The LADA VESTA family of cars uses a fuel supply system with a drainless fuel rail
The function of the fuel supply system is to ensure the supply of the required amount of fuel to the engine in all operating modes.
Fuel is supplied to the engine by injectors installed in the intake pipe.
An electric fuel pump installed in the fuel tank supplies fuel through fuel pipes to the injector rail.
A fuel pressure regulator built into the electric fuel pump maintains the fuel pressure supplied to the injectors within 364-400 kPa, depending on the engine operating mode.
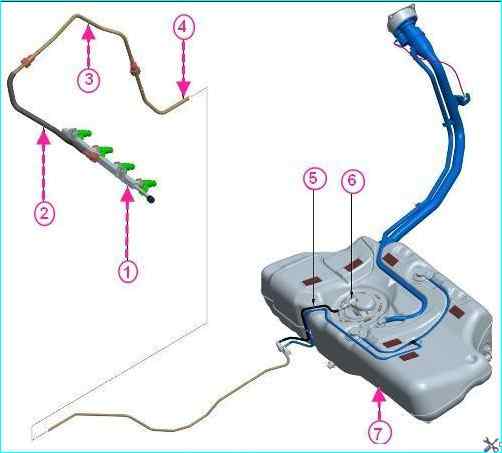
The controller turns on the fuel injectors sequentially.
Each of the injectors is turned on every 720° of crankshaft rotation.
The controller signal that controls the injector is a pulse, the duration of which corresponds to the amount of fuel required by the engine.
This pulse is supplied at a certain moment of crankshaft rotation, which depends on the engine operating mode.
The control signal supplied to the injector opens the normally closed valve of the injector, supplying fuel under pressure to the intake port.
The amount of fuel supplied is proportional to the time during which the injectors are open (injection pulse duration).
The controller maintains the optimal air/fuel ratio by changing the duration pulses.
Increasing the injection pulse duration increases the amount of fuel supplied at a constant air flow rate (enriching the mixture).
Decreasing the injection pulse duration decreases the amount of fuel supplied at a constant air flow rate (leaning the mixture).
Before servicing the fuel equipment, it is necessary to relieve the pressure in the fuel supply system.
Procedure for relieving pressure in the fuel supply system
- 1. Engage neutral gear, brake the car with the parking brake.
- 2. Remove fuse F26 (15A) from the mounting block.
- 3. Start the engine and let it idle until it stops due to running out of fuel.
- 4. Turn on the starter for 3 s to relieve pressure in the lines. After this, it is safe to work with the fuel supply system.
- 5. After releasing the pressure and completing the work, insert fuse F26 (15A) into the mounting block.
Electric fuel pump module (EFM)
The immersion-type EFM is installed in the fuel tank.
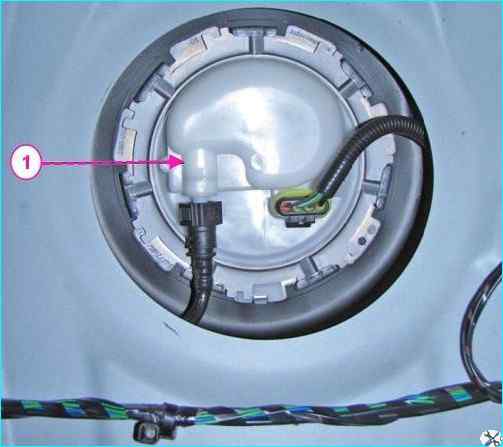
The EFM module includes a turbine-type electric fuel pump, a fuel pressure regulator, a fine fuel filter and a fuel level sensor fuel.
The pump supplies fuel from the fuel tank through the main fuel filter to the injector rail.
The electric fuel pump is switched on by the controller via a relay.
When the ignition is turned on, the controller powers the relay for 2 seconds to create the required fuel pressure in the injector rail.
If the engine does not start cranking during this time, the controller switches off the relay and waits for cranking to start. After it starts, the controller turns the relay on again.
If the ignition was turned on three times without cranking the engine, then the next activation of the electric fuel pump relay is possible only with the start of cranking.
Never allow the fuel to run out completely, as this can lead to premature wear and failure of the electric fuel pump.
Injector rail
The injector rail is a hollow tube with injectors installed on it. The injector rail is secured to the engine with two bolts.
Fuel under pressure is supplied to the internal cavity of the rail, and from there through the injectors to the intake pipe.
