Während der Kompressor läuft, verschleißt die Zylinder-Kolben-Gruppe und die Dichtheit der Ventile wird beeinträchtigt
Im Falle dieser Störungen überschreitet die Füllzeit des pneumatischen Systems (vor dem Erlöschen der Warnleuchten) bei einer Motordrehzahl von 2200 U/min die in den technischen Spezifikationen festgelegte Zeit, d. h. 8 Minuten, oder der Kompressor entwickelt nicht die angegebene Leistung Druck überhaupt, 7–7,5 kgf/cm 2
Darüber hinaus führt der Verschleiß der Zylinder-Kolben-Gruppe dazu, dass Ölnebel aus dem Kurbelgehäuse des Kompressors in die Zylinder aufgenommen wird und das Öl dann zusammen mit der Luft in das Pneumatiksystem gelangt.
Nachdem das pneumatische System mit Luft gefüllt ist, öffnet sich das Entlastungsventil im Druckregler, das Öl wird zusammen mit der Luft herausgeschleudert und setzt sich auf dem Regler und dem Rahmen ab.
Hier ist zu beachten, dass der Ölverbrauch durch den Kompressor aufgrund der Verschmutzung des Motorluftfilters steigt.
Tatsache ist, dass der Kompressor gefilterte Luft aus dem Ansaugkrümmer des Motors ansaugt.
Wenn der Filter verschmutzt, erhöht sich der Unterdruck im Ansaugkrümmer und der Kompressor saugt auch bei laufender Kolbengruppe Ölnebel aus dem Kurbelgehäuse an und wirft ihn dann beim Ausstoßhub in den pneumatischen Antrieb.
Lecks in der Zylinderkopfdichtung 18, innere Risse im Kopf oder Block führen dazu, dass Flüssigkeit aus dem Kühlsystem in die Zylinder gesaugt wird und dann zusammen mit Luft in den pneumatischen Antrieb gelangt.
Der Kühlmittelstand im Ausgleichsbehälter sinkt und die Flüssigkeit darin bildet Blasen.
Dies geschieht, weil der Kolben während des Kompressionshubs Luft in den Kühlmantel des Kompressors drückt, und dann verschmelzen Luft und Flüssigkeit im Ausgleichsbehälter.
Es gibt noch eine weitere gefährliche Folge der betrachteten Fehlfunktionen.
Die Flüssigkeit, die in den Kompressorzylinder gelangt ist, sickert durch die Spalte zwischen Zylinder, Kolben und Ringen in das Kurbelgehäuse des Kompressors und fließt von dort in die Ölwanne des Motors.
Wenn Flüssigkeit in das Öl gelangt, müssen Sie bei der Suche nach einem Leck auch den Kompressor im Auge behalten.
Andernfalls kann es aufgrund eines defekten Kompressors dazu kommen, dass fälschlicherweise ein funktionsfähiger Motor zur Reparatur geschickt wird und der defekte Kompressor möglicherweise in einen anderen wartungsfähigen Motor eingebaut wird.
Öl zur Schmierung des Kompressors wird vom zentralen Ölkanal des Motors zur in der Kurbelwelle eingebauten Gleitringdichtung 4 zugeführt.
Die Dichtung wird durch die Feder 5 an das Schwungradgehäuse gedrückt.
Wenn die mechanische Dichtung stark abgenutzt ist und die Feder gebrochen ist, fließt das Öl unter Umgehung des Kompressors direkt auf den Steuerblock und dann in die Motorwanne.
Diese Fehlfunktion kann nicht nur zum Ausfall des Kompressors (Festfressen aufgrund mangelnder Schmierung), sondern auch des Motors (Durchdrehen der Kurbelwellenbüchsen aufgrund von Ölmangel) führen.
Unvollständiges Öffnen der Auslassventile führt zu einer Überhitzung der Luft am Kompressorausgang.
Kompressor zerlegen
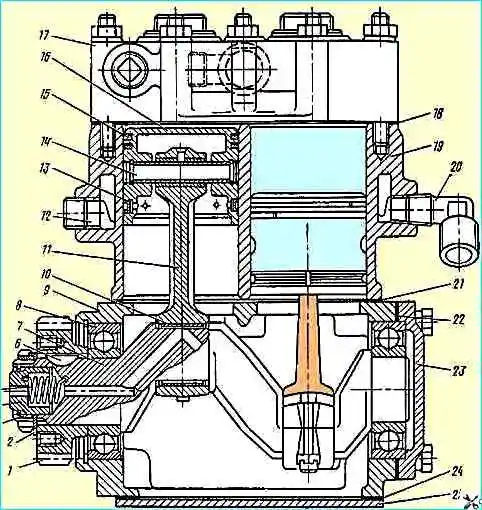
Die Demontage des auf dem Ständer montierten Kompressors beginnt mit dem Ausbau des Zylinderkopfes. Anschließend werden die Einlassventile, ihre Führungen und Sitze aus den Zylinderblocksockeln entfernt.
