Sensores de posición del acelerador
En el sistema con EDP se utilizan dos TPS. Los TPS son parte del cuerpo del acelerador con accionamiento eléctrico
El TPS es una resistencia potenciométrica, a uno de cuyos terminales se suministra la tensión de referencia (5 V) desde el controlador, y al segundo terminal la "tierra" desde el controlador
La señal de salida del TPS se envía al controlador desde el terminal conectado al contacto móvil del potenciómetro.
El controlador controla la posición de la válvula de mariposa mediante un accionamiento eléctrico de acuerdo con la posición del pedal del acelerador.
Basándose en las lecturas del TPS, el controlador monitorea la posición de la válvula del acelerador.
Al conectar el encendido, el controlador coloca la válvula en la posición previa al arranque, cuyo grado de apertura depende de la temperatura del refrigerante.
En la posición previa al arranque de la válvula del acelerador, la señal de salida del TPS 1 debe estar entre 0,58...0,70 V, la señal de salida del TPS 2 debe estar entre 4,30...4,42 V.
Si el motor no arranca y no se presiona el pedal del acelerador dentro de 15 segundos, el controlador desactiva el accionamiento eléctrico de la válvula del acelerador y la válvula del acelerador se establece en una apertura del acelerador del 6-7%.
En el estado desenergizado (LIMP HOME) del actuador del acelerador eléctrico, la señal de salida de TPS 1 está dentro de 0,70...0,75 V, la señal de salida de TPS 2 está dentro de 4,25...4,30 V.
Luego, si no se realiza ninguna acción dentro de los 15 segundos, comenzará el modo de prueba ("entrenamiento") de la válvula del acelerador en la posición 0: la válvula del acelerador se cerrará completamente y se abrirá a la posición previa al arranque, y luego el acelerador El accionamiento eléctrico de la válvula cambiará nuevamente al modo desenergizado.
En cualquier posición de la válvula de mariposa, la suma de las señales de TPS 1 y TPS 2 debe ser igual a (5±0,1) V.
Si ocurre un mal funcionamiento de los circuitos TPS, el controlador desenergiza el actuador del acelerador, almacena su código en su memoria y activa la alarma.
En este caso, la válvula del acelerador se establece en una posición de 6-7% de apertura del acelerador.
Sensor de presión y temperatura del aire (APTS)
El sensor de presión y temperatura del aire (APTS) está instalado en el módulo de admisión (Fig. 1).
El DDTV incluye un sensor de presión absoluta del colector (MAP) y un sensor de temperatura del aire de admisión (IAT).
La señal de salida del sensor MAP conectado al controlador es un voltaje CC en el rango de 0,15...4,6 V, cuyo valor depende de la presión en el colector de admisión.
En base a esta señal, el controlador calcula la cantidad de aire aspirado en el colector de admisión por ciclo.
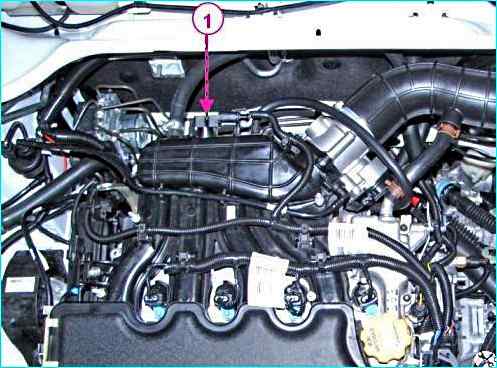
Cuando ocurre un mal funcionamiento en el circuito MAP, el controlador almacena su código en su memoria y activa la alarma.
En este caso, el controlador calcula la cantidad de aire que entra en función de la velocidad del cigüeñal y la posición del acelerador.
El elemento sensible del DTV es una resistencia termistor, que cambia la resistencia dependiendo de la temperatura.
La señal de salida del DTV conectado al controlador es un voltaje CC en el rango de 0,3...4,9 V, cuyo valor depende de la temperatura del aire que pasa a través del sensor.
Cuando ocurre un mal funcionamiento en el circuito DTV, el controlador almacena su código en su memoria y activa la alarma.
En este caso, el controlador reemplaza las lecturas del sensor con un valor fijo de temperatura del aire (32 °C).
