A medida que el compresor funciona, el grupo cilindro-pistón se desgasta y la estanqueidad de las válvulas se ve comprometida
En caso de estas averías, el tiempo de llenado del sistema neumático (antes de apagar los testigos) a un régimen del motor de 2200 rpm supera el establecido por las especificaciones técnicas, es decir 8 minutos, o el compresor no desarrolla el rendimiento especificado. presión total, 7-7,5 kgf /cm 2
Además, el desgaste del grupo cilindro-pistón provoca la absorción de la niebla de aceite del cárter del compresor hacia los cilindros, y luego el aceite junto con el aire pasa al sistema neumático.
Después de llenar el sistema neumático con aire, la válvula de descarga se abre en el regulador de presión, el aceite junto con el aire es expulsado y se deposita en el regulador y el marco.
Cabe señalar aquí que el consumo de aceite a través del compresor aumenta debido a la contaminación del filtro de aire del motor.
El hecho es que el compresor aspira aire filtrado del colector de admisión del motor.
A medida que el filtro se ensucia, el vacío en el colector de admisión aumenta y el compresor, incluso con un grupo de pistones en funcionamiento, aspira la neblina de aceite del cárter y luego la arroja al accionamiento neumático durante la carrera de escape.
Las fugas en la junta de culata 18 y las grietas internas en la culata o en el bloque provocan que el líquido del sistema de refrigeración sea aspirado hacia los cilindros y luego, junto con el aire, pase al accionamiento neumático.
El nivel de refrigerante en el tanque de expansión baja y el líquido que contiene burbujea.
Esto sucede porque el pistón durante la carrera de compresión empuja aire hacia la camisa de enfriamiento del compresor y luego el aire y el líquido se fusionan en el tanque de expansión.
Existe otra consecuencia peligrosa del mal funcionamiento considerado.
El líquido que ha entrado en el cilindro del compresor se filtra en el cárter del compresor a través de los espacios entre el cilindro, el pistón y los anillos, y desde allí fluye hacia el cárter de aceite del motor.
Si entra líquido en el aceite, a la hora de buscar una fuga, también hay que tener en cuenta el compresor.
De lo contrario, debido a un compresor defectuoso, un motor en buen estado puede enviarse por error a reparación y el compresor defectuoso puede reinstalarse en otro motor en buen estado.
El aceite para lubricar el compresor se suministra desde el canal de aceite central del motor al sello mecánico 4 instalado en el cigüeñal.
La junta se presiona contra la carcasa del volante mediante el resorte 5.
Si el sello mecánico está muy desgastado, así como el resorte está roto, el aceite, sin pasar por el compresor, fluye directamente hacia el bloque de distribución y luego hacia el cárter del motor.
Este mal funcionamiento puede causar fallas no solo en el compresor (ataque debido a la falta de lubricación), sino también en el motor (arranque de las camisas del cigüeñal debido a la falta de aceite).
La apertura incompleta de las válvulas de escape provoca el sobrecalentamiento del aire en la salida del compresor.
Desmontaje del compresor
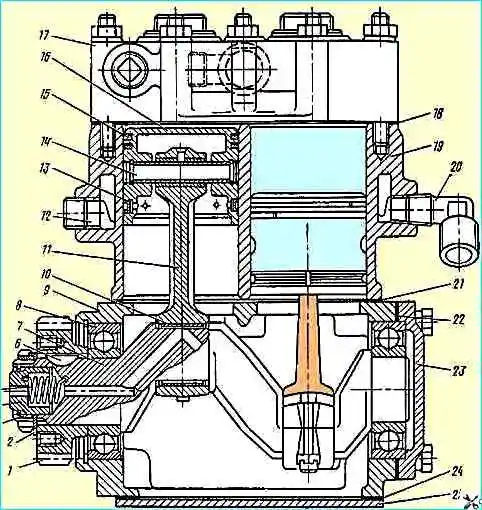
El desmontaje del compresor montado en el soporte comienza con la extracción de la culata. Luego se retiran las válvulas de admisión, sus guías y asientos de los casquillos del bloque de cilindros.
