Механизм газораспределения предназначен для обеспечения впуска в цилиндры свежего воздушного заряда и выпуска из них отработавших газов
Впускные и выпускные клапаны открываются и закрываются в определенных положениях поршня, что обеспечивается совмещением меток на шестернях привода агрегатов при их монтаже.
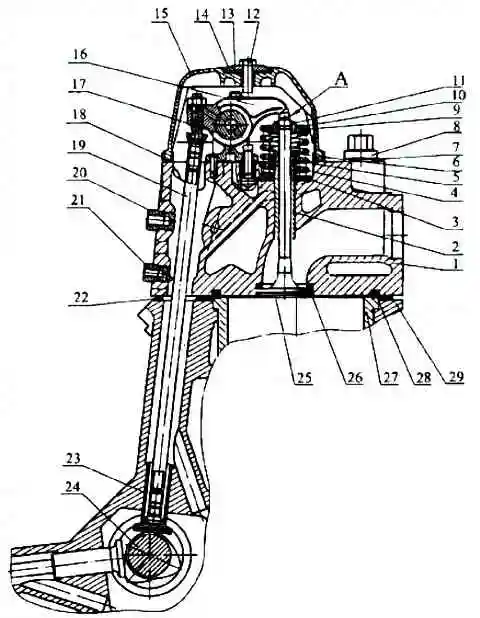
Механизм газораспределения - верхнеклапанный с нижним расположением распределительного вала.
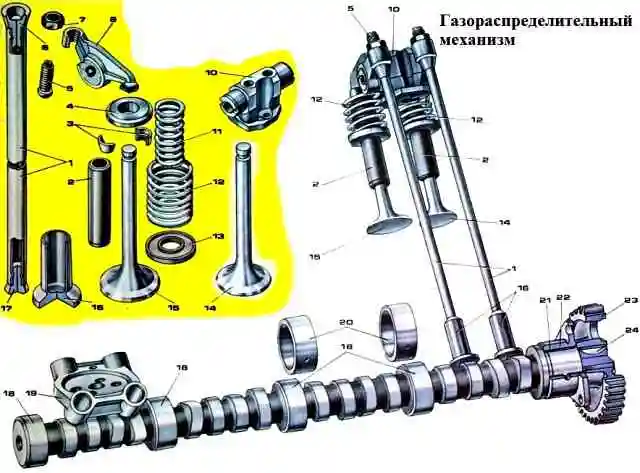
Кулачки распределительного вала 24 в соответствии с фазами газораспределения приводят в действие толкатели 23.
Штанги 19 сообщают качательное движение коромыслам 16, а они, преодолевая сопротивление пружин 7 и 8, открывают клапаны 25.
Закрываются клапаны под действием силы сжатия пружин.
Распределительный вал стальной, кулачки и опорные шейки подвергнуты термообработке ТВЧ;
- устанавливается в развале блока цилиндров на пяти подшипниках скольжения, представляющих собой стальные втулки, залитые антифрикционным сплавом.
Диаметр втулок на 6 мм больше по сравнению со втулками двигателя мод. 740.10.
Распределительный вал увеличенной размерности, измененными фазами газораспределения и ходом клапанов по сравнению с распредвалом двигателя мод. 740.10.
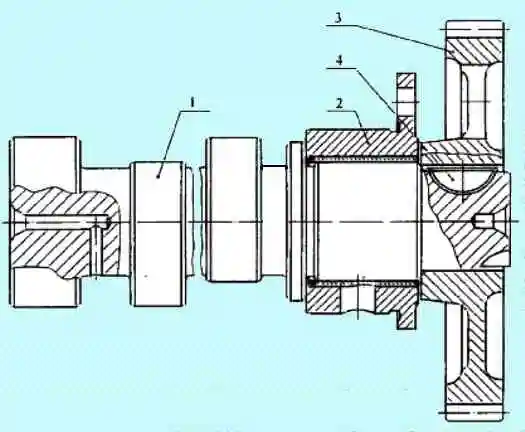
На задний конец распределительного вала напрессована прямозубая шестерня 3.
