Kompressor (Abb. 1) Kolbentyp, indirekter Durchfluss, zwei Zylinder, einstufige Kompression
Luft vom Motorluftfilter gelangt durch die Flügeleinlassventile in die Kompressorzylinder.
Die von den Kolben komprimierte Luft wird über Plattenauslassventile im Zylinderkopf in das Pneumatiksystem gedrückt.
Der Block und der Kopf werden durch Flüssigkeit gekühlt, die vom Motorkühlsystem geliefert wird.
Das Kompressorkühlsystem wird nur bei laufendem Motor gefüllt.
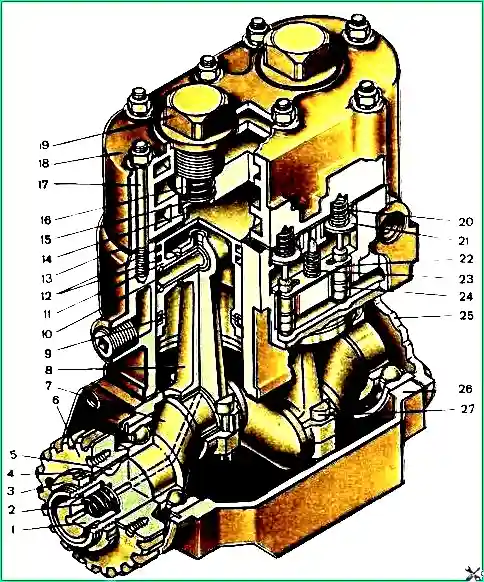
Ural-Autokompressor: 1 - Dichtung, 2 - Dichtungsfeder, 3 - Zahnradbefestigungsmutter, 4 - Sicherungsscheibe, 5 - Segmentschlüssel, 6 - Antriebsrad, 7 - Kurbelwelle, 8 - Pleuelstange, 9 - Ölabstreifer Ring, 10 – Kolbenbolzen, 11 – Kolben, 12 – Kompressionsringe, 13 – Kopfdichtung, 14 – Auslassventilsitz, 15 – Auslassventil, 16 – Auslassventilfeder, 17 – Zylinderkopfbolzen, 18 – Zylinderkopf, 19 - Auslassventilstopfen, 20 - Einlassventilfeder, 21 - Einlassventil, 22 - Kipphebel, 23 - Kipphebelfeder, 24 - Kolben mit Stange, 25 - Abdeckung, 26 - Kurbelgehäuse, 27 - Pleuelschraube
Öl wird den Reibflächen des Kompressors durch einen Schlauch von der Motorölleitung zur hinteren Abdeckung des Kompressorkurbelgehäuses und durch die Dichtung durch die Kurbelwellenkanäle zu den Pleuellagern zugeführt.
Anzeichen für eine Fehlfunktion des Kompressors sind Betriebsgeräusche, Klopfen und ein erhöhter Ölgehalt im aus den Luftzylindern abgelassenen Kondensat.
Erhöhter Ölgehalt im Kondensat ist meist eine Folge des Verschleißes der Kolbenringe und Lager der unteren Pleuelköpfe.
Der Kompressor ist im hinteren Teil des Motorsturzes installiert (Abb. 2) und mit vier Schrauben 15 an der Vorderwand der Steuerradabdeckung 14 befestigt, die aus demselben Gussteil wie das Schwungradgehäuse besteht.
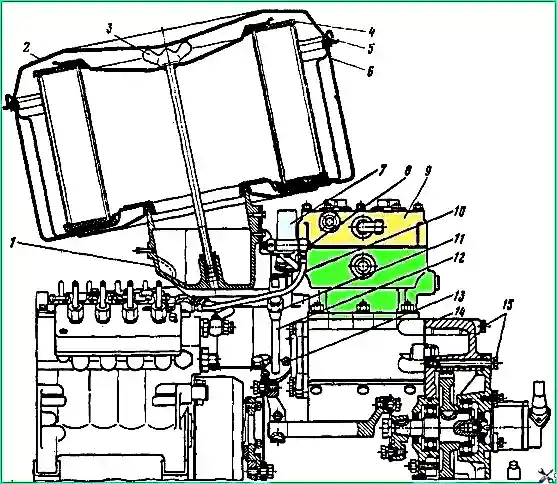
Montage des Kompressors am Motor: 7 - Verbindungsrohr; 2 - Luftfilterabdeckung; 3 - Stange zur Befestigung des Filterelements; 4 - Filterelement; 5 - Deckeldichtung; 6 - Filtergehäuse; 7 - Magnetventil; 8 - Kraftstoffleitungsschraube; 9 - Kompressor; 10 - Kraftstoffschlauch; 11 - Überwurfmutter; 12 - Wasserversorgungsrohr; 13 - Nüsse; 14 - Abdeckung; 15 - Schrauben
Kompressorwartung
Überlappungsventile, die die Sitze nicht dicht abdichten. Wenn sie abgenutzt oder beschädigt sind, ersetzen Sie sie.
