Die Hochdruck-Kraftstoffpumpe (Abb. 1 und 2), zusammengebaut mit der Einspritzverstellungskupplung und der Kraftstoffansaugpumpe, befindet sich in der Wölbung des Zylinderblocks und ist mit vier Schrauben am Block befestigt.
Der Antrieb der Pumpe erfolgt über die Verteilergetriebe durch angetriebene und angetriebene Kupplungshälften.
Die Pumpendrehung auf der Antriebsseite erfolgt rechts (im Uhrzeigersinn).
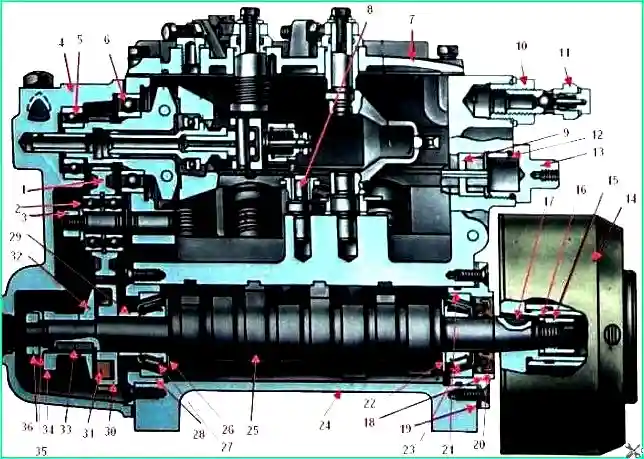
Längsschnitt der Hochdruck-Kraftstoffpumpe: 1 - Zwischenrad des Reglers; 2, 6 - Kugellager; 3, 36 - Nüsse; 4 - hintere Abdeckung des Reglers; 7 - obere Abdeckung des Reglers; 8 - Zahnstangenhebelachse; 9 - Zahnstangenbuchse; 10 - Pumpengehäuseschraube; 11 - Bypassventil; 12, 21 - Dichtungsringe; 13 - Rack-Stecker; 14 - Kraftstoffeinspritz-Vorlaufkupplung; 15 - Ringmutter; 16, 22, 26 - Unterlegscheiben; 11, 33 - Schlüssel; 18 - vordere Lagerabdeckung; 19 - Einstellscheiben; 20 - Manschette; 23, 27 - Kegelrollenlager; 24 - Körper; 25 - Nockenwelle; 28 - hintere Lagerabdeckung; 29 - Druckbuchse des Antriebsrads; 30 - Antriebsrad des Reglers; 31 - Cracker; 32 – Flansch; 34 - Exzenter der Kraftstoffpumpe; 35 - Sicherungsscheibe
Entfernen Sie während des Betriebs des Fahrzeugs regelmäßig die Hochdruck-Kraftstoffpumpe vom Motor, um sie am Ständer zu überprüfen und einzustellen.
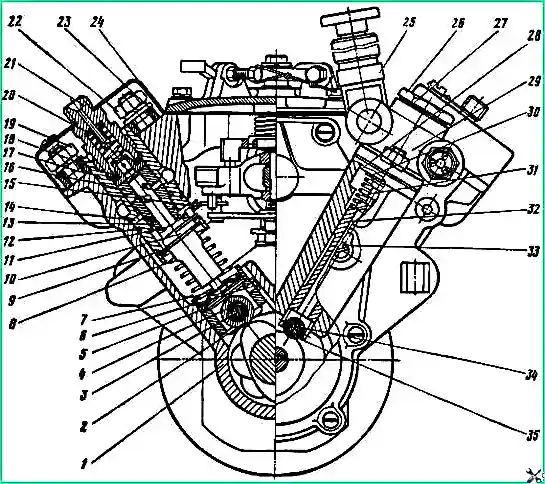
Querschnitt einer Hochdruck-Kraftstoffpumpe: 1 - Gehäuse; 2 - Druckrolle; 3 - Rollenachse; 4 - Rollenbuchse; 5 - Drückerferse; 6 - Cracker; 7 - Drückerfederplatte; 8 - Drückerfeder; 9 - Unterlegscheibe; 10 - Drehhülse; 11 - Kolben; 12,13 - Dichtungsringe; 14 - Befestigungsstift; 15 - rechte Schiene; 16 - Kolbenbuchse; 11 - Abschnittskörper; 18 - Dichtungen des Auslassgehäuses; 19,22 Nüsse; 20 - Federanschlag des Druckventils; 21 - passend; 23 - Abschnitt Gehäuseflansch; 24 - Schutzhülle; 25 - manuelle Kraftstoffansaugpumpe; 26 - Federstecker; 27 - Dichtung; 28 - Niederdruckpumpengehäuse; 29 - Niederdruck-Kraftstoffansaugpumpe; 30 - Stangenbuchse; 31 - Drückerfeder; 32 - Drücker; 33 - Feststellschraube; 34 - Rollenachse; 36 - Druckrolle
Um die Hochdruck-Kraftstoffpumpe vom Motor zu entfernen, entfernen Sie die Luftfilterabdeckung, schrauben Sie die Stange ab und entfernen Sie das Filterelement.
Lösen Sie die Klemmen an den Rohren des Luftfiltergehäuses und entfernen Sie es.
Schrauben Sie die Schrauben der Kraftstoffleitung ab und trennen Sie die Kraftstoffschläuche vom Magnetventil.
Trennen Sie das Kabel zum Magnetventil vom Steckverbinder.
Lösen Sie die vier Schrauben und entfernen Sie das Verbindungsrohr der Ansaugkrümmer und seine Dichtungen.
Verschließen Sie die Löcher in den Ansaugkrümmern mit Stopfen aus Sperrholz oder Pappe.
Schrauben Sie die Überwurfmuttern ab, die die Hochdruckleitungen mit der Hochdruck-Kraftstoffpumpe und den Einspritzdüsen verbinden. Lösen Sie die Schrauben, entfernen Sie die Halterungen und Hochdruckrohre.
Schrauben Sie die Schrauben der Kraftstoffleitung ab und trennen Sie die Brennstäbe und die Ölversorgungsleitung von der Hochdruck-Kraftstoffpumpe und der Druckerhöhungspumpe.
Lösen Sie die Schrauben, mit denen das Ölablassrohr befestigt ist.
Schrauben Sie die Schrauben ab und entfernen Sie die Hochdruck-Kraftstoffpumpenbaugruppe mit der Einspritzverstellungskupplung und der Druckerhöhungspumpe.
Verschließen Sie die abgetrennten Enden von Kraftstoffschläuchen und -rohren sowie Anschlüsse, Gewindelöcher an der Pumpe und den Einspritzdüsen mit Stopfen oder Isolierband.
Überprüfen und einstellen Sie die Hochdruck-Kraftstoffpumpe auf dem Ständer zusammen mit einem funktionsfähigen Satz Einspritzdüsen, die zuerst überprüft und eingestellt werden müssen.
Nachdem Sie die Pumpe auf dem Ständer installiert haben, füllen Sie den Pumpenraum bis zur Höhe der Ablassöffnung an der hinteren Abdeckung des Reglers mit Motoröl (0,16 ÷ 0,20 l).
Füllen Sie Öl durch das mit einem Stopfen verschlossene Loch im Deckel in die Pumpe.
Während des Tests installieren Sie das Ölablassrohr so an der Pumpe, dass sein zweites Ende nach oben zeigt, und entfernen Sie das Gehäuse 24 (siehe Abb. 2) von beiden Abschnittsreihen.
