Compresor (Fig. 1) tipo pistón, flujo indirecto, dos cilindros, compresión de una etapa
El aire del filtro de aire del motor ingresa a los cilindros del compresor a través de las válvulas de entrada de paletas.
El aire comprimido por los pistones es impulsado hacia el sistema neumático a través de válvulas de descarga de placa ubicadas en la culata.
El bloque y el cabezal se enfrían mediante líquido suministrado desde el sistema de refrigeración del motor.
El sistema de refrigeración del compresor se llena sólo cuando el motor está en marcha.
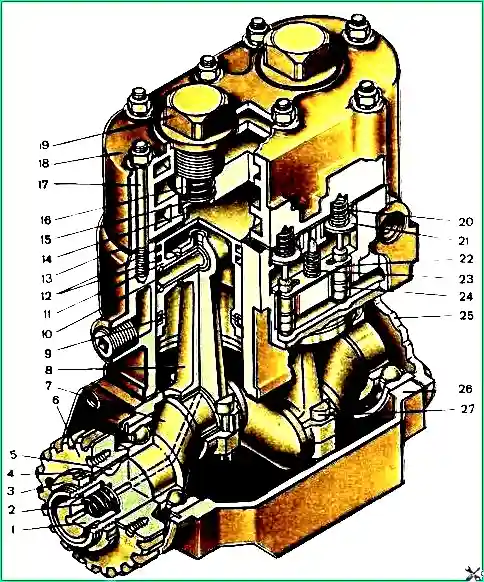
Compresor de automóvil Ural: 1 - junta, 2 - resorte de junta, 3 - tuerca de fijación del engranaje, 4 - arandela de seguridad, 5 - llave segmentada, 6 - engranaje impulsor, 7 - cigüeñal, 8 - biela, 9 - raspador de aceite anillo, 10 - pasadores de pistón, 11 - pistones, 12 - anillos de compresión, 13 - junta de culata, 14 - asiento de válvula de descarga, 15 - válvula de descarga, 16 - resorte de válvula de descarga, 17 - espárrago de culata, 18 - culata, 19 - tapón de la válvula de descarga, 20 - resorte de la válvula de admisión, 21 - válvula de admisión, 22 - balancín, 23 - resorte del balancín, 24 - émbolo con biela, 25 - tapa, 26 - cárter, 27 - perno de biela
El aceite se suministra a las superficies de fricción del compresor a través de un tubo desde la línea de aceite del motor hasta la cubierta trasera del cárter del compresor y a través del sello a través de los canales del cigüeñal hasta los cojinetes de biela.
Los signos de un compresor que funciona mal son ruido durante el funcionamiento, golpes y un mayor contenido de aceite en el condensado drenado de los cilindros de aire.
El aumento del contenido de aceite en el condensado suele ser consecuencia del desgaste de los aros del pistón y de los cojinetes de las cabezas inferiores de las bielas.
El compresor está instalado en la parte trasera de la inclinación del motor (Fig. 2) y está asegurado con cuatro pernos 15 a la pared frontal de la tapa del engranaje de distribución 14, realizada en la misma fundición que la carcasa del volante.
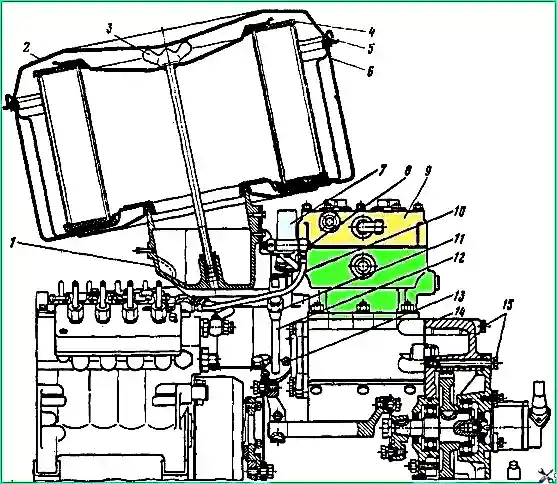
Instalación del compresor en el motor: 7 - tubo de conexión; 2 - tapa del filtro de aire; 3 - varilla para sujetar el elemento filtrante; 4 - elemento filtrante; 5 - junta de tapa; 6 - carcasa del filtro; 7 - válvula solenoide; 8 - perno de la línea de combustible; 9 - compresor; 10 - manguera de combustible; 11 - tuerca de unión; 12 - tubo de suministro de agua; 13 - nueces; 14 - tapa; 15 - tornillos
Mantenimiento del compresor
Válvulas de regazo que no proporcionan un sello hermético a los asientos; si están desgastadas o dañadas, reemplácelas.