Sujetando la cabeza del bloque en un tornillo de banco, desenrosque los tapones de las válvulas de inyección, retire las válvulas, los asientos y las juntas de estanqueidad.
Doblando el zarcillo de la arandela de seguridad 2 y desenroscando la tuerca 3 que sujeta el engranaje impulsor del cigüeñal, retire la arandela de seguridad.
Luego, mediante un dispositivo, se retira el engranaje impulsor del compresor y se retira la chaveta 6 de la ranura del cigüeñal.
Para quitar el sello mecánico y el resorte del cigüeñal, primero debe quitar el anillo de empuje del cigüeñal.
Girando el compresor sobre el soporte con la tapa inferior hacia arriba, desenrosque los tornillos de fijación y retire la tapa inferior con la junta 24.
Luego debe desenroscar y desenroscar la tuerca que sujeta las tapas de las bielas y retirar las tapas.
Golpeando el extremo de la cabeza inferior de la biela con el mango de un martillo, retire el pistón con la biela.
Después de quitar los revestimientos, debe conectar las cubiertas y las bielas en pares con pernos para no confundirlas en el futuro. Biela con a La tapa se procesa como un conjunto, por lo que solo se reemplazan en pares.
Girando el compresor con el bloque de cilindros hacia arriba, desenrosque las tuercas que sujetan el bloque al cárter y retire el bloque de cilindros con las 21 placas deflectoras de aceite.
Después de esto, desatornille los tornillos que sujetan la tapa del cárter trasero 23 y retire la tapa.
Antes de sacar el cigüeñal del cárter a presión, se retira el anillo de empuje del cojinete principal instalado en el lado del engranaje impulsor.
Sosteniendo la biela en un tornillo de banco, retire los anillos de aceite de compresión del pistón y retire el anillo de empuje del pasador del pistón.
Después de presionar hacia afuera el pasador del pistón 14, desconecte el pistón de la biela y luego presione hacia afuera el casquillo de la cabeza superior de la biela.
Defectos de las piezas del compresor
Si se detectan defectos, las piezas con grietas, astillas, rebabas, rayones en las superficies de trabajo y otros daños mecánicos están sujetas a rechazo.
Tabla 1:
Tamaño - Diámetro del cilindro, mm - Marcado
- Nominal - 60+0,03 - 0;
- Primera reparación - 60,4+0,03 - +0,4;
- Segunda reparación - 60,8+0,03 - +0,8
Si la superficie interior de los cilindros está desgastada en más de 0,02 mm, es necesario perforar los cilindros hasta el tamaño de reparación (Tabla 1).
El diámetro del asiento debajo del asiento de la válvula de admisión no debe exceder los 17,027 mm.
El diámetro de los rodamientos de bolas en el cárter del compresor no debe ser superior a 72,05 mm.
Con un diámetro mayor, no se garantiza un ajuste de interferencia del rodamiento.
La falta de planitud de la superficie de contacto del cabezal del compresor con el bloque de cilindros no debe ser superior a 0,1 mm.
Los riesgos y rastros de desgaste en la superficie de los asientos de las válvulas de descarga se eliminan mediante el rectificado y lapeado de las válvulas.
El diámetro del orificio para instalar la válvula de descarga no debe ser superior a 28,8 mm.
Tabla 2:
Tamaño - Diámetro de los muñones de biela, mm - Marcado
- Nominal - 28,5-0,021 - 0;
- Primera reparación - 28,2-0,021 - -0,3;
- Segunda reparación - 27,9-0,021 - -0,6
El diámetro del cigüeñal para rodamientos de bolas y engranajes debe ser de al menos 35 mm, para el sello mecánico no más de 25,05 mm y el ancho del chavetero no más de 5,02 mm.