Привод распределительного вала осуществляется от шестерни коленчатого вала через промежуточные шестерни.
Шестерни стальные, штампованные с термообработанными зубьями.
Для обеспечения заданных фаз газораспределения шестерни при сборке устанавливаются по меткам, выбитым на торцах (см. статью "Техническая характеристика двигателя КАМАЗ 740.11-240").
От осевого перемещения вал фиксируется корпусом 2 подшипника задней опоры, который крепится к блоку цилиндров тремя болтами.
Посадочный диаметр корпуса подшипника задней опоры больше по сравнению с корпусом подшипника двигателя мод. 740.10.
Установка корпуса подшипника задней опоры распределительного вала двигателя мод. 740.10 не допустима, так как приведет к аварийному снижению давления масла в системе и преждевременному выходу из строя двигателя.
Клапаны из жаропрочной стали.
Угол рабочей фаски клапанов 90°. Диаметр тарелки впускного клапана 51,6 мм, выпускного - 46,6 мм, высота подъема впускного клапана - 14,2 мм, выпускного - 13,7 мм.
Геометрия тарелок впускных и выпускных клапанов обеспечивают соответствующие газодинамические параметры впуска-выпуска газов и поэтому их замена на клапаны двигателя мод. 740.10 не рекомендуется.
Клапаны перемещаются в направляющих втулках изготовленных из металлокерамики.
Для предотвращения попадания масла в цилиндр и снижения его расхода на угар, на направляющих клапанов устанавливаются резиновые уплотнительные манжеты.
Толкатели тарельчатого типа с профилированной направляющей частью, изготовлены из стали с последующей наплавкой поверхности тарелки отбеленным чугуном.
Толкатель подвергнут химико-термической обработке.
Коромысла клапанов стальные, штампованные, представляют собой двуплечий рычаг, у которого отношение большого плеча к меньшему составляет 1.55.
Коромысла впускного и выпускного клапанов устанавливаются на общей стойке и фиксируются в осевом направлении пружинным фиксатором.
Коромысла клапанов двигателя 740.11-240. в отличие от коромысел двигателя мод. 740.10, не имеют бронзовой втулки.
Направляющие толкателей отлиты заодно с блоком цилиндров.
Штанги толкателей стальные, пустотелые с запрессованными наконечниками. Штанги на 3 мм короче штанг двигателя мод. 740.10 и не взаимозаменяемы с ними.
Стойка коромысел чугунная, её цапфы подвергнуты термической обработке ТВЧ.
Диаметр цапф на 2 мм больше по сравнению с цапфами стойки коромысел двигателя мод. 740.10.
Пружины клапанов винтовые, устанавливаются по две на каждый клапан.
Пружины имеют различные направления навивки. Диаметр проволоки наружной пружины 4,8 мм, внутренний - 3,5 мм.
Предварительно устанавливаемое усилие пружин 355 Н, суммарное рабочее - 821 Н.
Пружины взаимозаменяемы с пружинами двигателя мод. 740.10.
Головки цилиндров 1 (рис. 1) отдельные на каждый цилиндр, изготовлены из алюминиевого сплава.
Головка цилиндра имеет полость охлаждения, сообщающуюся с полостью охлаждения блока.
Для усиления днища головки увеличена ее толщина в зоне выпускного канала и выполнено дополнительное ребро по сравнению с головкой цилиндра двигателя мод. 740.10.
Каждая головка цилиндров устанавливается на два установочных штифта, запрессованные в блок цилиндров, и крепится четырьмя болтами из легированной стали.
Один из установочных штифтов одновременно служит втулкой для подачи масла на смазку коромысел клапанов.
Втулка уплотнена резиновыми кольцами.
В головке, по сравнению с головкой двигателя 740.10, увеличено отверстие слива моторного масла из-под клапанной крышки в штанговую полость.