Lape las válvulas nuevas en los asientos hasta que se obtenga un contacto anular continuo al comprobar si hay pintura.
Apriete las tuercas de los pernos de montaje de la culata en pares, comenzando con el par central ubicado diametralmente.
Apriete las tuercas en dos pasos: el par de apriete final debe ser de 12-16 N.m (1,2-1,6 kgf/m).
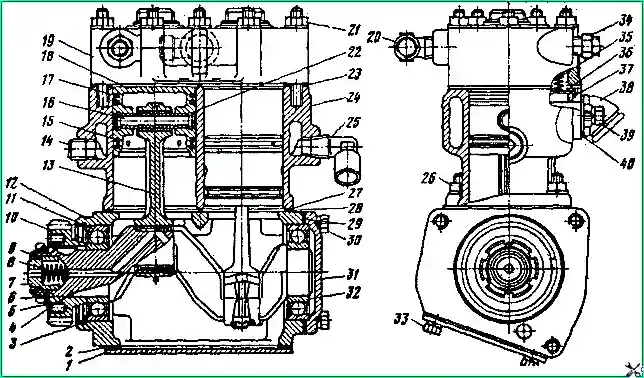
Compresor: 1 - tapa inferior del cárter; 2, 23, 27, 29 – juntas; 9, 9, 22 - anillos de retención; 4 - cigüeñal; 5 - arandela de seguridad; 6 - nuez; 7 - sello; 8 - primavera; 10 - engranaje; 11, 82 - rodamientos; 12 - cárter; 13 - biela; 14 - enchufe; 15 - anillo raspador de aceite; 16 - pasador de pistón; 17 - anillo de compresión; 18 - pistón; 19 - conjunto de cabezal; 20, 25 - cuadrados atornillados; 21, 26 - nueces; 24 - bloque de cilindros; 28 - placa reflectante; 30, 33, 39 - tornillos; 31 - tapa del cárter; 34 - ajuste; 35 - resorte de la válvula de admisión; 36 - válvula de entrada; 37 - guía de válvula de admisión; 38 - tubería; 40 - junta para tubo con filtro
Signos de mal funcionamiento del compresor: ruidos y golpes, aumento del calentamiento, aumento del contenido de aceite en el condensado, que suele ser consecuencia del desgaste de los aros del pistón y del sello en el extremo trasero del cigüeñal, de los cojinetes de la biela o Tarado del tubo de drenaje de aceite del compresor.
Para retirar el compresor del motor, drene 10 litros de refrigerante del sistema de refrigeración a través del grifo de la caldera del calentador.
Afloje la abrazadera de la manguera y desconecte el tubo de expulsión del amortiguador.
Retire la cubierta del filtro de aire 2, el elemento filtrante 4 y la carcasa del filtro de aire 6.
Desatornille los pernos y las tuercas de unión de la línea de combustible, desconecte las líneas de combustible de la válvula solenoide 7 y las bujías del dispositivo de arranque de la antorcha eléctrica.
Desconecta los cables de la electroválvula y las bujías.
Desatornille los tornillos y retire el tubo de conexión 1 de los colectores de admisión junto con la electroválvula.
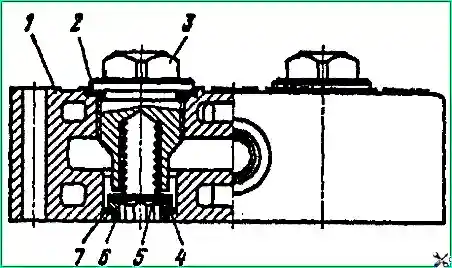
Cierra los orificios de los conductos de aire con tapones de cartón o madera contrachapada.
Desatornille las dos tuercas 13 que sujetan la brida del tubo de suministro de refrigerante al compresor, luego la tuerca de unión 11 y retire el tubo 12.
Retire la brida del tubo y la junta tórica de goma.
Desatornille las tuercas de unión y desconecte del compresor las tuberías que conectan el compresor con el sistema neumático del vehículo y el radiador del sistema de refrigeración del motor.
Desatornille los cuatro tornillos 15 que sujetan el compresor a la tapa del engranaje de distribución 14.
Retire el acoplamiento del tubo 38 (Fig. 3) y mueva el compresor hacia la bomba de combustible hasta que el engranaje 10 salga de la tapa, retire el compresor.
Cierra el agujero de la tapa con un tapón de madera contrachapada o cartón.
Desmontaje del compresor
Doblar el zarcillo de la arandela de seguridad 5, desenroscar la tuerca 6 y, utilizando el extractor “I 801.02.000”, retirar el engranaje 10 del eje 4.
Desatornille los tapones 3 (Fig. 4 ►) de las válvulas de descarga, retire los resortes 5 y las válvulas 4.