Überprüfen Sie bei der Überprüfung der Hochdruck-Kraftstoffpumpe Folgendes:
- - Beginn der Kraftstoffzufuhr durch Pumpenabschnitte;
- - die Menge und Gleichmäßigkeit der Kraftstoffzufuhr durch die Pumpenabschnitte;
- - Rotationsfrequenz der Pumpennockenwelle, entsprechend dem Beginn der Abschaltung und der vollständigen Abschaltung durch den Regler der Geschwindigkeit der Kraftstoffzufuhr durch die Pumpenabschnitte durch die Einspritzdüsen.
Überprüfung und Einstellung des Beginns der Kraftstoffzufuhr durch Pumpenabschnitte
Überprüfen und stellen Sie den Beginn der Kraftstoffzufuhr abschnittsweise am Ständer in der folgenden Reihenfolge ein
Kraftstoff Installieren Sie die Hochdruckpumpe auf dem Ständer und verbinden Sie sie über die angetriebene Halbkupplung der automatischen Kraftstoffeinspritzungsvorlaufkupplung mit dem Antrieb.
Schrauben Sie das Bypassventil 11 ab (siehe Abb. 1) und schrauben Sie stattdessen den M14 x 1,5-Stecker mit Dichtung ein.
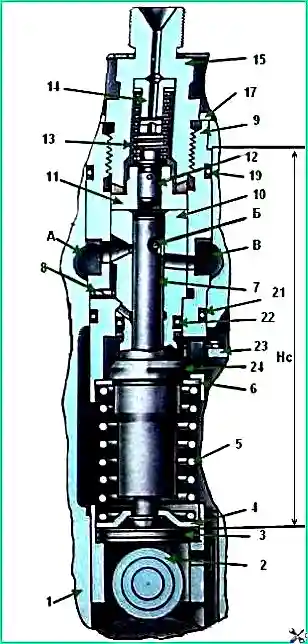
Abschnitt der Hochdruck-Kraftstoffpumpe: 1 - Pumpengehäuse; 2 - Drücker; 3 - Drückerferse; 4 - Drückerfederplatte; 5 - Drückerfeder; 6 - Unterlegscheibe; 7 - Kolben; 8 - Stift; 9 - Gehäuse des Pumpenabschnitts; 10 - Kolbenbuchse; 11 - Auslassventilkörper; 12 - Auslassventil; 13 - Auslassventilfeder; 14 - Federanschlag; 15 - passend; 16 - Einstellscheiben; 17 - Sicherungsscheibe der Armatur; 18 - Flansch; 19,21 und 22 - Dichtungsringe; 20 - Auslassventildichtung; 23 - linke Schiene; 24 - Drehhülse; A – Kraftstoffeinspritzhohlraum; B – spiralförmige Nut des Kolbens; B – Kraftstoffablasshohlraum; Hc – Größe, gemessen in dem Moment, in dem das Ende des Kolbens das Loch in der Kavität verschließt
Überprüfen Sie die Dichtheit der Auslassventile 12 (Abb. 3).
Zu diesem Zweck versorgen Sie die Pumpe über eine Rohrleitung mit einem Hahn und einem Manometer mit gefiltertem Kraftstoff unter einem Druck von 1,7–2,0 kgf/cm 2.
Schalten Sie die Kraftstoffzufuhr ab, indem Sie den Hebel 7 (Abb. 4) in die hinterste Position bewegen – bis zum Bolzen 8 (4 – Dichtung).
Es ist nicht zulässig, dass Kraftstoff aus den Anschlüssen 15 (siehe Abb. 3) 2 Minuten nach der Zufuhr zur Pumpe austritt.
Im Falle einer Undichtigkeit ersetzen Sie die Auslassventilbaugruppe durch Gehäuse 11.
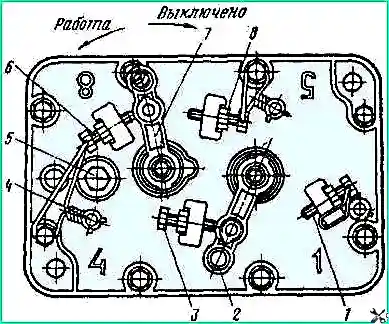
Überprüfen Sie den Öffnungsdruck der Ablassventile und stellen Sie ihn ggf. bei abgeschalteter Kraftstoffzufuhr ein.
Zu diesem Zweck wird über eine Rohrleitung mit Hahn und Manometer gefilterter Dieselkraftstoff durch den Versorgungsanschluss unter variablem, allmählich ansteigendem Druck von 5 kgf/cm 2 auf 15 kgf/cm 2 zugeführt
Messen Sie den Ventilöffnungsdruck mit dem Manometer an der Kraftstoffversorgungsleitung am Pumpenanschluss.
Als Öffnungsdruck des Auslassventils wird der Druck angenommen, der in dem Moment gemessen wird, in dem Kraftstoff aus dem Anschlussstück 15 zu fließen beginnt.
Der Öffnungsdruck des Auslassventils sollte innerhalb von 9 ÷ 10 kgf/cm 2 liegen.
Wenn der Ventilöffnungsdruck nicht dem angegebenen Wert entspricht, stellen Sie ihn mit der Dicke des Satzes Einstellscheiben 16 ein.
Mit zunehmender Dicke des Scheibenpakets nimmt der Öffnungsdruck des Auslassventils zu, mit abnehmender Dicke des Scheibenpakets nimmt er ab.
Nachdem Sie den Druck eingestellt haben, ziehen Sie die Armatur fest (Anzugsdrehmoment 10-12 kgf/m).
Beim Überprüfen und Einstellen des Beginns der Kraftstoffzufuhr in Abschnitten installieren Sie ein Drehmomentmessgerät (Abb. 5) am Anschlussstück des achten Abschnitts der Hochdruck-Kraftstoffpumpe (Abb. 5). Schließen Sie die restlichen Anschlüsse an die Einspritzdüsen an.
Durch den Einlassanschluss der Hochdruck-Kraftstoffpumpe über eine Rohrleitung mit Hahn und Manometer gefilterten Dieselkraftstoff mit einem Druck von 15–16 kgf/cm 2 zuführen.
Schalten Sie die volle Kraftstoffzufuhr ein, indem Sie den Hebel 2 (siehe Abb. 4) in die hinterste Position bewegen – bis zum Bolzen 1.
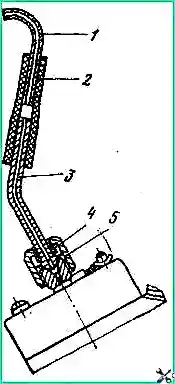
Öffnen Sie den Hahn und Kraftstoff fließt mit einem Druck von 15–16 kgf/cm 2 in den Hohlraum „A“ (siehe Abb. 3).
Drehen Sie die Pumpennockenwelle langsam im Uhrzeigersinn (von der Antriebsseite aus gesehen) durch die Einspritzvorstellkupplung und stellen Sie sicher, dass der Kraftstoffdruck das Einspritzventil 12 öffnet und Kraftstoff aus dem Kapillarrohr des Momentoskops zu fließen beginnt, das am Anschluss des angebracht ist Achter Abschnitt der Pumpe.
Eine weitere Drehung der Nockenwelle durch die Kupplung stoppt das Austreten von Kraftstoff aus dem Momentoskop.
