Hay dos culatas instaladas en el motor. Cada culata está centrada mediante dos pasadores de bloqueo presionados en el bloque de cilindros
Los casquillos guía y los asientos de válvula se presionan en las culatas.
Los casquillos de válvula son metal-cerámicos. El diámetro interior del manguito de la válvula de admisión es de 9 +0,022 mm y el de la válvula de escape es de 11 +0,022 mm.
El desgaste permitido del orificio de la guía de la válvula no debe exceder los 0,05 mm. Si el diámetro interior del casquillo aumenta aún más, se debe reemplazar.
Para las piezas de repuesto, las válvulas se fabrican en un tamaño estándar y los casquillos se fabrican con un diámetro interno reducido en 0,3 mm, es decir, con un margen de expansión después de presionar en la culata.
El casquillo desgastado se extrae utilizando un punzón. El casquillo nuevo se introduce a presión mediante un mandril de empuje desde el lado del balancín.
El casquillo situado encima del plano debajo del resorte de la válvula no debe sobresalir más de 22 mm.
Después de presionar, el orificio del manguito de la válvula se escaria hasta alcanzar el tamaño estándar apropiado.
Los
asientos de válvula están hechos de hierro fundido.
Los defectos menores en la superficie de trabajo del asiento se pueden eliminar durante el proceso de lapeado de la válvula al asiento, y los rayones profundos y otros defectos grandes se pueden eliminar rectificando el asiento y luego lapeando la válvula al asiento.
El ajuste perfecto de la válvula en el asiento también depende de la concentricidad del chaflán de trabajo del asiento y del orificio en el casquillo guía.
La concentricidad del sillín se mide con un dispositivo indicador.
La base es el orificio en la guía de la válvula y la pata indicadora se desliza a lo largo de la superficie de trabajo del asiento.
La falta de concentricidad aceptable sin reparación no debe exceder los 0,06 mm.
Al reemplazar, los asientos de las válvulas se retiran utilizando avellanadores de carburo.
Antes de instalar un asiento del tamaño de reparación, se perfora su asiento en la culata con las siguientes dimensiones:
Para el asiento de la válvula de admisión 49,25 +0,027 mm y escape - 38,75 +0,027 mm.
Antes de presionarlos en la culata, los asientos y las guías de las válvulas se enfrían en dióxido de carbono sólido (hielo seco) y la culata se calienta a 160-175 °C.
Los asientos y casquillos fríos durante el montaje deben encajar en los casquillos de la culata calentada libremente o con poco esfuerzo.
Al golpear ligeramente el mandril con un martillo, el asiento de la válvula y el manguito de la válvula deberían encajar en su lugar.
Bajo ninguna circunstancia se debe golpear con mucha fuerza el asiento o casquillo, ya que esto alterará el ajuste, y posteriormente cuando el motor esté en marcha, el asiento o casquillo podría caerse de su asiento.
La operación de instalación de asientos y casquillos en la culata debe realizarse rápidamente.
Cuando las temperaturas se igualan, aparecen grandes tensiones en este sentido, en las que es imposible seguir presionando sin un gran esfuerzo.
Muele los chaflanes de trabajo de los asientos recién instalados de forma concéntrica con los orificios de las guías de válvula. Para ello se utiliza un dispositivo especial.
La guía de expansión se instala en el orificio mecanizado del manguito y el vástago de la guía sirve como eje para la muela abrasiva (accionamiento desde un motor eléctrico) con un chaflán en un ángulo de 45°.
Al rectificar, la concentricidad del chaflán de trabajo del asiento y el orificio del manguito de la válvula debe ser de 0,03 mm (según el indicador).
La culata que llega para el montaje debe lavarse minuciosamente, la camisa de refrigeración debe limpiarse de incrustaciones y suciedad, los canales de aceite deben limpiarse de lodos y los canales de escape deben limpiarse de depósitos de carbón.
Las guías de válvula presionadas en la cabeza del bloque deben ser de tamaño nominal o uno de los tamaños de reparación y estar marcadas con pintura. Las dimensiones de los casquillos y sus marcas se indican en la tabla. 1.
La distancia desde el extremo superior del casquillo guía hasta el plano de la cabeza debe ser de 24 mm.