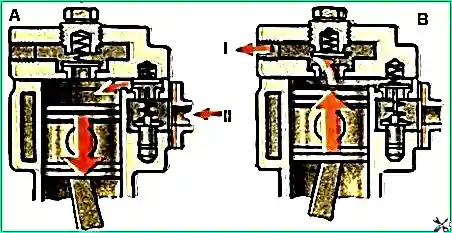
Utilice una llave cuadrada de 10x10 para desatornillar los asientos 6.
Las placas de válvula y los asientos están rectificados entre sí, por lo que no deben despersonalizarse durante las reparaciones.
Desatornille los pernos 39 (ver Fig. 3), retire el tubo 38.
Desatornille las tuercas 21, protegiendo la junta 23 de daños, separe la cabeza 19 del bloque 24, retírela y la junta.
Retire el resorte 35 y la válvula de entrada 36.
Si es necesario, utilice un extractor (Fig. 5) para extraer las guías 37 de las válvulas de admisión (ver Fig. 3).
Desatornille los tornillos 33 y con cuidado, protegiendo la junta 2 de daños, retire la tapa 1 y la junta.
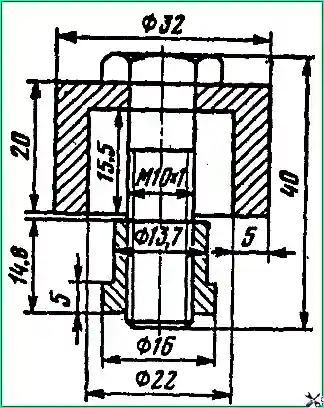
Marcar las bielas y las tapas de biela y sus posiciones relativas.
Destornillar y desenroscar las tuercas de los tornillos de biela, quitar los sombreretes de biela y retirar los pistones 18 ensamblados con bielas.
Instale las tapas de biela en las bielas en la misma posición y fíjelas con los pernos de biela.
Asegure el conjunto de biela con el pistón en un tornillo de banco, retire los anillos del pistón: dos anillos de compresión 17 y un anillo raspador de aceite 15.
Retirar los anillos de bloqueo 22 del pasador del pistón, retirarlo y desconectar la biela del pistón.
Desatornille las tuercas 26 de los espárragos que sujetan el bloque de cilindros 24 al cárter 12.
Retire el bloque 24, la placa reflectante 28 y la junta de sellado 27 de los espárragos.
Retire el anillo de retención 9, el sello 7 y el resorte del sello 8 del extremo trasero del cigüeñal.
Desatornille los tornillos 30 y retire la tapa 31, la junta 29.
Retirar el anillo de retención 3 del extremo trasero del cárter 12, instalar el cárter con su extremo delantero en una prensa y, a través de un espaciador de metal no ferroso “blando”, presionar el eje 4 ensamblado con los cojinetes 11 y 32. fuera del cárter.
Presione el eje para sacarlo de los cojinetes. Si es necesario, retire los pernos del cárter del compresor.
Al reparar la biela y el grupo de pistones, los pistones, anillos y camisas desgastados deben reemplazarse con kits de reparación.
Se reparan los cilindros del bloque y el cigüeñal: los cilindros se perforan y pulen, las muñequillas del cigüeñal se rectifican hasta las dimensiones de reparación (Tabla 1).
Tabla 1.
Cárter del compresor. Diámetro de orificios para cojinetes de cigüeñal:
- - tamaño nominal - 72+0,030 mm;
- - tamaño permitido - 72,05 mm
Bloque de cilindros. Diámetro del cilindro:
- - tamaño nominal - 60+0,030 mm;
- - tamaño permitido - 60,30 mm;
- - primera reparación - 60,4+0,030 mm;
- - segunda reparación - 60,8+0,030 mm
Cigüeñal. Diámetro del cuello:
- - cojinetes principales - tamaño nominal - 35+0,020 mm; tamaño permitido - 35,00 mm;
- - biela para rodamientos - tamaño nominal - 28,5-0,021 mm; primera reparación: 28,2-0,021 mm; segunda reparación - 27,9-0,021;
- - para el engranaje impulsor - tamaño nominal - 35+0,020 mm; aceptable - 35,00
Conjunto de biela con un ojito. Diámetro de los agujeros para el casquillo del pasador:
- - tamaño nominal - 14+0,019 mm;
- - tamaño permitido - 14,05 mm
Inserciones. Grosor de la pared:
- - tamaño nominal: 1,75-0,013 mm;
- - primera reparación - 1,90-0,013 mm;
- - segunda reparación - 2,05-0,013
Pistón. Diámetro exterior:
- - cabezas - tamaño nominal - 59,8-0,095 mm; primera reparación: 60,2-0,095 mm; segunda reparación - 60,6-0,095 mm;
- - faldas - tamaño nominal - 59,9-0,030 mm; primera reparación - 60,3-0,030 mm; segunda reparación - 60,7-0,030 mm
Anillo de compresión:
- El espacio en la junta cuando se instala en un calibre - tamaño nominal - 0,200-0,400 mm; primera reparación - 0,200-0,400 mm; segunda reparación - 0,200-0,400 mm;
- Diámetro del calibre - tamaño nominal - 60.000 mm; primera reparación - 60.400 mm; segunda reparación - 60.800
Anillo rascador de aceite:
- El espacio en la junta cuando se instala en un calibre - tamaño nominal - 0,200-0,400 mm; primera reparación - 0,200-0,400 mm; segunda reparación - 0,200-0,400 mm;
- Diámetro del calibre - tamaño nominal - 60,00 mm; primera reparación - 60.400 mm; segunda reparación - 60.800 mm
Al ensamblar piezas del grupo de pistones recién instaladas, los pistones, bielas y pasadores deben seleccionarse según los grupos (Tabla 2).
