головці циліндрів розточують до розмірів:
Для сідла впускного клапана 49,25 +0.027 мм та випускного - 38,75 +0,027 мм.
Перед запресовуванням у головку циліндрів сідла та направляючі втулки клапанів охолоджують у твердому двоокисі вуглецю (сухому льоді), а головку циліндрів нагрівають до 160—175°С.
Холодні сідла та втулки при складанні повинні входити до гнізда нагрітої головки циліндрів вільно або з невеликим зусиллям.
Під легкими ударами молотка по оправці сідло та втулка клапана повинні сісти на місце.
У жодному разі не можна забивати сідло або втулку з великим зусиллям, оскільки при цьому порушується посадка, і надалі при роботі двигуна сідло або втулка можуть випасти зі свого гнізда.
Операцію зі встановлення сідел та втулок у головку циліндрів необхідно виконувати швидко.
При вирівнюванні температур у цьому з'єднанні з'являються великі натяги, при яких подальше запресування неможливе без великих зусиль.
Робочі фаски знову встановлених сідел прошліфувати концентрично отворам у напрямних втулках клапанів. Для цього використовують спеціальний пристрій.
Розжимну довідку встановлюють в оброблений отвір втулки, а хвостовик оправлення служить віссю для шліфувального кола (привід електродвигуна) з фаскою під кутом 45°.
При шліфуванні має бути забезпечена концентричність робочої фаски сідла та отвори втулки клапана 0,03 мм (за індикатором).
Головка циліндрів, що надходить на складання, має бути ретельно промита, сорочка охолодження має бути очищена від накипу та бруду, масляні канали — від шламу, а випускні канали — від нагару.
Запресовані в головку блоку напрямні втулки клапанів повинні бути номінальними або одного з ремонтних розмірів і марковані фарбою. Розміри втулок та їх маркування зазначені у табл. 1.
Відстань від верхнього торця напрямної втулки до площини головки повинна бути 24 мм.
Сідла впускних та випускних клапанів повинні бути шліфовані під 45° до осі напрямних втулок.
Ширина робочої фаски сідла має бути 1,5 - 2,0 мм.
Биття конічних поверхонь всіх сідел клапана щодо осей отворів напрямних втулок клапанів — не більше 0,025 мм.
Запресовані в головку циліндрів напрямні втулки клапанів по зовнішньому діаметру можуть бути номінального розміру або ремонтного (збільшеного на 0,25 мм).
Таблиця 1. Номінальний та ремонтні розміри напрямної втулки клапана
- Номінальний розмір, маркування - жовтий, внутрішній діаметр напрямної втулки клапана - 9,00+0,022 мм;
- Перший ремонт, зменшення діаметра на 0,20 мм, маркування - білий, внутрішній діаметр напрямної втулки клапана - 8,80+0,022 мм;
- Другий ремонт, збільшення діаметра на 0,20 мм, маркування - зелений, внутрішній діаметр напрямної втулки клапана - 9,20+0,022 мм
Впускний та випускний клапани
Діаметри стрижнів клапанів повинні бути номінального або одного з ремонтних розмірів, наведених у таблиці.
Таблиця 2. Номінальні та ремонтні розміри стрижнів клапанів
- Номінальний розмір, маркування - жовтий, діаметр стержня впускного клапана - 9,0 -0,050 мм, діаметр стрижня випускного клапана - 9,0 -0,075 мм;
- Перший ремонт, зменшення діаметра на 0,20 мм, маркування - білий, діаметр стрижня впускного клапана - 8,80 -0,050 мм, діаметр стрижня випускного клапана - 8,80 -0,075 мм;
- Другий ремонт, збільшення діаметра на 0,20 мм, маркування - зелений, діаметр стрижня впускного клапана - 9,2 -0,050 мм, діаметр стрижня випускного клапана - 9,2 -0,075 мм
Робоча фаска головки клапана має бути шліфована під кутом 45° до осі стрижня.
Чистота робочої поверхні фаски після шліфування має відповідати 8-му класу.
Биття робочої поверхні фаски щодо стрижня клапана не більше 0,03 мм.
Складання та встановлення головки циліндрів
Перед встановленням клапани та отвори напрямних втулок повинні бути ретельно протерті.
Клапани зі стрижнями номінального або ремонтного розміру повинні бути встановлені у напрямні втулки відповідного розміру.
Перед складанням клапани повинні бути притерті до сідла в головці циліндрів.
Притирання виробляти пастою, що складається з однієї частини мікропорошку М20 ГОСТ 3647—59 і двох частин олії індустріальна 20 (веретенна).
Після притирання робочі фаски клапанів і сідел повинні мати по всьому колу суцільну матову смужку контакту шириною не менше ½ ширини фаски сідла.
Притерті клапани нумерують по своїх сідлах і після цього не знеособлюють.
Після притирання деталі потрібно ретельно промити.
Якість притирання повинна бути перевірена на герметичність (при надмірному тиску в 0,05 кг/см 2 кількість повітря, що пропускається клапаном, може бути не більше 12 см 3 хвилину).