On the injector rail there is a nipple 2 for monitoring the fuel pressure, closed with a threaded plug.
A number of diagnostic procedures during vehicle maintenance or when troubleshooting require monitoring the fuel pressure.
Using a pressure gauge connected to the nipple, you can determine the pressure of the fuel supplied to the injectors.
Fuele injectors
The injector of the distributed injection system is an electromagnetic device that doses the supply of fuel under pressure into the engine intake pipe.
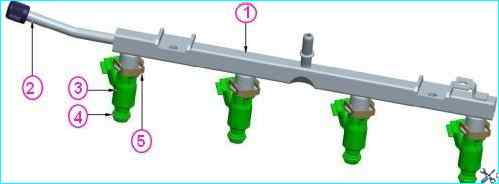
Injectors 3 are secured to the ramp using clips 5. The upper and lower ends of the injectors are sealed with sealing rings 4.
The controller controls the electromagnetic valve of the injector, which passes fuel through the guide plate, ensuring fuel atomization.
The guide plate has holes that direct the fuel, forming a conical torch.
The fuel torch is directed at the inlet valve. Before the fuel enters the combustion chamber, it evaporates and mixes with air.
An injector with a stuck valve in a partially open position causes a loss of pressure in the injector rail after the electric fuel pump is turned off, so on some engines an increase in cranking time will be observed.
In addition, an injector with a stuck valve can cause pre-ignition, since some fuel will enter the engine after it is turned off.
Fuel Delivery Control Modes
As mentioned earlier in this chapter, the amount of fuel delivered through the injectors is controlled by the controller.
Fuel is delivered using one of two different methods: synchronous, i.e. at a certain position of the crankshaft, or asynchronous, i.e. without synchronization with the crankshaft rotation.
Synchronized fuel supply is the predominantly used method.

Synchronization of the injector operation is ensured by using signals from the crankshaft position sensor and the phase sensor.
The controller calculates the moment of activation of each injector, and the fuel is injected once per one full working cycle of the corresponding cylinder.
This method allows for more accurate dosing of fuel to the cylinders and lowers the level of toxicity of exhaust gases.
Asynchronous fuel supply is used in the starting mode and dynamic modes of engine operation.
The controller processes the sensor signals, determines the engine operating mode and calculates the duration of the fuel injection pulse.
To increase the amount of fuel supplied, the duration of the injection pulse increases, to decrease it, it is shortened.
The duration of the injection pulse can be monitored using a diagnostic device.
Fuel supply is controlled in one of several modes described below.
Disabling fuel supply
Fuel supply is not performed in the following cases:
- - the ignition is off (this prevents pre-ignition);
- - the engine crankshaft does not rotate (no crankshaft position sensor signal);
- - if the controller has detected misfires in one or more cylinders, the fuel supply to these cylinders is stopped and the malfunction indicator starts to flash;
- - the engine crankshaft speed exceeds the limit of about 6200 rpm (the fuel supply is turned off together with the throttle valve closing and the ignition timing lowering);
- - when "rolling out" in gear, when "revving" the engine when the vehicle is stationary, if the engine speed exceeds 2000 rpm, the accelerator pedal is not pressed, the coolant temperature is above 40 °C.
Start mode
When the ignition is turned on, the controller uses a relay to turn on the electric fuel pump, which creates fuel pressure in the injector rail.
The controller processes the signal from the coolant temperature sensor to determine the required injection pulse duration start.
When the engine crankshaft starts to turn during start-up, the controller generates a pulse to turn on the injectors, the duration of which depends on the coolant temperature, cranking time and increase in speed.
On a cold engine, the injection pulse increases to increase the amount of fuel, and on a warm engine, the pulse duration decreases.
The system operates in start-up mode until a certain crankshaft speed (desired idle speed) is reached, the value of which depends on the coolant temperature.
A necessary condition for starting the engine is the engine speed must reach at least 80 rpm when the starter is cranked, and the voltage in the vehicle's electrical system must not be lower than 6 V.
Open-loop fuel supply control mode
After the engine has started and until the conditions for entering the closed-loop mode are met (the control oxygen sensor has warmed up to the required temperature), the controller controls the fuel supply in the open-loop mode.
In the open-loop mode, the controller calculates the duration of the injection pulses without taking into account the presence of oxygen in the exhaust gases.