Neue Ventile auf die Sitze läppen, bis beim Prüfen auf Farbe ein kontinuierlicher ringförmiger Kontakt entsteht.
Ziehen Sie die Muttern der Zylinderkopf-Befestigungsbolzen paarweise fest, beginnend mit dem diametral mittleren Paar.
Ziehen Sie die Muttern in zwei Schritten fest: Das endgültige Anzugsdrehmoment sollte 12–16 Nm (1,2–1,6 kgf/m) betragen.
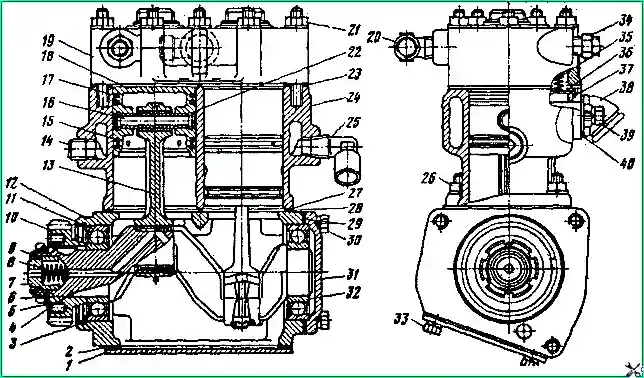
Kompressor: 1 – unterer Kurbelgehäusedeckel; 2, 23, 27, 29 – Dichtungen; 9, 9, 22 - Sicherungsringe; 4 - Kurbelwelle; 5 - Sicherungsscheibe; 6 - Nuss; 7 - Siegel; 8 - Frühling; 10 - Gang; 11, 82 - Lager; 12 - Kurbelgehäuse; 13 - Pleuel; 14 - Stecker; 15 - Ölabstreifring; 16 - Kolbenbolzen; 17 - Kompressionsring; 18 - Kolben; 19 - Kopfbaugruppe; 20, 25 - verschraubte Quadrate; 21, 26 - Nüsse; 24 - Zylinderblock; 28 - reflektierende Platte; 30, 33, 39 - Bolzen; 31 - Kurbelgehäusedeckel; 34 - passend; 35 - Einlassventilfeder; 36 - Einlassventil; 37 - Einlassventilführung; 38 - Rohr; 40 - Dichtung für Rohr mit Sieb
Anzeichen einer Kompressorstörung: Geräusche und Klopfen, erhöhte Erwärmung, erhöhter Ölgehalt im Kondensat, was meist eine Folge von Verschleiß an den Kolbenringen und der Dichtung am hinteren Ende der Kurbelwelle, Pleuellagern usw. ist Verteern der Ölablassleitung vom Kompressor.
Um den Kompressor vom Motor zu entfernen, lassen Sie 10 Liter Kühlmittel aus dem Kühlsystem durch den Hahn am Heizkessel ab.
Lösen Sie die Schlauchklemme und trennen Sie das Auswurfrohr vom Dämpfer.
Entfernen Sie den Luftfilterdeckel 2, das Filterelement 4 und das Luftfiltergehäuse 6.
Schrauben Sie die Schrauben und Überwurfmuttern der Brennstoffleitung ab, trennen Sie die Brennstoffleitungen vom Magnetventil 7 und den Zündkerzen der Elektrobrenner-Startvorrichtung.
Trennen Sie die Kabel vom Magnetventil und den Zündkerzen.
Schrauben herausdrehen und Verbindungsrohr 1 der Ansaugkrümmer samt Magnetventil abnehmen.
