Am Motor sind zwei Zylinderköpfe verbaut. Jeder Kopf wird durch zwei in den Zylinderblock eingepresste Sicherungsstifte zentriert
Führungsbuchsen und Ventilsitze werden in die Zylinderköpfe eingepresst.
Ventilbuchsen bestehen aus Metallkeramik. Der Innendurchmesser der Einlassventilhülse beträgt 9 +0,022 mm und der des Auslassventils 11 +0,022 mm.
Der zulässige Verschleiß der Ventilführungsbohrung sollte 0,05 mm nicht überschreiten. Wenn der Innendurchmesser der Buchse weiter zunimmt, sollte diese ausgetauscht werden.
Für Ersatzteile werden Ventile in Standardgröße und Buchsen mit einem um 0,3 mm verringerten Innendurchmesser hergestellt, d. h. mit einem Spielraum für die Ausdehnung nach dem Einpressen in den Zylinderkopf.
Die verschlissene Buchse wird mit einem Dorn herausgedrückt. Die neue Buchse wird mit einem Druckdorn von der Kipphebelseite her eingepresst.
Die Buchse über der Ebene unter der Ventilfeder sollte nicht mehr als 22 mm hervorstehen.
Nach dem Pressen wird das Ventilhülsenloch auf die entsprechende Standardgröße aufgebohrt.
Ventilsitze bestehen aus Gusseisen.
Kleinere Defekte in der Arbeitsfläche des Sitzes können durch das Läppen des Ventils auf den Sitz beseitigt werden, und tiefe Kratzer und andere große Defekte können durch Schleifen des Sitzes und anschließendes Läppen des Ventils auf den Sitz beseitigt werden.
Der feste Sitz des Ventils im Sitz hängt auch von der Konzentrizität der Arbeitsfase des Sitzes und der Bohrung in der Führungshülse ab.
Die Rundlaufgenauigkeit des Sattels wird mit einem Indikatorgerät gemessen.
Die Basis ist das Loch in der Ventilführung, und das Anzeigebein gleitet entlang der Arbeitsfläche des Sitzes.
Eine ohne Reparatur akzeptable Nichtkonzentrizität sollte 0,06 mm nicht überschreiten.
Beim Austausch werden die Ventilsitze mit Hartmetallsenkern entfernt.
Vor dem Einbau eines Sitzes in Reparaturgröße wird dessen Sitz im Zylinderkopf auf folgende Maße aufgebohrt:
Für den Einlassventilsitz 49,25 +0,027 mm und für den Auslass - 38,75 +0,027 mm.
Ventilsitze und Führungen werden vor dem Einpressen in den Zylinderkopf in festem Kohlendioxid (Trockeneis) gekühlt und der Zylinderkopf auf 160–175 °C erhitzt.
Bei der Montage kalte Sitze und Buchsen sollten frei oder mit geringem Kraftaufwand in die Buchsen des beheizten Zylinderkopfs passen.
Durch leichte Schläge mit einem Hammer auf den Dorn sollten Ventilsitz und Ventilhülse einrasten.
Auf keinen Fall darf der Sitz oder die Buchse mit großer Kraft eingeschlagen werden, da dies den Sitz stört und später bei laufendem Motor der Sitz oder die Buchse aus dem Sitz fallen kann.
Der Einbau von Sitzen und Buchsen in den Zylinderkopf muss schnell erfolgen.
Beim Temperaturausgleich treten in diesem Zusammenhang große Spannungen auf, bei denen ein weiteres Pressen ohne großen Kraftaufwand nicht möglich ist.
Schleifen Sie die Arbeitsfasen der neu eingebauten Sitze konzentrisch zu den Löchern in den Ventilführungen. Hierzu wird ein spezielles Gerät verwendet.
Die Spreizführung wird in das bearbeitete Loch der Hülse eingebaut und der Schaft der Führung dient als Achse für die Schleifscheibe (Antrieb durch einen Elektromotor) mit einer Fase im 45°-Winkel.
Beim Schleifen muss die Konzentrizität der Arbeitsfase des Sitzes und der Ventilhülsenbohrung 0,03 mm betragen (laut Anzeige).
Der zur Montage gelieferte Zylinderkopf muss gründlich gewaschen werden, der Kühlmantel muss von Zunder und Schmutz gereinigt werden, die Ölkanäle müssen von Schlamm befreit werden und die Abgaskanäle müssen von Kohlenstoffablagerungen befreit werden.
In den Blockkopf eingepresste Ventilführungen müssen die Nenngröße oder eine der Reparaturgrößen haben und mit Farbe gekennzeichnet sein. Die Abmessungen der Buchsen und deren Markierungen sind in der Tabelle angegeben. 1.
Der Abstand vom oberen Ende der Führungshülse bis zur Kopfebene sollte 24 mm betragen.
Einlass- und Auslassventilsitze müssen im 45°-Winkel zur Achse der Führungsbuchsen geschliffen werden.