Tabla 2.
Primer grupo:
- - diámetro del dedo - 12.500-12.497 mm;
- - diámetro del orificio del pistón - 12 500-1 2 497 mm;
- - diámetro del orificio en el casquillo de la biela - 12,507-12,504 mm;
- - color de marcado - Blanco
Segundo grupo:
- - diámetro del dedo - 12,497-12,494 mm;
- - diámetro del orificio en el pistón - 12,497-12,494 mm;
- - diámetro del orificio en el casquillo de la biela - 12,504-12,501 mm;
- - color de marcado - Verde
Tercer grupo:
- - diámetro del dedo - 12,494-12,491 mm;
- - diámetro del orificio en el pistón - 12,494-12,491 mm;
- - diámetro del orificio en el casquillo de la biela - 12,50 1-12,498 mm;
- - color de marcado - Azul
Cuarto grupo:
- - diámetro del dedo - 12,491-12,488 mm;
- - diámetro del orificio en el pistón - 12,491-12,488 mm;
- - diámetro del orificio en el casquillo de la biela - 12,498-12,495 mm;
- - color de marcado - Rojo
Las piezas del primer y segundo tamaño de reparación están marcadas:
Los números + 0,4 y + 0,8 están estampados en la parte inferior de los pistones, los números - 0,3 y - 0,6 en la parte posterior (acero) de las camisas, una o dos franjas de ancho están aplicadas a los anillos en la generatriz con pintura verde 10 mm.
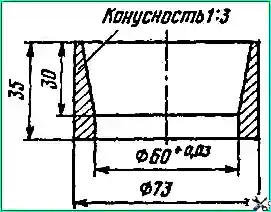
Antes del montaje, comprobar la estanqueidad del bloque de cilindros y del cabezal del compresor con aire comprimido a una presión de 15 kgf/cm 2 con inmersión en agua, para comprobar la ausencia de melladuras y deformaciones de los planos de separación.
La deformación de los planos del conector (0,040 mm) se controla mediante una regla de medición y una galga de espesores.
Una sonda de 0,05 mm de espesor no debe pasar por debajo de una regla instalada en el plano del conector.
Compruebe que la biela no esté doblada ni torcida utilizando un dispositivo especial. El no paralelismo de los ejes superior e inferior (las cabezas de las bielas se permiten 0,070 mm en una longitud de 100 mm, su torsión es de 0,100 mm en una longitud de 100 mm.
Monte el compresor en orden inverso al desmontaje. En este caso, es necesario cumplir una serie de los siguientes requisitos obligatorios:
- - lubricar generosamente las partes de la biela y del grupo de pistones con el aceite utilizado para lubricar el motor según la tabla de lubricación;
- - instale los anillos de compresión en el pistón con la ranura hacia arriba (hacia la parte inferior del pistón).
- - antes de instalar los pistones en el cilindro, separe las juntas de los anillos en un ángulo de 120˚. Instale los pistones en el cilindro usando un mandril (Fig. 6);
- - el par de apriete de las tuercas de los pernos de la biela debe ser de 1,5 a 4,7 kgf/m. No está permitido aflojar la tuerca para instalar la chaveta;
- - apriete el cabezal del bloque del compresor en dos pasos, el par de apriete final es de 1,2-1,7 kgcm;
- - al instalar el sello, inserte los extremos del resorte en los orificios del cigüeñal y el sello.
Instale el compresor reparado en el automóvil en el orden inverso al desmontaje.
También miramos el artículo sobre el compresor - “Reparación del compresor de un vehículo Kamaz”