Окна впускного и выпускного каналов расположены на противоположных сторонах головки цилиндров.
Впускной канал имеет тангенциальный профиль для обеспечения оптимального вращательного движения воздушного заряда, определяющего параметры рабочего процесса и экологические показатели двигателя, поэтому замена на головки цилиндров двигателя мод. 740.10 не допускается.
В головку запрессованы чугунные седла и металлокерамические направляющие втулки клапанов.
Седла клапанов имеют увеличенный натяг в посадке по сравнению с седлами двигателя мод. 740.10, и фиксируются острой кромкой.
Выпускное седло и клапан профилированы для обеспечения меньшего сопротивления выпуску отработавших газов.
Применение выпускного клапана мод. 740.10 не рекомендуется.
Стык "головка цилиндра - гильза" (газовый стык) - беспрокладочный (рис. Газовый стык).
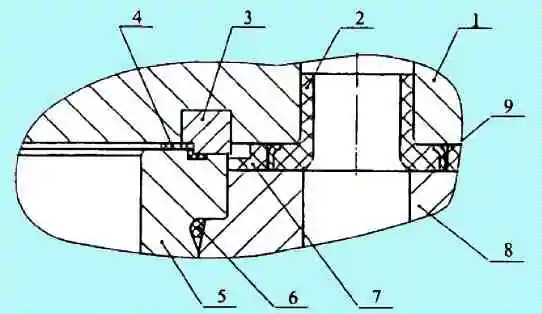
В расточенную канавку на нижней плоскости головки запрессовано стальное уплотнительное кольцо 3. Посредством этого кольца головка цилиндра устанавливается на бурт гильзы.
Герметичность уплотнения обеспечивается высокой точностью обработки сопрягаемых поверхностей уплотнительного кольца и гильзы цилиндра 5.
Уплотнительное кольцо дополнительно имеет свинцовистое покрытие для компенсации микронеровностей уплотняемых поверхностей.
Для уменьшения вредных объемов в газовом стыке установлена фторопластовая прокладка - заполнитель 4.
Прокладка - заполнитель фиксируется на выступающем пояске кольца газового стыка за счет обратного конуса с натягом.
Применение прокладки заполнителя снижает удельный расход топлива и дымность отработавших газов. Прокладка-заполнитель разового применения.
Для уплотнения перепускных каналов охлаждающей жидкости в отверстия днища головки установлены уплотнительные кольца 2 из силиконовой резины.
Пространство между головкой и блоком, отверстия стока моторного масла и отверстия прохода штанг уплотнены прокладкой 7 головки цилиндра из термостойкой резины.
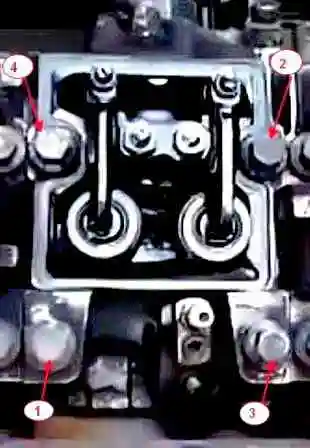
При сборке двигателя болты крепления головки цилиндра следует затягивать в три приема в порядке возрастания номеров, указанном на рис. 5
Величины моментов затяжки должны быть:
- 1 прием - до 39-49 Нм (4-5 кгс.м);
- 2 прием - до 98-127 Нм (10-13 кгс.м);
- 3 прием - до 186-206 Нм (19-21 кгс.м
Перед ввертыванием смазать резьбу болтов слоем графитовой смазки.
После затяжки болтов необходимо отрегулировать зазоры между клапанами и коромыслами (регулировка зазоров клапанов описана в статье - Как отрегулировать зазоры клапанов Камаз.
Клапанный механизм закрыт алюминиевой крышкой 15 (см. рис. 1).