Die Breite der Arbeitsfase des Sitzes sollte 1,5 - 2,0 mm betragen.
Die Unrundheit der konischen Flächen aller Ventilsitze relativ zu den Achsen der Ventilführungslöcher beträgt nicht mehr als 0,025 mm.
Ventilführungen, die entlang des Außendurchmessers in den Zylinderkopf eingepresst sind, können Nennmaß oder Reparaturmaß (um 0,25 mm erhöht) haben.
Tabelle 1. Nenn- und Reparaturmaße der Ventilführung
- Nenngröße, Markierung - gelb, Innendurchmesser der Ventilführung - 9,00 +0,022 mm;
- Erste Reparatur, Durchmesserreduzierung um 0,20 mm, Markierung - weiß, Innendurchmesser der Ventilführung - 8,80 +0,022 mm;
- Zweite Reparatur, Durchmesservergrößerung um 0,20 mm, Markierung - grün, Innendurchmesser der Ventilführung - 9,20 +0,022 mm
Einlass- und Auslassventile
Die Durchmesser der Ventilschäfte müssen dem Nenndurchmesser oder einer der Reparaturgrößen entsprechen in, in der Tabelle angegeben.
Tabelle 2. Nenn- und Reparaturabmessungen von Ventilschäften
- Nenngröße, Markierung – gelb, Einlassventilschaftdurchmesser – 9,0–0,050 mm, Auslassventilschaftdurchmesser – 9,0–0,075 mm;
- Erste Reparatur, Durchmesserreduzierung um 0,20 mm, Markierung – weiß, Einlassventilschaftdurchmesser – 8,80 – 0,050 mm, Auslassventilschaftdurchmesser – 8,80 – 0,075 mm;
- Zweite Reparatur, Durchmesservergrößerung um 0,20 mm, Markierung – grün, Einlassventilschaftdurchmesser – 9,2 – 0,050 mm, Auslassventilschaftdurchmesser – 9,2 – 0,075 mm
Die Arbeitsfase des Ventilkopfes muss in einem Winkel von 45° zur Schaftachse geschliffen werden.
Die Sauberkeit der Arbeitsfläche der Fase nach dem Schleifen muss der Klasse 8 entsprechen.
Die Unrundheit der Arbeitsfläche der Fase relativ zum Ventilschaft beträgt nicht mehr als 0,03 mm.
Zylinderkopf zusammenbauen und einbauen
Vor dem Einbau müssen Ventile und Führungsbuchsenlöcher gründlich abgewischt werden.
Ventile mit Spindeln in Nenn- oder Reparaturgröße müssen in Führungsbuchsen der entsprechenden Größe eingebaut werden.
Vor dem Zusammenbau müssen die Ventile in die Sitze im Zylinderkopf eingeschliffen werden.
Das Läppen sollte mit einer Paste erfolgen, die aus einem Teil Mikropulver M20 GOST 3647-59 und zwei Teilen Industrieöl 20 (Spindel) besteht.
Nach dem Einschleifen müssen die Arbeitsfasen von Ventilen und Sitzen über den gesamten Umfang einen durchgehenden matten Kontaktstreifen mit einer Breite von mindestens der halben Breite der Sitzfase aufweisen.
Geläppte Ventile werden anhand ihres Sitzes nummeriert und anschließend nicht mehr identifiziert.
Nach dem Einschleifen müssen die Teile gründlich gewaschen werden.
Die Mahlqualität muss auf Dichtheit überprüft werden (bei einem Überdruck von 0,05 kg/cm 2 darf die durch das Ventil geleitete Luftmenge nicht mehr als 12 cm 3 betragen in Minuten).
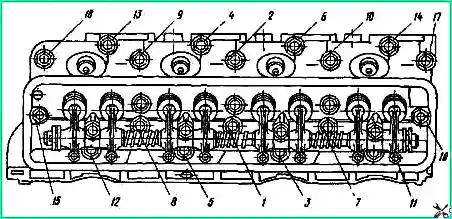
Die Reihenfolge der Platzierung der Stehbolzen zur Befestigung der Kipphebelachsstreben und der Abgasleitung:
a) Pfostenbolzen M10x1 L = 112 mm – zwei äußere;
Pfostenbolzen M10x1 L = 80 mm – zwei mittlere;
b) Ansaugkrümmer-Befestigungsbolzen:
- extrem M10x1 L = 30 mm;
- mittel M10x1 L = 42 mm.
Vor dem Einbau der Zylinderkopfbaugruppe mit Ventilen und Auspuffrohr müssen die Kopfbefestigungsbolzen in der in Abb. gezeigten Reihenfolge vollständig in den Block eingeschraubt werden. 1 und Tabelle.
Die Zylinderkopfdichtung darf keine Risse oder Asbestabsplitterungen aufweisen.
Vor der Montage muss der Kopf gründlich mit Druckluft ausgeblasen werden.