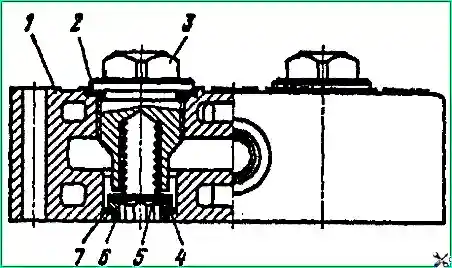
Verschließen Sie die Löcher in den Luftkanälen mit Papp- oder Sperrholzstopfen.
Schrauben Sie die beiden Muttern 13 ab, mit denen der Flansch des Kühlmittelzufuhrrohrs am Kompressor befestigt ist, dann die Überwurfmutter 11 und entfernen Sie das Rohr 12.
Entfernen Sie den Rohrflansch und den Gummi-O-Ring.
Schrauben Sie die Überwurfmuttern ab und trennen Sie die Rohrleitungen vom Kompressor, die den Kompressor mit dem Pneumatiksystem des Fahrzeugs und dem Kühler des Motorkühlsystems verbinden.
Lösen Sie die vier Schrauben 15, mit denen der Kompressor an der Steuerradabdeckung 14 befestigt ist.
Entfernen Sie die Kupplung von Rohr 38 (Abb. 3) und bewegen Sie den Kompressor nach vorne zur Kraftstoffpumpe, bis Zahnrad 10 aus der Abdeckung herauskommt. Entfernen Sie den Kompressor.
Verschließen Sie das Loch im Deckel mit einem Stopfen aus Sperrholz oder Pappe.
Kompressor zerlegen
Biegen Sie die Lasche der Sicherungsscheibe 5, schrauben Sie die Mutter 6 ab und entfernen Sie mit dem Abzieher „I 801.02.000“ das Zahnrad 10 von der Welle 4.
Schrauben Sie die Stopfen 3 (Abb. 4►) der Auslassventile ab, entfernen Sie die Federn 5 und die Ventile 4.
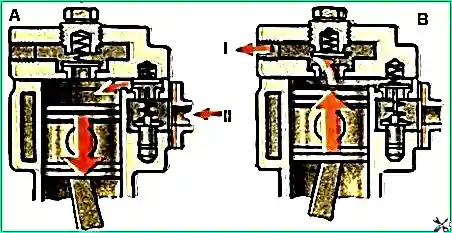
Verwenden Sie einen 10x10-Vierkantschlüssel, um die Sitze 6 abzuschrauben.
Ventilplatten und Ventilsitze sind ineinander geschliffen und sollten daher bei Reparaturen nicht entpersonalisiert werden.
Schrauben 39 herausdrehen (siehe Abb. 3), Rohr 38 entfernen.
Schrauben Sie die Muttern 21 ab, um die Dichtung 23 vor Beschädigung zu schützen, trennen Sie den Kopf 19 vom Block 24, entfernen Sie ihn und die Dichtung.
Entfernen Sie die Feder 35 und das Einlassventil 36.
Ggf. mit einem Abzieher (Abb. 5) die Führungen 37 der Einlassventile herausdrücken (siehe Abb. 3).
Schrauben 33 herausdrehen und vorsichtig, dabei Dichtung 2 vor Beschädigung schützen, Deckel 1 und Dichtung abnehmen.
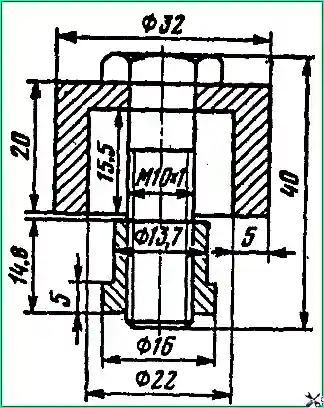
Markieren Sie die Pleuel und Pleueldeckel und ihre relativen Positionen.
Schrauben Sie die Muttern der Pleuelschrauben ab und lösen Sie sie, entfernen Sie die Pleuelkappen und entfernen Sie die mit den Pleueln montierten Kolben 18.
Montieren Sie die Pleuelkappen in der gleichen Position an den Pleueln und befestigen Sie sie mit Pleuelschrauben.
Befestigen Sie die Pleuelbaugruppe mit dem Kolben in einem Schraubstock und entfernen Sie die Ringe vom Kolben: zwei Kompressionsringe 17 und einen Ölabstreifring 15.