Wenn der Kraftstofffluss aus dem Momentoskop während der Inspektion stoppt, verschließt die spiralförmige Nut „B“ des Kolbens den Zugang des Kraftstoffs vom Hohlraum „A“ zum Auslassventil und das Momentoskop.
Der Moment, in dem der Kraftstoff während des Tests aufhört, aus dem Momentoskop zu fließen, entspricht dem Beginn der Verdrängung (Zufuhr) von Kraftstoff aus dem Raum zwischen dem Kolben und dem Auslassventil durch den Kolben.
Daher folgt Erfassen Sie mit besonderer Genauigkeit den Moment, in dem der Kraftstofffluss mit dem Momentoskop stoppt, und verwenden Sie das Stativrad, um den Winkel in diesem Moment festzulegen.
Dieser Drehwinkel der Pumpennockenwelle ist der Beginn der Kraftstoffzufuhr durch den achten Abschnitt der Hochdruck-Kraftstoffpumpe.
Überprüfen Sie den Beginn der Kraftstoffzufuhr durch den achten Pumpenabschnitt und stellen Sie ihn ggf. durch Auswahl des Drückers ein.
Für eine korrekt eingestellte Kraftstoffpumpe sollte der Beginn der Kraftstoffzufuhr im achten Abschnitt 42°30′ ± 30′ vor der Symmetrieachse des Nockenprofils liegen.
In dem Moment, in dem der achte Abschnitt mit der Kraftstoffzufuhr beginnt, müssen die Markierungen auf dem Pumpenkörper und der Einspritzverstellungskupplung übereinstimmen.
Bewegen Sie das Momentoskop in der Reihenfolge des Pumpenbetriebs zu den Anschlüssen der verbleibenden Abschnitte.
Drehen Sie weiterhin die Nockenwelle durch die Kupplung für die Kraftstoffeinspritzung in der oben angegebenen Weise weiter und bestimmen Sie die Zeitpunkte, zu denen das Kraftstoffleck vom Momentoskop auf die übrigen Abschnitte der Pumpe übertragen wird, während Sie die Skalenwerte auf dem Ständer notieren.
Diese Messwerte sind die Momente, in denen jeder Abschnitt der Kraftstoffpumpe basierend auf dem Drehwinkel der Nockenwelle beginnt, Kraftstoff zu liefern.
Wenn der Drehwinkel der Pumpennockenwelle, bei dem der achte Abschnitt mit der Kraftstoffzufuhr begann, herkömmlicherweise als Startpunkt angenommen wird - 0˚, dann sollten die verbleibenden Abschnitte in der Reihenfolge des Pumpenbetriebs in der folgenden Reihenfolge mit der Kraftstoffzufuhr beginnen ( in Grad des Drehwinkels der Nockenwelle): Abschnitt 8 - 0°; Abschnitt 4 - 45°; Abschnitt 5 - 90°; Abschnitt 7 - 135°; Abschnitt 3 - 180°; Abschnitt 6 - 225°; Abschnitt 2 - 270°; Abschnitt 1 - 315°
Die Ungenauigkeit des Beginns der Kraftstoffzufuhr durch einen Pumpenabschnitt im Vergleich zum achten Abschnitt darf nicht mehr als ± 0˚20′ betragen.
Stellen Sie den Beginn der Kraftstoffzufuhr ein, indem Sie einen Drückeransatz mit der erforderlichen Dicke in den Drücker unter dem Kolben einsetzen.
Beim Einbau eines Absatzes mit größerer Dicke beginnt der Kraftstoff früher zu fließen, bei Einbau eines Absatzes mit geringerer Dicke erst später.
Eine Änderung der Fersendicke um 0,05 mm entspricht einer Änderung des Drehwinkels der Nockenwelle um 0°12′.
Der Hersteller sieht die Produktion des Drückerabsatzes in neunzehn Größengruppen vor (Tabelle 2).
Tabelle 2. Bezeichnung der Größengruppe – Drückerstärke: -9 – 3,60–0,05 mm; -8 - 3,65-0,05 mm; -7 - 3,70-0,05 mm; -6 - 3,75-0,05 mm; -5 - 3,80-0,05 mm; -4 - 3,85-0,05 mm; -3 - 3,90-0,05 mm; -2 - 3,95-0,05 mm; -1 - 4,00-0,05 mm; 0 - 4,05-0,05 mm; 1 - 4,10-0,05 mm; 2 - 4,15-0,05 mm; 3 - 4,20-0,05 mm; 4 - 4,25-0,05 mm; 5 - 4,30-0,05 mm; 6 - 4,35-0,05 mm; 7 - 4,40-0,05 mm; 8 - 4,45-0,05 mm; 9 - 4,50-0,05 mm
Die Nummer der Größengruppe ist auf dem nicht beanspruchten Teil des Endes der Drückerferse markiert.
Überprüfung und Einstellung der Pumpe entsprechend der von den Abschnitten gelieferten Kraftstoffmenge
Überprüfen Sie die Pumpe und stellen Sie sie auf Größe und Gleichmäßigkeit der Kraftstoffzufuhr abschnittsweise in der folgenden Reihenfolge ein
Anstelle des Stopfens das Bypassventil 11 einbauen (siehe Abb. 1) und den Kraftstoffdruck am Einlass der Kraftstoffpumpe bei einer Nockenwellendrehzahl von 1300 U/min prüfen. Der Kraftstoffdruck sollte 0,6–0,8 kgf/cm 2 betragen.
Wenn der Druck vom angegebenen Wert abweicht, schrauben Sie den Ventilstopfen ab und stellen Sie ihn mit Unterlegscheiben ein.
Dieselkraftstoff muss vor der Zufuhr zur Pumpe gefiltert werden und eine Temperatur von 25–30 °C haben.
Schalten Sie die volle Kraftstoffzufuhr ein, indem Sie den Hebel 2 (siehe Abb. 4) in die hinterste Position bewegen, bis er am Bolzen 1 anschlägt.
Überprüfen Sie bei einer Nockenwellendrehzahl von 1300 ± 10 U/min die durchschnittliche zyklische Kraftstoffzufuhr jedes Pumpenabschnitts und passen Sie sie gegebenenfalls an. Sie sollte 75,0–77,5 mm/Zyklus betragen.
Die Dauer jedes Experiments bei der Bestimmung der volumetrischen Brennstoffzufuhr sollte sicherstellen, dass das Volumen des gemessenen Brennstoffs in den Büretten des Standes mindestens 20 cm 3 beträgt.
Die Ungleichmäßigkeit der zyklischen Kraftstoffzufuhr über die Pumpenabschnitte sollte 5 % nicht überschreiten.
Die Größe des zyklischen Flusses jedes Pumpenabschnitts wird durch Drehen des Gehäuses von Abschnitt 17 (siehe Abb. 2) relativ zum Pumpengehäuse 1 eingestellt.
Bei einer Drehung des Profilkörpers nach rechts verringert sich der Taktvorschub, bei einer Drehung nach links erhöht er sich.
Vor der Einstellung die Mutter der Hochdruckleitung um eine oder zwei Umdrehungen abschrauben, den Anzug der Muttern 19 und 22 um eine halbe Umdrehung lockern.
Nach der Einstellung die Muttern 19 und 22 festziehen (Anzugsdrehmoment 2,5–3,0 kgf/m).