Cuando los muñones de la biela se desgastan, se deben rectificar hasta el siguiente tamaño de reparación (tabla).
Tabla 3:
Grupo - Diámetro del orificio para pasador en casquillo, mm - Color de marcado
- I - 12.507-12.504 - blanco;
- II - 12.504-12.501 - verde;
- III - 12.501-12.498 - azul;
- IV - 12.498-12.496 - rojo
El no paralelismo de los ejes de los orificios en las cabezas superior e inferior de la biela (flexión) en una longitud de 100 mm no debe ser superior a 0,1 mm.
La desviación de los ejes de los orificios de los cabezales superior e inferior (giro) en una longitud de 100 mm no debe ser superior a 0,15 mm.
El diámetro de la cabeza inferior de la biela no debe ser superior a 32,02 mm, y el diámetro del casquillo de la cabeza superior no debe ser superior a 12,507 mm.
Si el casquillo superior del cabezal está flojo, se debe reemplazar.
Al reemplazar el casquillo, debe perforar un orificio de lubricación y girar el casquillo al tamaño nominal.
Las bielas se dividen en grupos a intervalos de 0,003 mm según el diámetro del orificio más pequeño y están marcadas con pintura (tabla).
Tabla 4
Tamaño - Diámetro del pistón en la falda, mm - Diámetro del pistón en la parte inferior, mm - marcado:
- Nominal - 59,9-0,03 - 59,8-0,03 -;
- Primera reparación - 60,3-0,03 - 60,2-0,095 - +0,4;
- Segunda reparación - 60,7-0,06 - 60,6-0,195 - +0,8
La altura del tapón de la válvula de descarga debe ser de al menos 31,1 mm.
El diámetro del asiento del sello no es inferior a 24,94 mm.
Para el engranaje impulsor del compresor, el espesor de los dientes a lo largo de la cuerda del círculo primitivo debe ser de al menos 4,2 mm y a lo largo del ancho del chavetero no más de 5,15 mm.
Tabla 5
Grupo - Diámetro del orificio para el pasador en el casquillo del pistón (diámetro del pasador) - color de marcado:
- I - 12.500-12.497 - blanco;
- II - 12,497-12,494 - verde;
- III - 12,494-12,491 - azul;
- IV - 12,491-12,488 - rojo
El desgaste del pistón en la parte inferior y en el faldón no está permitido en más de 0,015 mm del tamaño nominal o de reparación (Tabla 5).
Los pistones del tamaño de reparación están marcados en la superficie exterior de la parte inferior.
El diámetro del orificio en el saliente del pistón para el pasador no debe superar los 12,5 mm.
Según el diámetro del orificio del casquillo, los pistones se dividen en grupos cada 0,003 mm (Tabla 6).
El diámetro del pasador del pistón debe ser de al menos 12,488 mm. Los dedos se clasifican en grupos según su diámetro.
Las dimensiones y marcas en grupos corresponden a los tamaños y marcas de los pistones (ver Tabla 6).
No se permite el desgaste del revestimiento en más de 0,01 mm respecto al tamaño nominal o de reparación (Tabla 7).
Tabla 6
Tamaño - Espesor, mm - Marcado:
- Nominal - 1,75-0,013 -;
- Primera reparación - 1,90-0,013 - -0,3;
- Segunda reparación - 2,0,5-0,013 - -0,6
Al realizar la verificación, los anillos de pistón se instalan en calibres de anillo.
El espacio en la cerradura del anillo de pistón instalado en el calibre debe estar entre 0,2 y 0,6 mm.
Los kits de reparación de anillos están marcados con pintura verde, los diámetros de los calibres para comprobar los anillos se muestran en la tabla.