Entfernen Sie die Sicherungsringe 22 des Kolbenbolzens, entfernen Sie ihn und trennen Sie die Pleuelstange vom Kolben.
Schrauben Sie die Muttern 26 der Stehbolzen ab, mit denen der Zylinderblock 24 am Kurbelgehäuse 12 befestigt ist.
Entfernen Sie den Block 24, die reflektierende Platte 28 und die Dichtung 27 von den Stehbolzen.
Entfernen Sie den Sicherungsring 9, die Dichtung 7 und die Dichtungsfeder 8 vom hinteren Ende der Kurbelwelle.
Schrauben 30 herausdrehen und Deckel 31 und Dichtung 29 entfernen.
Entfernen Sie den Sicherungsring 3 vom hinteren Ende des Kurbelgehäuses 12, montieren Sie das Kurbelgehäuse mit seinem vorderen Ende auf einer Presse und pressen Sie durch ein Distanzstück aus „weichem“ Nichteisenmetall die mit den Lagern 11 und 32 zusammengebaute Welle 4 aus dem Kurbelgehäuse.
Drücken Sie die Welle aus den Lagern. Entfernen Sie bei Bedarf die Stehbolzen vom Kompressorkurbelgehäuse.
Bei der Reparatur der Pleuel- und Kolbengruppe müssen verschlissene Kolben, Kolbenringe und Laufbuchsen durch Reparatursätze ersetzt werden.
Der Zylinderblock und die Kurbelwelle werden repariert: Die Zylinder werden gebohrt und gehont, die Kurbelzapfen der Kurbelwelle werden auf Reparaturmaße geschliffen (Tabelle 1).
Tabelle 1.
Kompressor-Kurbelgehäuse. Durchmesser der Löcher für Kurbelwellenlager:
- - Nenngröße - 72+0,030 mm;
- - zulässige Größe - 72,05 mm
Zylinderblock. Zylinderdurchmesser:
- - Nenngröße - 60+0,030 mm;
- - zulässige Größe - 60,30 mm;
- - erste Reparatur – 60,4+0,030 mm;
- - zweite Reparatur - 60,8+0,030 mm
Kurbelwelle. Halsdurchmesser:
- - Hauptlager - Nenngröße - 35+0,020 mm; zulässige Größe - 35,00 mm;
- - Pleuel für Lager – Nenngröße – 28,5–0,021 mm; erste Reparatur - 28,2-0,021 mm; zweite Reparatur - 27,9-0,021;
- - für das Antriebsrad - Nenngröße - 35+0,020 mm; akzeptabel - 35,00
Pleuelstangenbaugruppe mit einem kleinen Auge. Durchmesser der Löcher für die Stiftbuchse:
- - Nenngröße - 14+0,019 mm;
- - zulässige Größe - 14,05 mm
Einfügungen. Wandstärke:
- - Nenngröße – 1,75–0,013 mm;
- - erste Reparatur – 1,90-0,013 mm;
- - zweite Reparatur – 2,05-0,013
Kolben. Außendurchmesser:
- - Köpfe – Nenngröße – 59,8–0,095 mm; erste Reparatur - 60,2-0,095 mm; zweite Reparatur - 60,6-0,095 mm;
- - Schürzen – Nenngröße – 59,9–0,030 mm; erste Reparatur - 60,3-0,030 mm; zweite Reparatur - 60,7-0,030 mm
Kompressionsring:
- Der Spalt in der Verbindung beim Einbau in ein Messgerät – Nenngröße – 0,200–0,400 mm; erste Reparatur - 0,200-0,400 mm; zweite Reparatur - 0,200-0,400 mm;
- Kaliberdurchmesser – Nenngröße – 60.000 mm; erste Reparatur - 60.400 mm; zweite Reparatur - 60.800
Ölabstreifring:
- Der Spalt in der Verbindung beim Einbau in ein Messgerät – Nenngröße – 0,200–0,400 mm; erste Reparatur - 0,200-0,400 mm; zweite Reparatur - 0,200-0,400 mm;
- Kaliberdurchmesser - Nenngröße - 60,00 mm; erste Reparatur - 60.400 mm; zweite Reparatur - 60.800 mm
Beim Zusammenbau neu eingebauter Kolbengruppenteile sollten Kolben, Pleuel und Bolzen entsprechend den Gruppen ausgewählt werden (Tabelle 2).
Tabelle 2.