Der Zylinderkopf muss frei und ohne Stöße auf die Stehbolzen aufgesetzt und auf zwei Stiften montiert werden.
Halten Sie beim Anziehen der Zylinderkopf-Stehbolzenmuttern die in Abb. gezeigte Reihenfolge ein. 1.
Das Anziehen der Muttern erfolgt in zwei Schritten, vorläufig und endgültig.
Das Anzugsdrehmoment sollte im Bereich von 7,3–7,8 kgm liegen.
Das endgültige Festziehen muss bei kaltem Motor erfolgen.
Überprüfen Sie nach einem Warmlauf und vollständiger Abkühlung des Motors das Anzugsdrehmoment, das 7,3–7,8 kgm betragen sollte.
Lösen Sie beim Anziehen der Zylinderkopfmuttern die Muttern des Ansaugkrümmers.
Tabelle 3. Einbaureihenfolge der Zylinderkopfbolzen
Anzahl der Stollen in der Reihenfolge / Größe des Stollens und seine Anzahl:
- 12-5-3-11 / 291859-P; M11x1L=170;
- 3-1-7-16 / 291860-P; M11x1L=208;
- 17-10-2-9-18 / 291826-P; M11x1L=195;
- 13-4-6-14 / 291823-P; M11x1L=108;
- 15 in der rechten Reihe des Zylinders / 291826-P; M11x1L=208;
- 15 in der linken Reihe des Zylinders / 291826-P; М11х1L=195
Montage und Einbau einer Achse mit Kipphebeln und Federbeinen
Reinigen Sie vor dem Zusammenbau den inneren Hohlraum der Kipphebelachse gründlich von Schlamm, Schmutz usw. und blasen Sie ihn mit Druckluft aus. Wischen Sie die Außenfläche mit einer Serviette ab und schmieren Sie sie mit einer dünnen Schicht Spindelöl.
Die montierten Kipphebel an der Achse sollten sich frei drehen lassen, ohne zu blockieren.
Die Einstellschraube sollte sich frei in den Kipphebel einschrauben lassen, ohne zu verklemmen.
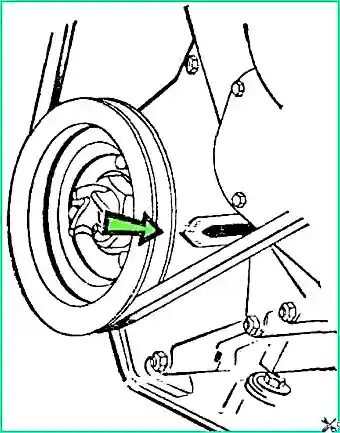
Montieren Sie die Kipphebelachsen mit Kipphebel- und Strebenbaugruppen auf den Blockkopfbolzen, sodass die Köpfe der Schubstangen in die Kipphebelsockel passen.
Der Spalt zwischen den Ventilen und dem Kipphebel sollte bei kaltem Motor zwischen 0,25 und 0,30 mm liegen.
Stellen Sie den Abstand in der folgenden Reihenfolge ein: Drehen Sie die Kurbelwelle in die Position, die c entspricht. m.t. Kompressionshub im ersten Zylinder, für den:
- - Verschließen Sie das Loch für die Zündkerze des ersten Zylinders mit Ihrem Finger und drehen Sie die Kurbelwelle, bis Druckluft unter dem Finger austritt. Dies geschieht zu Beginn des Kompressionshubs;
- - Drehen Sie die Kurbelwelle vorsichtig, bis die Markierungen auf der Kurbelwellenriemenscheibe mit der mittleren Markierung des Zeigers c übereinstimmen. m. t. (Abb. 2), befindet sich auf der vorderen Abdeckung des Blocks und stellt die Abstände zwischen den Ventilen und Kipphebeln des ersten Zylinders ein.
Stellen Sie dann, indem Sie die Kurbelwelle jedes Mal um 90° drehen, das Ventilspiel der verbleibenden sieben Zylinder in der Reihenfolge ihrer Betätigung ein: 5-4-2-6-3-7 und 8.
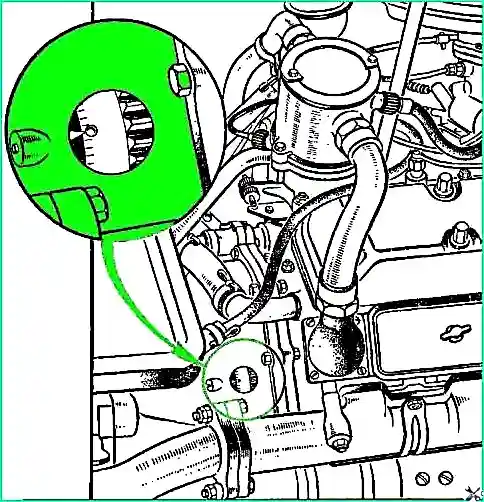