The gas distribution mechanism is designed to ensure the intake of fresh air charge into the cylinders and the release of exhaust gases from them
Intake and exhaust valves open and close in certain piston positions, which is ensured by the alignment of marks on the drive gears of the units during their installation.
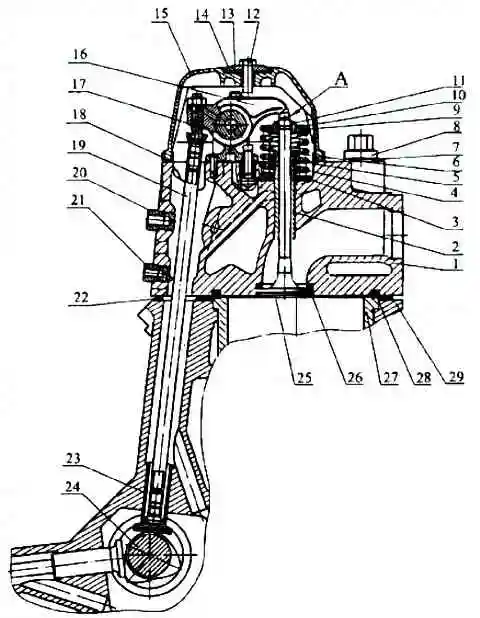
The gas distribution mechanism is overhead valve with a lower camshaft.
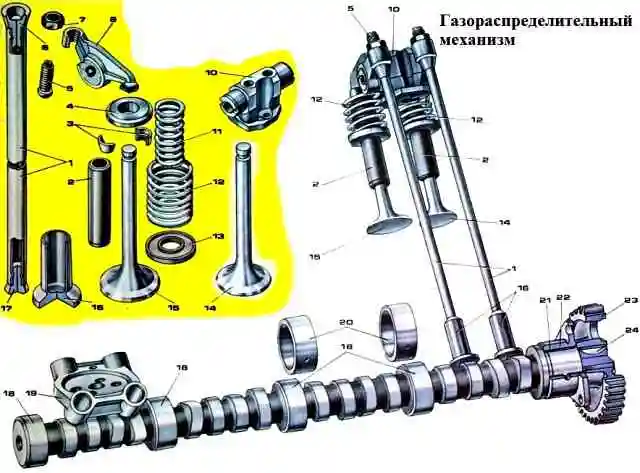
The camshaft cams 24, in accordance with the valve timing, activate the pushers 23.
Rods 19 impart a rocking motion to rocker arms 16, and they, overcoming the resistance of springs 7 and 8, open valves 25.
The valves close under the action of the compression force of the springs.
The camshaft is made of steel, the cams and bearing journals are subjected to high-frequency heat treatment;
- installed in the camber of the cylinder block on five plain bearings, which are steel bushings filled with anti-friction alloy.
The diameter of the bushings is 6 mm larger compared to the motor bushings mod. 740.10.
Camshaft of increased dimension, modified valve timing and valve stroke compared to the camshaft of the engine mod. 740.10.
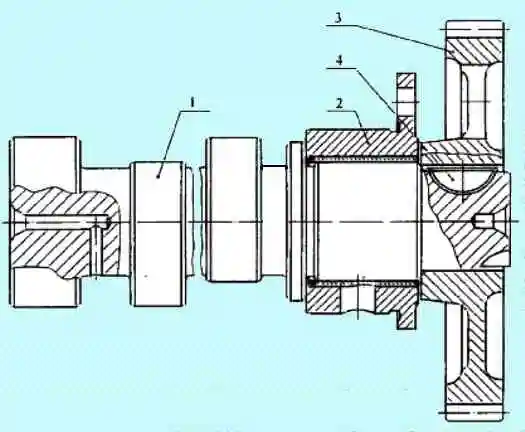
A spur gear 3 is pressed onto the rear end of the camshaft.
The camshaft is driven from the crankshaft gear through intermediate gears.
Steel gears, stamped with heat-treated teeth.
To ensure the specified valve timing, the gears are installed during assembly according to the marks stamped on the ends (see the article “Technical characteristics of the KAMAZ 740.11-240 engine”).
The shaft is secured against axial movement by housing 2 of the rear support bearing, which is attached to the cylinder block with three bolts.
The seat diameter of the rear support bearing housing is larger compared to the bearing housing of the engine mod. 740.10.
Installing the bearing housing of the rear camshaft support of the engine mod. 740.10 is not permissible, as it will lead to an emergency decrease in oil pressure in the system and premature engine failure.
Valves made of heat-resistant steel.