Tabla 7
Tamaño - Diámetro del calibre, mm - Marcas del anillo:
- Nominal - 60 - no marcado;
- Primera reparación - 60.4 - Una tira de 10 mm de ancho;
- Segunda reparación - 60.8 - Dos tiras de 10 mm de ancho
Conjunto del compresor
Antes de montar el compresor, es necesario seleccionar:
- - en grupos, pasadores de pistón a pistones y bielas con casquillos presionados en ellas;
- - según las dimensiones de reparación de pistones a cilindros;
- - según las dimensiones de reparación, anillos de pistón a pistones;
- - según las dimensiones de reparación de las camisas del cigüeñal. Al presionar el casquillo en la cabeza superior de la biela, debe asegurarse de que el orificio del casquillo coincida con el canal de aceite de la biela.
El pasador del pistón debe coincidir con los orificios de los resaltes del pistón con una separación de 0,003 mm y entrar en los orificios del pistón bajo la acción de ligeros golpes de martillo.
El espacio en la interfaz entre el pasador del pistón y el casquillo de la biela debe estar en el rango de 0,004-0,010 mm. El dedo debe encajar firmemente en el orificio de la funda utilizando la fuerza de la mano.
Después de haber lubricado previamente las superficies de fricción con aceite de motor, debe instalar la biela en el pistón y, alineando los orificios, presionar el pasador del pistón. El pasador se fija en el pistón mediante anillos de empuje.
Luego se instalan anillos en el pistón.
Los anillos de compresión se instalan en el pistón con una ranura escalonada hacia arriba, las juntas de los anillos adyacentes deben dirigirse en direcciones opuestas.
El espacio entre el anillo y la ranura debe ser de 0,035-0,09 mm.
A continuación debe ensamblar el cabezal del compresor. Para hacer esto, instale las juntas de los asientos de la válvula de descarga en la cabeza, atornille los asientos de las válvulas, inserte las válvulas de descarga, los resortes y las juntas de los tapones, y atornille los tapones de las válvulas de descarga.
El conjunto del cigüeñal con cojinetes se instala en el cárter del compresor hasta que tope contra el anillo.
Luego se instala una chaveta en la ranura del cigüeñal, se monta un engranaje en el eje y una chaveta, que se fija al eje con una tuerca y una arandela de seguridad.
El resorte y el sello instalados en el cigüeñal están asegurados con un anillo de empuje.
Después de instalar el sello, debe verificar su movilidad: cuando presione el extremo con el dedo, el sello debe moverse libremente.
Habiendo instalado el cárter del compresor en el soporte y seleccionado un juego de juntas 22, fije la cubierta trasera al cárter.
Luego, instalando la placa reflectora 21 en el cárter, fije el bloque de cilindros al mismo.
Girando el bloque de cilindros con el conjunto del cárter sobre el soporte con el cárter hacia arriba, sople aire comprimido a través de los cilindros y el cigüeñal.
Instale camisas del mismo tamaño de reparación que los muñones del cigüeñal en la biela y en la cubierta de la biela.
Habiendo lubricado previamente las superficies de los cilindros, pistones y muñequillas del cigüeñal con aceite de motor, instale los conjuntos de pistones y bielas en los cilindros.
Luego instale los conjuntos de cubiertas con revestimientos en los muñones del cigüeñal y apriete las tuercas de fijación con un par de 1,6-1,8 kgm, asegure las tuercas.
Luego verifique la facilidad de rotación del cigüeñal. El par de giro no debe exceder los 0,8 kgf m. Después de haber lubricado previamente los planos de contacto con esmalte nitro, fije la tapa inferior con una junta al cárter.
Habiendo presionado los asientos de las válvulas de admisión en el bloque de cilindros, instale las guías y las válvulas.
Después de instalar los resortes de la válvula de admisión y la junta 18, fije la culata al bloque de cilindros. Apriete las tuercas de fijación del cabezal uniformemente en dos pasos.
El par de apriete final de las tuercas debe ser de 1,2-1,6 kgm.