Überprüfen Sie die Drehzahl der Pumpennockenwelle in dem Moment, in dem sich die Zahnstangen in Richtung Abschalten der Kraftstoffzufuhr zu bewegen beginnen, und stellen Sie sie gegebenenfalls mit der Schraube 1 (siehe Abb. 4) ein.
Entfernen Sie vor der Überprüfung den Stecker 13 des Racks (siehe Abb. 1). Bei der Kontrolle sollte der Hebel 2 (Abb. 4) gegen den Bolzen 1 gedrückt werden.
Die Zahnstangen sollten sich bei einer Nockenwellengeschwindigkeit von 1335–1355 U/min zu bewegen beginnen.
Überprüfen Sie die Drehzahl der Nockenwelle entsprechend der vollständigen Abschaltung des Kraftstoffzufuhrgeschwindigkeitsreglers durch die Einspritzdüsen, wenn der Hebel 2 an der Schraube 1 anliegt.
Kraftstoffzufuhr bei einer Nockenwellendrehzahl von 1480-1555 U/min ist nicht zulässig.
Überprüfen und ggf Es ist möglich, die Drehzahl der Nockenwelle entsprechend dem Beginn des Abschaltens der Kraftstoffzufuhr durch die Einspritzdüsen einzustellen, wenn der Hebel 2 auf der Schraube 3 aufliegt.
Eine vollständige Abschaltung der Zufuhr sollte bei einer Nockenwellendrehzahl der Pumpe von 300–350 U/min erfolgen. Mit Schraube 3 einstellen.
Sollte die Kraftstoffzufuhr bei höherer Nockenwellendrehzahl abgeschaltet werden, Schraube 3 herausdrehen und bei niedrigerer Drehzahl festziehen.
Überprüfen Sie die Position des Bolzens 8, der den Weg des Hebels 7 in Richtung des Ausschaltens des Vorschubs begrenzt, und passen Sie ihn gegebenenfalls an.
Wenn Hebel 7 auf Bolzen 8 ruht, muss die Kraftstoffzufuhr von den Einspritzdüsen aller Abschnitte der Pumpe in jedem Geschwindigkeitsmodus der Pumpe vollständig gestoppt werden.
Überprüfen Sie gleichzeitig die Gangreserve der Zahnstangen in Richtung der Vorschubabschaltung, die 0,7-1,0 mm betragen sollte.
Überprüfen Sie die Menge der Startkraftstoffzufuhr und stellen Sie sie gegebenenfalls mit Schraube 6 bei einer Nockenwellendrehzahl von 100 ± 10 U/min ein und Hebel 2 stoppt in Schraube 1.
Die durchschnittliche Kraftstoffzufuhr zu Beginn sollte 195–210 mm 3/Zyklus betragen. Passen Sie die Menge der Startkraftstoffzufuhr mit der Schraube 6 an; Um den Vorschub zu erhöhen, schrauben Sie die Schraube heraus, um ihn zu verringern, ziehen Sie ihn fest.

Nach Überprüfungs- und Einstellarbeiten die Kraftstoffpumpe an den dafür vorgesehenen Stellen abdichten, um die Möglichkeit willkürlicher Einstelländerungen zu verhindern.
In einigen Fällen ist es beim Betrieb eines Fahrzeugs sowie bei der Durchführung von Kontroll- und Einstellarbeiten erforderlich, die Hochdruck-Kraftstoffpumpe teilweise oder vollständig zu zerlegen, um den Stößelfuß, das Auslassventil, das Kolbenpaar usw. auszutauschen.
Komplette Demontage der Hochdruck-Kraftstoffpumpe:
Montieren und befestigen Sie die Pumpe auf einem speziellen Ständer oder in einem Schraubstock;
- - Entfernen Sie die Dichtungen, lösen Sie die vier Schrauben und entfernen Sie das Schutzgehäuse 24 (siehe Abb. 2);
- - Entfernen Sie die Dichtung, lösen Sie die acht Schrauben und entfernen Sie die montierte Abdeckung 7 (siehe Abb. 1);
- - Zerlegen Sie den Zentrifugalgeschwindigkeitsregler (Abb. 6), indem Sie die Achse 44 entfernen und, ohne sie zu lösen, die Hebel 42, 43 und 35, den Druckknopf 47 mit Unterlegscheiben und die Feder 37 entfernen.
- - Trennen Sie die entfernten Teile. Um die Hebel 42 und 43 zu trennen, entfernen Sie die Buchse. Entfernen Sie im Notfall die Feder 39 und den Hebel 36. Entfernen Sie die Gewichtskupplung 12 mit Lager 11;
- - Wenn das Lager ausgetauscht wird, entfernen Sie den Sicherungsring und drücken Sie das Lager 11 von der Kupplung. Schrauben Sie die Stopfen 13 ab (siehe Abb. 1);
- - Lösen Sie die beiden Muttern und entfernen Sie die Kraftstoffansaugpumpe 29 (siehe Abb. 2) mit der Druckfeder 31 und der manuellen Kraftstoffansaugpumpe 25. Lösen Sie bei Bedarf die Schraube und entfernen Sie die manuelle Kraftstoffansaugpumpe;
- - Lösen Sie die sieben Schrauben und entfernen Sie, um die Dichtung vor Beschädigungen zu schützen, die hintere Abdeckung 1 (siehe Abb. 6) mit Lager 4 und Niederdruckpumpenstößel. Entfernen Sie die Dichtung 7;
- - Öffnen Sie die Klammern 34 an den Lamellen, lösen Sie die beiden Sicherungsschrauben der Buchsen und entfernen Sie die Buchsen 9 (siehe Abb. 1), entfernen Sie die rechten Lamellen 33 (siehe Abb. 6) und die linken Lamellen 38. Lösen Sie den Splint, entfernen Sie die Unterlegscheibe und den Zahnstangenhebel 41;
- - Entfernen Sie den Sicherungsring 8 und den Gewichtshalter 9 mit Lager 23 und Gewichten 13. Drücken Sie bei Bedarf die Achsen 10 heraus, entfernen Sie die Gewichte 13 und drücken Sie das Lager 23 zusammen;
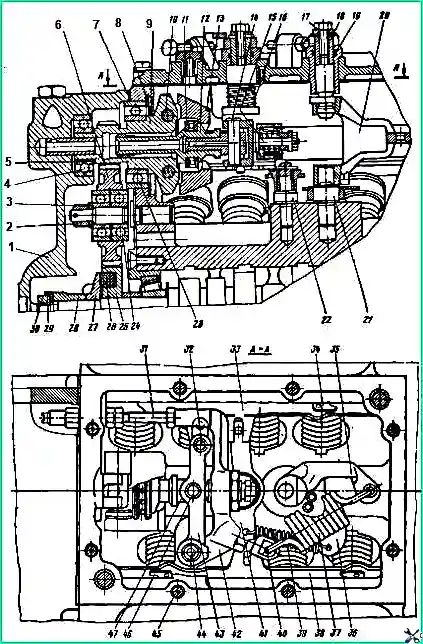
Drehzahlregler: 1 - hintere Abdeckung des Reglers: 2, 30 - Mutter; 3 - Unterlegscheibe; 4 - Lager; 5 - Einstelldichtung; 6 - Zwischengang; 7 - Dichtung für die hintere Abdeckung des Reglers; 8 - Sicherungsring; 9 - Gewichtshalter; 10 - Lastachse; 11 - Axiallager; 12 - Kupplung; 13 - Fracht; 14,46 - Finger; 15 - Korrektor; 16 - Rückholfeder des Anschlaghebels; 17 - Bolzen; 18 - Buchse: 19 - Ring; 20 - Reglerfederhebel; 21 - Federhebelachse: 22 - Zahnstangenhebelachse; 23, 24 - Lager; 25 - Antriebsrad; 26 - Antriebsradblock; 27 - Antriebsradflansch; 28 - Exzenter der Kraftstoffpumpe; 29 - Biegesicherungsscheibe; 31 - Einstellschraube; 32 - Stift; 33 - rechte Schiene; 34 - Riegel; 35 - Reglerfederhebel; 36 - Startfederhebel; 37 - Reglerfeder; 38 - linke Schiene; 39 - Startfeder (Zahnstangenhebelfeder); 40 - Einstellschraube der Reglerfeder; 41 - Zahnstangenhebel; 42 - Reglerhebel; 43 - Lastkupplungshebel; 44 - Achse der Reglerhebel; 45 - Befestigungsschraube der Abdeckung; 47 – hartnäckiger Absatz
- - Entfernen Sie die zusammengebauten Teile der Kraftstoffpumpe. Markieren Sie dazu die Position der Abschnitte relativ zur Buchse im Pumpengehäuse – machen Sie einen Kern am Gehäuse Pumpenmarkierung und gegen die Markierungen am Flansch 23 (siehe Abb. 2) des Sektionsgehäuses.