Для шумоизоляции и уплотнения стыка крышка - головка цилиндра применены виброизоляционная шайба 14 и резиновая уплотнительная прокладка 19.
Болты крепления крышек головок цилиндров затянуть с крутящим моментом 12,7-17,6 Нм (1,3-1,8 кгс.м).
Основные неисправности механизма газораспределения
Отклонения в работе механизма газораспределения при естественном износе деталей вызывают ухудшение динамики механизма, способствуют ускоренному износу сопряжений. Из общего числа отказов всех систем двигателя 25-27 % приходится на ГРМ.
Основными неисправностями двигателя, обуславливаемые неисправностями ГРМ, могут быть следующие:
- - уменьшение мощности двигателя, увеличение расхода топлива и масла;
- - повышение дымности отработавших газов;
- - уменьшение давления масла в системе двигателя при температуре выше 0° С;
- - неустойчивая работа двигателя на холостом ходу;
- - работа двигателя с перебоями или перегревом;
- - подтекания жидкости в соединениях системы охлаждения.
Признаками неисправностей ГРМ являются стуки в головке цилиндра. Звонкий стук в головке цилиндра вызывается стуком клапанов о коромысла из-за большого теплового зазора между клапаном и носком коромысла.
Глухой металлический стук на холостом ходу и усиление его при подаче топлива являются признаком поломки клапанных пружин или заедании клапанов.
Неплотная посадка клапана на седло возникает при отсутствии или уменьшении теплового зазора между носком коромысла и клапаном, а так же при нарушении несущей способности неподвижного соединения головка цилиндров – седло клапана.
При неплотной посадке клапана на седло на отдельных участках между клапаном и седлом образуются зазоры.
Раскалённые газы под давлением и с большой скоростью проходят в образовавшиеся щели, поэтому поверхности фаски в этом месте интенсивно коррозируют, ухудшается прилегание фаски к седлу.
На поверхности фаски накапливаются продукты сгорания, вследствие чего нарушается герметичность соединения.
Анализ характерных повреждений клапанов и их сёдел показывает, что примерно 90% всех повреждений возникает при нарушении герметичности соединения седло – клапан.
При увеличении теплового зазора уменьшается высота подъёма клапанов, вследствие чего ухудшается наполнение и очистка цилиндров, растут ударные нагрузки и износ деталей ГРМ.
При очень маленьких тепловых зазорах, в результате сгорания или износа рабочих фасок клапана или седла клапана, не обеспечивается герметичность камеры сгорания, двигатель теряет компрессию, перегревается и не развивает полной мощности.
Наиболее часто встречающиеся неисправности ГРМ следующие:
- – преждевременный износ посадочных поверхностей седла и клапана; износ направляющей втулки клапана;
- – нарушение стабильности посадки в сопряжении седло клапана - головка цилиндров;
- – деформация головки цилиндров;
- – деформация седла и стержня клапана;
- – деформация тарелки клапана; обрыв стержня клапана и коррозия; износ отверстий под толкатели;
- – износ втулок распределительного вала; износ кулачков распределительного вала; износ коромысел клапанов.
Перед выполнением технических обслуживаний необходим индивидуальный контроль состояния ГРМ, позволяющий при помощи специального оборудования, без разборки двигателя заблаговременно выявить указанные выше скрытые неисправности и определить перечень профилактических и ремонтных воздействий.
Оценивать техническое состояние ГРМ следует по диагностическим параметрам, а определить необходимость выполнения операций обслуживания и ремонта – по предельным значениям этих параметров.
Характерный дефект штанг: ослабление посадки наконечников и погнутость стержня штанги.
Характерными дефектами клапанов являются износ рабочих фасок, погнутость стержня, облом тарелки клапана, износ торца клапана
Характерными дефектами толкателей являются износ тарелки, раковины на рабочей поверхности, износ стержня
Изношенные тарелки и стержни толкателей восстанавливаются хромированием.
После восстановления клапаны притираются в седлах головок цилиндров.