Los asientos de las válvulas de admisión y escape deben rectificarse a 45° con respecto al eje de los casquillos guía.
El ancho del chaflán de trabajo del asiento debe ser de 1,5 - 2,0 mm.
El descentramiento de las superficies cónicas de todos los asientos de válvula en relación con los ejes de los orificios de la guía de válvula no es superior a 0,025 mm.
Las guías de válvula presionadas en la culata a lo largo del diámetro exterior pueden ser de tamaño nominal o tamaño de reparación (aumentado en 0,25 mm).
Tabla 1. Dimensiones nominales y de reparación de la guía de válvula
- Tamaño nominal, marca: amarillo, diámetro interior de la guía de válvula: 9,00 +0,022 mm;
- Primera reparación, reducción del diámetro en 0,20 mm, marca - blanca, diámetro interno de la guía de la válvula - 8,80 +0,022 mm;
- Segunda reparación, aumento del diámetro en 0,20 mm, marca - verde, diámetro interno de la guía de la válvula - 9,20 +0,022 mm
Válvulas de admisión y escape
Los diámetros de los vástagos de las válvulas deben ser nominales o uno de los tamaños de reparación en, dado en la tabla.
Tabla 2. Dimensiones nominales y de reparación de vástagos de válvulas
- Tamaño nominal, marca - amarillo, diámetro del vástago de la válvula de admisión - 9,0 -0,050 mm, diámetro del vástago de la válvula de escape - 9,0 -0,075 mm;
- Primera reparación, reducción del diámetro en 0,20 mm, marca - blanca, diámetro del vástago de la válvula de admisión - 8,80 -0,050 mm, diámetro del vástago de la válvula de escape - 8,80 -0,075 mm;
- Segunda reparación, aumento del diámetro en 0,20 mm, marca - verde, diámetro del vástago de la válvula de admisión - 9,2 -0,050 mm, diámetro del vástago de la válvula de escape - 9,2 -0,075 mm
El chaflán de trabajo de la cabeza de la válvula debe rectificarse en un ángulo de 45° con respecto al eje del vástago.
La limpieza de la superficie de trabajo del chaflán después del rectificado debe corresponder a la clase 8.
El descentramiento de la superficie de trabajo del chaflán en relación con el vástago de la válvula no es superior a 0,03 mm.
Montaje e instalación de la culata
Antes de la instalación, las válvulas y los orificios del casquillo guía se deben limpiar minuciosamente.
Las válvulas con vástagos de tamaño nominal o de reparación deben instalarse en casquillos guía del tamaño adecuado.
Antes del montaje, las válvulas deben esmerilarse en los asientos de la culata.
El lapeado debe realizarse con una pasta compuesta por una parte de micropolvo M20 GOST 3647-59 y dos partes de aceite industrial 20 (husillo).
Después del pulido, los chaflanes de trabajo de válvulas y asientos deben tener una banda de contacto mate continua a lo largo de toda la circunferencia con un ancho de al menos la mitad del ancho del chaflán del asiento.
Las válvulas lapeadas están numeradas por sus asientos y no se anonimizan posteriormente.
Después del pulido, las piezas deben lavarse a fondo.
Se debe comprobar la estanqueidad de la calidad del triturado (con un exceso de presión de 0,05 kg/cm 2 la cantidad de aire que pasa a través de la válvula no puede ser superior a 12 cm 3 en minutos).
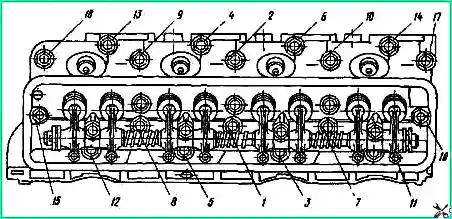
El orden de colocación de los pernos para sujetar los puntales del eje del balancín y el tubo de escape:
a) montantes de poste M10x1 L = 112 mm - dos exteriores;
montantes de poste M10x1 L = 80 mm - dos del medio;
b) pernos de montaje del colector de admisión:
- extremo M10x1 L = 30 mm;
- mediano M10x1 L = 42 mm.
Antes de instalar el conjunto de culata con válvulas y tubo de escape, los pernos de montaje de la culata deben atornillarse completamente al bloque en el orden que se muestra en la Fig. 1 y tabla.