Dies hilft bei der Montage, die Abschnitte in der Position zu platzieren, in der sie sich vor der Demontage befanden.
Muttern 19 und 22 abschrauben. In diesem Fall ist es notwendig, die Nockenwelle so zu drehen, dass sich Drücker und Stößel des Abschnitts beim Lösen der Muttern in der unteren Position befinden.
Andernfalls können unter der Kraft der Feder 8 des Drückers die Gewinde der Bolzen und Muttern 19 und 22 beschädigt werden;
- - Entfernen Sie die Sicherungsscheiben der Anschlüsse, entfernen Sie die Abschnitte und Schieberbaugruppen vom Pumpenkörper und ordnen Sie sie in den Zellen des tragbaren Gestells an. Schrauben Sie die Muttern 19 und 22 von Hand auf die Stehbolzen des Pumpengehäuses;
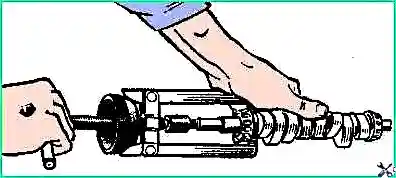
- - Mutter 15 abschrauben (siehe Abb. 1), Unterlegscheibe 16 entfernen und mit dem Abzieher I-801.16.000 die Kupplung 14 von der Nockenwelle drücken, Passfeder 17 entfernen;
- - Drehzahlreglerantrieb demontieren, dazu Mutter 3 auf- und abschrauben, Unterlegscheibe entfernen und mit einem Abzieher das mit den Lagern 2 zusammengebaute Zahnrad 1 abnehmen.
Mutter 36 lösen und abschrauben, Abzieher I-801.26.000 einbauen (Abb. 7) und Exzenter 34 (siehe Abb. 1), Flansch 32, Zahnrad 30 mit Muttern 31 entfernen;
- - Lösen Sie die Schrauben, mit denen die vorderen Nockenwellenlagerdeckel 18 und die hinteren Nockenwellenlagerdeckel 28 befestigt sind, entfernen Sie die Deckel mit zwei Schraubendrehern vom Pumpengehäuse und entfernen Sie die mit den Lagern 23 und 27 zusammengebaute Nockenwelle 25.
An den Flanschen der Abdeckungen 18 und 28 sind zur Demontage mit Schraubendrehern zwei diametral angeordnete Nuten angebracht;
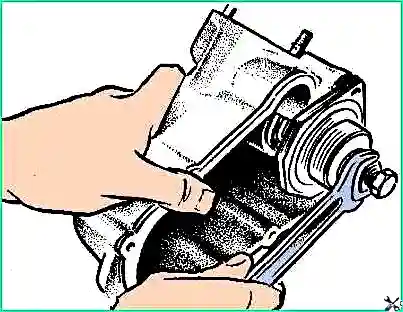
- - Installieren Sie den Abzieher I-801 .29.000 (Abb. 8) und entfernen Sie die Lager von der Nockenwelle;
- - Abzieher I-801.24.000 einbauen (Abb. 9) und Lager 5 vom Deckel 4 abnehmen (siehe Abb. 1);
- - Lösen Sie die Feststellschraube 33 (siehe Abb. 2) und entfernen Sie die Drückerbaugruppe 32;
- - Zerlegen Sie ggf. den Abschnitt der Kraftstoffpumpe;
- - Fitting 15 abschrauben (siehe Abb. 3), Federanschlag 14 und Feder 13 zusammen mit dem Fitting entfernen.
Installieren Sie das Gerät I-801.21.000 (Abb. 10) und entfernen Sie durch Drücken des Griffs des Geräts das Gehäuse 11 (siehe Abb. 3), die Dichtung 20 und das Auslassventil 12;
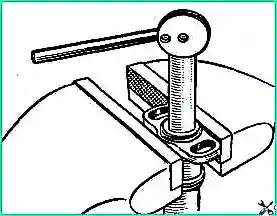
- - Drücken Sie die Feder 5 zusammen, entfernen Sie die Platte 4, die Feder 5 und die Unterlegscheibe 6. Entfernen Sie die Kolbenpaarbaugruppe aus dem Gehäuse 9 des Pumpenabschnitts (Kolben 7, Kolbenhülse 10). Drehhülse 24 aus Gehäuse 9 entfernen.
Berühren Sie beim Zerlegen eines Abschnitts die Arbeitsflächen des Kolbenpaars nicht mit ungeschützten Händen.
Bauen Sie die Kraftstoffausrüstungseinheiten in umgekehrter Reihenfolge wie die Demontage zusammen. Folgendes muss beachtet werden.
Eine Entpersonalisierung der zusammengebauten Abschnitte der Kraftstoffpumpe und der Kolbenschieber entlang der Buchsen des Kraftstoffpumpengehäuses ist nicht zulässig – sie sind hinsichtlich der Abmessungsparameter aufeinander abgestimmt.
Daher sollten Teile der Kraftstoffpumpe und der Stößel nach Möglichkeit aus bereits vorhandenen geeigneten Verschleißteilen zusammengebaut und in denselben Schlitzen des Kraftstoffpumpengehäuses eingebaut werden, in denen sie vor der Demontage standen.
Die zusammenzubauenden Teile müssen sauber sein und die Reibflächen müssen mit Motoröl geschmiert sein. Korrosion, Schmutz und Kerben auf den Arbeitsflächen der Teile sind nicht zulässig.
Wischen Sie Teile nicht mit Reinigungsmittel ab und fassen Sie sie nicht mit ungeschützten Händen an.
Neue Kolbenpaare oder Auslassventile müssen in gefiltertem Dieselkraftstoff gewaschen werden.
Vor dem Einpressen der Achsen und Befestigungsstifte in das Pumpengehäuse muss dieses im Ölbad auf 80 ÷ 100 °C erhitzt und die eingepressten Teile mit Motoröl geschmiert werden.
Gummidichtringe mit Dornen in die Nuten einbauen, ohne sie zu beschädigen oder zu verdrehen.
