Throttle Position Sensors
The system with EDP uses two TPS. TPS are part of the throttle body with an electric drive
TPS is a potentiometric resistor, to one of the terminals of which the reference voltage (5 V) from the controller is supplied, and to the second "ground" from the controller
The output signal of TPS is supplied to the controller from the terminal connected to the movable contact of the potentiometer.
The controller controls the position of the throttle valve using an electric drive in accordance with the position of the accelerator pedal.
Based on the TPS readings, the controller monitors the position of the throttle valve.
When the ignition is turned on, the controller sets the valve to the pre-start position, the degree of opening of which depends on the temperature of the coolant.
In the pre-start position of the throttle valve, the output signal of TPS 1 should be in within 0.58...0.70 V, the output signal of TPS 2 within 4.30...4.42 V.
If the engine is not started and the accelerator pedal is not pressed within 15 seconds, the controller de-energizes the electric drive of the throttle valve and the throttle valve is set to the position of 6-7% throttle opening.
In the de-energized state (LIMP HOME) of the electric drive of the throttle valve, the output signal of TPS 1 is within 0.70...0.75 V, the output signal of TPS 2 is within 4.25...4.30 V.
Then, if no action is taken within 15 seconds, the 0-position throttle valve check ("training") mode will begin - complete closing and opening of the throttle valve to the pre-start position and then the electric drive the throttle valve will again go into de-energized mode.
At any position of the throttle valve, the sum of the signals from TPS 1 and TPS 2 should be equal to (5±0.1) V.
If a malfunction of the TPS circuits occurs, the controller de-energizes the throttle valve electric drive, stores its code in its memory and turns on the indicator.
In this case, the throttle valve is set to the position of 6-7% throttle opening.
Air pressure and temperature sensor (APTS)
The air pressure and temperature sensor (APTS) is installed on the intake module (Fig. 1).
The DDTV includes an absolute pressure sensor in the intake manifold (MAP) and an intake air temperature sensor (IAT).
The output signal of the MAP connected to the controller is a DC voltage in the range of 0.15 ... 4.6 V, the value of which depends on the pressure in the intake manifold.
Based on this signal, the controller calculates the amount of air sucked into the intake manifold per cycle.
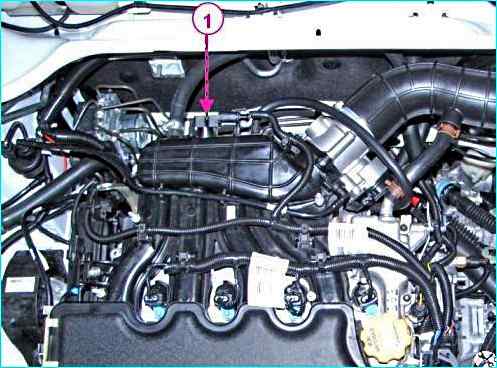
If a malfunction occurs in the MAP circuit, the controller stores its code in its memory and turns on the alarm.
In this case, the controller calculates the amount of air intake based on the crankshaft speed and the position of the throttle valve.
The sensing element of the MAP is a thermistor resistor that changes resistance depending on the temperature.
The output signal of the MAP connected to the controller is a DC voltage in the range of 0.3 ... 4.9 V, the value of which depends on the temperature of the air passing through the sensor.
If a malfunction occurs in the MAP circuit, the controller stores its code in its memory and turns on the alarm.
In this case, the controller replaces the sensor readings with a fixed air temperature value (32 °C).
Table of the dependence of the MAP resistance on the temperature of the intake air air:
Temperature ° C - Ohm Resistance:
- -40 - 42661-54224
- -30 - 23970-30015
- -20 - 14039-17333
- -10 - 8529.5-10399
- 0 - 5358-6458
- +5 - 4296-5150
- +10 - 3469-4137
- +20 - 2309-2727
- +30 - 1586-1853
Electronic accelerator pedal (EPA)
Cars with EDP use an electronic accelerator pedal (EPA), which electrically transmits a signal about the accelerator pedal position to the controller.
EPA is located on the bracket under the driver's right foot.