La junta de culata no debe presentar grietas ni desconchones de amianto.
Antes de la instalación, se debe soplar a fondo el cabezal con aire comprimido.
La culata debe colocarse libremente sobre los espárragos sin impactos e instalarse sobre dos pasadores.
Al apretar las tuercas de los espárragos de la culata del cilindro, siga el orden que se muestra en la Fig. 1.
Las tuercas se aprietan en dos etapas, preliminar y final.
El par de apriete debe estar en el rango de 7,3-7,8 kgm.
El apriete final debe realizarse con el motor frío.
Después de un rodaje en caliente y un enfriamiento completo del motor, compruebe el par de apriete, que debe ser de 7,3-7,8 kgm.
Al apretar las tuercas de la culata, afloje las tuercas del colector de admisión.
Tabla 3. Orden de instalación de los espárragos de culata
Número de montantes en orden / tamaño de montante y su número:
- 12-5-3-11 / 291859-P; M11x1L=170;
- 3-1-7-16 / 291860-P; M11x1L=208;
- 17-10-2-9-18 / 291826-P; M11x1L=195;
- 13-4-6-14 / 291823-P; M11x1L=108;
- 15 en la fila derecha del cilindro / 291826-P; M11x1L=208;
- 15 en la fila izquierda del cilindro / 291826-P; М11х1L=195
Montaje e instalación de un eje con balancines y puntales
Antes del montaje, limpie a fondo la cavidad interna del eje del balancín de lodos, suciedad, etc. y sople con aire comprimido. Limpie la superficie exterior con una servilleta y lubrique con una fina capa de aceite para husillos.
Los balancines ensamblados en el eje deben girar libremente sin atascarse.
El tornillo de ajuste debe atornillarse libremente en el balancín sin atascarse.
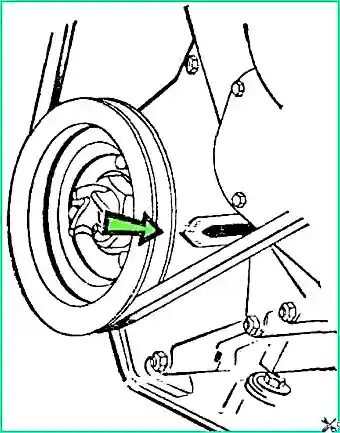
Instale los ejes de los balancines con los conjuntos de balancines y puntales en los pernos de la cabeza del bloque de modo que las cabezas de las varillas de empuje encajen en los casquillos de los balancines.
El espacio entre las válvulas y el balancín en un motor frío debe estar entre 0,25 y 0,30 mm.
Ajuste la separación en el siguiente orden: gire el cigüeñal a la posición correspondiente a c. monte . carrera de compresión en el primer cilindro, para lo cual:
- - cierre el orificio para la bujía del primer cilindro con el dedo, gire el cigüeñal hasta que comience a salir aire comprimido por debajo del dedo. Esto sucederá al comienzo de la carrera de compresión;
- - girar con cuidado el cigüeñal hasta que las marcas de la polea del cigüeñal coincidan con la marca central del puntero c. m. t. (Fig. 2), ubicado en la tapa frontal del bloque, y ajuste los espacios entre las válvulas y los balancines del primer cilindro.
Luego, girando el cigüeñal 90˚ cada vez, ajuste las holguras de las válvulas de los siete cilindros restantes en el orden de funcionamiento 5-4-2-6-3-7 y 8.
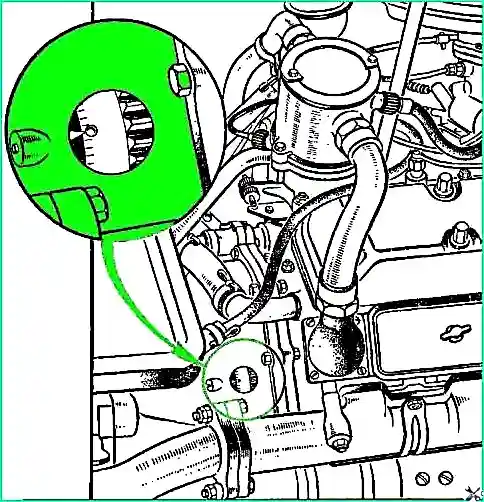