The calculations are based on data on the crankshaft speed, mass air flow, coolant temperature and the requested torque (this is expressed in the position of the throttle valve, ignition timing and directly in the fuel supply), which can additionally be affected by the inclusion of electrical consumers (lights, seat heating, fan and etc.).
Power enrichment mode
The controller monitors the accelerator pedal position and crankshaft speed to determine when maximum engine power is required.
To develop maximum power, a richer fuel mixture is required (the UDC control mode is disabled), which is achieved by increasing the duration of the injection pulses.
Compensation for changes in on-board network voltage
When the on-board network voltage drops, energy accumulation in the ignition coils occurs more slowly, and the mechanical movement of the injector electromagnetic valve takes longer.
The controller compensates for the drop in on-board network voltage by increasing the energy accumulation time in the ignition coil and the duration of the injection pulses.
Accordingly, when the voltage in the vehicle's on-board network increases, the controller reduces the energy accumulation time in the ignition coil and the pulse duration injection.
Closed loop fuel control
The system enters closed loop mode when all of the following conditions are met:
- 1. The oxygen sensor is warm enough for normal operation (the "dew point" has been passed - the temperature on the ceramic of the HO2S sensing element exceeds the temperature determined depending on the ambient temperature, the output signal is outside the range of 1.2-1.7 V).
- 2. The coolant temperature is above a certain value.
- 3. The engine has run for a certain period of time since starting, depending on the coolant temperature at the time of starting.
- 4. The engine is not running in any of the following modes: engine start, fuel cut-off, maximum power mode, ECM protection mode.
- 5. The engine operates within a certain range based on the load parameter.
In closed-loop fuel control mode, the controller initially calculates the injection pulse duration based on the same sensors as in open-loop mode (basic calculation).
The difference is that in closed-loop mode, the controller uses the signal from the control oxygen sensor to adjust the injection pulse duration calculations to ensure maximum efficiency of the catalytic converter.
There are two types of fuel supply adjustments - current and self-learning adjustments.
The first (current) adjustment is calculated based on the oxygen sensor readings and can change relatively quickly to compensate for current deviations in the mixture composition from stoichiometric.
The second (self-learning adjustment) is calculated for each set of "rpm/load" parameters based on the current adjustment and changes relatively slowly.
The current adjustment is reset each time the ignition is turned off.
The self-learning adjustment is stored in the controller memory permanently, until the "ECU reset with initialization" mode is performed using the diagnostic tool.
The purpose of the adjustment based on the self-learning results is to compensate for deviations in the air-fuel mixture composition from the stoichiometric one, which arise as a result of the spread of the characteristics of the ECU elements, tolerances in the manufacture of the engine, as well as deviations in engine parameters during operation (wear, coking, etc.).
For more accurate compensation of the deviations that arise, the entire range of engine operation is divided into 4 characteristic learning zones:
- - idle;
- - high speed at low load;
- - partial loads;
- - high loads.
When the engine is operating in any of the zones, the injection pulse duration is adjusted according to a certain logic until the actual mixture composition reaches the optimal value.
When the engine operating mode is changed, the last value of the correction coefficient for the this zone.
The correction factors obtained in this way characterize a specific engine and participate in the calculation of the injection pulse duration when the system is operating in open loop mode and at start-up, without being able to change.
The correction value at which closed-loop fuel supply regulation is not required is 1 (for the fuel supply correction parameter based on the results of self-learning at idle, it is 0).
Any change from 1(0) indicates that the closed-loop fuel supply regulation function changes the injection pulse duration.
If the closed-loop fuel supply correction value is greater than 1(0), the injection pulse duration increases, i.e. the fuel supply increases.
If the closed-loop fuel supply correction value is less than 1(0), the injection pulse duration decreases, i.e. decrease in fuel supply.
The maximum range of change of the current fuel supply correction and self-learning correction is the range of 1±0.25 (±5).
If any of the correction coefficients goes beyond the regulation limits towards enrichment or depletion of the mixture, this indicates a malfunction in the engine or ECM (deviation of fuel pressure, air leakage, leak in the exhaust system, etc.).
Self-learning correction for regulating fuel supply on vehicles with a catalytic converter is a continuous process throughout the entire service life of the vehicle and ensures compliance with strict standards for exhaust gas toxicity.
In this ECM, when the battery is disconnected, the values of the adaptation correction coefficients are not reset.