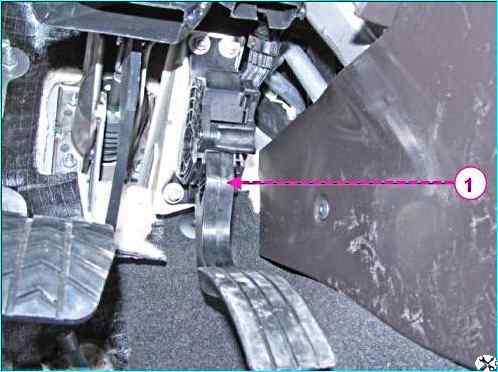
EPA uses two accelerator pedal position sensors (APPS).
APPS are potentiometric resistors to which voltage is supplied 5 V power supply from the controller.
DPPA are mechanically connected to the drive from pedal lever.
Two independent springs between the pedal lever and the housing create a return force.
By receiving an analog electrical signal from the EPA, the controller generates a signal to control the position of the throttle valve.
The output voltage of the EPA changes proportionally to pressing the accelerator pedal.
When the accelerator pedal is released, the signal from EPA 1 should be within 0.50 ... 0.85 V, the signal from EPA 2 should be within 0.25 ... 0.43 V.
When the accelerator pedal is fully pressed, the signal from EPA 1 should be within 4.19 ... 4.59 V, the signal from EPA 2 should be within 2.095 ... 2.295 V.
For any position of the accelerator pedal, the signal from EPA 1 should be in two times the signal of the DPPA 2.
Coolant temperature sensor (CTS)
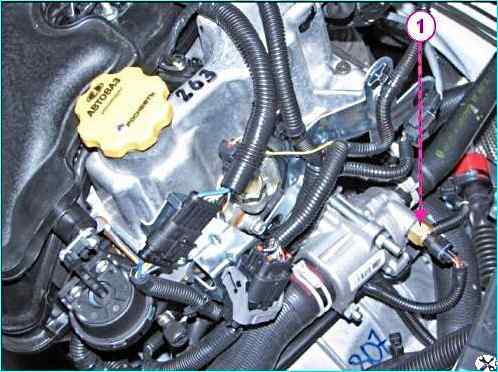
The sensor is installed in the flow of engine coolant on the thermostat, on the cylinder head.
The sensitive element of the coolant temperature sensor is a thermistor, i.e. a resistor whose electrical resistance changes depending on the temperature.
High temperature causes low resistance, and low coolant temperature - high resistance (see table 2).
The controller supplies 5 V to the coolant temperature sensor circuit.
The controller calculates the coolant temperature based on the voltage drop across the coolant temperature sensor.
The voltage drop is relatively high when the engine is cold and low when it is warm.
The coolant temperature is used in most engine management functions.
If a malfunction occurs in the coolant temperature sensor circuit, the controller stores its code in its memory, turns on the alarm and the cooling system fan, and calculates the coolant temperature using a special algorithm.
Be careful when working with the sensor.
Damage to the sensor may result in disruption of the normal operation of the engine management system.
Table of dependence of the coolant temperature sensor resistance on the coolant temperature (±2%):
Temperature ° C - Resistance Om:
- -40 - 100700
- -30 - 52700
- -20 - 28680
- -15 - 21450
- -10 - 16180
- -5 - 12300
- 0 – 9420
- +5 - 7280
- +10 - 5670
- +15 - 4450
- +20 - 3520
- +25 - 2796
- +30 - 2238
- +40 – 1459
- +45 - 1188
- +50 - 973
- +60 - 667
- +70 - 467
- +80 - 332
- +90 - 241
- +100 - 177
Knock sensor (DS)
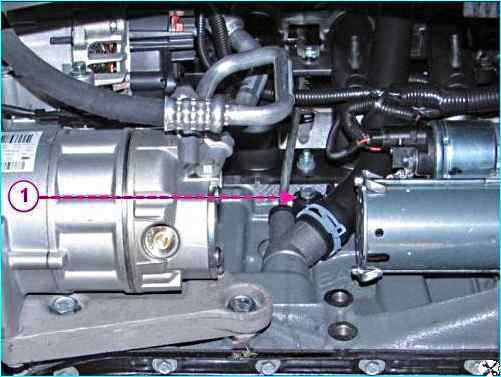
The knock sensor (KS) is installed on the cylinder block.