Schmieren Sie die Einführschrägen und Oberflächen von Teilen, die mit Dichtringen und Dichtungen zusammenpassen, vor dem Zusammenbau mit dem Schmiermittel CIATIM-20I oder CIATIM-203.
Prüfen Sie beim Einbau von Lagern nach dem Aufpressen des Innenrings auf die Welle den Zustand des Innenrings.
Montieren Sie die Frontabdeckung 18 (siehe Abb. 1) vorsichtig und schützen Sie dabei die Manschette 20 vor Beschädigung.
Ziehen Sie die Befestigungsschrauben 18 und 28 der Abdeckung fest an und verriegeln Sie sie, indem Sie das Gehäusemetall im Kopfschlitz verstemmen Schraube.
Wenn die Deckelbefestigungsschrauben 18 und 28 festgezogen sind, sollte sich die Nockenwelle in den Lagern von Hand frei drehen lassen.
Das Längsspiel (axial) der Welle sollte bei Anwendung einer Axialkraft von 5–6 kgf im Bereich von 0,01–0,07 mm liegen. Mit Unterlegscheiben 19 anpassen.
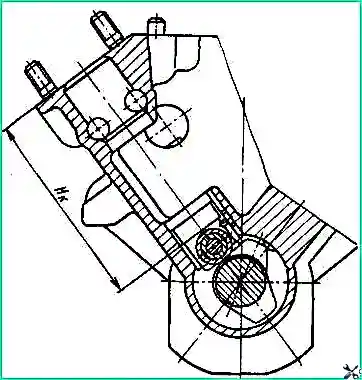
Beim Zusammenbau der Kolbenschieber drücken Sie den Stift bündig mit der Auflagefläche unter dem Schieberfuß.
Die Druckrolle sollte sich frei auf der Buchse drehen, und die Buchse sollte sich frei auf der Rollenachse drehen. Ein Verklemmen beim Zusammenstecken der angegebenen Teile ist nicht zulässig.
Die mit Motoröl geschmierte Stößel- und Blockbaugruppe muss sich unter dem Einfluss der Schwerkraft frei im Kraftstoffpumpensockel bewegen können.
Wenn Sie die Nockenwelle, das Kraftstoffpumpengehäuse oder die Kolbenstößel austauschen, messen Sie die Abschnitte des Kraftstoffpumpengehäuses – Größe „Hc“ (Abb. 11).
Wenn Sie Messungen durchführen, installieren Sie die Nockenwelle so, dass sich der Kolbenstößel des zu messenden Abschnitts in der untersten Position befindet.
Wenn Sie das Kolbenpaar des neu zusammengebauten Abschnitts austauschen, messen Sie das Maß „Hk“ (siehe Abb. 3). Das Maß „N“ wird in dem Moment gemessen, in dem das Ende des Kolbens 7 das Loch des Auslasshohlraums „A“ verschließt.
Gemäß Messergebnissen und Tabelle. 3 Bestimmen Sie die Gruppennummer und markieren Sie diese Nummer deutlich am Abschnittssockel am Kraftstoffpumpengehäuse, Flansch 18 des Abschnittsgehäuses. Prägen Sie die vorherigen Gruppennummern.
Tabelle 3. „Hk“ – Kraftstoffpumpengehäuse – Hc – Kraftstoffpumpenabschnitte – Gruppennummer:
- 117,80-117,85 mm - 110,70-110,75 mm - 0;
- 117,85-117,90 mm - 110,75 -110,80 mm - 1;
- 117,90-117, 95 mm - 110,80-110,85 mm - 2;
- 117,95–118,00 mm – 110,85–110,90 mm – 3;
- 118,00-118,05 mm - 110,90-110,95 mm - 4;
- 118,05–118,10 mm – 110,95–111,00 mm – 5;
- 118,10-118,15 mm - 111,00-111,05 mm - 6;
- 118,15–118,20 mm – 111,05–111,10 mm – 7;
- 118, 20–118,25 mm – 111,10–111,15 mm – 8;
- 118,25-118,30 mm - 111,15-111,20 mm - 9
Der Unterschied zwischen den Gruppennummern der Sektionsbuchse im Pumpenkörper und der Sektion 1-Baugruppe bestimmt die Gruppennummer und die Größe des Drückerabsatzes 3.
Beim Zusammenbau eines Kraftstoffpumpenteils mit einem neuen Kolbenpaar ist zusätzlich die Leichtgängigkeit des Kolbens über die gesamte Hublänge und den Drehwinkel zu prüfen; Ein Verklemmen des Stößels in der Buchse ist nicht zulässig.
Überprüfen Sie, ob der Kolbenschaft 7 in der Platte 4 versenkt ist.
Das untere Ende des Kolbens 7 sollte die Ebene der Platte 4 nicht um 0,1–0,3 mm erreichen.
Beim Zusammenbau Anschluss 15 mit Dieselkraftstoff schmieren und festziehen (Anzugsdrehmoment 10-12 kgf/m).
Überprüfen Sie nach der Montage die Leichtgängigkeit der Drehhülse 24 bei gespannter Feder des Drückers 5. Die Hülse darf nicht verklemmen.
Installieren Sie die zusammengebauten Abschnitte so in das Kraftstoffpumpengehäuse, dass sich die Befestigungsbolzen der Abschnitte in der Mitte der Löcher im Flansch des Abschnittsgehäuses befinden.
In diesem Fall sollten die Schlitze am Gehäuse des Abschnitts für die Installation des Racks und die Markierung am Kolben zum Hohlraum im Pumpengehäuse für den Regler zeigen.
Ziehen Sie die Muttern 19 und 22 (siehe Abb. 2) fest, mit denen der Flansch 23 des Kraftstoffpumpenabschnitts befestigt ist (Anzugsdrehmoment 2,5–4,5 kgf/m).
Prüfen Sie nach dem Anziehen der Muttern 19 und 22 die reibungslose Bewegung der Zahnstange beim Drehen der Nockenwelle.
Nachdem Sie den Beginn der Kraftstoffzufuhr durch die Pumpenabschnitte eingestellt haben, überprüfen Sie die Kraftstoffpumpe mithilfe der folgenden Methode auf Undichtigkeiten in der Niederdruck-Kraftstoffleitung.
Lassen Sie den Kraftstoff aus der Niederdruckleitung ab und verschließen Sie die Öffnung des Bypassventils mit einem Stopfen.
Tauchen Sie die Kraftstoffpumpe in ein Bad mit Dieselkraftstoff, sodass sich die Gewinde der Anschlüsse 21 über dem Niveau der Kraftstoffoberfläche befinden. Führen Sie Luft durch den Kraftstoffversorgungsanschluss in die Niederdruck-Kraftstoffleitung ein.
Das Kraftstoffsystem der Pumpe ist dicht, wenn der Druck mit einer Geschwindigkeit von 1,5 kgf/cm 2/min von 0,5 kgf/cm 2 allmählich ansteigt bis 5 kgf/cm 2 werden keine Luftblasen aus der Pumpe beobachtet.
Stellen Sie beim Zusammenbau des Reglers sicher, dass sich das Zahnrad 25 (siehe Abb. 6) auf der Nockenwelle dreht, ohne zu blockieren.
Nach dem Einbau der Dämpferteile (Zahnrad 25, Block 26, Distanzstück, Passfeder, Flansch 27 und Exzenter 28) Mutter 30 festziehen (Anzugsdrehmoment 4-6 kgf/m) und mit Unterlegscheibe 29 sichern.