Tabla de dependencia de la resistencia DTV con la temperatura del aire de admisión:
Temperatura °C - Resistencia Ohm:
- -40 - 42661-54224
- -30 - 23970-30015
- -20 - 14039-17333
- -10 - 8529,5-10399
- 0 - 5358-6458
- +5 - 4296-5150
- +10 - 3469-4137
- +20 - 2309-2727
- +30 - 1586-1853
Pedal acelerador electrónico (EPA)
Los automóviles con EDP utilizan un pedal acelerador electrónico (EPA), que transmite eléctricamente una señal sobre la posición del pedal acelerador al controlador.
La EPA está ubicada en un soporte debajo del pie derecho del conductor.
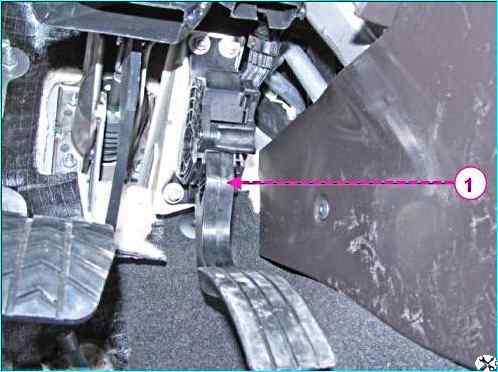
La EPA utiliza dos sensores de posición del pedal del acelerador (APPS).
Las DPPA son resistencias de tipo potenciométrico, a las que se les suministra una potencia de 5 V desde el controlador.
El DPPA está conectado mecánicamente al variador desde palanca de pedal.
Dos resortes independientes entre el brazo del pedal y el cuerpo crean la fuerza de retorno.
Al recibir una señal eléctrica analógica de la EPA, el controlador genera una señal para controlar la posición de la válvula del acelerador.
El voltaje de salida del DPPA cambia proporcionalmente a la presión del pedal del acelerador.
Cuando se suelta el pedal del acelerador, la señal de DPPA 1 debe estar entre 0,50 y 0,85 V, y la señal de DPPA 2 debe estar entre 0,25 y 0,43 V.
Cuando el pedal del acelerador está completamente presionado, la señal de DPPA 1 debe estar entre 4,19…4,59 V, la señal de DPPA 2 debe estar entre 2,095…2,295 V.
En cualquier posición del pedal del acelerador, la señal de DPPA 1 debe ser el doble de grande que la señal de DPPA 2.
Sensor de temperatura del refrigerante (CTS)
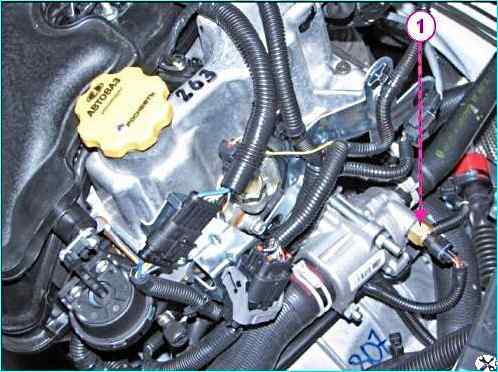
El sensor se instala en el flujo de refrigerante del motor, en el termostato, en la culata.
El elemento sensible del sensor de temperatura del refrigerante es un termistor, es decir, una resistencia cuya resistencia eléctrica cambia en función de la temperatura.
La temperatura alta provoca una baja resistencia, y la temperatura baja del refrigerante provoca una alta resistencia (consulte la Tabla 2).
El controlador suministra 5 V al circuito del sensor de temperatura del refrigerante.
El controlador calcula la temperatura del refrigerante en función de la caída de voltaje en el sensor de temperatura del refrigerante.
La caída de tensión es relativamente alta cuando el motor está frío y baja cuando está caliente.
La temperatura del refrigerante se utiliza en la mayoría de las funciones de gestión del motor.
Cuando ocurre un mal funcionamiento de los circuitos del sensor de temperatura del refrigerante, el controlador almacena su código en su memoria, enciende la alarma y el ventilador del sistema de enfriamiento y calcula el valor de la temperatura del refrigerante utilizando un algoritmo especial.