The piezoelectric sensitive element of the KS generates an alternating current voltage signal, the amplitude and frequency of which correspond to the parameters of engine vibrations.
When detonation occurs, the amplitude of vibrations of a certain frequency increases.
The controller adjusts the ignition timing to suppress detonation.
When a malfunction of the KS circuits occurs, the controller stores its code in its memory and turns on the alarm.
To determine and eliminate the malfunction, it is necessary to use the appropriate diagnostic card.
Control oxygen sensor (COS)
The most effective reduction in the toxicity of exhaust gases of gasoline engines is achieved with a mass ratio of air and fuel in the mixture (14.5-14.6): 1.
This ratio is called stoichiometric. With this composition of the fuel-air mixture, the catalytic converter most effectively reduces the amount of hydrocarbons, carbon monoxide and nitrogen oxides emitted with the exhaust gases.
To optimize the composition of the exhaust gases in order to achieve the greatest efficiency of the converter, closed-loop fuel supply control with feedback on the presence of oxygen in the exhaust gases is used.
The controller calculates the injection pulse duration based on parameters such as air mass flow, crankshaft speed, coolant temperature, etc.
To adjust the calculations of the injection pulse duration, information about the presence of oxygen in the exhaust gases, which is provided by the oxygen sensor, is used.
The UDC is installed on the intake pipe. Its sensitive element is located in the exhaust gas flow. The UDC generates a voltage that changes which is in the range of 180...950 mV.
This output voltage depends on the presence or absence of oxygen in the exhaust gases and on the temperature of the sensing element of the UDC.
When the UDC is cold, the output signal of the sensor is absent, since in this state its internal electrical resistance is very high - several MOhms.
As the sensor warms up, the resistance drops and the ability to generate an output signal appears.
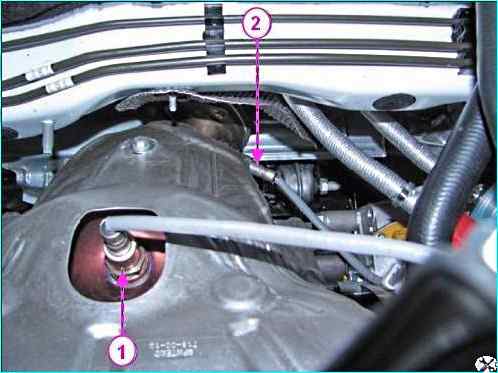
For efficient operation, the O2 sensor must have a temperature of at least 300°C.
For quick warm-up after starting the engine, the O2 sensor is equipped with an internal electric heating element controlled by the controller.
The duty cycle of the heater control pulse signals (the ratio of the on-state duration to the pulse repetition period) depends on the O2 sensor temperature and the engine operating mode.
If the sensor temperature is above 300°C, then at the moment of crossing the stoichiometry point, the sensor output signal switches between a low level (180…250 mV) and a high level (850…950 mV).
A low signal level corresponds to a lean mixture (oxygen present), a high signal corresponds to a rich mixture (oxygen absent).
Description of circuit operation
The controller outputs to the circuit UDC stable reference voltage of 1.7 V. When the UDC is not warmed up, the sensor output voltage is in the range of 1.2 ... 1.7 V.
As the sensor warms up, its internal resistance decreases, and it begins to generate a changing voltage that goes beyond this range.
By changing the voltage, the controller determines that the UDC has warmed up, and its output signal can be used to control the fuel supply in closed loop mode.
During normal operation of the fuel supply system in closed loop mode, the output voltage of the UDC changes between low and high levels.
Oxygen sensor poisoning
The UDC can be poisoned as a result of using leaded gasoline or using sealants vulcanizing at room temperature during assembly, which contain a large amount of silicone (silicon compounds) with high volatility.
Silicone vapors can enter the crankcase ventilation system and be present during the process combustion.
The presence of lead or silicon compounds in the exhaust gases can cause the O2 sensor to fail.