Umlaufendes Spiel in den Getriebedämpferteilen ist nicht zulässig.
Die Reglerlasten sollten sich im statischen Moment um 2x10 kgf/m unterscheiden, nicht mehr. Die auf der Halterung montierten Gewichte müssen unter dem Einfluss ihres Eigengewichts frei um ihre Achsen schwingen.
Bevor Sie die Buchse auf die Kupplung 12 aufpressen, erhitzen Sie die Buchse im Ölbad auf 80–100 °C und schmieren Sie die Kupplung mit Motoröl.
Muss kostenlos sein, ohne zu klemmen oder zu kleben, bewegen und drehen:
- - Kupplung 12 im Halter 9;
- - Ferse in Kupplung 12 und auf Stift 14 des Lastkupplungshebels drücken.
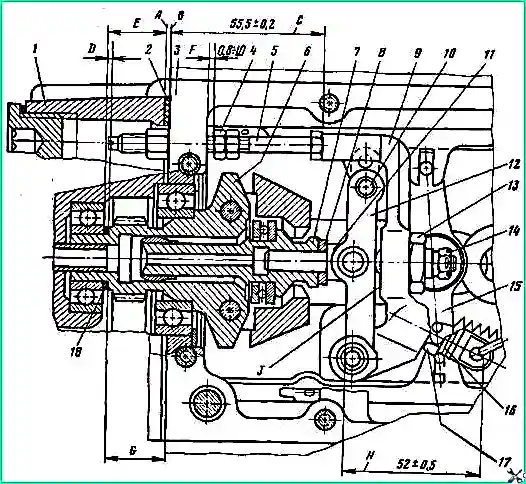
Geschwindigkeitsregler; 1 - hintere Abdeckung des Reglers; 2 - Dichtung für die hintere Abdeckung des Reglers; 3 - Pumpengehäuse; 4- Begrenzungsmutter; 5 - Hebeleinstellschraube; 6 - Reglergewichtshalter; 7 - Reglergewichtskupplung; 8 - Messgerät; 9 - Reglerhebel 10 - Stift; 11 - Schubfuß der Lastkupplung: 12 - Hebel der Lastkupplung; 13 - Korrekturkörpermutter: 14 - Korrekturmutter; 15 - Zahnstangenhebel; 16 - Federeinstellschraube; 17 - Kontermutter; 18 – Einstellscheiben
Beim Zusammenbau der Hebel 9 und 12 (Abb. 11) ist darauf zu achten, dass die Einstellschraube 16 der Reglerfeder auf das Maß H = 52 ± 0,5 mm in den Hebel 9 eingeschraubt und mit der Mutter 17 gesichert wird.
Stellen Sie die Vorspannung der Korrekturfeder mit Mutter 14 ein. Sie sollte 15–16 kgf betragen.
Sichern Sie nach der Einstellung die Mutter 14 mit einem Splint. Wickeln Sie den Korrektorkörper so in den Hebel 9, dass der Korrektorkopf 0,05–0,15 mm über die „J“-Ebene hinausragt.
Befestigen Sie das Korrektorgehäuse nach der Installation mit der Mutter 13.
Stellen Sie beim Zusammenbau der oberen Abdeckung Folgendes sicher
Bevor Sie die Buchsen einpressen, erhitzen Sie den Deckel auf 80–100 °C und schmieren Sie die Buchsen mit Motoröl.
Die Rückholfeder 16 (siehe Abb. 6) sollte den Hebel 7 (siehe Abb. 4) in seine ursprüngliche Position zurückbringen (bis er am Bolzen 6 anschlägt).
Wickeln Sie die Einstellschrauben zur Hubbegrenzung der Hebel 2 und 7 in die Vorsprünge und sichern Sie sie mit Muttern.
Außerdem sollten die Schrauben 3 und 6 2–4 bzw. 8–10 mm aus den Vorsprüngen herausragen und die Schrauben 1 und 8 sollten bündig mit den Enden der Vorsprünge verschraubt sein.
Beim Zusammenbau von Deckel 1 (siehe Abb. 6) vor dem Einpressen von Lager 4 den Deckel auf 80-100° C erwärmen.
Nach dem Pressen kühlen Sie die Abdeckung auf 20 ± 3° C ab und messen das Maß „E“ (siehe Abb. 12) von der Passebene „A“. die Abdeckung bis zum Ende des Halterlagers.
Stellen Sie beim Einbau von Teilen in das Hochdruck-Kraftstoffpumpengehäuse Folgendes sicher.
Die Einstellhebel sollten sich frei bewegen lassen, ohne zu blockieren, und die Lagersicherungsringe sollten in ihren Nuten liegen.
Montieren Sie die Reglerfedern 37 (siehe Abb. 6) und den Startvorschub 39 so, dass das freie Ende des Federhakens nach unten zur Nockenwelle gerichtet ist.
Der Überstand des Endes des Kopfes der Schraube 5 (siehe Abb. 12) aus der Passebene „B“ des Pumpengehäuses sollte dem Maß C = (55,5 ± 0,2 mm entsprechen ).
Der Spalt zwischen dem Kraftstoffpumpengehäuse 3 und der Begrenzungsmutter 4 sollte der Größe „F“ = (0,8-1,0 mm) entsprechen.
Einstellbolzen 5 und Begrenzungsmutter 4 müssen verriegelt sein.
Überprüfen Sie vor der Montage des Hebels 35 (siehe Abb. 4) die Bewegungskraft des Hebels 43, der über den Stift 32 mit den Lamellen verbunden ist, in Richtung der Achse der Gewichtskupplung.
Bei einer stationären Nockenwelle sollte diese Kraft in der mittleren Position der Zahnstangen nicht mehr als 0,15 kgf und in den äußersten Positionen 0,6 kgf betragen.
Bestimmen Sie beim Einbau der Reglerteile in das Hochdruck-Kraftstoffpumpengehäuse die Dicke „E“des Ausgleichsscheibenpakets 18 (siehe Abb. 12).
Die Dicke des Pakets der Einstellscheiben 18 beeinflusst die Gangreserve der Zahnstangen in Richtung des Abschaltens der Kraftstoffzufuhr, wenn die Reglerlasten vollständig ausgefahren sind, die Drehzahl der Nockenwelle 500–550 U/min beträgt und der Hebel 2 (siehe Abb. 4) liegt auf Bolzen 3.
Mit abnehmender Dicke des Dichtungspakets erhöht sich die Gangreserve der Zahnstangen, mit zunehmender Dicke nimmt sie ab.
Zur Durchführung dieser Arbeiten bewegen Sie die Gewichtskupplung 7 (siehe Abb. 12), den mit Gewichten bestückten Halter 6 in axialer Richtung in Richtung der hinteren Abdeckung 1.
In den entstandenen Spalt zwischen Kupplung 7 und Fünftel 11 ein Messgerät mit einer Dicke von 3,75-0,026 mm einbauen.
Nach der Installation des Messgeräts legen Sie den Hebel 9 gegen den Kopf der Schraube 5 und den Hebel 12 gegen den Hebel 9. Bewegen Sie gleichzeitig den Halter 6 mit der Kupplung 7 an die Ferse 11, sodass diese festgeklemmt wird:
- - Messgerät zwischen Kupplung 7 und Quinte 11;
- - Gewichtsrollen zwischen der Plattform des Halters 6 und der Kupplung 7. In dieser Position des Halters 6 messen Sie das Maß G – den Überstand des Endes des Halters über die Passebene „B“ des Pumpengehäuses.