Tenga cuidado al trabajar con el sensor.
Los daños en el sensor pueden provocar que el sistema de gestión del motor no funcione correctamente.
Tabla de dependencia de la resistencia del sensor de temperatura del refrigerante con respecto a la temperatura del refrigerante (±2%):
Temperatura °C - Resistencia Ohm:
- -40 - 100700
- -30 - 52700
- -20 - 28680
- -15 - 21450
- -10 - 16180
- -5 - 12300
- 0 – 9420
- +5 - 7280
- +10 - 5670
- +15 - 4450
- +20 - 3520
- +25 - 2796
- +30 - 2238
- +40 – 1459
- +45 - 1188
- +50 - 973
- +60 - 667
- +70 - 467
- +80 - 332
- +90 - 241
- +100 - 177
Sensor de detonación (KS)
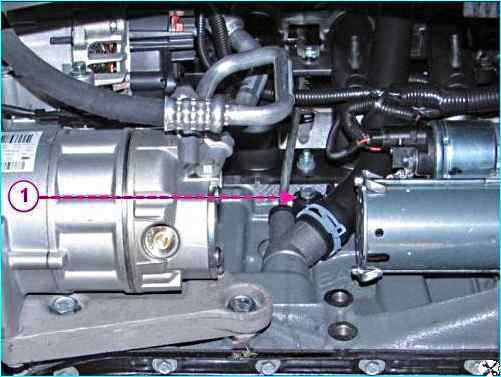
El sensor de detonación (KS) está instalado en el bloque de cilindros.
El elemento sensor piezoeléctrico del DD genera una señal de voltaje CA, cuya amplitud y frecuencia corresponden a los parámetros de vibración del motor.
Cuando se produce una detonación, la amplitud de las vibraciones de una determinada frecuencia aumenta.
El controlador ajusta el tiempo de encendido para suprimir la detonación.
Cuando ocurre una falla en los circuitos DD, el controlador almacena su código en su memoria y enciende la alarma.
Para identificar y eliminar el mal funcionamiento, es necesario utilizar la tarjeta de diagnóstico adecuada.
Sensor de control de oxígeno (OCS)
La reducción más efectiva de la toxicidad de los gases de escape de los motores de gasolina se logra con una relación de masa de aire y combustible en la mezcla (14,5-14,6): 1.
Esta relación se llama estequiométrica. Con esta composición de la mezcla aire-combustible, el convertidor catalítico reduce de forma más efectiva la cantidad de hidrocarburos, monóxido de carbono y óxidos de nitrógeno emitidos con los gases de escape.
Para optimizar la composición de los gases de escape con el fin de lograr la máxima eficiencia del neutralizador, se utiliza un control de suministro de combustible de circuito cerrado con retroalimentación de la presencia de oxígeno en los gases de escape.
El controlador calcula la duración del pulso de inyección en función de parámetros como el flujo de masa de aire, la velocidad del cigüeñal, la temperatura del refrigerante, etc.
La información sobre la presencia de oxígeno en los gases de escape, proporcionada por el sensor de oxígeno, se utiliza para ajustar los cálculos de la duración del pulso de inyección.
El UDC se instala en la tubería receptora. Su elemento sensible está situado en el flujo de gases de escape. UDC genera voltaje, cambios apareciendo en el rango de 180...950 mV.
Este voltaje de salida depende de la presencia o ausencia de oxígeno en los gases de escape y de la temperatura del elemento sensor del UDC.
Cuando el UDC está en estado frío, no hay señal de salida del sensor, ya que en este estado su resistencia eléctrica interna es muy alta: varios megaohmios.
A medida que el sensor se calienta, la resistencia disminuye y aparece la capacidad de generar una señal de salida.
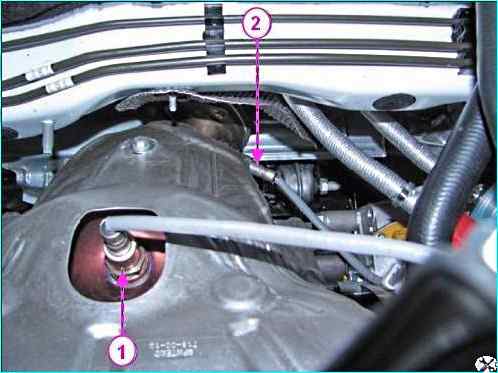
Para un funcionamiento eficiente, el UDC debe tener una temperatura de al menos 300 °C.