Halten Sie den Blockkopf in einen Schraubstock, schrauben Sie die Stopfen des Einspritzventils ab, entfernen Sie die Ventile, Sitze und Dichtungen.
Biegen Sie die Schlinge der Sicherungsscheibe 2 und lösen Sie die Mutter 3, mit der das Kurbelwellenantriebsrad befestigt ist, und entfernen Sie die Sicherungsscheibe.
Dann wird mit einer Vorrichtung das Antriebsrad des Kompressors entfernt und die Passfeder 6 aus der Nut der Kurbelwelle entfernt.
Um die Gleitringdichtung und die Feder von der Kurbelwelle zu entfernen, müssen Sie zuerst den Druckring von der Kurbelwelle entfernen.
Drehen Sie den Kompressor mit der unteren Abdeckung nach oben auf dem Ständer, lösen Sie die Befestigungsschrauben und entfernen Sie die untere Abdeckung mit der Dichtung 24.
Dann müssen Sie die Mutter lösen, mit der die Pleuelstangenabdeckungen befestigt sind, und die Abdeckungen entfernen.
Durch Klopfen mit dem Griff eines Hammers auf das Ende des unteren Kopfes der Pleuelstange entfernen Sie den Kolben mit der Pleuelstange.
Nachdem Sie die Laufbuchsen entfernt haben, müssen Sie die Abdeckungen und Pleuel paarweise mit Schrauben verbinden, um sie in Zukunft nicht zu verwechseln. Pleuel mit zu Der Deckel wird als Baugruppe verarbeitet und kann daher nur paarweise ausgetauscht werden.
Drehen Sie den Kompressor mit dem Zylinderblock nach oben, lösen Sie die Muttern, mit denen der Block am Kurbelgehäuse befestigt ist, und entfernen Sie den Zylinderblock mit den 21 Ölabweiserplatten.
Danach lösen Sie die Schrauben, mit denen die hintere Kurbelgehäuseabdeckung 23 befestigt ist, und entfernen Sie die Abdeckung.
Bevor die Kurbelwelle aus dem Kurbelgehäuse gedrückt wird, wird der Anlaufring des auf der Antriebsradseite montierten Hauptlagers entfernt.
Halten Sie die Pleuelstange in einen Schraubstock, entfernen Sie die Kompressionsölringe vom Kolben und entfernen Sie den Druckring des Kolbenbolzens.
Nachdem Sie den Kolbenbolzen 14 herausgedrückt haben, trennen Sie den Kolben von der Pleuelstange und drücken Sie dann die Buchse aus dem oberen Kopf der Pleuelstange heraus.
Defekte von Kompressorteilen
Wenn Mängel festgestellt werden, werden Teile mit Rissen, Spänen, Graten, Kratzern auf den Arbeitsflächen und anderen mechanischen Schäden zurückgewiesen.
Tabelle 1:
Größe – Zylinderdurchmesser, mm – Markierung
- Nominal – 60+0,03 – 0;
- Erste Reparatur – 60,4+0,03 – +0,4;
- Zweite Reparatur – 60,8+0,03 – +0,8
Wenn die Innenfläche der Zylinder mehr als 0,02 mm abgenutzt ist, müssen die Zylinder auf das Reparaturmaß aufgebohrt werden (Tabelle 1).
Der Sitzdurchmesser unter dem Einlassventilsitz darf 17,027 mm nicht überschreiten.
Der Durchmesser der Kugellager im Kompressorkurbelgehäuse darf nicht mehr als 72,05 mm betragen.
Bei einem größeren Durchmesser ist ein Presssitz des Lagers nicht gewährleistet.
Die Unebenheit der Kontaktfläche des Kompressorkopfes zum Zylinderblock sollte nicht mehr als 0,1 mm betragen.
Risiken und Verschleißspuren an der Oberfläche der Auslassventilsitze werden durch Schleifen und Läppen der Ventile beseitigt.
Der Durchmesser des Lochs für den Einbau des Auslassventils darf nicht mehr als 28,8 mm betragen.
Tabelle 2:
Größe – Durchmesser der Pleuellagerzapfen, mm – Markierung
- Nominal - 28,5-0,021 - 0;
- Erste Reparatur – 28,2-0,021 – -0,3;
- Zweite Reparatur – 27,9-0,021 – -0,6
Der Durchmesser der Kurbelwelle für Kugellager und Zahnräder muss mindestens 35 mm, für die Gleitringdichtung nicht mehr als 25,05 mm und die Breite der Keilnut nicht mehr als 5,02 mm betragen.