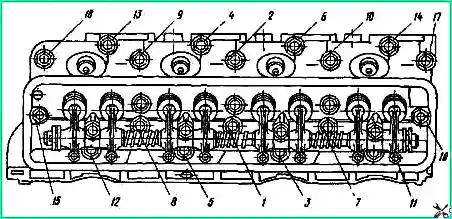
Порядок розміщення шпильок кріплення стійок осі коромисел та випускного трубопроводу:
а) шпильки стійок М10х1 L = 112 мм - дві крайні;
шпильки стійок М10х1 L = 80 мм — дві середні;
б) шпильки кріплення впускного трубопроводу:
- крайні М10х1 L = 30 мм;
- середні М10х1 L = 42 мм.
Перед установкою головки циліндрів у зборі з клапанами та випускним трубопроводом шпильки кріплення головки повинні бути вкручені в блок до відмови в порядку, зазначеному на рис. 1 та таблиці.
Прокладка головки циліндрів не повинна мати тріщин і фарбування азбесту.
Перед постановкою голівку потрібно ретельно продути стисненим повітрям.
Головка циліндрів повинна бути вільно без ударів одягнена на шпильки і встановлена на два штифти.
При затягуванні гайок шпильок головки циліндрів дотримуватись порядку, вказаного на рис. 1.
Гайки затягують у два прийоми попередньо та остаточно.
Момент затягування має бути в межах 7,3—7,8 кгм.
Остаточну затяжку потрібно проводити на холодному двигуні.
Після гарячої обкатки та повного остигання двигуна перевірити момент затяжки, який має бути 7,3—7,8 кГм.
При підтягуванні гайок головки циліндрів гайки кріплення впускного трубопроводу послабити.
Таблиця 3. Порядок встановлення шпильок кріплення головки циліндрів
Номер шпильок по порядку / розмір шпильки та її номер:
- 12-5-3-11/291859-П; М11х1L=170;
- 3-1-7-16/291860-П; М11х1L=208;
- 17-10-2-9-18/291826-П; М11х1L=195;
- 13-4-6-14/291823-П; М11х1L=108;
- 15 у правому ряду циліндра / 291826-П; М11х1L=208;
- 15 у лівому ряду циліндра / 291826-П; М11х1L=195
Складання та встановлення осі з коромислами та стійками
Перед складанням внутрішню порожнину осі коромисел ретельно очистити від шламу, бруду тощо і продути стисненим повітрям. Зовнішню поверхню протерти серветкою і змастити тонким шаром веретеної олії.
Зібрані коромисла на осі повинні вільно прокручуватися без заїдань.
Регулювальний гвинт повинен вільно без заїдань ввертатися в коромисло.
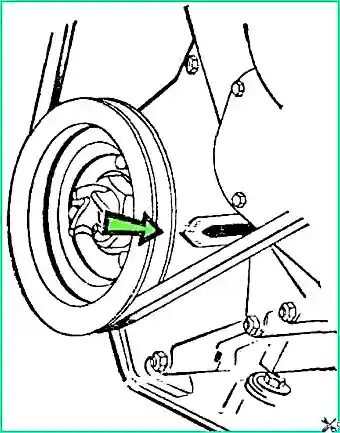
Осі коромисел з коромислами та стійками в зборі встановлювати на шпильки головки блоку так, щоб у гнізда коромисел увійшли головки штанг штовхачів.
Зазор між клапанами та коромислом на холодному двигуні має бути в межах 0,25—0,30 мм.
Регулювання зазору проводити в наступному порядку: повернути колінчастий вал у положення, що відповідає ст. м. т. ходу стиску в першому циліндрі, для чого:
- - закрити пальцем отвір для свічки першого циліндра, повернути колінчастий вал до початку виходу стисненого повітря з-під пальця. Це станеться на початку ходу стиснення;
- - обережно повернути колінчастий вал до збігу ризики на шківі колінчастого валу з центральною ризиком покажчика ст. м. т. (рис. 2), розташованого на передній кришці блоку, і відрегулювати зазори між клапанами та коромислами першого циліндра.
Потім, повертаючи колінчастий вал щоразу на 90˚, відрегулювати зазори клапанів решти семи циліндрів у порядку їх роботи 5-4-2-6-З-7 та 8.
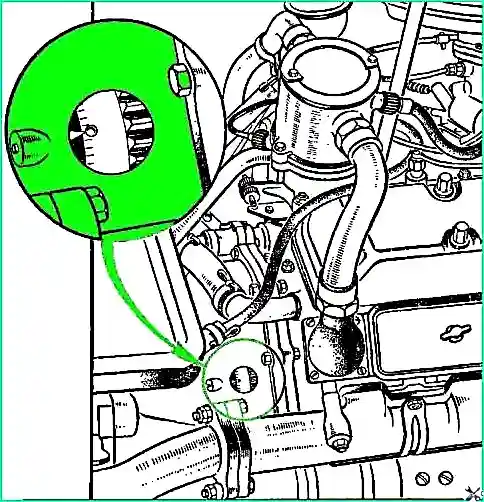