All regulator parts must be clean before assembly, and the rubbing surfaces must be lubricated with engine oil
The presence of traces of corrosion and dirt on the surface of the parts and wiping them with a wiping material is not allowed.
At the beginning of the assembly, the thrust washer must be pressed until it stops.
When the camshaft of the pump rotates, the thrust washer must not touch the bearing cup.
When assembling weights with a hub, the ends of the weight axles must be flared.
The protrusion of the flared part of the axles must be no more than 0.5 mm.
The weights must swing freely on their axles.
Jamming and seizures are not allowed. At the ends of the weight axis, 1 - 2 metal breaks from flaring are allowed.
Only weights of one group are allowed to be installed in the regulator.
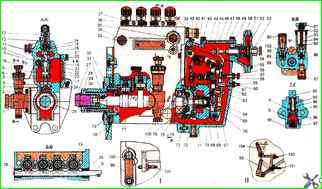
The belonging of the weights to the first or second group is marked with paint on their outer surfaces:
- - white - the second group;
- - red - the first group.
When assembling the regulator with a thrust bearing, a thrust bearing 8110 must be installed on the weight hub, the inner ring of which must be pressed until it stops against the shoulders of the hub.
The bearing must be lubricated with engine oil.
Install crackers in the inner cavity of the hub, which must be lubricated with engine oil, and put the assembled unit on the camshaft of the fuel pump so that the projections of the thrust washer enter between the crackers.
When installing a new bearing, it is necessary to de-preserve it and then lubrication with engine oil.
The retaining spring ring must fit tightly in the annular groove of the camshaft, while there must be a guaranteed gap between the spring ring and the hub of the weights.
Before installing the regulator coupling with a thrust bearing, press the inner ring of the thrust bearing onto the coupling, while distortions of the ring are not allowed.
When installing the regulator coupling, rotation of the outer ring of the bearing and free movement of the coupling on the camshaft tail must be ensured.
The bearing is lubricated by pouring 150 - 200 ml of grease into the regulator before installing it on the stand for adjusting fuel pumps.
Before installing the corrector in the regulator, the corrector stroke should be pre-adjusted in the range of 0.5-0.7 mm.
Finally, the corrector stroke is adjusted on the stand to ensure the specified fuel supply according to the adjustment table.
The main and intermediate levers installed in the regulator body should swing freely on the axis without jamming.
Touching the bolt main lever for the groove of the intermediate lever is not allowed.
Bolt 56 (see Fig. 1), limiting the travel of the levers, must be installed on the KLT-75T compound.
From the inside of the regulator, screw the idle spring onto the bolt.
Rigid stop 60 must also be installed on the KLT-75T compound.
The bolt must be screwed in until its outer end protrudes above the surface of the regulator body boss by 12-13 mm and locked with a nut.
When installing in the regulator body, the enrichment roller cuff must be lubricated with engine oil.
When installing the control lever in the regulator body, the lever shaft must be lubricated with engine oil.
The adjusting screw located on the side of the regulator must be screwed in into the eye until its end protrudes above the surface of the eye by approximately 17 mm and is locked (measure from the rear wall of the regulator).
In the assembled regulator, the regulator spring must not touch the intermediate lever along the entire length of the control lever stroke.
Before installing the assembled regulator body onto the pump body, it is necessary to: check for the presence of cotter pins in the regulator units; connect the rack rod with the intermediate lever pin, it is allowed to apply KLT-75T compound to the mating surfaces of the pump body and the regulator body (after degreasing them) instead of a gasket.
When installing the regulator body as an assembly on the pump body, the regulator body must fit tightly, without distortions, onto the pump body pin.
In the assembled regulator, all parts must move without jamming.
At maximum forward deflection of the intermediate lever, the adjusting screw of the corrector must not rest against the spring lever.
The pump must be run in in cases of replacing the pump body, regulator body, plunger pair, pushers, plunger springs, regulator coupling, fuel pump, camshaft, and also if more fuel than the permissible amount is detected getting into the pump body.
The run in should be carried out with injectors, the springs of which are tightened to the injection start pressure of 12 - 17 MPa, at a rotation speed of 750 min -1 for 40 min.
Running-in is carried out with a variable position of the control lever.
During the running-in, it is necessary to monitor the normal operation of all units and mechanisms of the pump and regulator.
After running-in, the following threaded connections should be checked and, if necessary, tightened:
- - fuel pump mounting bolts;
- - regulator mounting bolts;
- - plate and mounting flange mounting bolts;
- - nipple clamps.