The valve working chamfer angle is 90°. The diameter of the intake valve plate is 51.6 mm, the exhaust valve is 46.6 mm, the lift height of the intake valve is 14.2 mm, the exhaust valve is 13.7 mm.
The geometry of the intake and exhaust valve plates provides the appropriate gas-dynamic parameters for the intake and exhaust of gases and therefore their replacement with engine valves mod. 740.10 is not recommended.
The valves move in guide bushings made of cermet.
To prevent oil from entering the cylinder and reducing its consumption through waste, rubber sealing cuffs are installed on the valve guides.
Talk Disc-type casters with a profiled guide part, made of steel with subsequent surfacing of the surface of the disc with bleached cast iron.
The pusher is subjected to chemical-thermal treatment.
Valve rocker arms are steel, stamped, and are a double-arm lever with a ratio of the largest arm to the smallest arm of 1.55.
The rocker arms of the intake and exhaust valves are mounted on a common stand and fixed in the axial direction with a spring retainer.
Engine valve rocker arms 740.11-240. in contrast to the rocker arms of the engine mod. 740.10, do not have a bronze bushing.
The pushrod guides are cast integrally with the cylinder block.
Push rods are steel, hollow, with pressed tips. The rods are 3 mm shorter than the motor rods mod. 740.10 and are not interchangeable with them.
The rocker arm stand is cast iron, its trunnions are subjected to high-frequency heat treatment.
The diameter of the trunnions is 2 mm larger compared to the trunnions of the rocker arm strut of the engine mod. 740.10.
Valve springs are screw-type, two are installed on each valve.
Springs have different winding directions. The wire diameter of the outer spring is 4.8 mm, the inner one is 3.5 mm.
Preset spring force 355 N, total working force - 821 N.
The springs are interchangeable with engine springs mod. 740.10.
Cylinder heads 1 (Fig. 1) are separate for each cylinder, made of aluminum alloy.
The cylinder head has a cooling cavity that communicates with the cooling cavity of the block.
To strengthen the bottom of the head, its thickness in the area of the exhaust channel has been increased and an additional rib has been made in comparison with the cylinder head of the engine mod. 740.10.
Each cylinder head is mounted on two locating pins pressed into the cylinder block and secured with four alloy steel bolts.
One of the locating pins also serves as a bushing for supplying oil to lubricate the valve rocker arms.
The bushing is sealed with rubber rings.
In the head, compared to the engine head 740.10, the hole for draining engine oil from under the valve cover into the rod cavity is enlarged.
The intake and exhaust ports are located on opposite sides of the cylinder head.
The inlet channel has a tangential profile to ensure optimal rotational movement of the air charge, which determines the operating process parameters and environmental performance of the engine, therefore replacing the engine cylinder heads mod. 740.10 is not allowed.
Cast iron seats and cermet valve guides are pressed into the head.
Valve seats have an increased fit in comparison with engine seats mod. 740.10, and are fixed with a sharp edge.
The exhaust seat and valve are profiled to provide less resistance to exhaust gases.
Application of exhaust valve mod. 740.10 is not recommended.
The joint “cylinder head - liner” (gas joint) is gasketless (Fig. Gas joint).
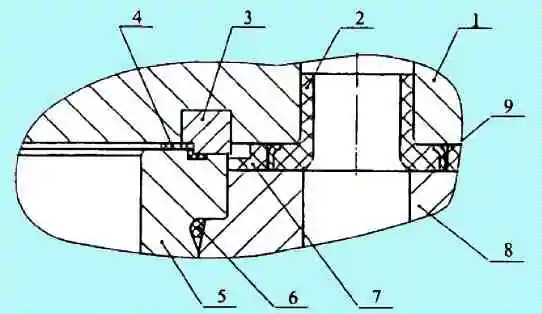
A steel sealing ring 3 is pressed into a bored groove on the bottom plane of the head. Using this ring, the cylinder head is installed on the liner collar.
The tightness of the seal is ensured by high precision processing of the mating surfaces of the sealing ring and cylinder liner 5.
The sealing ring additionally has a lead coating to compensate for micro-roughness of the sealing surfaces.
To reduce harmful volumes in the gas joint, a fluoroplastic gasket is installed - filler 4.
The gasket - filler is fixed on the protruding flange of the gas joint ring due to the reverse cone with interference.
The use of a filler gasket reduces specific fuel consumption and exhaust smoke. Single use filler pad.
To seal the coolant bypass channels, O-rings 2 made of silicone rubber are installed in the holes in the bottom of the head.
The space between the head and the block, the engine oil drain holes and the rod passage holes are sealed with cylinder head gasket 7 made of heat-resistant rubber.