O2 sensor circuit faults, sensor poisoning, or unheated condition can cause the signal voltage to remain in the range of 1.2-1.7 V for a long time. In this case, the controller will store a corresponding fault code.
Fuel supply will be controlled in an open circuit.
If the controller receives a signal with a voltage indicating a long-term lean condition, the corresponding fault code (low oxygen sensor signal) will be stored in its memory.
The cause of the fault may be a short circuit in the O2 sensor output circuit to ground, a leak in the air intake system, or low fuel pressure.
If the controller receives a signal with a voltage indicating a long-term rich condition, the corresponding fault code will be stored in its memory. (High oxygen sensor signal level).
The cause of the malfunction may be a short circuit in the O2 sensor output circuit to a voltage source or increased fuel pressure in the injector rail.
When oxygen sensor malfunction codes occur, the controller controls the fuel supply in open loop mode.
Oxygen sensor maintenance
If the harness, connector or plugs of the oxygen sensor are damaged, the O2 sensor must be replaced. Repair of the harness, connector or plugs is not allowed.
For normal operation, the O2 sensor must communicate with atmospheric air. Communication with the atmospheric air is ensured by air gaps in the sensor wires.
Attempts to repair wires, connectors or plugs may disrupt communication with the atmospheric air and impair the operation of the sensor.
When servicing the sensor, the following requirements must be observed:
Do not allow contact cleaning fluid or other materials to come into contact with the sensor or harness connectors. These materials may get into the sensor and cause malfunction. In addition, do not damage the insulation of the wires, leading to their exposure.
Do not strongly bend or twist the sensor harness and the injection system wiring harness connected to it. This may disrupt the flow of atmospheric air into the sensor.
To prevent malfunction as a result of water falling must not cause damage to the seal on the periphery of the control system harness block.
Handle the new sensor with care. Do not allow grease or dirt to come into contact with the sensor wiring harness connector or the slotted end of the sensor housing.
Diagnostic Oxygen Sensor (DOS)
A catalytic converter is used to reduce the content of hydrocarbons, carbon monoxide and nitrogen oxides in the exhaust gases.
The converter oxidizes hydrocarbons and carbon monoxide, as a result of which they are converted into water vapor and carbon dioxide.
The converter also restores nitrogen from nitrogen oxides.
The controller monitors the oxidation-reduction properties of the converter by analyzing the signal from the diagnostic oxygen sensor installed after the converter.
The DOS operates on the same principle as the UDC. The ODS generates a signal indicating the presence of oxygen in the exhaust gases at the inlet to the neutralizer.
The signal generated by the ODS indicates the presence of oxygen in the exhaust gases after the neutralizer.
If the neutralizer is operating normally, the ODS readings will differ significantly from the ODS readings.
The output signal of a warmed-up diagnostic oxygen sensor when operating in feedback mode, with a serviceable neutralizer in steady-state mode, should be in the range of 590 to 750 mV and should not repeat the ODS signal.
If a malfunction occurs in the circuits or the ODS itself, the controller stores its code in its memory and turns on the alarm, signaling the presence of a malfunction.
The ODS maintenance requirements are no different from those described above for the ODS.
Crankshaft Position Sensor (DPKV)
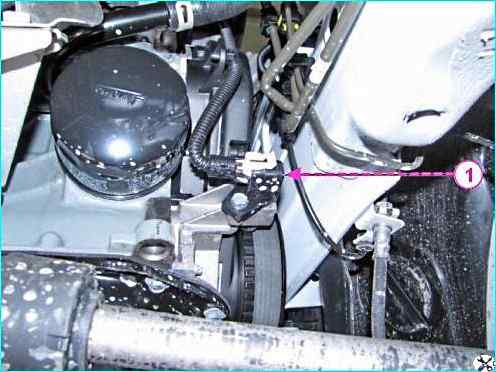
The crankshaft position sensor is installed on the oil pump cover at a distance of 0.9±0.5 mm from the top of the tooth of the timing disk, fixed on the engine crankshaft.
The timing disk is combined with the generator drive pulley and is a toothed wheel with 58 teeth located at a pitch of 6°, and a "long" depression for synchronization, formed by two missing teeth.