Bei Verschleiß der Pleuelzapfen müssen diese auf das nächste Reparaturmaß (Tabelle) geschliffen werden.
Tabelle 3:
Gruppe – Durchmesser des Lochs für Stift in der Buchse, mm – Markierungsfarbe
- I – 12.507-12.504 – weiß;
- II – 12.504-12.501 – grün;
- III - 12.501-12.498 - blau;
- IV – 12.498-12.496 – rot
Die Nichtparallelität der Achsen der Löcher im oberen und unteren Kopf der Pleuelstange (Biegung) auf einer Länge von 100 mm sollte nicht mehr als 0,1 mm betragen.
Der Versatz der Lochachsen der oberen und unteren Köpfe (Verdrehung) auf einer Länge von 100 mm sollte nicht mehr als 0,15 mm betragen.
Der Durchmesser des unteren Kopfes der Pleuelstange darf nicht mehr als 32,02 mm betragen, und der Durchmesser der Buchse des oberen Kopfes darf nicht mehr als 12,507 mm betragen.
Wenn die obere Kopfbuchse locker ist, muss sie ersetzt werden.
Beim Austausch der Buchse müssen Sie ein Schmierloch bohren und die Buchse auf die Nenngröße drehen.
Pleuelstangen werden entsprechend dem kleineren Lochdurchmesser im Abstand von 0,003 mm in Gruppen eingeteilt und mit Farbe gekennzeichnet (Tabelle).
Tabelle 4
Größe – Kolbendurchmesser am Schaft, mm – Kolbendurchmesser am Boden, mm – Markierung:
- Nominal - 59,9-0,03 - 59,8-0,03 -;
- Erste Reparatur – 60,3–0,03 – 60,2–0,095 – +0,4;
- Zweite Reparatur – 60,7–0,06 – 60,6–0,195 – +0,8
Die Höhe des Auslassventilstopfens muss mindestens 31,1 mm betragen.
Der Sitzdurchmesser der Dichtung beträgt nicht weniger als 24,94 mm.
Beim Kompressorantriebsrad muss die Zahndicke entlang der Sehne des Teilkreises mindestens 4,2 mm und entlang der Breite der Keilnut nicht mehr als 5,15 mm betragen.
Tabelle 5
Gruppe – Durchmesser des Lochs für den Stift in der Kolbennabe (Stiftdurchmesser) – Markierungsfarbe:
- I – 12.500-12.497 – weiß;
- II – 12.497-12.494 – grün;
- III – 12.494-12.491 – blau;
- IV – 12.491-12.488 – rot
Der Kolbenverschleiß am Boden und am Kolben darf nicht mehr als 0,015 mm vom Nenn- oder Reparaturmaß abweichen (Tabelle 5).
Die Reparaturkolbengröße ist auf der Außenfläche des Bodens markiert.
Der Durchmesser des Lochs in der Kolbennabe für den Bolzen darf nicht mehr als 12,5 mm betragen.
Entsprechend dem Durchmesser des Lochs in der Nabe werden die Kolben alle 0,003 mm in Gruppen eingeteilt (Tabelle 6).
Der Durchmesser des Kolbenbolzens muss mindestens 12,488 mm betragen. Die Finger werden nach Durchmesser in Gruppen sortiert.
Abmessungen und Markierungen in Gruppen entsprechen den Größen und Markierungen für Kolben (siehe Tabelle 6).
Eine Abnutzung der Auskleidung um mehr als 0,01 mm vom Nenn- oder Reparaturmaß (Tabelle 7) ist nicht zulässig.
Tabelle 6
Größe – Dicke, mm – Markierung:
- Nominal - 1,75-0,013 -;
- Erste Reparatur - 1,90-0,013 - -0,3;
- Zweite Reparatur – 2,0,5-0,013 - -0,6
Bei der Prüfung werden Kolbenringe in Lehrringe eingebaut.
Der Spalt in der Verriegelung des im Kaliber eingebauten Kolbenrings muss zwischen 0,2 und 0,6 mm liegen.
Ringreparatursätze sind mit grüner Farbe gekennzeichnet; die Durchmesser der Lehren zur Prüfung der Ringe sind in der Tabelle aufgeführt.