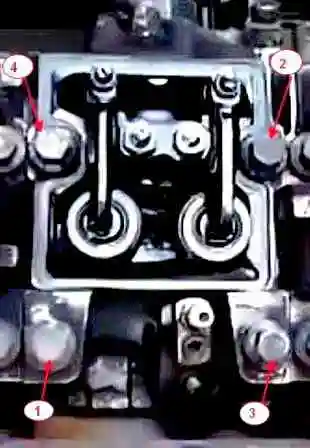
When assembling the engine used The cylinder head mounting bolts should be tightened in three steps in the ascending order of numbers shown in Fig. 5
The tightening torque values should be:
- 1st dose - up to 39-49 Nm (4-5 kgf.m);
- 2nd reception - up to 98-127 Nm (10-13 kgf.m);
- 3rd reception - up to 186-206 Nm (19-21 kgf.m
Before screwing in, lubricate the bolt threads with a layer of graphite grease.
After tightening the bolts, it is necessary to adjust the clearances between the valves and rocker arms (adjusting valve clearances is described in the article - How to adjust Kamaz valve clearances.
The valve mechanism is closed with an aluminum cover 15 (see Fig. 1).
For noise insulation and sealing of the joint between the cover and the cylinder head, a vibration-isolating washer 14 and a rubber sealing gasket 19 are used.
Tighten the cylinder head cover bolts with a torque of 12.7-17.6 Nm (1.3-1.8 kgf.m).
Main malfunctions of the gas distribution mechanism
Deviations in the operation of the gas distribution mechanism due to natural wear of parts cause a deterioration in the dynamics of the mechanism and contribute to accelerated wear of the interfaces. Of the total number of failures of all engine systems, 25-27% occur in the timing belt.
The main engine malfunctions caused by timing belt malfunctions may be the following:
- - decrease in engine power, increase in fuel and oil consumption;
- - increased smokiness of exhaust gases;
- - reduction of oil pressure in the engine system at temperatures above 0° C;
- - unstable engine operation at idle;
- - engine operation with interruptions or overheating;
- - fluid leaks in the cooling system connections.
Signs of timing belt malfunctions are knocking noises in the cylinder head. A loud knocking sound in the cylinder head is caused by the knocking of the valves on the rocker arms due to the large thermal gap between the valve and the toe of the rocker arm.
A dull metallic knock at idle and an increase in noise when fuel is supplied are a sign of broken valve springs or stuck valves.
Loose fit of the valve on the seat occurs when there is no or a decrease in the thermal gap between the toe of the rocker arm and the valve, as well as when the load-bearing capacity of the fixed connection between the cylinder head and the valve seat is impaired.
If the valve is not seated tightly on the seat, gaps form in certain areas between the valve and the seat.
Hot gases under pressure and at high speed pass into the formed cracks, so the chamfer surfaces in this place intensively corrode, and the fit of the chamfer to the seat deteriorates.
Combustion products accumulate on the surface of the chamfer, as a result of which the tightness of the connection is compromised.
Analysis of typical damage to valves and their seats shows that approximately 90% of all damage occurs when the seal of the seat-valve connection is broken.
As the thermal gap increases, the valve lift height decreases, as a result of which the filling and cleaning of the cylinders worsens, shock loads and wear of timing parts increase.
With very small thermal clearances, as a result of combustion or wear of the working chamfers of the valve or valve seat, the combustion chamber is not sealed, the engine loses compression, overheats and does not develop full power.
The most common timing faults are as follows:
- – premature wear of the seat and valve seating surfaces; wear of the valve guide;
- – violation of the stability of the fit in the valve seat-cylinder head interface;
- – cylinder head deformation;
- – deformation of the valve seat and stem;
- – deformation of the valve plate; valve stem breakage and corrosion; wear of holes for pushers;
- – wear of camshaft bushings; wear of camshaft cams; wear of valve rocker arms.
Before performing maintenance, it is necessary to individually monitor the condition of the timing belt, which allows, using special equipment, without disassembling the engine, to identify the above hidden faults in advance and determine a list of preventive and repair actions.
The technical condition of the timing belt should be assessed using diagnostic parameters, and the need to perform maintenance and repair operations should be determined based on the limit values of these parameters.
Characteristic defect of rods: loose fitting of tips and bent rod rod.
Characteristic defects of valves are wear of the working chamfers, bent rod, broken valve plate, wear of the valve end
Characteristic defects of pushers are wear of the plate, shell on the working surface, wear of the rod
Worn plates and pusher rods are restored by chrome plating.
After restoration, the valves are ground into the cylinder head seats.