Bestimmen Sie anhand der Formel die Dicke D des Unterlegscheibenpakets 18:
B = E +0,6 – G
In dieser Formel wurden die Abmessungen von E und G durch Messungen ermittelt, 0,6 ist die Dicke der Paronitdichtung 2.
Sie können die Dicke D auch aus einem Paket Einstellscheiben ermitteln, wenn Sie über ein Messgerät mit einer Dicke von 3,75–0,025 mm und einen Satz Fühlerlehren verfügen.
Gleichzeitig gibt es 3 Installationen am Pumpengehäuse Schrauben Sie die hintere Abdeckung 1 mit der Dichtung 2 ein und befestigen Sie sie mit Schrauben. Bewegen Sie den Halter 6 mit der Kupplung 7 in Richtung der Abdeckung 1, bis das Ende der Halterung am Abdeckungslager anschlägt.
Drücken Sie Hebel 9 auf den Kopf von Bolzen 5, Hebel 12 auf Hebel 9 und installieren Sie eine Messvorrichtung und ein Paket Fühlerlehren in dem Spalt, der zwischen der Ferse 11 und der Kupplung 7 entsteht.
Die Dicke des Stiftpakets muss so sein, dass die Gewichtsrollen zwischen der Gewichtshalterplattform und der Gewichtskupplung eingeklemmt werden.
Die Dicke der Sonden bestimmt die Dicke „E“ des Dichtungspakets 18. Nach Abschluss der Arbeiten Deckel 1 abnehmen und das Dichtungspaket 18 mit der Dicke E, überprüfen Sie die Sicherung der Muttern 3 und 36 (siehe Abb. 1).
Montieren Sie die Abdeckung am Pumpengehäuse und befestigen Sie sie mit Schrauben.
Befestigen Sie die drei oberen Schrauben, mit denen die hintere Abdeckung befestigt ist, mit Dichtpaste. Der Unterschied zwischen der ermittelten Dicke Ddes Dichtungspakets und der tatsächlich verbauten Dicke sollte 0,1 mm nicht überschreiten.
Stellen Sie nach der Montage sicher, dass die Hubreserve der Zahnstangen in Richtung der Vorschubabschaltung bei vollständig ausgefahrenen Reglergewichten mindestens 0,5 mm beträgt.
Im zusammengebauten Regler sollten sich alle Teile ohne Blockierung bewegen lassen.
Die Steuer- und Abschalthebel des Reglers müssen unter der Wirkung der Federn deutlich in ihre Ausgangsposition zurückkehren.
Beachten Sie beim Zusammenbau der Niederdruck-Kraftstoffpumpe und der manuellen Kraftstoffansaugpumpe bitte Folgendes.
Die Stange und die Buchse der Niederdruck-Kraftstoffpumpe sind ein Präzisionspaar, das nicht zerlegt werden darf.
Wenn es notwendig ist, eines der Teile auszutauschen, tauschen Sie es als Ganzes aus.
Montieren Sie eine neue Buchse mit einer Stange mit Epoxidkleber im Gehäuse. Überprüfen Sie nach dem Trocknen des Klebers die Dichtheit des Gehäuses mit Luft unter einem Druck von 4–6 kgf/cm 2.
Das Gehäuse und der Kolben der Niederdruck-Kraftstoffpumpe sind entsprechend dem Durchmesser des Zylinders bzw. des Kolbens in zwei Größengruppen unterteilt; der Zylinder und der Kolben der Handpumpe sind in drei Größengruppen unterteilt.
Die Gruppennummer ist an einer gut sichtbaren Stelle auf den Teilen markiert. Im Falle eines Austauschs muss das neu eingebaute Teil derselben Größengruppe angehören.
Beim Zusammenbau der Niederdruck-Kraftstoff-Verschleißteile und der Handpumpe diese mit gefiltertem Dieselkraftstoff schmieren (befeuchten)
Ziehen Sie die Gewindeverbindung des Handpumpenzylinders am Zylinderkörper und die Schraube fest, mit der die Handpumpenbaugruppe am Niederdruckpumpenkörper befestigt ist. Das Anzugsdrehmoment sollte die Dichtheit der Verbindung gewährleisten.
Beim Zusammenbau der automatischen Kraftstoffeinspritz-Vorlaufkupplung dürfen die Lasten nicht entpersonalisiert werden.
Basierend auf dem statischen Moment relativ zum Loch für die Lastachse werden sie in sechs Größengruppen eingeteilt.
Der Unterschied im statischen Lastmoment einer Gruppe sollte 8x10 kgf/m betragen, nicht mehr.
Bevor Sie die Teile der Kraftstoffeinspritz-Vorstellkupplung zusammenbauen, schmieren Sie diese mit Motoröl.
Schraubverbindung von Gehäuse 1 mit angetriebener Kupplungshälfte 9 festziehen (Anzugsdrehmoment 25-28 kgf).
Nach dem Zusammenbau wird die Hochdruck-Kraftstoffpumpenbaugruppe mit der Niederdruckpumpe und der Einspritzverstellkupplung eine Stunde lang unter Prüfstandsbedingungen mit Dieselkraftstoff und einer Nockenwellendrehzahl von 1000 ± 50 U/min betrieben.
Beim Betrieb auf einem Ständer sollte die Pumpe durch Zwangszirkulation von gefiltertem Motoröl unter einem Druck von 1–7 kgf/cm 2 geschmiert werden.
Vor dem Test 0,16-0,20 Liter Motoröl durch das mit Stopfen 5 (siehe Abb. 4) verschlossene Loch in die Pumpe und durch die mit Schrauben 13 verschlossenen Löcher in die Kupplung gießen.
Der Kraftstoffdruck in der Niederdruckleitung der Kraftstoffpumpe sollte 0,5–2 kgf/cm 2 betragen.
Während der ersten 10 Minuten des Einfahrens sollte Hebel 2 (siehe Abb. 4) an Bolzen 3 anliegen.
In den nächsten 50 Minuten sollte sich Hebel 2 mit einer Frequenz von 10–12 vollständigen Bewegungen pro Minute zwischen Bolzen 1 und 3 bewegen.
Führen Sie die Einfahrphase mit einem getesteten Satz Einspritzdüsen durch.
Während des Einlaufens der Pumpe sind Stöße und Fremdgeräusche nicht zulässig. Die Öltemperatur am Ausgang der Kraftstoffpumpe sollte 80° C nicht überschreiten.
Sollten Sie beim Einlaufen ein Klopfgeräusch, Fremdgeräusche oder eine andere Störung bemerken, stoppen Sie den Einlauf, zerlegen Sie die Pumpe, beheben Sie den Fehler und bauen Sie die Pumpe wieder zusammen.
Wiederholen Sie den vollständigen Einlauf der Pumpe, wenn bei der Fehlerbehebung mindestens eines der folgenden Teile (Baugruppen) durch ein neues, nicht eingelaufenes ersetzt wurde: Kraftstoffpumpengehäuse, Kolbenpaar, Nockenwelle mit Lagern, Kolbenschieber, Auslassventil, Reglerantriebsrad, Gewichtshalter, Druckstück, Einstellhebeln, hinterer Einstellerabdeckung, Zahnstange, Gehäuse oder Kolben oder Schieber der Niederdruck-Kraftstoffpumpe.