Erste Gruppe:
- - Fingerdurchmesser – 12.500–12.497 mm;
- - Durchmesser des Lochs im Kolben - 12.500-1 2.497 mm;
- - Lochdurchmesser in der Pleuelbuchse – 12,507–12,504 mm;
- - Markierungsfarbe – Weiß
Zweite Gruppe:
- - Fingerdurchmesser – 12,497–12,494 mm;
- - Durchmesser des Lochs im Kolben – 12,497–12,494 mm;
- - Lochdurchmesser in der Pleuelbuchse – 12,504–12,501 mm;
- - Markierungsfarbe – Grün
Dritte Gruppe:
- - Fingerdurchmesser – 12,494–12,491 mm;
- - Durchmesser des Lochs im Kolben – 12,494–12,491 mm;
- - Lochdurchmesser in der Pleuelbuchse - 12,50 1-12,498 mm;
- - Markierungsfarbe – Blau
Vierte Gruppe:
- - Fingerdurchmesser – 12,491–12,488 mm;
- - Durchmesser des Lochs im Kolben – 12,491–12,488 mm;
- - Lochdurchmesser in der Pleuelbuchse – 12,498–12,495 mm;
- - Markierungsfarbe – Rot
Teile der ersten und zweiten Reparaturgröße sind gekennzeichnet:
Die Zahlen + 0,4 und + 0,8 sind auf der Unterseite der Kolben eingeprägt, die Zahlen 0,3 und - 0,6 auf der Rückseite (Stahl) der Laufbuchsen, ein oder zwei Streifen breit sind auf den Ringen auf der Mantellinie angebracht mit grüner Farbe 10 mm.
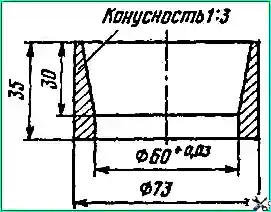
Überprüfen Sie vor dem Zusammenbau den Zylinderblock und den Kompressorkopf mit Druckluft unter einem Druck von 15 kgf/cm 2 und Eintauchen in Wasser auf Dichtheit, um sicherzustellen, dass keine Kerben und Verformungen der Trennebenen vorhanden sind .
Die Verformung der Steckerebenen (0,040 mm) wird mit einem Messlineal und einer Fühlerlehre kontrolliert.
Eine 0,05 mm dicke Sonde sollte nicht unter einem auf der Steckerebene installierten Lineal hindurchgehen.
Überprüfen Sie die Pleuelstange mit einem speziellen Gerät auf Biegung und Verdrehung. Die Nichtparallelität der Achsen der oberen zur unteren Achse (der Pleuelköpfe) darf 0,070 mm auf einer Länge von 100 mm betragen, ihre Verdrehung beträgt 0,100 mm auf einer Länge von 100 mm.
Kompressor zusammenbauen in umgekehrter Reihenfolge der Demontage. In diesem Fall ist es notwendig, eine Reihe der folgenden zwingenden Anforderungen zu erfüllen:
- - Schmieren Sie die Teile der Pleuel- und Kolbengruppe großzügig mit dem Öl, das zur Schmierung des Motors verwendet wird, gemäß der Schmiertabelle;
- - Montieren Sie die Kompressionsringe mit der Nut nach oben (in Richtung Kolbenboden) am Kolben.
- - Bevor Sie die Kolben in den Zylinder einbauen, trennen Sie die Ringverbindungen in einem Winkel von 120˚. Installieren Sie die Kolben mit einem Dorn im Zylinder (Abb. 6);
- - Das Anzugsdrehmoment der Pleuelschraubenmuttern sollte 1,5–4,7 kgf/m betragen. Es ist nicht erlaubt, die Mutter zu lösen, um den Splint zu installieren;
- - Ziehen Sie den Kompressorblockkopf in zwei Schritten fest, das endgültige Anzugsdrehmoment beträgt 1,2–1,7 kgcm;
- - Führen Sie beim Einbau der Dichtung die Enden der Feder in die Bohrungen an der Kurbelwelle und der Dichtung ein.
Bauen Sie den reparierten Kompressor in umgekehrter Reihenfolge wie beim Ausbau in das Fahrzeug ein.
Wir schauen uns auch den Artikel über den Kompressor an – „Reparatur des Kompressors eines Kamaz-Fahrzeugs“