Tabelle 7
Größe – Kaliberdurchmesser, mm – Ringmarkierungen:
- Nominal – 60 – nicht markiert;
- Erste Reparatur – 60,4 – Ein Streifen 10 mm breit;
- Zweite Reparatur – 60,8 – Zwei Streifen 10 mm breit
Kompressorbaugruppe
Bevor Sie den Kompressor zusammenbauen, müssen Sie Folgendes auswählen:
- - in Gruppen, Kolbenbolzen zu Kolben und Pleuelstangen mit eingepressten Buchsen;
- - entsprechend den Reparaturmaßen von Kolben zu Zylinder;
- - entsprechend den Reparaturmaßen, Kolbenringe zu Kolben;
- - entsprechend den Reparaturmaßen der Kurbelwellenlaufbuchsen. Beim Einpressen der Buchse in den oberen Pleuelkopf ist darauf zu achten, dass das Loch in der Buchse mit dem Ölkanal im Pleuel übereinstimmt.
Der Kolbenbolzen muss mit einem Spalt von 0,003 mm auf die Löcher in den Kolbennaben abgestimmt sein und unter Einwirkung leichter Hammerschläge in die Kolbenlöcher eindringen.
Der Spalt in der Schnittstelle zwischen Kolbenbolzen und Pleuelbuchse sollte im Bereich von 0,004–0,010 mm liegen. Der Finger sollte mit Handkraft fest in das Loch der Hülse passen.
Nachdem Sie die Reibflächen zuvor mit Motoröl geschmiert haben, müssen Sie die Pleuelstange in den Kolben einbauen und den Kolbenbolzen unter Ausrichtung der Löcher hineindrücken. Der Bolzen wird durch Anlaufringe im Kolben fixiert.
Ringe werden dann am Kolben angebracht.
Kompressionsringe werden mit einer abgestuften Nut nach oben am Kolben montiert, die Verbindungen benachbarter Ringe sollten in entgegengesetzte Richtungen gerichtet sein.
Der Spalt zwischen Ring und Nut sollte 0,035–0,09 mm betragen.
Als nächstes sollten Sie den Kompressorkopf zusammenbauen. Dazu die Sitzdichtungen des Auslassventils in den Kopf einbauen, Ventilsitze einschrauben, Auslassventile, Federn und Stopfendichtungen einsetzen, Auslassventilstopfen einschrauben.
Die Kurbelwellenbaugruppe mit Lagern wird bis zum Anschlag am Ring in das Kurbelgehäuse des Kompressors eingebaut.
Dann wird eine Passfeder in die Nut der Kurbelwelle eingebaut, ein Zahnrad wird auf die Welle montiert und die Passfeder wird mit einer Mutter und einer Sicherungsscheibe auf der Welle befestigt.
Die in der Kurbelwelle eingebaute Feder und Dichtung wird mit einem Anlaufring gesichert.
Nach dem Einbau der Dichtung müssen Sie deren Beweglichkeit prüfen: Wenn Sie mit dem Finger auf das Ende drücken, sollte sich die Dichtung frei bewegen.
Nachdem Sie das Kurbelgehäuse des Kompressors auf dem Ständer installiert und einen Satz Dichtungen 22 ausgewählt haben, befestigen Sie die hintere Abdeckung am Kurbelgehäuse.
Dann installieren Sie den Plattenreflektor 21 am Kurbelgehäuse und befestigen den Zylinderblock daran.
Drehen Sie den Zylinderblock mit der Kurbelgehäusebaugruppe auf dem Ständer mit dem Kurbelgehäuse nach oben und blasen Sie Druckluft durch die Zylinder und die Kurbelwelle.
Montieren Sie Laufbuchsen mit derselben Reparaturgröße wie die Kurbelwellenzapfen auf der Pleuelstange und in der Pleuelstangenabdeckung.
Nachdem Sie zuvor die Oberflächen der Zylinder, Kolben und Kurbelzapfen der Kurbelwelle mit Motoröl geschmiert haben, bauen Sie die Kolben- und Pleuelstangenbaugruppen in die Zylinder ein.
Dann montieren Sie die Abdeckungsbaugruppen mit Laufbuchsen auf den Kurbelwellenzapfen und ziehen Sie die Befestigungsmuttern mit einem Drehmoment von 1,6–1,8 kgm fest. Sichern Sie die Muttern.
Überprüfen Sie anschließend die Leichtgängigkeit der Kurbelwelle. Das Drehmoment sollte 0,8 kgf·m nicht überschreiten. Nachdem Sie die Kontaktflächen zuvor mit Nitrolack geschmiert haben, befestigen Sie die untere Abdeckung mit einer Dichtung am Kurbelgehäuse.
Nachdem Sie die Einlassventilsitze in den Zylinderblock gedrückt haben, installieren Sie die Führungen und Ventile.
Befestigen Sie nach dem Einbau der Einlassventilfedern und der Dichtung 18 den Kopf am Zylinderblock. Ziehen Sie die Kopfbefestigungsmuttern gleichmäßig in zwei Schritten an.
Das endgültige Anzugsdrehmoment der Muttern sollte 1,2–1,6 kgm betragen.