Para un calentamiento rápido después de arrancar el motor, el UDC está equipado con un elemento de calentamiento eléctrico interno, que es controlado por el controlador.
El ciclo de trabajo de las señales de pulso de control del calentador (la relación entre la duración del estado encendido y el período de repetición del pulso) depende de la temperatura del UDC y del modo de funcionamiento del motor.
Si la temperatura del sensor es superior a 300 °C, entonces, en el momento de transición a través del punto de estequiometría, la señal de salida del sensor cambia entre nivel bajo (180...250 mV) y alto (850...950 mV). .
Un nivel de señal bajo corresponde a una mezcla pobre (oxígeno presente), un nivel de señal alto corresponde a una mezcla rica (oxígeno ausente).
Descripción del funcionamiento del circuito
El controlador suministra un voltaje de referencia estable de 1,7 V al circuito UDC. Cuando el UDC no está calentado, el voltaje de salida del sensor está en el rango de 1,2...1,7 V.
A medida que el sensor se calienta, su resistencia interna disminuye y comienza a generar un voltaje cambiante que va más allá de este rango.
En función del cambio de voltaje, el controlador determina que el UDC se ha calentado y su señal de salida se puede utilizar para controlar el suministro de combustible en modo de circuito cerrado.
Durante el funcionamiento normal del sistema de combustible de circuito cerrado, el voltaje de salida del UDC alterna entre niveles bajos y altos.
Intoxicación por sensor de oxígeno
El UDC puede resultar envenenado por el uso de gasolina con plomo o por el uso de selladores vulcanizantes a temperatura ambiente que contengan grandes cantidades de silicona altamente volátil (compuestos de silicio) durante el ensamblaje.
Los vapores de silicona pueden ingresar al sistema de ventilación del cárter y estar presentes durante el proceso de combustión.
La presencia de compuestos de plomo o silicio en los gases de escape puede provocar la falla del UDC.
Los fallos de funcionamiento de los circuitos UDC, los defectos de los sensores, el envenenamiento o la falta de calentamiento pueden provocar que el voltaje de la señal permanezca en el rango de 1,2 a 1,7 V durante mucho tiempo. En este caso, se introducirá el código de error correspondiente en el controlador. memoria.
El control del suministro de combustible se realizará en circuito abierto.
Si el controlador recibe una señal de voltaje que indica una condición pobre a largo plazo, se almacena un código de falla correspondiente (señal de sensor de oxígeno bajo) en su memoria.
La causa del mal funcionamiento puede ser un cortocircuito en el circuito de salida del UDC a tierra, una fuga en el sistema de admisión de aire o baja presión de combustible.
Si el controlador recibe una señal de voltaje que indica una condición de mezcla enriquecida a largo plazo, se almacena un código de falla correspondiente (nivel alto de señal del sensor de oxígeno) en su memoria.
La causa del mal funcionamiento puede ser un cortocircuito en el circuito de salida del UDC a la fuente de voltaje o un aumento de la presión de combustible en el riel del inyector.
Cuando ocurren códigos de falla del sensor de oxígeno, el controlador controla el suministro de combustible en modo de circuito abierto.
Mantenimiento del sensor de oxígeno
Si el arnés, el conector o los enchufes del sensor de oxígeno están dañados, se debe reemplazar el sensor de oxígeno. No se permite la reparación del arnés, del conector ni de los enchufes.
Para su funcionamiento normal, el DC debe comunicarse con el aire atmosférico. La comunicación con el aire atmosférico está asegurada por espacios de aire en los cables del sensor.
Los intentos de reparar cables, conectores o enchufes pueden provocar la interrupción de la conexión de aire y el deterioro del funcionamiento de CC.
Al realizar el mantenimiento del DC, se deben cumplir los siguientes requisitos:
No permita que el líquido de limpieza de contactos u otros materiales entren en contacto con el sensor o las almohadillas del arnés. Estos materiales pueden ingresar al DK y provocar un mal funcionamiento. Además, no se permite dañar el aislamiento de los cables provocando su exposición.