When the middle of the first tooth of the toothed sector of the disk after the "long" depression is aligned with the crankshaft position sensor axis, the engine crankshaft is in the position of 114° (19 teeth) before the top dead center of the 1st and 4th cylinders.
When the timing disk rotates, the magnetic flux in the sensor's magnetic circuit changes, inducing AC voltage pulses in its winding.
The controller determines the position and speed of the crankshaft by the number and frequency of these pulses and calculates the phase and duration of the control pulses for the injectors and ignition coil.
The crankshaft position sensor wires are protected from interference by a screen shorted to ground.
If a malfunction occurs in the crankshaft position sensor circuit, the engine stops working, the controller enters the malfunction code into its memory and turns on the alarm.
Phase sensor (DF)
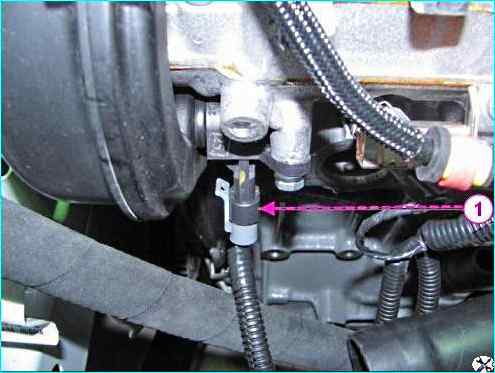
The phase sensor of the 21129 engine is installed on the cylinder head near the intake camshaft pulley.
The operating principle of the sensor is based on the Hall effect.
A timing disk with a slot is located on the intake camshaft pulley. When the slot passes through the phase sensor groove, the sensor sends a voltage pulse of the "ground" level (about 0 V) to the controller, which corresponds to the position of the piston of the 1st cylinder in the compression stroke.
The phase sensor signal is used by the controller to organize sequential fuel injection in accordance with the order of operation of the engine cylinders.
If a malfunction of the circuits or the phase sensor itself occurs, the controller stores its code in its memory and turns on the alarm.
Vehicle speed sensor (VSS)
On LADA VESTA family vehicles, information about the vehicle speed is sent to the ECM controller from the ABS control unit via the CAN bus.
Brake light switch
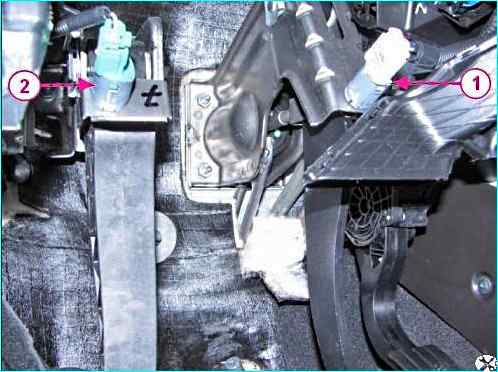
The brake light switch is part of the brake pedal assembly and is designed to send the appropriate signals to the ECM about the driver pressing/releasing the brake pedal.
In the throttle-by-wire (E-throttle) control systems, the brake pedal switch signals play an important role, since they are used by the ECM software safety function.
For this reason, it is very important to ensure that the brake light switch is always in working order.
If the switch electrical circuits are faulty, the vehicle engine may go into emergency operation mode with forcibly reduced power.
The brake light switch has two sets of contacts, the first of which switches the voltage from Terminal 15, and the second - the voltage from Terminal 30, which is supplied to the brake light lamp.
Both of these signals are sent to the ECM. When the brake pedal is released, the contacts of the first group should be normally closed, and the contacts of the second should be normally open.
Clutch pedal position signal switch (CPPS)
The CPPS is installed on LADA VESTA family vehicles with a manual transmission.
The switch is part of the clutch pedal unit and is designed to supply the control units with a signal about the clutch pedal being pressed.
The switch has one group of contacts that switches voltage from Terminal 15.
When the clutch pedal is pressed, the contacts are open.
The signal from the CPPS is used by the ECM software to improve the vehicle's driving characteristics.
On LADA VESTA family vehicles, information about the CPPS status is sent to the ECM from the BCM controller via the CAN bus.