Está prohibido doblar o torcer fuertemente el arnés DK y el arnés de cableado del sistema de inyección conectado a él. Esto puede interrumpir el flujo de aire atmosférico hacia el DK.
Para eliminar el mal funcionamiento como resultado deм En caso de caída de agua, es necesario evitar dañar el sello en la periferia del bloque del arnés del sistema de control.
Manipule el nuevo sensor con cuidado. No permita que la grasa o la suciedad entren en contacto con el conector del arnés de cableado del sensor o con el extremo ranurado de la carcasa del sensor.
Sensor de oxígeno de diagnóstico (DOS)
Un convertidor catalítico se utiliza para reducir el contenido de hidrocarburos, monóxido de carbono y óxidos de nitrógeno en los gases de escape.
El neutralizador oxida los hidrocarburos y el monóxido de carbono, convirtiéndolos en vapor de agua y dióxido de carbono.
El neutralizador también restaura el nitrógeno de los óxidos de nitrógeno.
El controlador monitorea las propiedades de oxidación-reducción del neutralizador analizando la señal del sensor de oxígeno de diagnóstico instalado después del neutralizador.
DDC funciona según el mismo principio que UDC. El UDC genera una señal que indica la presencia de oxígeno en los gases de escape en la entrada del neutralizador.
La señal generada por el DDC indica la presencia de oxígeno en los gases de escape después del neutralizador.
Si el neutralizador funciona correctamente, las lecturas del DDC diferirán significativamente de las lecturas del UDC.
La señal de salida de un sensor de oxígeno de diagnóstico calentado cuando funciona en modo de retroalimentación, con un neutralizador útil en modo de estado estable, debe estar en el rango de 590 a 750 mV y no debe repetir la señal UDC.
Si ocurre un mal funcionamiento en los circuitos o en el propio sensor de oxígeno de diagnóstico, el controlador almacena su código en su memoria y enciende el indicador, señalando la presencia de un mal funcionamiento.
Los requisitos para el mantenimiento del DDC no son diferentes a los descritos anteriormente para el UDC.
Sensor de posición del cigüeñal (CPS)
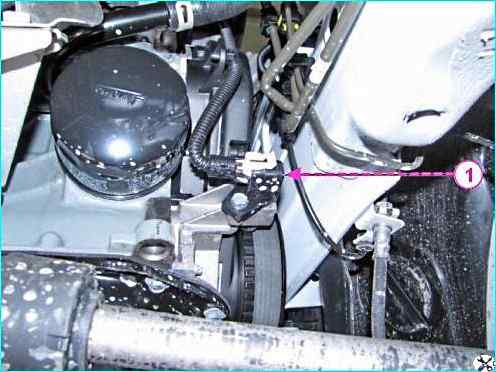
El sensor de posición del cigüeñal está instalado en la tapa de la bomba de aceite a una distancia de 0,9 ± 0,5 mm de la parte superior del diente del disco de sincronización, fijado en el cigüeñal del motor.
El disco de sincronización está combinado con la polea de accionamiento del generador y es una rueda dentada con 58 dientes, dispuestos en incrementos de 6°, y una ranura "larga" para la sincronización formada por dos dientes faltantes.
Cuando la mitad del primer diente del sector dentado del disco después de la depresión "larga" está alineada con el eje del sensor de posición del cigüeñal, el cigüeñal del motor está en la posición de 114° (19 dientes) antes del punto muerto superior. centro del 1er y 4to cilindro.
Cuando el disco maestro gira, el flujo magnético en el circuito magnético del sensor cambia, induciendo pulsos de voltaje de CA en su devanado.
El controlador determina la posición y la frecuencia de rotación del cigüeñal basándose en el número y la frecuencia de estos pulsos y calcula la fase y la duración de los pulsos de control de los inyectores y la bobina de encendido.
Los cables DPKV están protegidos contra interferencias mediante una pantalla en cortocircuito a tierra.
Si ocurre una falla en el circuito del sensor de posición del cigüeñal, el motor deja de funcionar, el controlador almacena un código de falla en su memoria y enciende el indicador.
Sensor de fase (PS)
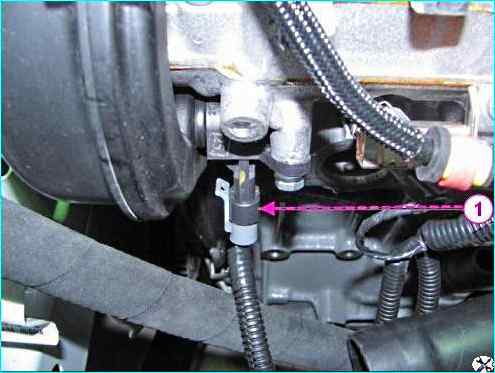
El sensor de fase del motor 21129 está instalado en la culata, cerca de la polea del árbol de levas de admisión.
El principio de funcionamiento del sensor se basa en el efecto Hall.
Hay un disco de sincronización con una ranura en la polea del árbol de levas de admisión. Cuando la ranura pasa a través de la ranura del sensor de fase, el sensor envía un pulso de voltaje del nivel del suelo (aproximadamente 0 V) al controlador, que corresponde a la posición del pistón del 1er cilindro en la carrera de compresión. p>
La señal del sensor de fase es utilizada por el controlador para organizar la inyección secuencial de combustible de acuerdo con el orden de funcionamiento de los cilindros del motor.
Cuando ocurre un fallo en los circuitos o en el propio sensor de fase, el controlador almacena su código en su memoria y enciende la alarma.
Sensor de velocidad del vehículo (VSS)
En los vehículos de la familia LADA VESTA, la información sobre la velocidad del vehículo se envía al controlador ECM desde la unidad de control ABS a través del bus CAN.
Interruptor de luz de freno
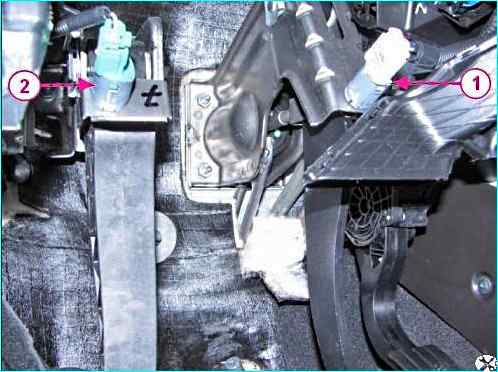
El interruptor de señal de freno es parte del conjunto del pedal de freno y está diseñado para enviar al controlador ECM las señales apropiadas sobre el momento en que el conductor presiona o suelta el pedal del freno.
En los sistemas de aceleración por cable (E-throttle), las señales del interruptor del pedal de freno juegan un papel importante porque son utilizadas por la función de seguridad del software ECM.
Por este motivo, es muy importante asegurarse de que el interruptor de la luz de freno esté siempre en condiciones de funcionamiento.
En caso de mal funcionamiento de los circuitos eléctricos del interruptor, el motor del vehículo puede pasar al modo de funcionamiento de emergencia con potencia reducida forzosamente.
El interruptor de luz de freno tiene dos grupos de contactos, el primero de los cuales conmuta el voltaje de Cl. 15, y el segundo es el voltaje con Cl. 30, suministrado para alimentar la lámpara de luz de freno.
Ambas señales se envían al ECM. Cuando se suelta el pedal del freno, los contactos del primer grupo deben estar normalmente cerrados y los contactos del segundo deben estar normalmente abiertos.
Interruptor de señal de posición del pedal del embrague (CPPS)
El interruptor de señal de posición del pedal del embrague está instalado en los automóviles de la familia LADA VESTA con transmisión manual.
El interruptor es parte del conjunto del pedal del embrague y está diseñado para enviar una señal a las unidades de control sobre la presión del pedal del embrague.
El interruptor tiene un grupo de contactos que conmuta el voltaje de Cl. 15.
Cuando se presiona el pedal del embrague, los contactos están abiertos.
La señal del interruptor de posición del pedal del embrague es utilizada por el software ECM para mejorar las características de conducción del vehículo.
En los vehículos de la familia LADA VESTA, la información sobre el estado del VSPPS se envía al controlador ECM desde el controlador VSM a través del bus CAN.